Пресс форма для производства двухцветной подошвы из ТПР,Пресс форма для подошв
Вступление
Двухцветная пресс форма для подошв из ТПР используется для производсва подошв из термопластической резины. С помощью данного оборудования можно получать следующую продукцию: кеды, ботинки для отдыха, туристическую обувь и кроссовки. К преимуществам данного оборудования следует отнести низкую стоимость и возможности регулировки скорости впрыска, а также большую скорость сжатия, которые снижают расходы материала. Оборудование состоит из верхней, средней и нижней заготовки пресс формы. Для осуществления одного цикла производства продукции необходимо 2 процедуры впрыска. К тому же, средняя пресс форма управляется только вручную. Благодаря жесткому контролю качества (более 4 испытаний), наши пресс формы не изменяют форм даже при температуре 400 ℃.
Свойства
(1) Открытие пресс формы происходит плавно, но быстро.
(2) Данная пресс форма является влагоотталкивающей.
(3) Она универсальна в работе.
(4) Конструкция не опасна по отношению к окружающей среде.
(5) Для ее конструкции применяется высококачественный сплав алюминия.
Преимущества
1. Для производства данных пресс форм используется импортное оборудование. Для этого используются 45 станков с програмным управлением, 4 специальные проектные комнаты, которые используются на нашем заводе для производства данного оборудования. Сканнер 3D, лавочка и испытательное оборудование поставляется из Германии. Хроматическая 3D пресс форма главной установки импортируется из США и позволяет выполнять работу сразу в 3/4/5 плоскостях.
2. Материалом для производства пресс форм служит металл от профессионального производителя металла в провинции Гуандонг, который прошел сертификацию качества ISO9001:2000.
3. У нас есть сервис центры по всему миру. Клиенты могут попросить о поддержке, ремонте либо техобслуживании, а также получить квалифицированную консультацию специалиста в ближайшем сервисном центре.
Параметры пресс формы для производства двухцветных подошв из ТПР
Цвет продукции | Двухцветная |
Тип продукции | Подошвы |
Материал пресс формы | Железо |
Тип пресс формы | Пресс форма на одну пару обуви |
Размеры пресс формы | Д(200-400) × Ш(150-240) × В(80-220) mm |
Вес пресс формы | 50-80 кг |
Упаковка | Картон |
Производство | CNC / Литье |
Температура производства | 100℃-275℃ |
Время доставки | 20 дней после подтверждения заказа деревянной пресс формы |
Срок службы | > 5 лет |
Предостережения
(1) Регулярно производите чистку и техническое обслуживание пресс формы для производства одноцветных подошв из ТПР
(2) Часто проверяйте положение впрыска
Прочее
(1) Доставка пресс форм осуществляется морем.
(2) Оплата возможна банковским переводом либо оплатой с помощью международных платежных систем.
Производство пресс форм для изготовления подошв из ТПР осуществляется параллельно с производством вспенивающе-инжекционного оборудования для производства обуви. Процесс производства управляется с помощью системы автоматического контроля, а управлять пресс формой для производства подошвы из ТПР достаточно легко. Компания Jili занимается производством вспенивающе-инжекционного оборудования, пресс форм для обуви, вспомогательного оборудования для производства обуви и т.д. Наша продукция успешно продается как в Китае так и за границей.
Похожая продукция- Пресс форма для производства одноцветных подошв из ТПРПресс форма для производства одноцветных подошв из ТПР для кедов, ботинок, туристической обуви и кроссовок из пенообразных термопластических материалов. К преимуществам данного оборудования следует отнести низкую стоимость и возможности регулировки скорости впрыска.
Пресс форма для производства обуви,Производитель пресс форм для обуви,Оборудование для изготовления обуви
- Пресс форма для обуви из ЭВАПресс форма для производства обуви из ЭВА используется для производства обуви, сделанной из ЭВА. С помощью данного оборудования можно выпускать следующую продукцию: обувь, аксессуары к обуви, подошву для кроссовок, встельки для обуви и обувь для альпинизма…
- Пресс форма для обуви из ПВХПресс форма для производства обуви из ПВХ используется для производства обуви стандартного внешнего вида. Она состоит из верхней, нижней и средней заготовки, а также средней пластины. Все перечисленные компоненты делаются из стали либо алюминиевого сплава, что делает устройство долговечным…
- Пресс форма для производства подошв из ТПРПресс форма для производства ТПР используется для производства подошв из ТПР, а также аксессуаров к подошвам.
Данное оборудование может быть разделено на одно-, двух-, трехцветные пресс формы для производства подошвы из ТПР. Разные пресс формы имеют различные компоненты и принцип работы. Например…
- Пресс форма для производства подошв из резиныДанная пресс форма используется для производства резиновых подошв и аксессуаров к ним. Оборудование для производства подошв из резины используется совместно с оборудованием для производства обуви. На выбор клиентов мы предлагаем пресс форму для одно- и двухветных изделий из резины. Благодаря тому…
Вступление
1. Компоненты
Пресс форма состоит из верхней заготовки, нижней заготовки, средней заготовки и средней пластины. С ее помощью можно производить подошвы, шлепанцы, сандали и другую обувь.
Процесс проектирования пресс формы для обуви состоит из нескольких процедур.
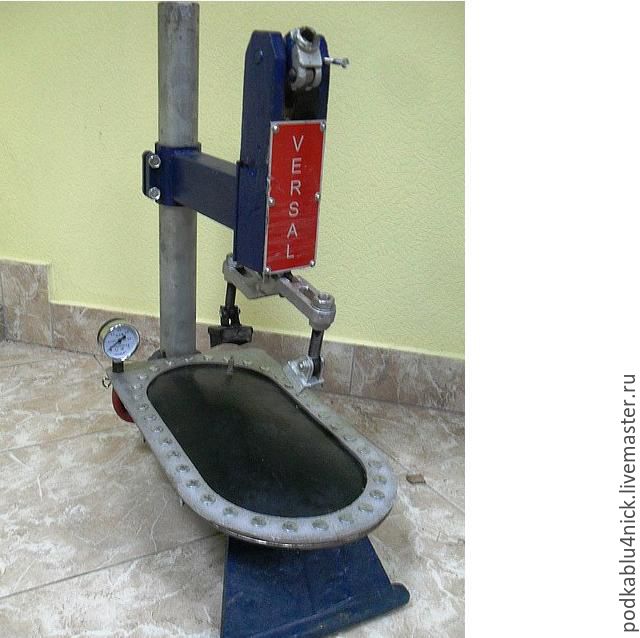
3.Свойства
Свойства определяются типом используемой заготовки. Некоторые пресс формы сделаны из алюминиевых сплавов, тогда когда другие делают из железа. Кроме того, абразивная стойкость разных пресс форм тоже разная.
4. Оборудование для производства обуви
Оборудование для производства обуви, которое выпускается нашей компанией может производить шлепанцы, санали, кроссовки и всякого рода подошвы из таких материалов: ЭВA/ПВХ/TПР/обычная резина.
Преимущества
(1) Мы предлагаем пресс формы для производства ЭВА обуви инжекционным/вспенивающим способом, пресс формы для ПВХ, ПВХ, резины и т. д.
(2) Профессиональная команда исследователей и разработчиков сделали все возможное для получения продукции высокого качества, которая соответствует тенденциям моды.
(3) Наши преес формы прошли сертификацию качства ISO и характеризуются длительным сроком эксплуатации.
(4) Имея больше 10 лет опыта, у нас есть свои сервис-центры по всему миру, что позволяет решить возникшие технологические и операционные проблемы.
Обратите внимание при покупке пресс формы на:
1. Цель использования
2. Длительность использования
3. Размеры пресс формы
Техническое обслуживание
(1) Очищайте данное обоурдование с помощью медного прутка, медного провода или специального очистителя и осушите его. Твердые материалы, такие как металлический провод, стальной прут запрещены к использованию, так как могут повредить поверхность пресс формы. Места со ржавчиной должны быть зачищены и потом покрыты специальной защитной смазкой.
(2) При износе деталей либо метаморфии смазки и возникновении коррозии вследствие попадания воды и грязи решается путем обязательного ремонта.
Аутентификация
Сертификация ISO
Способы оплаты данного оборудования
Банковский перевод
Перевод с помощью международных платежных систем
Доставка
Деревянные пресс формы доставляются в течении 20 дней после заказа. Груз покрывается картоном либо тремя слоями древесины.
Мы разаработали оборудование под брендом JIC которое включает в себя оборудование для производства EVA обуви, оборудование для производства резиновых сапог, оборудование для производства подошв, шлепанец, сандалей и другого вспомогательного оборудования за последние 5 лет.
ЗАПУЩЕНО НОВОЕ ПРЕДПРИЯТИЕ ПО ПРОИЗВОДСТВУ ПРЕСС-ФОРМ И ОСНАСТКИ ДЛЯ ОБУВНОЙ ПОДОШВЫ
Сегодня на витринах магазинов можно найти практически любую обувь, однако при покупке всё зависит от наших вкусов и возможностей. Тем не менее, каждый потребитель старается выбрать обувь, которая выглядит красиво, имеет хорошее качество и, несомненно, комфортна и удобна.
Специалисты также говорят о важности того, что хорошая обувь должна идеально подходить к стопе, а одним из важных элементов при её выборе является подошва, которая должна быть крепкой, эластичной и устойчивой к погодным и сезонным условиям.
До сегодняшнего времени отечественные производители обуви завозили всю необходимую оснастку для производства подошвы из зарубежных стран. Теперь отечественные предприниматели могут приобрести абсолютно любые пресс-формы у нашего местного производителя – узбекско-китайского СП «MARWEN», которое начало свою деятельность в городе Маргилан Ферганской области.
В целях ознакомления с процессом производства, руководство Ассоциации «Узчармсаноат» посетило данное предприятие. В рамках поездки состоялся обмен мнениями по дальнейшему расширению деятельности предприятия за счет продуктивного использования производственных мощностей. Так же была обсуждена возможность увеличения ассортимента пресс-форм, согласно потребностям внутреннего и внешнего рынков. Также был проведен анализ качества пресс-форм, оснастки и сырья, производимого на данном предприятии.
Для создания и запуска нового предприятия, которое способно производить 3000-4000 пресс-форм для обуви в год, было инвестировано 1,5 млн. долларов США, из которых 800 тыс. долларов США приходится на долю инвесторов из КНР.
На данном хозяйствующем субъекте установлено передовое зарубежное высокотехнологическое оборудование. Благодаря этому, производимые здесь пресс-формы и оснастки для обувной подошвы имеют хорошее качество и длительный срок действия. Данная оснастка является универсальной и её можно использовать для изготовления подошв различных видов обуви. С помощью этих пресс-форм создана возможность производства обувной подошвы в нескольких цветах.
По предварительным расчетам, на предприятии планируется выпускать 300-400 пар пресс-форм в месяц, а в дальнейшем этот показатель будет увеличен.
Кроме того, на предприятии также производится сырьё, используемое для изготовления обуви и её подошвы. Необходимое сырье для подошв и обуви производятся из термоэластопластов с применением методов «sebs и sbs». Твердость подошвы, изготовленной на основе таких полимеров составляет 25-90+ градусов.
Совместное предприятие ООО «MARWEN» на сегодняшний день является первым предприятием в Узбекистане, которое производит данные виды продукции. В будущем компания готова обеспечивать оснасткой для обувной подошвы и пресс-формами не только внутренний рынок Узбекистана, но рынки стран Центральной Азии, СНГ, Индии и Пакистана.
Вся продукция, производимая на предприятии, а это: пресс-формы, оснастка для литья подошвы и сырьё для подошв являются стопроцентной импортозамещающей и конкурентоспособной продукцией. Благодаря запуску проекта было создано около 100 новых рабочих мест. Работа на предприятии ведется в эффективном сотрудничестве с китайскими специалистами.
В перспективе предприятие планирует выпускать парты и стулья для инновационных аудиторий, оборудование для детских площадок, а также изготовить сырьё и оснастку для автомобильной и пищевой промышленности.
СП ООО «MARWEN» эффективно функционирует с начала ноября текущего года и уже сейчас оно приступило к процессу производства востребованной и качественной продукции с целью планомерного и своевременного исполнения договоренностей, достигнутых в ходе переговоров с крупнейшими хозяйствующими субъектами нашей страны.
Пресс-формы для шлепанцев из ЭВА, Пресс-формы для трех пар обуви
Пресс-формы для шлепанцев
Наша компания может изготовить пресс-формы для одной пары, двух пар и трех пар обуви. Все будет зависеть от размеров плиты формы вашего оборудования. Благодаря тому, что наша обувь изготавливается из высококачественного материала ЭВА, она может выдержать усилие смыкания в 190 тонн.
Наука и технологии – это первоначальные производственные силы. В нашей компании есть 45 станков ЧПУ и 4 офиса для осуществления компьютерного дизайна. Также наша компания обладает 3D-сканером из Германии, машинами для производства цветных трехмерных пресс-форм из США, 3-4-5-х осевым программированием, 3-4-5-х осевым программированием, ПО PowerSHAPE для проектирования пресс-формы и т.д.
Для успешного изготовления пресс-форм необходимо несколько раз проводить процесс деформирования и обработку после каждого данного процесса.
2. Мы изготавливаем пресс-формы в соответствии с параметрами Вашего оборудования.
3. Для производства мы используем самый дорогостоящий и высококачественный алюминий в Китае — Guangdong Zhiyuan 712 (3500 долларов США/тонна)
4. После изготовления пресс-форм мы тестируем их как минимум четыре раза на своем собственном тестирующем оборудовании из Тайваня.
Параметры пресс-формы
Материал: алюминий
Код ГС: 8480719090
Модель: пресс-форма для одной пары/двух пар/трех пар
Оборудование: пресс-формы для открытых шлепанцев из ЭВА подойдут для инжекционных литьевых машин, изготовленных в Италии, на Тайване, в материковом Китае и т. д.
Размер: длина(405-600)*ширина(240-580)*высота(110-255)мм
Вес: 30-250кг
Упаковка: картонная коробка или трехслойная картонная коробка
Обработка: на станке ЧПУ
Производственная среда: 175℃-210℃
Обувная колодка: для каждого размера обуви предоставляются четыре бесплатных колодки
Доставка: 25 дней (после изготовления деревянной пресс-формы)
Срок годности: Более 5 лет
Компания XIELI – это профессиональный производитель и поставщик пресс-форм для шлепанцев из ЭВА в Китае. Наша компания рада предложить Вам широкий ассортимент продукции, включая: инжекционные пресс-формы для обуви из ЭВА, пресс-формы для ТЭП подошв, пресс-формы для воздухопроницаемой обуви из ПВХ, пресс-формы для резиновых подошв и т.д.
Информация, связанная с данным продуктом
Пресс-форма для тапочек | Пресс-форма для туфлей без задника | Пресс-форма для полузакрытой обуви
3.
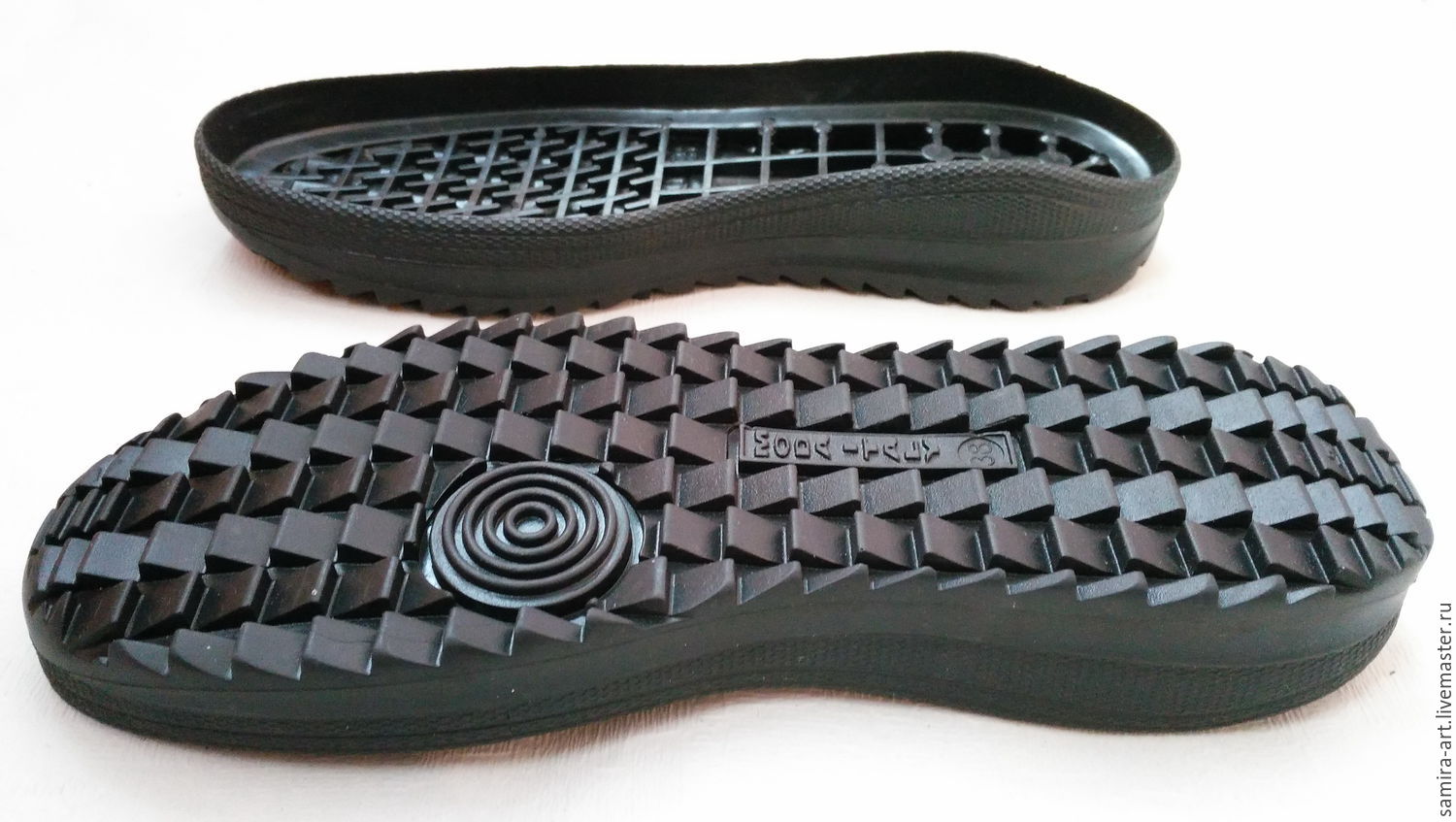
3.5 Производство обуви методом литья под давлением
Во многих странах широко применяется метод литья обуви из резины и термопластичных материалов. Ленинградский завод резиновой обуви ЛПО «Красный треугольник» был одним из создателей этого метода в отечественной практике. Сущность его заключается в том, что в закрытую полость пресс-формы впрыскивают дозу разогретого и пластифицированного полимерного материала. Если материал является эластомером (резиновая смесь), в пресс-форме происходит вулканизация изделия, если же материал термопластичен (ПВХ, ТЭП), то пресс-форма интенсивно охлаждается для устранения излишней пластичности термопласта.
Существует много конструкций литьевых машин, но все они имеют следующие узлы и механизмы: литьевую головку, устройство для дозирования, пресс-форму, системы обогрева и охлаждения, привод литьевой машины и пульт автоматической системы управления.
Литьевые машины выпускает ряд зарубежных фирм: «Штюббе» и «Десма» (Германия), «Сефом» (Франция), «Энгель» (Австрия), «Оттогалли» (Италия) и др.
Производство обуви методом литья под давлением имеет важные преимущества перед другими существующими методами: повышается производительность за счет сокращения времени вулканизации; улучшается качество резиновой обуви; ликвидируются операции изготовления заготовок; уменьшаются отходы материалов; появляется возможность полной механизации и автоматизации процессов.
Применение термопластичных материалов исключает необходимость подготовительного процесса. Изготовление обуви из них начинается на литьевом автомате и на нем заканчивается. Метод литья обуви из термопластичных материалов дает значительную экономию энергетических затрат, так как исключается процесс вулканизации. Производительность труда на одного работающего при этом методе в 2 раза выше, чем при методе формования, и в 9 раз выше, чем при методе клейки.
3.5.1 Производство обуви из резиновых смесей методом литья
При реализации процесса литья под давлением отпадает необходимость в изготовлении и сборке резиновых деталей, так как резиновая смесь в виде заготовки простой конфигурации (ленточка, жгут, гранулы) автоматически подается в литьевой узел.
В цилиндре литьевой машины резиновая смесь пластицируется, разогревается и после перехода в вязкотекучее состояние под давлением впрыскивается в закрытую нагретую пресс-форму, которая движется по кругу и автоматически размыкается после окончания цикла вулканизации.
До последнего времени в мировой практике не имелось опыта изготовления цельнорезиновой обуви на текстильной подкладке методом литья под давлением, за исключением отдельных экспериментов по литью галош на ЛПО «Красный треугольник» еще в 30-х годах, и рекламных данных немецких фирм «Штюббе» и «Десма» о разработке оборудования для литья сапог. Однако, несмотря на широкую рекламу, эти агрегаты для литья сапог высотой до 450 мм были изготовлены всего в одном экземпляре, и опыт их эксплуатации не увенчался успехом, так как не удалось получить изделия стабильного качества.
Сложность проблемы литья высокой резиновой обуви состоит в том, что в отличие от термопластов, которые при переработке методом литья под давлением вследствие разогрева переходят в истинно вязкое состояние (расплав), каучук и резиновые смеси характеризуются высокой вязкостью вследствие большой молекулярной массы эластомеров, и при их переработке развиваются большие высокоэластические деформации релаксационного характера.
В связи с этим для переработки резиновых смесей применяется литьевое оборудование, обеспечивающее более высокие давления литья при заполнении пресс-формы, а запирающее формы устройство обеспечивает при этом повышенные усилия смыкания в момент литья и вулканизации. Вулканизация требует выдержки изделия в течение определенного времени при высоких температурах нагрева формы.
Наличие текстильной подкладки с высокоразвитой поверхностью, а также сложная форма высокой резиновой обуви оказывает существенное влияние на реологическое поведение резиновых смесей и параметры процесса переработки, что в свою очередь требует как создания специального литьевого оборудования, так и синтеза резиновых смесей со сложным –комплексом свойств.
Эти трудности являются основными причинами отсутствия в мировой практике опыта изготовления эластичной резиновой обуви на текстильной подкладке методом литья под давлением.
3.5.2 Производство обуви из термопластичных материалов
Процесс переработки термопластичных материалов при литье обуви под давлением состоит в пластикации и плавлении гранулированного полимера в инжекторе литьевой машины, впрыске расплава в форму при высоком давлении и окончательном формировании изделия при охлаждении расплава в форме.
Применение высокого давления при литье необходимо не только для осуществления впрыска материала в форму, но и в основном для компенсации усадки при охлаждении. Чем выше давление литья, тем в меньшей степени происходят усадочные явления, так как за счет сжимаемости полимерного расплава при высоком давлении частично или полностью компенсируется уменьшение объема при резком охлаждении. Если эта компенсация происходит лишь частично, то применяют дополнительное нагнетание в пресс-форму расплава полимера давлением на начальной стадии охлаждения (дополнительную подпитку).
Наряду с давлением расплава полимера важнейшим технологическим параметром работы литьевых установок является температура материала, которая существенно меняется на разных стадиях процесса переработки, начиная с предварительного подогрева холодных гранул материала в специальном устройстве.
Еще одним важнейшим параметром процесса является продолжительность цикла литья—основной фактор, определяющий не только технологический режим литья, но и производительность установки. Резервы времени для увеличения производительности заключены в технологической части цикла, которая в основном определяется временем литья и охлаждения.
В качестве материала для литья обуви в отечественной и зарубежной практике в основном используются пластифицированные композиции поливинилхлорида.
При литье обуви используются две основные схемы литья: простое однослойное литье и многослойное, так называемое сэндвич-литье. Однослойное литье может применяться при изготовлении относительно простой по конструкции обуви, например полусапожек, невысоких туфель, сандалий, детской обуви. При этом в составе агрегата находится одна литьевая машина, а материал заполняет пресс-форму через один литьевой канал (литник). Примером такого оборудования являются агрегаты типа ТПН-10 и Н-6.
Многослойное литье состоит в поочередном впрыскивании двух и более расплавов полимеров из двух и более литьевых устройств в литьевую форму.
Принципиальное отличие процесса производства обуви из композиций ПВХ методом литья под давлением заключается почти в полном исключении закройно-заготовительного и подготовительного производства. Обувь, выпускаемая методом литья из ПВХ, состоит из внутреннего текстильного каркаса и наружного слоя ПВХ. Но так как требования к верху обуви и подошве различны, для их изготовления применяют ПВХ разных марок: для верха—ПЛ-1, для подошвы и каблука—ПЛ-2 (таблица 3.8).
Т а б л и ц а 3.8—Рецептуры композиций ПВХ
Наименование компонентов | Количество компонентов | |
ПЛ-1 | ПЛ-2 | |
ПВХ М-64 или С-63 | 100 | — |
ПВХ С-70 | — | 100 |
Диоктилфталат | 100 | 100 |
Стеараты | 1 | 1 |
Дифенилпропан | 0,1 | 0,1 |
Эпоксидная смола | 2 | 2 |
Красители (технический углерод, пигменты, титановые белила и т. | 0,01¸0,50 | 0,01¸0,50 |
Композиции ПВХ поступают на предприятия в виде гранул различных цветов. Гранулы ПВХ упакованы в двухслойные мешки (внутренний из полиэтилена, наружный из бумаги или текстиля), для защиты ПВХ от влаги. Перед пуском в производство ПВХ проверяют следующие его показатели:
ПЛ-1 | ПЛ-2 | |
Термостабильность при температуре 175±10С, мин | 100 | 100 |
Показатель текучести расплава при 1700С | 20 | 1 |
Перед тем как засыпать ПВХ в расходные бункеры литьевого автомата, его выдерживают в производственном помещении не менее 12 часов.
Технологическая схема производства сапог из ПВХ методом литья под давлением представлена на рисунке 3.10.
В качестве подкладки сапога применяют чулок, сшитый или из трикотажной трубки плюшевого переплетения, или из кроя трикотажного двухластичного технического полотна. Трикотажная трубка поступает на завод в рулонах. Перед раскроем она раскатывается в настил и подвергается вылежке в течение суток. При раскрое подкладки делают два реза: под углом 450 и поперечный по шаблонам, указанным в спецификации на изделие. Сборку подкладки-чулка производят на двух швейных машинах фирмы «АЛИМАТ», расположенных под углом 900 друг к другу. На первой швейной машине выполняется продольный шов по всей длине отреза, а на второй—поперечный, перпендикулярный первому. Сшитая подкладка в пачках по 10 штук подается к литьевому автомату.
Для изготовления сапог методом литья из ПВХ применяют литьевые автоматы «Десма 609/10». После запуска автомата в работу технологический процесс протекает автоматически в определенном рабочем цикле. Длительность рабочего цикла определяется временем, затрачиваемым на перемещение формоносителя из одного положения в другое. В зависимости от типа выпускаемой обуви время такта составляет 17¸23 с. Рабочий цикл включает в себя:
надевание подкладки-чулка на сердечник пресс-формы,
; подтяжку подкладки на штыри,
; смыкание полуформ,
; впрыск композиции ПВХ для верха обуви,
; перемещение пуансонного щита в положение впрыска подошвы,
; впрыск композиции ПВХ для подошвы,
; открытие пресс-формы, снятие сапога с сердечника и навешивание его на штырь тележки.
1—участок сборки подкладки-чулка на швейных машинах ф. «Алимат»,
2—склад композиций ПВХ,
3—бункер для загрузки ПВХ,
4—литьевой агрегат,
5—карусельный стол,
6—машины для обрезки излишков подкладки и ПВХ по верху голенища,
7—ленточный конвейер,
Ι—контроль качества,
ΙΙ—вкладывание стелек,
ΙΙΙ—подбор в пары,
ΙV—упаковка в короба,
V—упаковка в ящики, маркировка, отправка на склад.
Рисунок 3.10—Схема технологического процесса литья сапог из ПВХ
Основные технологические параметры литья приведены в таблице 3.9
Т а б л и ц а 3.9—Основные технологические параметры литья
Показатели | Композиции на основе ПВХ для | ||
верха обуви | низа обуви | ||
импортные | отечественные | ||
Температура обогрева литьевых машин по зонам шнека, 0С: | |||
первая зона | 165±10 | 165±10 | 165±10 |
вторая зона | 170±10 | 170±10 | 175±10 |
третья зона | 180±10 | 180±10 | 185±10 |
сопло | 175±10 | 175±10 | 175±10 |
Давление впрыска, МПа | 4,2±0,3 | 1,5±0,3 | 1,2±0,3 |
Давление пластикации, МПа: | |||
1 ступень | 1,5 | 1,0 | 1,0 |
2 ступень | 2,5 | 1,5 | 1,5 |
Время дополнительного нагнетания, с | 2,0±1,0 | 2,0±1,0 | 2,0±1,0 |
Давление дополнительного нагнетания, МПа | 1,5 | 0,5 | 0,5 |
Режим литья ПВХ при производстве сапог следующий:
Температура смеси при впрыске, 0С | 180±10 |
Время цикла, с | |
для сапог | 21±2 |
для сапожков | 19±2 |
Температура эмульсии при охлаждении сердечников, 0С | 20 |
Давление эмульсии при охлаждении сердечников, МПа | 0,4 |
Температура сердечников, 0С: | |
пяточная часть | 20±5 |
носочная часть | 40±5 |
Температура полуформ, 0С: | |
верх | 60±5 |
низ | 50±5 |
Литьевой автомат обслуживают 3 оператора. Они выполняют ручные операции рабочего цикла, пускают и останавливают литьевой автомат, контролируют параметры технологического процесса.
Первый оператор берет подкладку и натягивает ее на носочную часть сердечника, не закрепляя на шпильки. После поворота стола сердечник с подкладкой подходит ко второму оператору. Пресс-форма с готовым сапогом открывается на рабочем месте у первого оператора, который снимает сапог, проверяет его качество и вешает на штырь стоящей рядом тележки.
Второй оператор натягивает подкладку-чулок, расправляет, чтобы не было складок и натягивает подкладку на шпильки. Он же извлекает отходы ПВХ из литниковых отверстий пресс-формы. После размельчения на специальной машине литники снова используют в производстве.
Третий оператор засыпает гранулы ПВХ в бункер литьевых машин, обеспечивает первого оператора подкладкой-чулком, останавливает и пускает литьевой автомат, следит за параметрами технологического процесса.
Чтобы физическая нагрузка операторов была более равномерна, они через 1,5¸2 ч меняются рабочими местами.
Надетый на стержень тележки сапог находится в таком положении не менее 40 мин для охлаждения и стабилизации. В это время не следует изделие брать в руки и перемещать, так как возможна его деформация.
Готовые изделия поступают в сортировочно-упаковочное отделение для обрезки излишков по верху голенища и разбраковки. В годную продукцию вкладывают утепленную стельку, после чего сапоги подбирают в пары. Обувь укладывают в картонные коробки или деревянные ящики и отправляют на склад готовой продукции.
Несомненными преимуществами ТЭП по сравнению с ПВХ являются высокая эластичность при пониженных температурах эксплуатации, низкая плотность, а также относительно низкий уровень выделения летучих и токсичных веществ в процессе переработки. Однако низкая температуростойкость ТЭП, особенно бутадиен-стирольных, даже при относительно небольшом повышении температуры требует особо тщательного подхода при выборе как состава композиций, так и области их применения в производстве резиновой обуви.
По реологическому поведению термоэластопласты также существенным образом отличаются от ПВХ.
Изучение особенностей реологического поведения расплавов ТЭП позволило более обоснованно подойти к выбору режимов их переработки на литьевом оборудовании. Так, при переработке ТЭП, по-видимому, нет необходимости чрезмерно повышать давление литья, так как это не обеспечивает такого резкого повышения объемного расхода материала, как в случае переработки резиновых смесей.
В то же время относительно высокое значение кажущейся энергии активации вязкого течения ТЭП, наоборот, свидетельствует о целесообразности использования фактора температуры для интенсификации пластикации в червячной литьевой машине.
Еще более мощным средством для улучшения литьевых свойств ТЭП является его пластификация, причем значительный эффект достигается уже при относительно небольшом содержании пластификатора. Для снижения их вязкости применены те же методы, что и при разработке маловязких резиновых композиций для процессов литья и штампования обуви.
Т а б л и ц а 3.10— Техническая характеристика литьевых агрегатов для
Показатели | Тип агрегата, изготовитель | |||||||
G-2S, «Оттогалли» | U78/2, «Унион» | Sanpak-500 «Бата» | 611/10б «Десма» | TRN/10 Супер, «Нуова Дзарине» | F2C/14, «Оттогалли» | D2/14, «Оттогалли» | Delta 110, «Лоренцин» | |
Число формоносителей | 6; 8 | 12; 14 | 10 | 10 | 10 | 14 | 14 | 10 |
Число литьевых машин: червячно-плунжерных | 2 | 2 | 1; 2 | 2 | 1 | 1 | 1 | 1 |
червячных с дополнительным цилиндром | — | — | — | — | — | 1 | 1 | — |
Число пар обуви на формоносителе | 1 | 1 | 0,5 | 0,5 | 0,5 | 1 | 1; 0,5 | 0,5 |
Вид выпускаемой обуви | Сапоги, сапожки,сандалии | Сапоги, сапожки | Сапоги | Сапоги, сапожки | Сапожки, галоши, сандалии | Сапоги, сапожки | Сапожки, галоши | Сапоги, сапожки, сандалии |
максимальная высота, мм | 490 | 480 | 480 | 470 | 200 | 470 | 400 | 450 |
Производительность G, пар/ч | 90¸105 | 120¸160 | 90¸100 | 90¸130 | 80¸130 | 92¸105 | 92¸140 | 92¸140 |
Максимальная скорость пластикации Qmax, г/с | ||||||||
ЛМ-1 | 144,0 | 61,0 | 50,0 | 50,0 | 55,5 | 61,1 | 50,0 | 69,4 |
ЛМ-2 | 96,0 | 61,1 | 50,0 | 50,0 | — | 38,8 | 45,8 | — |
Максимальный объем впрыска Vmax, см3 | ||||||||
ЛМ-1 | 2350 | 2160 | 2160 | 1900 | 1420 | 2350 | 1400 | 1400 |
ЛМ-2 | 1250 | 2160 | 2160 | 760 | — | 1100 | 1100 | 1100 |
Максимальное давление впрыска Р, МПа | ||||||||
ЛМ-1 | 60 | 95 | 70 | 86 | 69 | 45 | 45 | 80 |
ЛМ-2 | 60 | 95 | 70 | 95 | — | 60 | 45 | 80 |
Максимальное усилие запирания форм F1, кН | 1600 | 2200 | 1600 | 1500 | 1500 | 1620 | 1200 | 2000 |
Диаметр червяка d, мм | ||||||||
ЛМ-1 | 100 | 100 | 75 | 90 | 85 | 100 | 100 | 80 |
ЛМ-2 | 80 | 100 | 75 | 65 | — | 80 | 80 | 80 |
Отношение L/d | ||||||||
ЛМ-1 | 20 | 20 | 22 | 18 | 17 | 13 | 13 | 15 |
ЛМ-2 | 18 | 20 | 22 | 18 | — | 18 | 18 | 15 |
изготовления цельнополимерной обуви
Робототехнологические комплексы | |||||||||
Delta 214 «Лоренцин» | Bipak, «Бата» | T2S/6 «Оттогалли» | Н/6, НЕ/6 «Оттогалли» | AZ-250, «Нуово Дзарине» | Sanpak-1, «Бата» | 603/10 «Десма» | 618S/10, «Десма» | U78/2C-8, «Унион» | U76/2D-8, «Унион» |
14 | 10 | 6 | 6 | 10 | 10 | 10 | 10 | 8 | 8 |
2 | 2 | 2 | — | 2 | 1 | 2 | 2 | 2 | 2 |
— | — | — | 1 | — | — | — | — | — | — |
0,5 | 0,5 | 1 | 1 | 0,5 | 0,5 | 0,5 | 0,5/1 | 0,5/1 | 0,5/1 |
Сапоги, сапожки, сандалии | Сапожки, галоши | Сапожки, сандалии | Галоши, сандалии | Сапожки, сан-далии, галоши | Сапоги, сапожки | ||||
450 | 370 | 320 | 210 | 320 | 200 | 180 | 300 | 450/380 | 360/240 |
120¸160 | — | 100¸160 | 90¸120 | 80¸180 | 80¸150 | 90¸110 | 100¸150 | 110¸170 80¸130 | 70¸110/ 90¸150 |
69,4 | 27,7 | 96,0 | 50,0 | 50,0 | 50,0 | 55,5 | 50,0 | 61,0 | 50,0 |
— | 37,5 | 96,0 | — | 30,5 | — | 33,3 | 50,0 | 61,0 | 50,0 |
1400 | 1320 | 1250 | 1200 | 1420 | 600 | 495 | 1900 | 2350 | 1360 |
1400 | 1560 | 1250 | — | 900 | — | 760 | 800 | 1360 | 1360 |
80 | 70 | 60 | 45 | 45 | 70 | 70 | 90 | 90 | 58 |
80 | 70 | 60 | — | 45 | — | 95 | 90 | 58 | 58 |
2000 | 1600 | 830 | 1080 | 1200 | 550 | 300 | 1500 | 2200 | 1600 |
80 | 70 | 80 | 100 | 70 | 50 | 55 | 90 | 100 | 90 |
80 | 70 | 80 | — | 70 | — | 55 | 90 | 90 | 90 |
15 | 22 | 18 | 13 | 16 | 20 | 18 | 18 | 20 | 18 |
15 | 22 | 18 | — | 16 | — | 18 | 18 | 18 | 18 |
Продолжение таблицы 3.10
Показатели | Тип агрегата, изготовитель | |||||||
G-2S, «Оттогалли» | U78/2, «Унион» | Sanpak-500 «Бата» | 611/10б «Десма» | TRN/10 Супер, «Нуова Дзарине» | F2C/14, «Оттогалли» | D2/14, «Оттогалли» | Delta 110, «Лоренцин» | |
Общая установленная мощность, кВт | ||||||||
электродвигателей | 99 | 75 | 57 | 109 | 50 | 75 | 83 | 60 |
нагревателей | 40 | 21 | 30 | 50 | 16 | 47 | 39 | 18 |
Масса, кг | 30000 | 36000 | 10000 | 39000 | 10240 | 39000 | 21700 | 25000 |
Габаритные размеры, мм | ||||||||
длина | 9200 | 9170 | 6200 | 9800 | 5600 | 7800 | 6300 | 32000 |
ширина | 4500 | 7180 | 3080 | 9000 | 2700 | 7100 | 4200 | 4000 |
высота | 3900 | 2050 | 2280 | 2345 | 2000 | 3950 | 3300 | 1870 |
Примечания.
1. Перерабатываемые материалы: пластикаты ПВХ, композиции на основе ТЭП, гранулированные полиуретаны.
2. ЛМ-1 и ЛМ-2 литьевые машины соответственно для первого и второго слоя.
3. Максимальная скорость пластикации приводится по пластикату ПВХ.
4. В состав РТК входят промышленные роботы для извлечения литников и съема обуви.
5. Максимальная температура переработки 2500С.
Для получения композиций, удовлетворяющих этим требованиям и обеспечивающим необходимый уровень физико-механических и эксплуатационных свойств материала, необходимо использовать α-метилстирольные ТЭП. При одной и той же степени наполнения и одинаковом количестве пластификатора композиции на основе α-метилстирольных ТЭП имеют существенно более высокие физико-механические показатели (в том числе при повышенных температурах) по сравнению с композициями на основе бутадиен-стирольных ТЭП . Кроме того, как показали проведенные исследования, более высокая температуростойкость α-метилстирольных ТЭП (особенно радиальной структуры) обеспечивает улучшение эксплуатационного качества (прочности связи полимерной обсоюзки с текстильным верхом) полимернотекстильной обуви.
Исследования структурной пластификации эластомеров и термоэластопластов применительно к задачам создания композиций ТЭП для расширения ассортимента материалов, используемых для литья обуви, оказались особенно плодотворными при разработке композиций на основе маслонаполненных ТЭП. Используя маслонаполненный полимер, содержащий пластификатор оптимальной молекулярной массы, и вводя в состав композиции
Робототехнологические комплексы | |||||||||
Delta 214 «Лоренцин» | Bipak, «Бата» | T2S/6 «Оттогалли» | Н/6, НЕ/6 «Оттогалли» | AZ-250, «Нуово Дзарине» | Sanpak-1, «Бата» | 603/10 «Десма» | 618S/10, «Десма» | U78/2C-8, «Унион» | U76/2D-8, «Унион» |
102 | 100 | 80 | 50 | 93 | 45 | 46 | 110 | 90 | 66,5 |
32 | 50 | 30 | 18 | 23 | 20 | 28 | 50 | 40 | 23 |
38000 | 15000 | 24400 | 7900 | 17500 | 8000 | 20000 | — | 28000 | 20500 |
8500 | 4280 | 6800 | 4500 | 7080 | 6200 | 8400 | — | 13000 | 11400 |
8000 | 6850 | 3670 | 2300 | 7000 | 3090 | 6500 | — | 7000 | 7000 |
1900 | — | — | 2800 | 2050 | 2280 | — | — | 2200 | 2200 |
олигомерный пластификатор (атактический полипропилен), удалось создать композиции, приближающиеся по реологическим свойствам к композициям ПВХ. Вследствие этого можно перерабатывать эти композиции на многопозиционных литьевых автоматах и получать различные виды обуви типа галош и сапожек.
Развитие технологии литья и более широкий круг материалов для обуви обусловили появление разнообразных конструкций литьевых агрегатов. Ведущие машиностроительные фирмы «Десма» (Германия), «Оттогалли», «Лоринцин» (Италия) и другие— выпускают в настоящее время роторные литьевые полуавтоматы различного назначения для переработки на них монолитных и вспененных композиций ПВХ, термоэластопластов. Сравнительная характеристика современных литьевых установок приведена в таблице 3.10.
укрепляет свои позиции на рынке
SR решил выяснить, с какими проблемами пришлось жить и работать российским обувщикам, и спросить производителей о работе в сегодняшних реалиях. В данной статье речь пойдет о влиянии пандемии коронавируса на отечественный обувной бизнес, общие настроения на обувном рынке, о первом опыте внедрения обязательной маркировки и стратегии импортозамещения в стране, которая почему-то обошла обувной сегмент. Несмотря на все трудности, российские производители обуви продолжали развиваться и двигаться вперед: так, ростовская компания DEOX начала предлагать услуги создания обувных брендов «под ключ».
На вопросы SR отвечает Виталий Картавых, директор крупной производственно-консалтинговой обувной компании DEOX. На протяжении 20 лет компания является разработчиком, изготовителем пресс-форм нашивных резиновых изделий и подошвы, производство расположено в Ростове-на-Дону. С 2019 года компания запустила собственный бренд и начала изготовление женской, детской и мужской обуви (с 16-го по 45-й размер). Сегодня, производя модную, яркую и качественную обувь в ценовом сегменте средний+, компания DEOX является достойным конкурентом поставщикам европейской обуви.
Виталий Картавых — директор крупной производственно-консалтинговой обувной компании DEOX.SR: Виталий, как развивались российские компании в условиях очень непростого 2020 года?
Виталий Картавых: Объемы заказов крупнейших производителей обуви начали сокращаться с 2019 года. Еще тогда, принимая заказы на нашивные изделия от крупных компаний, мы на личном опыте убедились, что основная масса производителей уходит в дешевый сегмент обуви и начинает сокращать объемы производства. В 2020 году, уже в условиях пандемии, российские компании пытались еще больше минимизировать свои затраты и продолжали сокращать объемы выпуска обуви. Большие остатки в торговле и на складах производителей привели к демпингу цен в опте. Однако в конце 2019 года серый импорт из Китая вырос примерно вдвое (по данным неофициальных источников). В итоге падение цен в оптовой торговле не принесло успеха ни одному из производителей обуви. А сложный и дорогой процесс работы с маркировкой только добавил проблем.
SR: Как повлияла пандемия на бизнес процессы: производственный цикл, развитие розницы и клиентских сервисов?
В.К.: Многие покупатели перестроились на покупки через интернет, а некоторые и вовсе сократили расходы на обувь. Пандемия при-вела к закрытию большого количества розничных магазинов ввиду их нерентабельности, однако онлайн-формат показывает хорошие результаты по продажам. Что касается нашего производства, обувь DEOX укрепляет лидирующие позиции на российском рынке. Кроме того, мы решили предложить оптовым клиентам новую услугу по совместному созданию бренда обуви. Мы будем помогать в разработке, регистрации бренда клиента в РОСПАТЕНТЕ, сможем изготовить новые модели обуви, а также обеспечим необходимые упаковочные материалы. То есть практически весь процесс по созданию бренда обуви мы можем взять на себя. Продажи у нас и наших клиентов идут через офлайн-магазины и интернет-магазин Wildberries в пропорции50/50. Мы уже запустили 5 новых брендов.
SR: Как прошло внедрение обязательной маркировки, плюсы и минусы, которые уже выявили?
В.К.: Внедрение маркировки оказалось довольно дорогостоящим процессом и сопровождалось огромным стрессом для обувного рынка. Это еще одна дополнительная отчетность, которая еще более усложняет и без того огромный документооборот. К сожалению, китайский серый импорт остался и неплохо существует – контрафактный товар и сейчас успешно реализуется без документов.
SR: Импортозамещение: насколько успешно оно идет в обувном секторе?
В.К.: Средний и средний+ сегменты обуви в России постепенно исчезают – осталось всего несколько компаний, работающих в данном ценовом диапазоне. А в дешевом сегменте импортозамещение сделать невозможно без помощи государства. Правительство не занимается данным вопросом, финансирования нет, поэтому каждый выживает, как может, на собственных ресурсах.
SR: Какие есть проблемы, например, с комплектующими, материалами?
В.К.: Так как производителей обуви в среднем сегменте мало, то поставщики кожи, подошвы и фурнитуры не особо стремятся привозить более качественный ассортимент. Отсюда и задержки с поставками, и сложности с доставкой. Поэтому мы всегда рассчитываем свои производственные сроки, учитывая этот фактор.
SR: Ваши итоги 2020 года и планы/пожелания на 2021 год…
В.К.: В 2020 году компания DEOX масштабировалась. Под нашим брендом выпущены коллекции обуви с длинными размерными рядами – с 16-го до 45-го размера. Также мы стали производить коллекции в популярном стиле Family look. У нас огромное предприятие, и наши производственные мощности позволяют делать сложные модели из натуральной кожи и меха. Мы осуществляем и консалтинговые услуги. И наконец, мы запустили услугу «Создание бренда обуви «под ключ» для наших клиентов. В 2021 году планируем продолжить в том же духе и выпустить коллекцию сумок в стиле Family look из натуральной кожи. Первая сумка уже представлена для продажи в нашем Instagram и на Wildberries.
Материалы подготовила Екатерина Сергеева
SR решил выяснить, с какими проблемами пришлось жить и работать российским обувщикам, и спросить производителей о работе в сегодняшних реалиях. В данной подборке материалов речь пойдет о влиянии…
Пресс-формы – изготовление пресс-форм в Туле / «МашМет»
Завод металлообработки / Услуги / Изготовление пресс-форм
Металлическая пресс-форма — элемент, основное назначение которого заключается в ускорении серийного производства изделий из резины и пластика. С помощью пресс-форм создаются подошвы для обуви и стулья, корпусы для ноутбуков и предметы интерьера. От качества пресс-формы зависят и характеристики конечной продукции, поэтому к процессу производства самих пресс-форм следует относиться максимально внимательно и ответственно.
Изготовление пресс-форм — одно из направлений завода «МашМет». В распоряжении наших мастеров современное оборудование, что снимает любые ограничения с фантазии заказчиков: для нас нет неразрешимых задач, есть только задачи, которые требуют чуть больше времени.
Этапы производства пресс-форм
Весь процесс производства пресс-форм можно условно разделить на несколько этапов. На каждом этапе необходимо достигнуть оптимальных результатов, чтобы итог работы — пресс-форма — максимально полно отвечала требованиям заказчика.
Создание ТЗ. Техническое задание требуется для того, чтобы мы точно понимали, каким критериям должна соответствовать изготавливаемая пресс-форма. Во время брифинга с заказчиком мы выясняем все нюансы, и только после этого переходим к следующему этапу.
1. Создание трехмерной модели — сначала изделия, а потом пресс-формы, в масштабе 1:1. Чтобы создать 3D-модель пресс-формы, нужно сначала изготовить точную модель изделия, которое заказчик хочет получать с использованием пресс-форм. На полученную трехмерную модель изделия реальных размеров потом «наращивается» пресс-форма.
2. Производство пресс-формы. В цеху пресс-форма изготавливается и закаляется, благодаря чему становится более прочной, надежной, долговечной. Закалка также повышает устойчивость пресс-форм к воздействию внешних факторов. Все процессы проводятся под наблюдением технолога, на каждом этапе осуществляется контроль качества форм.
3. Сборка пресс-формы и пробная отливка изделия. После того, как конструкция собрана, необходимо провести пробную первую отливку, чтобы проверить точность формы, ее соответствие изначальным требованиям заказчика. Мы не просто отливаем пробное изделие, чтобы оценить его внешнее соответствие ТЗ, но и тестируем получившийся продукт, чтобы оценить его надежность, долговечность, прочность.
4. Доработка. В случае, если во время тестирования пресс-формы выявлены даже незначительные дефекты, если изготавливаемые с помощью пресс-формы изделия требуют дополнительной инструментальной обработки, проводится доработка.
Цены на изготовление
Основная задача пресс-формы — ускорить и удешевить производство изделий без ущерба для конечного качества результата. При этом сами пресс-формы для пластмассы не должны стоить слишком дорого, в противном случае, смысл такой технологии пропадает.
Говорить о том, сколько стоит изготовление пресс-формы, можно только относительно конкретных ситуаций — цены на такие формы могут варьироваться в большом диапазоне, определяясь:
- способом прессования. Наиболее востребована сегодня технология прямого прессования — это самый экономичный и рациональный вариант при производстве низкодетализированных изделий небольшими партиями. Есть альтернатива — пресс-формы для литьевого прессования, которые используются при производстве элементов с маленьким диаметром и большой глубиной: такие пресс-формы дороже в изготовлении, но позволяют создавать более детализированные изделия;
- запасом прочности. Речь идет о максимальном количестве циклов использования пресс-формы. По этому признаку пресс-формам присваиваются классы. Так, например, класс 105 будет дешевле — он может выдержать до 500 рабочих циклов (при производстве используются мягкие металлы) и используется преимущественно для прототипирования. Класс 101 обойдется заметно дороже, так как изготавливается из высококачественной закаленной стали, но зато с его помощью вы сможете изготовить до 1 000 000 изделий. Пресс-формы 103-104 классов — золотая середина, как в плане стоимости, так и в плане производительности, способны выдержать до 500 000 рабочих циклов;
- количеством плит. Если с помощью пресс-форм планируется создавать простые детали, то лучше выбрать формы с двумя плитами — пуансоном и матрицей: плиты соединяются с формообразующим пакетом, составляя единое целое. К недостаткам такого варианта можно отнести единственную плоскость разъема, что определяет довольно узкую сферу применения таких пресс-форм. Трехплитные модели дороже и используются при изготовлении сложных изделий: благодаря двум плоскостям разъема раскаленный материал может достигнуть любой точки изделия при заливке в пресс-форму;
- типом литниковой системы. Функция литниковой системы заключается в подаче в пресс-форму материала по трубкам и отверстиям. Существуют разные типы литниковых систем. Есть холодноканальные — расплав вместе с литником остывает, после чего его вынимают вместе с отлитым объектом, то есть, в этом случае литник здесь является одноразовым расходником. Есть также горячеканальные литники, в которых применяются нагревательные элементы, сохраняющие равномерную температуру в системе — в результате литник не твердеет, и в будущем его можно использовать снова. Последний вариант более дорогой, но он экономичнее и позволяет ускорить процесс производства изделий.
Виды пресс форм и применение
Каждая пресс-форма для литья пластмасс имеет уникальные характеристики, которые определяются ее видом. Существует несколько способов классификации пресс-форм:
- прямого и литьевого прессования. В первом случае сырье выкладывается на матрицу, уплотняется, истончается. Литьевые формы предполагают залив сырья с помощью загрузочной камеры и используются для больших объемов;
- съемные и стационарные формы. Первые можно убрать с плит литьевых машин, чтобы извлечь готовые изделия. Стационарные формы встречаются чаще — они не снимаются с плит автомата для литья;
- формы с вертикальными и горизонтальными плоскостями;
- одногнездные и многогнездные. Первые позволяют за один цикл литья изготовить только одно изделие, вторые, соответственно, два и больше;
- формы с вкладышами, выталкивающими стержнями, без выталкивателя, со сталкивающей плитой;
- с горяче- и холодноканальной литниковой системой. О них мы уже писали выше.
Наши преимущества
Мы предлагаем вам возможность заказать пресс-формы в Туле на выгодных условиях — гарантируем высокое качество нашей продукции, индивидуальный подход, возможность выполнения заказов любой сложности, доступные цены. Работаем как с юридическими, так и с физическими лицами, с любыми объемами. Ждем вас!
Заказать производство пресс-формы
Формовка подошвы обуви: 5 шагов
У меня было ограниченное время и деньги, поэтому мне пришлось очень тщательно планировать (а потом все равно пришлось переделывать вещи).
Визуализируйте и нарисуйте свой дизайн.
Визуализируйте и нарисуйте процесс, которому вы будете следовать.
Дизайн подошвы
Мой дизайн был довольно плоской подошвой, от 11 мм высотой в пятке до 7 мм спереди. Я использовал 1 слой стельки толщиной 1 мм для дизайна на нижней части подошвы, поэтому числа нечетные. У меня также была высота по периметру 2 мм, поэтому общая высота подошвы составляет 13 мм сзади и 9 мм спереди.Чем больше вы увеличиваете, тем больше материалов вам нужно и больше слоев в форме.
Нижний узор Последнего является отправной точкой. Ваша стелька (к которой приклеивается верх) будет точно такой же, как и нижний узор.
Верхняя поверхность подошвы должна быть примерно на 2 мм больше со всех сторон. Это учитывает толщину кожи и подкладки в сложенном виде (показано на изображении).
Мой рейтинг был шириной 2 мм и высотой 2 мм (1 слой стельки толщиной 2 мм)
Это основные размеры, от них просто используйте свое воображение.Изображения на первой странице показывают дизайн, который я сделал, это довольно простой дизайн.
Дизайн пресс-формы
Я решил спроектировать пресс-форму с перевернутой подошвой. Это означает, что сзади есть «глубокая» точка, уходящая вверх к большому отверстию. Я разработал подошву, когда работал над формой. С помощью программного обеспечения вы можете показать все слои сразу, таким образом, вы можете легко поместить кривую или деталь в один слой и при необходимости перенести их на другие слои.
Моя форма была разделена на 3 части, но это можно было сделать и на 2 части.Я сделал его в 3 слоя, чтобы было легче заливать резину в форму. Идея состоит в том, чтобы соединить две нижние части вместе, вылить наверх, затем положить верхний слой формы и заполнить ее через небольшие отверстия для выпуска воздуха.
Можно сделать с 2 секциями. Просто добавьте отверстия чуть большего размера, чтобы в них залить резину.
Начните с базового слоя и двигайтесь вверх, помня, что вы проектируете полость для своей подошвы, а не для самой подошвы.
К сожалению, я потерял исходные изображения моего настоящего дизайна.Я сделал быстрый пример в Solidworks, чтобы попытаться объяснить процесс и дизайн.
Производство пресс-форм для подошвы обуви — Экскурсия по фабрике пресс-форм
Сегодня мы посетили компанию Yuan Shen Metal Mold Company. Мой друг Дэвид Коллинз, ветеран обувного дела более 30 лет, является вице-президентом по продажам и отвечает за отношения с англоговорящими клиентами. Дэвид работал в Корее, Тайване, Китае и Вьетнаме, производя обувь для многих ведущих брендов.
Расположен в Южном Китае
Yuan Shen Metal Mold Company находится в городе Чанг Ань на юге Китая.Юань Шэнь находится в центре китайской обувной торговли; до завода можно добраться на машине из Гонконга за 2 часа или из аэропорта Шэньчжэня за 45 минут.
Yuan Shen — это фабрика по проектированию и производству форм для подошвы с полным спектром услуг. Завод имеет возможности 2D и 3D проектирования подошвы, межподошвы и деталей для инъекций. Вы предоставляете прочный верх и двухмерный дизайн, а наша команда разработает дизайн вашей подошвы по размеру. Юань Шен работает напрямую с выбранной вами обувной фабрикой в качестве субподрядчика.Когда вы работаете с таким подрядчиком, как Юань Шэнь, вы владеете формами подошвы и контролируете их.
Дэвид работал с Юань Шен, чтобы убедиться, что у них есть необходимое оборудование для изготовления всех типов форм для обуви. Имея 6 высокоскоростных станков с ЧПУ, Yuan Shen может выполнить крупную серию распилов по дереву за 3 дня и полный набор металлических форм за 40 дней.
Внутренняя SLA 3D-печать
У них есть служба быстрой разработки прототипов. Дэвид показал нам собственное оборудование для 3D-печати SLA. Они также могут создавать силиконовые формы для заливки из полиуретана.Эти формы стоят около 350 долларов и могут использоваться для изготовления до 15 гибких пригодных для носки тестовых деталей для прототипов обуви.
Их цены на пресс-формы очень конкурентоспособны для рынка инструментальной оснастки Южного Китая.
Формовка резиновой подошвы за 1,400 долл. США
От 1800 до 2000 долларов за пресс-формы для литой алюминиевой подошвы из ЭВА.
Производство во Вьетнаме
Компания Yuan Shen Metal Mold Company построила дочернюю фабрику за пределами Хошимина для обслуживания клиентов с производством во Вьетнаме.Многие из их клиентов пользуются их услугами по разработке в Китае, а затем производят пресс-формы во Вьетнаме.
Если вы хотите организовать экскурсию или обсудить ваши требования к пресс-форме,
свяжитесь напрямую с Дэвидом Коллинзом. [email protected]
Нравится:
Нравится Загрузка …
10. Формовка и литье — FabAleza
На этой неделе я просмотрел паспорта безопасности для каждого из ваших формовочных и литейных материалов, затем сделал и сравнил тестовые отливки с каждым из них и спроектировал 3D-форму вокруг заготовки и инструментов, которые вы будете использовать, фрезеровать и использовать. это для литья деталей.Я решил спроектировать и изготовить свои собственные подошвы для обуви, и, если будет достаточно времени, связать остальные в 3D и построить целую обувь.
Мне всегда нравились туфли, в частности кроссовки. Фактически, я собирал обувь, независимо от ее размера и назначения, любые кроссовки, которые меня привлекали, я добавлял в свою коллекцию. В дополнение к коллекционированию обуви я также всегда добавляю к ней свои собственные штрихи, обычно рисуя фломастерами. Моя мечта — стать дизайнером обуви. Я подумал, что задание на этой неделе будет идеальным местом для начала.
Ниже представлен один из моих любимых дизайнов кроссовок Бринко
Было изготовлено всего 1000 экземпляров этих туфель, эти кроссовки ограниченным тиражом — больше искусство, чем обувь. Judi Werthein , Brincos были созданы для рабочих-мигрантов, пересекающих границу США и Мексики. К каждой паре прилагается фонарик и компас, прикрепленные к шнуркам, небольшой карман на языке для денег или обезболивающих и карта границы, напечатанная на съемной стельке. Рисунок на пятке в расцветке мексиканского флага представляет собой мексиканский орел, а рисунок на носке напоминает американский орел, изображенный на четверти доллара.Небольшой портрет утвержденного Ватиканом покровителя мигрантов Св. Торибио Ромо Гонсалеса украшает заднюю щиколотку. В то время как Brincos можно было купить в Printed Matter за 215 долларов, Вертейн бесплатно распространял их на пограничных переходах. ДОВОЛЬНО КРУТО!
FabSole
Исследования
Инструмент для подошвы обуви
Типы подошвы
фабрика кроссовок
- Подошва или подошва: нижний компонент обуви, обеспечивающий сцепление и сцепление.Подошва обычно изготавливается из резины, но может быть из пенополиуретана или этиленвинилацетата высокой плотности. Классические туфли могут иметь кожаную подошву.
Промежуточная подошва подушки безопасности
Промежуточная подошва воздушной подушки изготовлена методом выдувного формования. Промежуточная подошва представляет собой экструзионную трубку из горячего полужидкого пластика (называемую заготовкой). Стальная форма зажимает трубу, и воздух вводится внутрь, чтобы заполнить мешок, и надувает форму, чтобы заполнить форму. Инструменты и станки очень дорогие. Пластик можно тонировать, а верхнюю и нижнюю поверхности пакета можно красить.В этом случае воздушная подушка прикрепляется к лотку из этиленвинилацетата, который затем прикрепляется к подошве обуви с помощью процесса холодного цемента. Тип подошвы отлично подходит для бега и кросс-тренинга. Воздушная подушка выглядит круто, но из-за процесса выдувания пластиковые стенки сумки могут быть немного толстыми. Для этого единственного блока требуется пресс-форма из ЭВА, пресс-форма для резины и выдувные формы.
Подошва Компонент обуви между верхом и подошвой, используемый для обеспечения амортизации, посадки, комфорта и поддержки.Будет изготовлен из пенополиуретана или этиленвинилацетата. — Пена EVA или CM EVA — Формованный под давлением EVA или этиленвинилацетат. Вспененный материал межподошвы, обеспечивающий хорошую амортизацию и сжатие. Nike ™ любит называть свой «Пилон ™», но это то же самое, что бы вы ни называли. Самый распространенный поролон для подошвы обуви. Легкая форма для резки, формования, литья под давлением. Он легкий и прочный. EVA может быть разных сортов в зависимости от состава. Более или менее наполнитель, более или менее винилацетат в смеси. Подушка из ЭВА может быть мягкой или твердой.- Пенополиуретан: обычная набивка внутри язычков и воротников обуви. Открытые ячейки пропускают воздух и воду. Может быть очень мягким. Ноу и поролон KFF или K360 Кожа PU Полиуретановое пластиковое покрытие поверх синтетической основы. Это очень распространенный материал для любой современной спортивной обуви.
ЭВА или CMEVA, формованная сжатием
Стандартная двухкомпонентная подошва изготовлена из легкой межподошвы CM EVA, прикрепленной к резиновой подошве. Пена EVA расширяется в блоки, а затем разрезается, чтобы поместиться в форму.Форма нагревается, что приводит к повторному расширению EVA и заполнению пресс-формы. Плотность и дюрометр устанавливаются в зависимости от того, сколько пены вдавливается в форму, и по формуле пены. Чем больше пены, тем тверже и придает подошве больше четкости. Промежуточная подошва приклеивается к резине в примерочной до того, как изделие встретится с верхом при сборке. Эта подошва требует пресс-формы из ЭВА и резиновой пресс-формы.
- Пена EVA:
Этиленвинилацетат — сополимер этилена и винилацетата.Весовой процент винилацетата обычно варьируется от 10 до 40%, а остальная часть составляет этилен. Чаще всего используется пена для амортизации обуви. EVA может подвергаться горячему или холодному прессованию, может быть любого цвета и различной твердости. Этот материал также можно получить путем инъекции. EVA — наиболее распространенная набивка межподошвы, но также используется в верхней части обуви. Есть ли у пены eva набор для сжатия? Да! Низкокачественный или очень мягкий EVA будет иметь высокую степень сжатия. EVA более высокого качества будет сопротивляться сжатию.
Дюрометр
- Дюрометр — это твердость материала. Вам нужно будет указать твердость всех резиновых, поролоновых и пластмассовых деталей обуви. Вам понадобятся 2 разных тестера твердомера. Asker «C» — это стандарт EVA. 25 «С» — очень мягкая, 55 «С» — стандартная межподошва, 85 «С» — как дерево. Для резиновой пластмассы вам понадобится тестер Шора «А». Для резиновой подошвы Shore «A» 55 подходит для резины. При температуре выше 60 резина будет жесткой, тяжелой и скользкой. См. Обувные инструменты .
Инъекционная межподошва
Многие фирмы экспериментируют с бесшовной подошвой, полученной литьем под давлением.Под пяткой в обуви имеется жесткая регулирующая пластина, обеспечивающая устойчивость обуви. Конструкция межподошвы, вероятно, сделана из нейлона или пластика TPU. Резиновый протектор крепится с помощью приклада. Этот блок подошвы требует пресс-формы из ЭВА для скрытой внутри межподошвы, резиновой пресс-формы для протектора и литьевых форм для компонента промежуточной подошвы.
- Протектор или протектор обуви
- Часть обуви, контактирующая с землей. Чаще всего протектор обуви резиновый.
Подошва из ЭВА для инъекций
В этих беговых кроссовках используется межподошва из литого этиленвинилацетата с резиновыми вставками.Межподошва Injection имеет более толстую и гладкую кожу, чем межподошва из прессованного EVA. Межподошва из впрыснутого EVA имеет более однородную плотность и лучшую детализацию, чем формованная под давлением EVA. Это устройство очень легкое, очень гибкое, но быстро изнашивается. Оснастка для литья под давлением имеет высокую производительность, но пресс-формы стоят более 3000 долларов за каждый размер и требуют дорогостоящего станка. Инструмент для сжатия EVA стоит вдвое дешевле и может быть изготовлен в самом простом прессовом цехе. Этот блок подошвы требует формы для литья под давлением из этиленвинилацетата и пресс-формы для резины.
Клин из EVA
Эта классическая межподошва Die Cut с клином из EVA прикреплена к резиновой подошве, изготовленной методом прессования. Форма верхнего клина EVA обрезается путем нажатия на EVA профильным роликом, в то время как лезвие отделяет нижние слои. Белый слой полируется и приклеивается к резиновому дну. Все три части отполированы, чтобы создать наклонную боковую стенку. Трудоемко, но требовалось очень мало инструментов. Фактически, один нижний инструмент можно обрезать до размеров от 4 до 6.Для этой обуви New Balance требуется резиновый инструмент для сжатия.
Промежуточная подошва из полиуретана
Обувь изготовлена из пенополиуретана прямого крепления. В этом процессе верхняя часть зажимается в верхней части формы. Форма заполняется двумя порциями: сначала формируется подошва, как только дно остынет в течение нескольких минут, вторая порция легкого полиуретана заполняет пространство между верхом и дном. ПУ соединяется непосредственно с верхом. Эта подошва требует формы для литья под давлением из 2 частей полиуретана И машины за миллион долларов.
- Пенополиуретан
- Обычная набивка внутри язычков и воротников обуви. Открытые ячейки пропускают воздух и воду. Может быть очень мягким. Ноу и поролон KFF или K360 Кожа PU Полиуретановое пластиковое покрытие поверх синтетической основы. Это очень распространенный материал для любой современной спортивной обуви.
Резиновая подошва Classic
Классическая обувь с чашечками и цельной резиновой подошвой. Белая боковая стенка и черная резина сливаются вместе за одну операцию.Форма имеет среднюю пластину, позволяющую формировать детали по отдельности, прежде чем резина полностью затвердеет, средняя пластина удаляется, и цвета резины могут сплавиться вместе без грязного шва. Боковой логотип окрашен после литья. Внутри вы найдете вырезанный из пеноматериала EVA кусок. Канавка для шва в форме находится под надрезом, но растяжимая резина легко удаляется после формования. Прошивка каналов производится после сборки. Для этого требуется только резиновая пресс-форма.
Форма подошвы чашки может изготавливаться без вспененного наполнителя внутри.Самая дешевая обувь может иметь резиновый наполнитель ящика для яиц.
Резиновая межподошва ящика для яиц Рисунок ящика для яиц в виде квадратных или ромбовидных стенок может заполнять пятку твердой резиновой подошвы ботинка. Они экономят вес, но обеспечивают прочную подошву. Ящик для яиц также можно использовать для замены пены внутри межподошвы недорогой обуви. Ящик для яиц также можно использовать для выравнивания внутренней поверхности резиновой подошвы, чтобы межподошва, вырезанная из листа, могла правильно прилегать.
ПУ разлитый воздух
Эта классическая межподошва для обуви с воздушной подушкой изготовлена из литого полиуретана, но в этом случае воздушная подушка закреплена в пятке и открыта.Окно — это то место, где зажимы удерживают сумку на месте и не позволяют полиуретановой оболочке закрывать сумку. Резиновая подошва изготовлена методом сжатия, верх черной части — линия разъема формочки. Желтая часть со спецификациями — это та же часть из полиуретана, которая удерживает подушку безопасности, но эта область замаскирована и окрашена. После того, как детали из полиуретана очищены и окрашены, они прикрепляются к резиновым деталям с помощью линии подгонки. Прошивка носочного канала выполняется после сборки. Для этой подошвы требуется резиновый инструмент для сжатия, пресс-форма для подушки безопасности и пресс-форма для промежуточной подошвы из полиуретана.
- Линия разъема или плоскость разъема подошвы Линия в пресс-форме подошвы образуется закрывающимися краями инструмента. Инструмент разделяется по линии разъема. Форма может иметь одну или две плоскости разъема. Из-за линии разъема может растекаться лишняя резина, ее нужно будет обрезать. Узкая плотная линия разъема или плоскость разъема — признак качественной оснастки.
Подошва Cup & Cut & Buff
Эти кроссовки для домашнего футбола представляют собой комбинацию подошвы, кроя и полировки.Резина прижимается, затем клин из этиленвинилацетата цементируется. Затем этиленвинилацетат полируют до уровня резиновой боковой стенки. Эта конструкция более гибкая и легкая, чем стандартная резиновая подошва. Для этой подошвы требуется резиновая пресс-форма.
- Цемент для обуви или контактный цемент: Цемент для обуви обычно представляет собой контактный полиуретановый цемент на основе растворителя или воды. Каждую часть покрывают цементом и дают высохнуть. Затем поверхности прижимаются друг к другу. Нажатие критически важно для хорошего склеивания. ПУ цемент затвердевает за считанные минуты, но полное отверждение может занять несколько дней.Также может называться клеем или клеем.
Классическая вулканизированная подошва
Эта подошва представляет собой стандартную вулканизированную конструкцию обуви. Так делают обувь Vans и так делают Converse All Star. Нижняя часть подошвы приклеивается к верху, затем их оборачивает полосатая резиновая лента. После того, как эта операция сборки завершена, вся обувь подвергается тепловой обработке для отверждения резины, делая соединения прочными. См. «Вулканизированный против холодного цемента» Для этой подошвы требуется резиновая пресс-форма для нижней части и специализированный завод по производству вулканизации.
Литьевая подошва
Эта подошва с футбольными шипами изготовлена методом литья под давлением. Обувь с шипами для футбола, футбола и бейсбола требует жестких поддерживающих подошв с тяжелыми шипами. Очищенная обувь изготавливается методом холодного цемента. Подошва может быть пришита к верху после цементирования. Для этой подошвы требуется пластиковая форма для литья под давлением. Сложные конструкции нескольких цветов требуют дорогостоящей формы, простые конструкции требуют менее дорогих инструментов.Шипы с металлическими шипами или вставками требуют дополнительной формовки. Для этого типа литьевого инструмента требуется специализированный завод по литью под давлением.
Дизайн
На основе Vibram, моих любимых производителей резиновых подошв, которые на самом деле базируются в Массачусетсе. В моем дизайне есть «губа», проходящая по верху подошвы. Подобно вулканизированной подошве, которую имеют Converse и Vans, где нижняя часть подошвы соединяется с верхом, затем полосатая резиновая лента оборачивает их обе, но ближе к подошве с чашечкой с цельной резиновой подошвой.Белая боковая стенка и черная резина сливаются вместе за одну операцию. Как и в случае с подошвой для чашки, я соединил нижнюю и верхнюю часть подошвы в одно целое, сократив процесс изготовления за меньшее количество шагов.
Было важно убедиться, что размер инструмента, который я буду использовать, может поместиться в канавки конструкции подошвы подошвы. is Когда твердая форма (подошва) была готова, я создал два прямоугольника, масштабированных по длине и высоте обрабатываемых восковых блоков, которые я решил использовать. Затем я экструдировал, чтобы соответствовать высоте блока.Затем я сделал копию подошвы и поместил верхнюю половину в один блок, а нижнюю — в другой. Я выстроил их в ряд, чтобы убедиться, что они разделены поровну.
Затем я использовал команду логической разницы, чтобы создать негатив подошвы в обоих блоках, и добавил направляющие с обеих сторон для облегчения выравнивания при забросе.
Форма
Обработано очень красиво!
VCarve
Открыть VCarve -> Создать новый файл
Настройка задания
Подробное описание рабочего процесса VCarve см. На неделе 8
Следует отметить кое-что другое: когда вы импортируете файл в программу, вам необходимо убедиться, что вы следуете по этому пути: Файл -> импорт-> компонент импорта или 3D-модель
Траектории
Настройка материала Очень важно правильно установить ось Z.Высота моих материалов по z составляет 1,5 дюйма, поэтому я установил зазор 0,5 дюйма, погружение z tp 0,25 дюйма, начальное положение z 0,5 дюйма
Траектория инструмента 1
Черновая 3D-обработка
Инструмент выбора
- 1/4 дюйма с верхним вырезом (52-287)
- Тип инструмента: концевая фреза
- диаметр: 0,25 дюйма
- глубина прохода: 0,25 дюйма
- шаг шага: 0,125 дюйма при 50%
- Скорость шпинделя: 16000 об / мин
- Скорость подачи: 1,5 дюйма / сек
- Скорость погружения: 1,0 дюйм / сек
Траектория 2
3D чистовая
Инструмент выбора
- Шаровидный наконечник 1/8 дюйма (13727)
- Тип инструмента: концевая фреза
- диаметр: 0.125 дюймов
- глубина прохода: 0,25 дюйма
- шаг шага: 0,05 дюйма при 24%
- Скорость шпинделя: 14000 об / мин
- Скорость подачи: 3,0 дюйма / сек
- Скорость погружения: 2,0 дюйма / сек
Предварительный просмотр траекторий
Приложение предварительного просмотра траекторий очень полезно для просмотра того, как фрезерный станок с ЧПУ будет выполнять ваши траектории. В итоге я использовал это при настройке шага-овера. По мере уменьшения шага точность резки повышалась.
Литой
SORTA-Clear ™ 37
Каучуки серииSORTA-Clear ™ — это водно-белые полупрозрачные силиконовые каучуки высшего качества (платиновый катализатор), отверждающиеся при комнатной температуре с незначительной усадкой.Sorta Clear 37 имеет твердость по Шору 37A и отличается высокой прочностью на разрыв и разрыв. Этот продукт также предлагает удобство смешивания 1A: 1B по объему.
После некоторых исследований я обнаружил, что правильная твердость по Шору для подошв обуви составляет около 80-90.
SORTA-Clear ™ 37 безопасен для кожи и сертифицирован независимой лабораторией.
Процесс
Изучив паспорт безопасности и технический обзор, я начал с подготовки своего рабочего места с пластиковым покрытием и надел защитные перчатки и очки.Затем я обработал форму средством Ease Release ™ 200 для извлечения из формы. Было важно убедиться, что материалы хранились при комнатной температуре и не оставались открытыми. После того, как я проверил это, я начал с смешивания частей A и B по отдельности, прежде чем смешивать 1A: 1B вместе. После смешивания в течение 3 минут я использовал вакуумный воздух в течение 2-3 минут, чтобы удалить захваченный воздух. Когда я пошел заливать ее в отверстие для заливки двойной формы, смесь была слишком густой и не текла, поэтому я использовал большой шприц, чтобы ввести ее. Видео выше демонстрирует мой процесс.Обратите внимание, что это было сделано после моего первого раунда, поэтому смесь окрашена в красный цвет, а мой конечный продукт, описанный здесь, нет.
Модель-инструктор Лучано Бетольди на фото выше.
Не уверен, можете ли вы сказать, но я действительно люблю обувь, и я всегда хотел разработать и изготовить свои собственные кроссовки, поэтому эта неделя была для меня очень крутой. Теперь я знаю намного больше о подошвах и процессе производства. Возможно, в следующий раз я спроектирую обувь целиком ..
Файлы дизайна
форма
башмак
Полезные ссылки
вдохновение
ссылка
ссылка
Прицелы-DF
Индекс класса
Как делают подошву обуви
Мы считаем само собой разумеющимся, что резина на подошве наших ботинок — материал, который удерживает нас и удерживает устойчивость в теннисных туфлях, кроссовках, повседневных туфлях и даже модельных туфлях.Но как резиновая подошва обуви стала настолько обычным явлением? И как современные производители массово производят миллионы резиновых подошв, которые необходимо производить каждый год, чтобы ноги в мире были безопасными и удобными?
Процесс производства обуви восходит к 1844 году, когда Чарльз Гудиер совершил прорыв после многих лет экспериментов. Он использовал процесс, который он назвал «вулканизацией», чтобы нагреть натуральный каучук, чтобы смешать его с серой — смесь, которая помогла создать тип каучука, который сегодня используется в подошвах обуви.
Мы по-прежнему используем тот же метод вулканизации для изготовления резины для материала подошвы обуви. Комбинация отверждения, смешивания и нагрева Goodyear приводит к появлению прочных подошв, которые мы знаем сегодня.
Процесс производства подошвы обуви
Мы — химическая компания, специализирующаяся на смазке пресс-форм для полиуретановой внутренней облицовки подошв. Мы — небольшая, но важная часть процесса, который помогает обуви завершить свое дело и встать на ноги.В процесс входят:
- Прессование резиновой подошвы: Формы для обуви используются для создания двух частей — стельки и подошвы. Во-первых, на подошве указывается цвет логотипа, а также цвет фона. Средняя пластина закрывается с добавлением красок, а затем сырая резина помещается в форму, где она скоро потечет, образуя подошву. Закройте форму полностью и нагрейте в течение короткого времени, чтобы создать подошву. После извлечения из духовки лишнюю резину срезают, чтобы подошва осталась идеально сформированной.
- Резиновая стелька Прессование: Вместо добавления логотипа и цвета фона для стельки требуется цвет пятки. Добавьте необработанную резину, которая образует переднюю часть, и снова поместите форму в тепло, чтобы сформировать стельку.
- Фьюзинг: Теперь пришло время соединить стельку и подошву, чтобы сформировать законченный продукт резиновой подошвы. После расплавления просто срежьте лишнюю резину и наслаждайтесь красивой (и удобной) резиновой подошвой, которая не так уж отличается от того, как Чарльз Гудиер создавал свою резину более 150 лет назад.
Этот процесс может варьироваться в зависимости от типа подошвы, которую вы создаете, и типа обуви, для которой вы ее создаете. Но основные элементы процесса одинаковы, и вы можете найти этот базовый процесс на заводах по всему миру. Операции смешивания и прессования резины беспорядочные, с большим количеством движущихся частей и большим количеством лишнего, поэтому процесс так часто передается на аутсорсинг. Но поскольку эти фабрики специализируются на производстве резиновых подошв, они могут выполнять большие объемы работы и производить невероятное количество подошв каждый день — эффективно и точно.
Индивидуальные решения для выпуска пресс-форм
Компания W.N. Shaw специализируется на формовании полиуретана, резины и композитных материалов, включая разделительные агенты для подошв как одинарной, так и двойной плотности. С 1985 года мы предоставляем производителям смазочные материалы для нестандартных моделей, повышая ценность наших экономичных решений и передовых технологий.
Мы можем создавать индивидуальные решения для смазки пресс-форм для производителей, работающих в различных отраслях промышленности, в производстве обуви и за его пределами.Мы также можем адаптироваться по мере появления новых технологий и инноваций. Мы разделяем вашу срочность в создании максимально эффективных и доступных процессов.
У нас есть практический опыт, полученный в нашем собственном цехе, где эти специальные разделительные агенты тестируются и разрабатываются. По мере совершенствования этих разделительных агентов мы делаем их доступными для производителей в США и Канаде, а также через дистрибьюторов в Мексике, Китае, Японии, Азии, Южной Америке и Европе. Наш глобальный охват дает нам опыт и знания в реальном времени о том, что работает, а что нет, а также об агентах, продуктах и возможностях, которые больше всего ценят производители.
Качественная продукция
Мы гордимся тем, что продолжаем традицию производства высококачественной подошвы для обуви, отдавая дань уважения наследию Чарльза Гудиера. В процессе производства подошв для обуви мы уделяем особое внимание деталям и добиваемся результатов, которые отражают максимальную заботу. Если вам нужны специальные смазки для форм для производства подошв обуви, обратитесь к W.N. Shaw — компании, которая предлагает опыт, знания и ресурсы для выполнения этой работы.
Свяжитесь с нами
Свяжитесь с нами сегодня по поводу смазок для форм для единичных подошв одинарной и двойной плотности.
FindSourcing — Процесс прямого впрыска (DIP)
Прямой впрыск — это процесс введения расплавленного материала, обычно TPR, PVC или PU, в полость формы для достижения желаемой формы. Этот процесс можно использовать для изготовления подошв, декоративных деталей или для непосредственного соединения подошвы с верхом. Последний известен как процесс прямого впрыска или DIP. Инвестиции в установку DIP-линии высоки из-за стоимости пресс-форм, которые имеют большие размеры, но также должны быть очень точными.Преимуществом DIP является высокая эффективность производства и низкий уровень потерь материала во время производства.
Процесс
Расплавленный материал, обычно полимер, вдавливается в полость формы. Это достигается благодаря высокой скорости и давлению, заставляющим материал реагировать и затвердевать непосредственно в форме. Обычно, но в зависимости от материала, высокая скорость смешивания впрыскиваемого материала приводит к лучшей зернистой структуре и лучшим физическим свойствам. Обычно винт, регулирующий скорость перемешивания, в процессе впрыска вращается со скоростью около 18000 об / мин.Когда материал затвердевает в форме, он принимает желаемую форму и вынимается из формы.
Процесс впрыска полимеров. Форма и окружающая структура определяют цель.
В обувной промышленности, где основное внимание уделяется сборной обуви, обычно используется процесс «прямого формования». При этом готовый верх обуви сначала подготавливается путем обработки последней формы. Эту последнюю форму окружает еще одна форма из двух частей с полостью для подошвы, которая полностью закрывает верх.Эта двухкомпонентная форма включает точку впрыска, через которую будет проталкиваться расплавленный материал, образующий подошву. Когда материал остывает, он прикрепляется к верху, создавая прочную связь.
Форма для литья под давлением для высоких сапог вала, потенциально дождевых сапог
Обычно установка состоит из одной или нескольких машин для литья под давлением, расположенных вокруг карусели пресс-формы с 8, 12 или 16 рычагами. Процесс литья под давлением автоматизирован, но формы необходимо одевать верхом, а после завершения литья готовую обувь необходимо удалить.
Карусель из 32 форм DIP. Любезно предоставлено DesmaОдна из проблем, связанных с процессом впрыска, состоит в том, чтобы обеспечить плотную «линию зажима», обод, где заканчивается подошва, и начинается верх. Это проявляется в кровотечении или «чрезмерном впрыске» материала из подошвы в верх. Обычно допуск форм составляет + -0,25 мм. Если материал превышает это значение, возрастает риск нестабильности линии зажима.
По сравнению с другими процессами, первоначальные вложения в оборудование и пресс-формы требуют сравнительно больших капиталовложений, что делает процесс пригодным для крупных проектов или когда требуется определенная точность.Одна форма и последняя стоит около 800-900 долларов США для производства кроссовок. Форма большего размера, используемая в случае с резиновыми сапогами, стоит дороже.
Одноцветный процесс направленного впрыска с использованием ПВХ.
Многосекционный впрыск
Недавние разработки процесса прямого впрыска позволили удовлетворить потребности в различных характеристиках подошвы в зависимости от местоположения. Вместо того, чтобы впрыскивать только один материал в форму, при экструзии смешиваются два материала с разными свойствами.Это создает подошву, полностью адаптированную к назначению обуви, в высокоавтоматизированном процессе.
Теоретически многосекционный впрыск. Светло-синий более прочный, темно-синий — более гибкий.
Подошва путем впрыска
Процесс изготовления подошвы с прямым впрыском аналогичен тому, что используется форма из двух или более частей с полостью для конструкции подошвы. Впрыснутый материал вводится в форму, образуя подошву. Эти подошвы позже используются в процессе вулканизации или цементирования.
Ротационная машина для литья под давлением подошвы из ПВХ / ТПР
История
1872 г. первая машина для литья под давлением была запатентована Джоном Уизли Хаяттом и его братом Исайей. Это не относилось к обуви, но использовался поршень, чтобы вдавить полимерный материал в форму, состоящую из двух частей, в основном для пуговиц, гребней и держателей для пуговиц.
Разработка более совершенного оборудования для литья под давлением происходила как реакция новых возможностей на разработку все более очищенных полимеров.
В 1946 году Джеймс Уотсон Хендри разработал машину для впрыска шнеков, которая обеспечила большую точность и скорость. В 1970 году он снова попытался усовершенствовать свое собственное изобретение, чтобы теперь работать с газом, что позволило поддерживать более сложные конструкции, в которых полые конструкции могли охлаждаться быстрее. Помимо того, что он был более быстрым, он был более эффективным с точки зрения материалов.
Эскиз термопластавтомата Джеймса Ватсона Хендри, патентный файл, 1955 год
Вскоре после 1972 года процесс был дополнительно улучшен, чтобы также можно было автоматически снимать детали.В это время инжекторные машины работали с гидравлическими двигателями, которые требовали создания давления с помощью постоянно работающих масляных насосов.
В настоящее время большинство машин с прямым впрыском работают от электричества, что дает большое преимущество, заключающееся в том, что энергия не потребляется, когда машина не работает. Цифровые датчики и технологии также позволили оператору машины обнаруживать и проверять результат впрыска, не открывая формы, что еще больше повысило согласованность производственного процесса.
Современные формы для литья под давлением и последние
Производство подошв для обуви | Разделительные агенты McLube
По процессу
Резиновая подошва
McLube® уже несколько десятилетий является ведущим производителем смазок для резиновых форм. Наши смазки для отделения резины в настоящее время используются в Соединенных Штатах и во всем мире для производства прочных, износостойких резиновых подошв для обуви в стиле милитари, защитной обуви и многого другого.
Смазки для резиновых форм McLube® позволили нашим клиентам в производстве подошв для обуви сократить накопление в форме, уменьшив частоту операций по очистке.Смазки для резины McLube® со временем защищают формы от коррозии, особенно во влажном климате, и предотвращают накопление грязи и сажи во время простоя / хранения. Другие преимущества технологии смазки для резиновых форм McLube® включают незначительный перенос, ограниченное накопление в форме и улучшенное качество поверхности. Свяжитесь с McLube® сегодня, чтобы узнать больше о том, что мы можем сделать для обработки резиновой подошвы вашей обуви.
Отливка подошвы одинарной плотности
Одинарные подошвы или подошвы «моноплотности» обычно производятся методом открытой разливки с добавлением разделительного агента, наносимого на каждый цикл.Частота применения разделительного агента в этих процессах может быстро привести к накоплению и засорению формы, особенно при нанесении покрытий на основе воска. McLube® разработала линейку покрытий для производства подошв обуви, которые создают чрезвычайно тонкую разделительную пленку на основе, чтобы ограничить накопление в форме с течением времени. Без быстрого налипания наши клиенты меньше простаивают для очистки и могут отливать больше подошв за смену. Наши микротонкие разделительные покрытия также сохранят мельчайшие детали пресс-формы, улучшая четкость рисунка протектора и позволяя наносить более сложные надписи и графику.Технология смазки пресс-формы McLube® не будет мешать этапам отделки или прикреплению к верхнему башмаку. Наша линейка разделительных агентов для подошв одинарной плотности включает варианты на водной основе и на основе растворителей с настраиваемыми концентрациями, коэффициентами скольжения и уровнями блеска для удовлетворения индивидуальных требований технологического процесса. McLube® также разработала разделительные агенты для литья подошвы одинарной плотности, которые для некоторых производителей обеспечивают несколько смазок на спрей. Свяжитесь с нами сегодня, чтобы получить дополнительную информацию о продуктах и образцы.
Отливка подошвы двойной плотности
Подошвы обуви двойной плотности или «двухплотности» включают в себя подошву и межподошву, которые соединены между собой внутри формы. «Манекен» служит временным верхним покрытием для отливки подошвы и удаляется перед заливкой и отверждением материала промежуточной подошвы по подошве. Разделительные агенты McLube на водной основе и на основе растворителей для подошв двойной плотности разработаны для обеспечения эффективного отсоединения, не мешая склеиванию межподошвы и подошвы или этапам постформовки, таким как покраска и крепление верхней части обуви.Эти покрытия подходят для нанесения на поверхность пресс-формы, а также на манекены и достаточно универсальны, чтобы выделять различные соединения подошвы и межподошвы. Свяжитесь с McLube® сегодня, и один из наших местных технических представителей будет работать с вами, чтобы предоставить идеальный разделительный агент для вашего процесса двойной плотности.
Отлитые под давлением подошвы с прямым креплением
Для литья под давлением требуются разделительные агенты, которые способны прилипать к поверхности формы, а также обеспечивают достаточное скольжение, чтобы способствовать потоку материала через всю полость.Если используется смазка с плохой адгезией к поверхности, материал будет выталкивать покрытие вокруг формы, вызывая вязаные линии и неэффективное высвобождение. Разделительный агент с плохими характеристиками текучести (высокая поверхностная энергия) может вызвать неравномерную толщину подошвы и даже истощение материала в сложных областях полости формы. Нехватка материалов особенно актуальна для процессов подошвы обуви с RIM, которые включают сложные рисунки протектора и рисунки. В то время как определенная степень скольжения необходима для облегчения потока материала, слишком большое скольжение приведет к ухудшению сцепления разделительного агента с поверхностью.
McLube® понимает тонкий баланс между поверхностной адгезией и характеристиками текучести материала, который имеет решающее значение для обеспечения идеальной разделительной способности внутри литьевых форм. Наши разделительные агенты для обработки подошв обуви содержат запатентованные добавки, которые позволяют нашим покрытиям сцепляться с поверхностью формы, обеспечивая непревзойденную долговечность. McLube® также адаптирует коэффициенты скольжения для создания оптимальной поверхностной энергии внутри вашей формы, чтобы способствовать потоку материала, не вызывая линий вязания.
Процессы прямого присоединения составляют большую часть литья под давлением смол и эластомеров в обувной промышленности.Уменьшение количества брака и брака имеет особое значение при операциях прямого прикрепления, поскольку во время этого процесса подошва приклеивается непосредственно к верху обуви; если подошва не освобождается должным образом, верхняя часть обуви также расходуется впустую. McLube® обычно разрабатывает индивидуальный состав для формовщиков с использованием процессов прямого прикрепления, чтобы гарантировать, что подошвы извлекаются точно так, как задумано, и сводится к минимуму брака. Свяжитесь с McLube® сегодня, и наши опытные технические представители и химики помогут вам разработать идеальное покрытие для вашего процесса, а также проведут вас через испытания и внедрение.
Приложения
Поддерживаемые материалы
McLube® предлагает разделительные материалы на основе воды и растворителей для многих материалов подошв обуви, включая натуральный и синтетический каучук, термопластичный каучук (TRP) и полиуретан (системы полиэфира и полиэфира PU), этилвинилацетат (EVA), ПВХ, BPU, и акрилонитрилбутадиенстирол (ABS).
Производители подошв для обуви постоянно разрабатывают новые составы для увеличения прочности, снижения веса и улучшения амортизации.Независимо от того, занимаетесь ли вы исследованиями и разработками в лаборатории или переходите к полноценному производству, химики и технические представители McLube® обладают отраслевыми знаниями и опытом, необходимыми для разработки антиадгезионного агента с индивидуальной рецептурой, адаптированного к вашему новому материалу или процессу.
Металлические формы для распыления в обувной промышленности
Метод, используемый большинством производителей форм для обуви
Изготовление выкройки — это работа изготовителя модели. Могут использоваться самые разные материалы, такие как дерево, гипс, кожа, дерево, покрытое воском, и пробка — самые распространенные из них.Все эти материалы должны выдерживать давление воздуха от пистолета для распыления металла и повышение температуры во время процесса распыления (до 55 фунтов на квадратный дюйм и приблизительно 45-50 ° C). Затем шаблон соответствующим образом устанавливают на деревянное основание, которое образует линию разделения изготавливаемой формы. В качестве альтернативы можно использовать гипс на основе парижа, который позволяет удалить рисунок при нанесении на обратную сторону. Наконец, узор покрывается тонким слоем антиадгезива и полностью высыхает перед нанесением следующего слоя.Обычно необходимо 2-3 слоя. После нанесения разделительного состава необходимо проявлять особую осторожность, чтобы предотвратить любой контакт с поверхностью модели, потому что даже отпечаток пальца будет воспроизводиться при распылении металла.
Оборудование
Metallisation 340 или 140E Arcspray или Mark 73 Flamespray System
Приложения
Наилучшие результаты будут достигнуты при использовании системы Arcspray с узлом распылительной форсунки CG диаметром 1,6 мм.Наилучшая обработка поверхности достигается при использовании формовочного сплава Metallisation 24E для первых 0,40–0,65 мм, за которым следует 1,0 мм чистого цинка. Для получения как можно более плотной струи необходимо использовать настройку тонкой струи.
Во время распыления пистолет следует держать на расстоянии не менее 25 см и, по возможности, под углом 90 ° к рабочей поверхности. На протяжении всего процесса распыления пистолет следует перемещать по рабочей поверхности, чтобы обеспечить равномерное нанесение распыления на рисунок.Рекомендуется следить за тем, чтобы температура формы не превышала 50 ° C. Избыточное нагревание приведет к отрыву распыляемого сплава от рисунка и образованию трещин на поверхности формы при охлаждении. Идеальный метод охлаждения формы — это наличие струи воздуха непосредственно над распыляемой формой. Это будет способствовать охлаждению, а также снизит вероятность попадания частиц пыли под поверхность. Когда будет достигнута разумная толщина — 2,0–3,0 мм, форма готова для нанесения основы.
Опора от напыляемой оболочки
Три основных метода резервного копирования: —
1. Кирксите
Этот метод чаще всего используется при производстве изделий из ПВХ. Сплав на основе цинка выдерживает давление впрыска. Это очень тяжелый материал с весом 6,90 г / см³. Одним из недостатков этого метода является степень усадки кирксита, составляющая около 1%, а также отсутствие адгезионных свойств. Невозможно получить соединение между киркситом и напыляемой оболочкой.
2. Эпоксидная смола с алюминиевым наполнителем
Этот материал можно использовать при производстве полиуретановых подошв, где нет большого давления, и он обеспечивает хорошее сцепление с металлическим напылением. Незначительным недостатком этого метода подложки является низкая теплопроводность, которая должна быть выше при производстве полиуретановых подошв.
3. Уретан с алюминиевым наполнителем
Это один из последних используемых материалов, который также сокращает время производства. Время отверждения составляет всего 30 минут по сравнению с 24 часами для эпоксидных смол.По теплопроводности сопоставима с эпоксидными смолами. Теплопроводность сравнима с эпоксидной смолой и имеет такие же адгезионные свойства.
Наиболее подходящий метод основы зависит от формованного материала; мягкий ПВХ, жесткий ПВХ, полиэфир или полиэстер.
После того, как полость в половине формы для обуви заполнена, мы переходим к крышке или месту сварки формы. При извлечении монтажного блока из формы открывается сварная сторона модели.
Крышка или рант модели
Теперь на чистую, недавно сформированную поверхность, покрытую напылением, необходимо нанести непрозрачный антиадгезионный состав.Это важно для того, чтобы после завершения обе половины формы можно было разделить. Распыление снова повторяют, как и на стороне полости, чтобы сформировать крышку формы и подпорку таким же образом. Теперь форма для обуви готова к открытию и удалению формы, после чего остается полость, которая является ее точной копией.
Удаление модели
Если модель сделана из дерева или пробки, обтянутой кожей, ее обычно нужно «сотрясать» или выламывать из формы. Когда воск используется в качестве покрытия, можно удалить древесину из центра, а затем удалить воск изнутри формы, оставив ее чистой и готовой к производству, и это является преимуществом, когда требуются дублирующие формы.Деревянная часть модели собрана, только воск необходимо заменить.
Обобщить
В связи с изменениями в моде формы для металлического напыления становятся все более популярными. Они дают производителю возможность производить формы в более широком диапазоне стилей и получать обувь от чертежной доски до магазинов в гораздо более короткие сроки. Очень важно производить точные образцы в кратчайшие сроки, чтобы производство продолжалось. Мелкие производители обнаруживают, что формы с металлическим напылением помогают им конкурировать с более крупными компаниями из-за низкой стоимости оборудования и скорости доставки форм.
СПРАВОЧНЫЙ ТЕХНИЧЕСКИЙ БЮЛЛЕТЕНЬ № S: —
2.3.15 Металлизация 24E цинковый сплав
.