Как развивалась технология: история клееного бруса
Клееный брус ― безупречное дерево. Ведь он не гниет, устойчив к перепадам температуры и влажности. Усадка клееного бруса минимальна: 2-4 %. Легкий и экологичный материал. Технология производства клееного бруса появилась не в один момент, а развивалась на протяжении девяти веков.
С чего все началось
Идея склеивания деревянных досок известна еще с XII века в Японии. Чтобы сделать лук дугообразной формы, японские воины склеивали его части из сухого бамбука и различных пород дерева. Оружие получалось более упругим и прочным. В странах Европы в XVI-XVII веках архитекторы и инженеры использовали гнутые деревянные конструкции при строительстве мостов и арок. Составные деревянные части не склеивались, а сцеплялись специальными клиньями, а в XIX веке ― металлическими скобами.
Кто придумал клееный брус
Родоначальником клееной древесины считается немецкий плотник Карл Фридрих Отто Хетцер.
В конце XIX века он начал склеивать казеиновым клеем небольшие доски шириной 3,5 см. В 1906 году Отто Хетцер запатентовал изобретение. В первой четверти XX века клееные деревянные конструкции Хетцера применялись в строительстве жилых домов в Швейцарии. Многие из этих домов сохранились до сих пор. Способ соединения дощечек казеиновым клеем позволил создавать массивные конструкции, но не решил главной проблемы дерева ― неустойчивости к влажности и температурным перепадам. Со временем брусья расклеивались, набухали от влаги, а после ― гнили. После Первой мировой войны дерево уступило место железобетону как дешевому и жесткому материалу.
Европейские технологии
В Европе проблему подверженности дерева атмосферному воздействию решили в 1950-х годах с началом развития химической промышленности. Новые синтетические клеевые составы повысили прочностные и теплоизоляционные качества дерева. Слои досок склеивали таким образом, чтобы направления древесных волокон чередовались.
В Германии совершенствовали методы шипового сращивания и удаления пороков древесины. Выпускались новые станки для различных работ по обработке древесины.
В 1960-х годах в Финляндии братья Саарелайнен наладили технологию индустриального производства клееного бруса для малоэтажного домостроения. Впервые брус стал производиться не только как строительный материал, но и в заводских комплектах. Появились понятия «комплект дома», «сборка дома». Это нововведение повысило технологичность производства. Государство разработало программу поддержки деревянного строительства, ведь клееный брус соответствует современным требованиям экологичного строительства. Финская продукция вышла на мировой рынок. В Хельсинки создавали первые кварталы, микрорайоны из дерева.
В 2000 году в Лахти построили крупнейший деревянный концертный зал и конгресс-холл Sibeliustalo («Сибелиус Холл»).
Со временем помимо Германии и Финляндии клееный брус стали выпускать Австрия, Италия, Швеция, Дания. Одновременно с развитием малоэтажного строительства клееные деревянные конструкции применялись при возведении большепролетных общественных зданий, производственных сооружений, павильонов
Павильон Японии, арх. Фрай Отто. Expo 2000. Ганновер, 2000 годВ Северной Америке широкое применение клееного бруса началось в 1960-х годах. В качестве сырья применялась дешевая древесина березы, клена, амбрового дерева. Появился брус из шпона (LVL ― Laminated Veneer Lumber), разработанный еще в 1935 году.
LVL-брусВ 1990-х годах малоэтажное каркасное строительство из клееного дерева заняло 85 % рынка.
Клееный брус в России
В России исследования клееных деревянных конструкций начались в 1930-х годах для сооружения большепролетных производственных зданий. Первые соединения на дубовых пластинчатых нагелях для сплачивания брусьев создал инженер В. Деревягин. Их использовали для металлодеревянных ферм. Однако с открытием железобетона деревянное производство остановилось. Бетон как строительный материал был дешевле и долговечнее дерева. Во время Великой Отечественной войны разработки клееных деревянных конструкций продолжались в ЦНИПС (Центральный научно-исследовательский институт промышленных строительных материалов). Возводились опытные промышленные конструкции: склады, амбары, производственные помещения.
В 1950-х годах А. Фоломин создал способ сушки и пропитки древесины специальными химическими жидкостями. А. Борщевский описал систему мероприятий по защите дерева от гниения. В это же время при строительстве цехов, спортзалов, мостовых пролетов применяли клеефанерные несущие конструкции (балки, фермы, арки). Клеефанерные балки длиной 12 м использовались в перекрытии цеха в городе Электросталь.
Синтетический клей появился в Советском Союзе на десять лет позже, чем в странах Европы, поэтому промышленный масштаб производства клееных деревянных конструкций был организован в 1970-х годах. В стране работало двадцать заводов. Помимо ели, сосны, лиственницы использовали древесину кедра. Появилась советская школа проектировщиков деревянных клееных конструкций. К концу 1980-х годов в стране выпускалось 100 тыс. м³ продукции в год. После перестройки 1990-х годов из двадцати заводов остался только один.
Брус в XXI веке
Сегодня клееный брус ― высокотехнологичный материал. Из него строят даже многоэтажные здания. В Норвегии уже в этом году можно увидеть самое высокое деревянное здание Mjøstårnet (Mjos Tower). Высота будущего небоскреба 51 ― м. По проекту Voll Arkitekter на восемнадцати этажах разместятся апартаменты, отель, офисы, ресторан, плавательный бассейн и другие общественные пространства.
Mjøstårnet (Mjos Tower), арх. Voll Arkitekter. Брумунддаль, Норвегия, 2018 годКомпания GOOD WOOD стала инициатором строительства самого высокого офисного здания из дерева в России ― GOOD WOOD Plaza. Его высота ― 19,754 м. Все конструкции деревянные и выполнены на собственном производстве компании. GOOD WOOD Plaza занесена в «Книгу рекордов России».
Дома из клееного бруса появились в России в начале 2000-х годов. Сам клееный брус привозился из Финляндии, поэтому стоил очень дорого. Дом из клееного бруса считались роскошью. Наши производители переняли западный опыт изготовления бруса, разработали собственные методы обработки древесины около пятнадцати лет назад, хотя чаще всего используют европейское оборудование. Необходимость привозить материал из-за границы отпала, что существенно снизило стоимость дома. Клееный брус стал популярным в частном домостроении.
Сегодня один из крупнейших производителей клееного бруса в России ― GOOD WOOD. Производство в Зеленограде занимает 10 тыс. м2 и оснащено современным европейским оборудованием.
Идея склеивать древесину существует уже 9 тыс. лет. История клееного бруса связана с развитием клеевой промышленности XX века.
Технология строительства домов из клееного бруса – видео от производителя
Фото монтажа (сборки) дома из клееного бруса 1. Строительство домов из клееного бруса – выбор сырья Строительство домов из клееного бруса в современном мире стало весьма популярным. Это объясняется в первую очередь тем, что дома из клееного бруса, помимо своих качественных характеристик, обладают отличными экологичными показателями. Производство клееного бруса осуществляется на современном деревообрабатывающем оборудовании от ведущих европейских компаний. Прежде чем получить готовый продукт, все поступающее на лесокомбинат сырье проходит целый ряд этапов обработки.
Минуя процесс сортировки, лучшее сырье попадает в лесопильный цех, где располагаются два потока работающие независимо друг от друга. Проводится окорка круглого леса, затем распиловка на высокопроизводительных лесопильных потоках, причем, распиловка исчисляется с учетом распила 2/4 ex log. Мощности же при этом процессе составляют 6-8 тыс. м3/мес. Все отходы лесопильного производства, такие как опилки, древесная кора и другие, комбинат использует для котельного оборудования, мощность которого составляет 1.75 МВт (MAWERA Австрия) и соответственно 1.
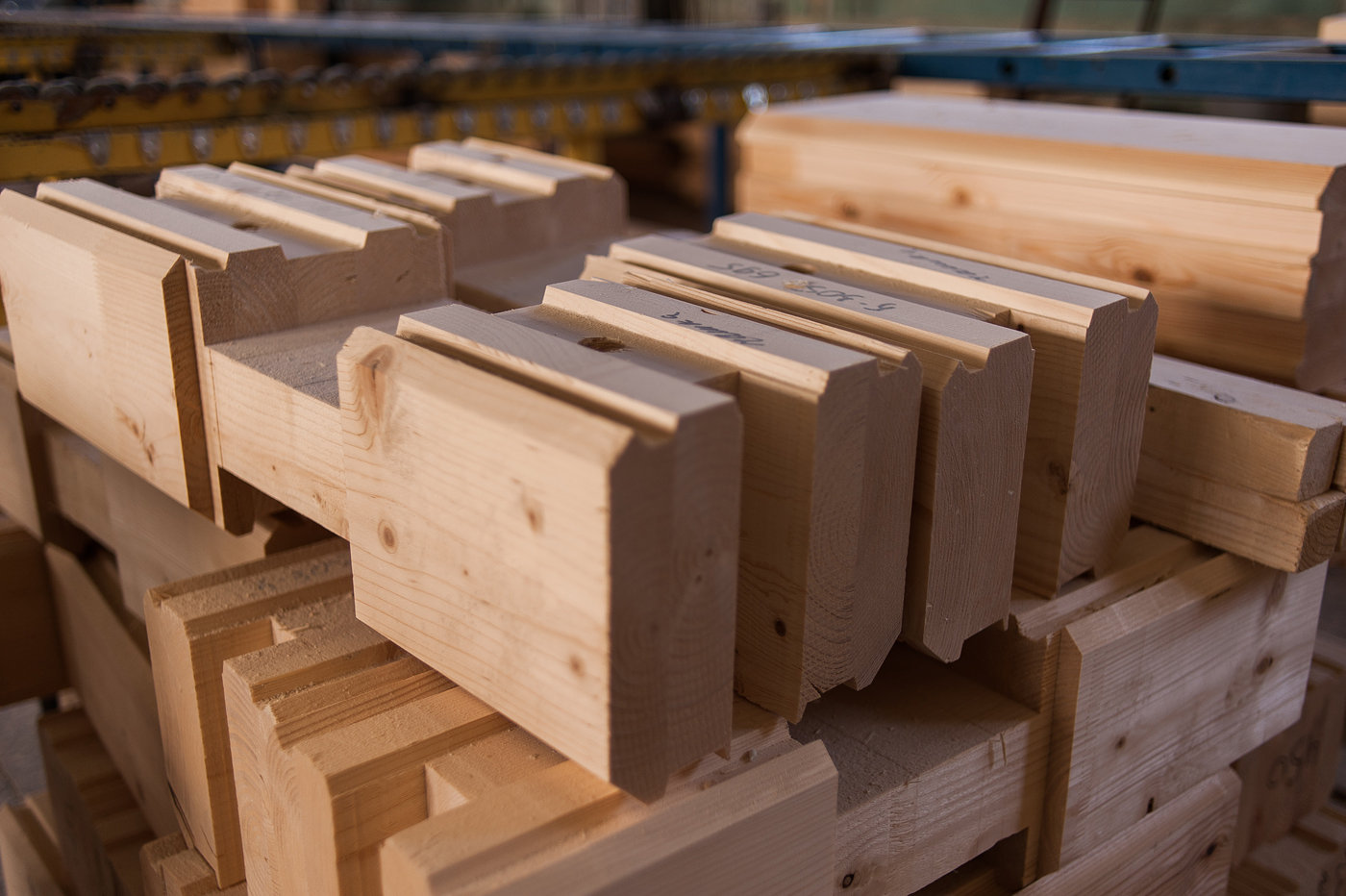
Технология и оборудование для производства клееного бруса
Технология производства и производственное оборудование являются важной составляющей, от которого зависит качество клееного бруса.
В производстве клееного бруса, из которого строит дома компания ХОРОМЫ, используется оборудование европейских производителей — лидеров деревообрабатывающей отрасли.
Производство клееной древесины делится на несколько этапов:
Этап 1. Приемка и сортировка пиломатериала осуществляется на основании ГоСТов и технических условий. Укладка пиломатериала на прокладки, формирование пакета заданных параметров.
Этап 2. Заготовка укладывается в штабель 1000*1000*6050 и сушится до влажности 10-12%. Для этого используется сушильные камеры конвективного типа Mühlböck-Vanicek — современные, надежные, экономичные автоматизированные комплексы для сушки пиломатериалов.
В процессе сушки пиломатериал проходит несколько стадий нагрева и увлажнения для достижения оптимальной равновесной влажности древесины, а также этап кондиционирования, при котором пиломатериал постепенно, в течение нескольких часов, охлаждается, чтобы исключить негативное влияние остаточного напряжения, а также минимизировать коробление и растрескивание материала. Соблюдение мягкого режима сушки материала позволяет наряду с другими технологическими процедурами снизить риск растрескивания материала в процессе эксплуатации клееного бруса.
Этап 3. Сортировка и торцовка пиломатериала. На этом этапе производится повторная сортировка доски на лицевые и внутренние ламели с последующей торцовкой по длине. В данном случае применяется пакетная торцовка.
Этап 4. Калибровка заготовки. Для того чтобы снять остаточные напряжения с заготовки, получить необходимое
сечение и вскрыть не видимые пороки доски производится калибровка заготовки на 4-х стороннем станке.
Четырехсторонние станки Weinig Hydromat и REX немецких лидеров по производству высокотехнологичного оборудования для деревообработки, обеспечивающих идеальную геометрию деталей и безупречное качество строганых поверхностей за счет большого числа строгающих валов и технологии джойнтирования (возможность правки строгальных ножей во время работы станка).
Поддерживать режущий инструмент в идеальном состоянии позволяет заточное оборудование серии Rondamat.
Этап 5. Сращивания и склейка бруса. Отсортированная доска набирается в будущий брус. Доски по отдельности пропускается через клееналивную машину, с последующей загрузкой в пресс.
Автоматизированная линия непрерывного сращивания деталей немецкой компании Dimter, позволяет производить заготовки любой длины, ограниченные лишь габаритами транспорта и пресса для склеивания заготовок.
Большая производительность и идеальное качество соединения гарантируют надежность и эстетичность соединительных швов, а также великолепные прочностные характеристики деталей.
Клееналивное оборудование поставлено в соответствии с маркой клеевой системы представительством концерна Akzo Nobel с услугами контроля производственных параметров и технического обслуживания оборудования экспертами компании.
Вертикальный холодный гидравлический пресс предназначен для склеивания заготовок длиной до 13,6 метров.
Этап 6. Профилирование бруса. Здесь клееный брус поступает в строгальный станок, где осуществляется его строжка под нужный профиль.
Этап 7. Изготовление домокомплекта, согласно проекта. На высокоточном оборудовании производится изготовление будущего дома. С последующей маркировкой всех деталей.
Чашкорезный станок швейцарской фирмы Krüsi с числовым программным управлением позволяет обработать все детали проекта с миллиметровой точностью автоматически загружая данные проекта (после выполненного архитектурного раскроя проекта и автоматического перевода в машинокоды станка) с внешнего носителя информации и исключая влияние человеческого фактора.
Этап 8. Проверка произведенного домокомплекта с учётом спецификации и упаковка в транспортный пакет.
Этап 9. Загрузка продукции в автомашину и отправка из Вологды.
Этап 10. Приемка на объекте заказчика в Беларуси.
Технология производства клееного бруса | Меридиан
По согласованию с заказчиком производится антисептирование бруса антисептиком Rеmmers Германия.
С помощью сканера удаляются сучки, гниль и другие дефекты досок, которые затем подаются на сортировку.
Цикл прессования – 20 минут. На выходе из пресса мы получаем клееный брус, готовый для дальнейшей обработки в различные изделия.
Доска — пиломатериал толщиной до 100 мм и шириной более двойной толщины. Доски изготовляются из брёвен или брусьев в зависимости от технологии лесопиления и размеров применяемых в производстве клееного бруса.
Калибровка (строгание) древесины осуществляется непосредственно после сушки. Качественно проведенная калибровка позволяет выявить такие видимые дефекты, как сколы, обзолы, смоляные «карманы», сучки и т.д. Все обнаруженные дефекты древесины удаляются.
Нанесение клея
После скленивания по длине ламели снова строгаются. тем самым сглаживаются неровности, возникшие при склеивании минишипов. На широкие поверхности ламелей наносится клей, они укладываются друг на друга.
На данном этапе профилированный или строганный клееный брус подается на автоматический чашконарезной станок.Станок производит нарезку деталей Вашего будущего дома, согласно переданному ему машинному файлу. На выходе на каждое изделие наносится маркировка.
Со склада хранения наша продукция отгружается потребителю с использованием только «мягких строп» исключающих повреждение готовой продукции.
На горизонтальном прессе осуществляется склеивание обработанных ламелей по пласти на гладкую фугу прессованием с равномерно распределенным усилием для исключения непроклеенных мест и разнотолщинности клеевого шва.
Разметка
В местах недопустимых дефектов сучков, трещин, проростей и смоляных кармашков специальным флюоресцентным мелком наносятся маркеры, отражающие излучение, генерируемое светодиодом. Это отражение улавливают сканеры, а станок автоматически удаляет дефекты.
Сортировка
Заготовки сортируются:- на два сорта – для наружных слоев клееного бруса (длиной от 500 мм. ) и — для внутреннего слоя ( длиной от 300мм).- при склеивании на шип важно, чтобы разница во влажности между соседними элементами не превышала ±1%.
Сращивание
Заготовки без пороков и дефектов попадают на линию сращивания: на концах ламелей, различных по длине, вырезаются минишипные соединения затем с помощью клеенананосящей машины наносится клей и под давлением соединяют ламели длиной до 13,5 метров.
Брусья сортируют, высушивают методом камерной сушки до влажности дальнейшего применения (12±2%) и проверяют на соответствие стандарту прочности DIN 4074-S10.
Производство домов из клееного бруса в Санкт-Петербурге
На этой странице мы расскажем о том, как производится клееный брус на нашем высокоэкологичном производстве. Технология производства представляет собой ответственный и сложный процесс, который начинается ещё на лесном участке в процессе отбора сосновых бревен. Они должны отвечать необходимым требованиям технологии производства.
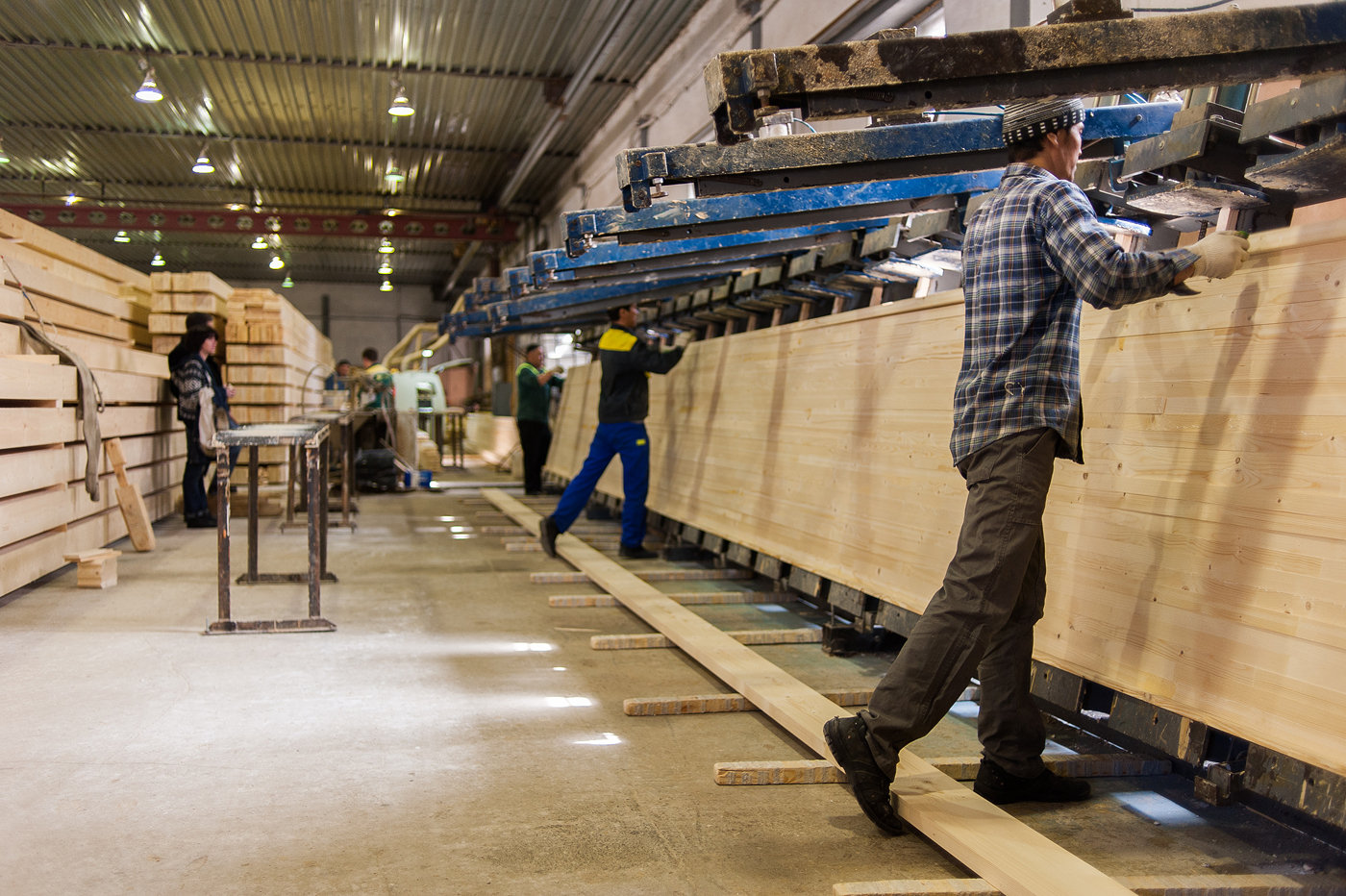
Этапы изготовления клееного бруса:
- Распиловка леса
- Сушка полученных заготовок до влажности 12±2%
- Калибровка заготовок
- Устранение дефектов
- Сращивание ламелей
- Калибровка досок
- Склеивание заготовок по плоскости
- Пресс
- Строгание полученных заготовок
- Покрытие специальными защитными составами
- Торцовка
- Зарезка соединений (угловых)
- Сверление отверстий
- Покрытие соединений защитными составами
Распиловка леса
Сосновые бревна сортируются по свойствам и размерам в цеху, где также отбраковываются неподходящие бревна, которые в дальнейшем распускаются на доски. Все полученные доски тщательно осматриваются на присутствие каких-либо дефектов, которые во время производства клееного бруса не допускаются.
Сушка заготовок
Сушка является 2-м этапом изготовления дома из клееного бруса. На нашем производстве клееного бруса сушильные камеры представляют собой автоматизированные сложные комплексы, вместимость которых за 1 загрузку составляет 900 кубометров. Такие объемы полностью обеспечивают завод материалом, при этом насыщая возрастающие потребности строительного рынка.
Под постоянным присмотром автоматики доска сохнет примерно 7-10 дней, после чего она имеет оптимальную влажность 12%. Также стоит отметить, что ее геометрические размеры сохраняются, а не выявленные дефекты проявляются.
Калибровка полученных заготовок
После сушки доска проходит отбор по качеству у специалистов. На следующем этапе производства домов из клееного бруса доске придается идеальная форма по действующим стандартам. Доска строгается, в результате чего удаляются мелкие неровности.
Устранение дефектов
Следующим этапом в производстве профилированного клееного бруса является устранение маленьких дефектов. Такие дефекты отмечаются оператором при помощи мела, после чего станок их удаляет автоматически. Часто такой процесс осуществляется вручную.Сращивание ламелей по технологии мини-шип
Далее из досок создаются заготовки-ламели. Для постройки домов из клееного бруса используются изделия длиной от 6 до 12 метров. Ламели такой длины сращиваются, из которых в дальнейшем клеится брус, а из него в свою очередь делается дом.
Калибровка досок
Чтобы поверхность ламели отличалась высоким качеством и точностью, от которой зависит прочность склейки, заготовки обрабатываются на 4-стороннем строгальном станке.
Склеивание заготовок по плоскости
На следующем этапе производства клееного профилированного бруса осуществляется операция склеивания. Такой процесс выполняется специальной машиной, которая смешивает клей и обеспечивает его попадание на заготовки. На видео вы увидите как выполняется склеивание по правильной технологии без клеевых комочков с равномерной толщиной слоя, благодаря чему обеспечивается высокое качество склейки. Под пресс ламели поступают в определенном порядке.
Пресс
Далее при помощи пресса создается необходимое давление для кристаллизации клея, которое должно составлять 16 кг/кв. После такой процедуры получается полуфабрикат для элитного строительства, который отправляют на склад на 72 часа, чтобы клей получил нужную прочность. После этого заготовки отправляются на 2-ой участок производства домов, сделанных из клееного профилированного бруса.
Строгание полученных заготовок
Дальше клееному брусу придается безупречная форма при помощи 4-стороннего строгального станка.
Покрытие специальными защитными составами
Следующий этап заключается в защите поверхности от различных вредных воздействий. Для такой цели используется специальный пропиточный состав под названием «Remmers Imprägniergrund GN». С его помощью дереву не страшны жуки, грибок и другие опасности.Торцовка клеенного бруса
Клееный брус торцуют по размеру, исходя из размеров конкретного дома. Такая операция выполняется с высокой точностью, так как от данного процесса зависит качество сборки. Важным моментом считается качество реза, точность режущего инструмента и отсутствие биения.
Зарезка соединений (угловых)
Ни один производитель клееного бруса не может похвастаться такой технологией зарезки угловых соединений, которая есть у нашей компании. Благодаря такой разработке дома не продуваются по углам, что очень важно. При этом точность сборки является недосягаемой для других строителей.
Сверление отверстий
Под стяжки и проводку сверлятся отверстия по проекту.
Покрытие соединений защитными составами
Чтобы защитить брус от различных биологических угроз, угловые соединения пропитывают специальным пропитывающим составом. Этот этап производства домокомплектов из клееного бруса является последним.Теперь вы знаете как изготавливается клееный брус и каким образом с линии выходит готовый к сборке
домокомплект, который в дальнейшем нужно только погрузить, перевезти на место постройки и собрать.Технология производства клееного бруса
Изготавливается клееный брус из деревянных досок, которые склеиваются между собой в направлении, параллельном волокнам. Возможно производство одного клееного бруса из разных пород дерева. К примеру, внешние ламели могут быть из лиственницы, в то время как на внутренние идет сосна. Чаще всего для клееного бруса используют сосну и ель, несколько реже клееный брус изготавливается из лиственницы или из кедра.
Технология производства клееного бруса включает в себя несколько последовательных действий. Начинается всё с сушки пиломатериала, затем делается черновое прострагивание, при котором выявляются дефекты. После чего выполняется торцовка, при которой обнаруженные дефекты удаляются. Доска нарезается по размеру будущего клееного бруса и производится торцевое сращивание ламели. Затем ламель калибруется и выполняется собственно склеивание бруса, который в свою очередь калибруется и профилируется. Наконец, клееный брус из лиственницы, сосны, ели или кедра подвергается окончательной торцовке и прострагиванию.
Рассмотрим некоторые этапы производства более детально. Вначале заготовки в виде отрезков бревен попадают на производственные линии, где их распиливают на доски. Оборудование настраивается таким образом, чтобы получить наибольшее количество досок из одной заготовки. Полученные доски укладывают в сушильные камеры, где они находятся восемь-девять дней. Быстрая сушка древесины проводится с помощью конвекционных потоков воздуха. Окончательная влажность досок составляет примерно 8-12%, это намного ниже, чем у цельных бревен после высушивания.
Производится зрительная проверка материала на наличие дефектов. Найденные поврежденные участки вырезаются, остаток сращивается методом мини-шипа. Брус, изготовленный из сращенных ламелей, достигает длины 12 метров и таким образом получается заметно длиннее бруса, изготовленного из цельных досок.
После сушки досок и обработки антисептиками и составами против горения, их остругивают по первому классу чистоты. В итоге получаются специальные собранные из кусков доски, которые профессионалы называют ламелями. Эти ламели склеивают в готовый брус на специальных прессах под давлением. В брусе может быть от 2 до 5 ламелей, так что клееный брус можно сделать довольно толстым, его максимальная ширина оказывается равной 230 мм, а высота — 320 мм. Ламели склеиваются специальным клеем.
Это может быть полезным:
Клееный брус — современный высокотехнологичный строительный материал, обладающий всеми качествами, присущими дереву, а также рядом дополнительных достоинств. Клееный брус является самым прочным строительным материалом, применяемым для стен жилых домов. Также этот материал используют для изготовления оконных блоков, столбов, перекрытий, напольных покрытий, подоконников, ступеней и пр. Для его производства используются хвойные породы древесины, в основном – ель и сосна. Наилучшими качествами обладают стройматериалы, изготовленные из северной древесины. Они отличаются прочностью и долговечностью.
Строительство домов из клееного бруса является быстро развивающимся направлением и имеет ряд преимуществ, к примеру, по сравнению с домами, сделанными из массивной древесины.
Производство клееного бруса состоит из следующих основных этапов:
|
Клееный брус — обзор
После изучения различных видов разрушения древесины в этом разделе рассматривается разрушение структурных соединений, то есть когда соединяются различные элементы деревянной конструкции, такие как стойки или балки. Соединение этих элементов — самая сложная часть деревянной конструкции. Чтобы избежать обрушения здания, необходим точный расчет и проектирование соединений.
В этой главе разрабатываются только критерии отказа последнего, механические соединения, поскольку это гораздо более распространенная система.
2.1 Виды отказов механических деревянных соединений
Геометрия соединения, материал основных элементов (только деревянных или в сочетании с другими элементами, такими как стальные пластины), тип используемого крепежа и его свойства, расстояние между крепежными элементами , а угол между нагрузкой и ориентацией волокна являются наиболее важными параметрами соединения.
Соединения часто выполняются, например, с помощью гвоздей, дюбелей, болтов, (саморезов) винтов, вклеенных стержней или соединителей, работающих на срез.Количество креплений в соединении зависит от типа используемого крепежа. Крепежные детали малого диаметра, такие как гвозди или заклепки, часто используются в большом количестве в одном соединении, тогда как крепежные детали большого диаметра, такие как болты, вклеенные стержни или соединители, работающие на сдвиг, могут использоваться даже по отдельности.
Возможны два основных режима разрушения: пластичный и хрупкий. Как объяснялось в разделе 1, сжимающие напряжения связаны с пластическим разрушением, а напряжения растяжения и сдвига могут привести к хрупкому разрушению.Поскольку хрупкое разрушение происходит внезапно, его следует избегать. Пластичное разрушение — это долговременное разрушение, развивающееся в диапазоне пластмасс, которое может быть обнаружено заранее, чтобы пользователи здания могли покинуть здание до того, как конструкция рухнет. Таким образом, желаемое пластичное разрушение деревянных соединений достигается, когда разрушение происходит из-за крепежа, и предотвращается разрыв дерева.
Пластичность в целом описывает способность конструкции подвергаться большим деформациям в пластическом диапазоне перед ее разрушением.Его часто определяют как отношение предельного вытеснения к пределу текучести [30].
(7,14) μ = umaxuy
Хрупкие разрушения связаны с разрушением древесного материала (раздел 1). Поскольку этот вид разрушения является хрупким, различные нормы проектирования всегда стараются его избежать, особенно когда он возникает перпендикулярно напряжениям в зернах.
Отказ структурных деревянных соединений может быть отнесен к трем различным категориям в соответствии с соотношением между пластической способностью крепежа и емкостью древесины, как показано на рис.7.12.
Рисунок 7.12. Возможные виды отказов в деревянном соединении [31].
- •
Режим хрупкого разрушения. Когда происходит разрыв древесины, застежка находится в диапазоне упругости.
- •
Смешанный режим отказа. Разрушение древесины происходит в пластическом диапазоне деформации крепежа.
- •
Режим разрушения из-за вязкости. Разрушение происходит из-за предельной прочности крепежа после деформации.Никакого разрыва древесины не происходит.
Режимы хрупкого и смешанного разрушения весьма схожи с феноменологической точки зрения, поскольку в обоих случаях древесина разрушается. Заметная разница между ними заключается в фактической нагрузке на застежку по отношению к ее пластической и предельной прочности.
2.1.1 Режим вязкого разрушения
На рис. 7.13 показаны различные возможные режимы разрушения соединения, нагруженного при растяжении параллельно волокну. Первый вариант (заделка) — единственный, который отличается пластичностью.В остальном — разные механизмы разрушения древесины, что приводит к хрупкому разрушению.
Рисунок 7.13. Возможные виды отказов в механическом соединении [32].
В настоящее время расчет прочности механических швов древесины в режиме заделки в основном выполняется в соответствии с так называемой европейской моделью текучести, первоначально предложенной Йохансеном [33]. Принимая во внимание пластический момент застежки и прочность древесины на заделку, можно получить различные возможные пластические механизмы, учитывая геометрию элементов соединения.Эта модель действительна только для соединений, которые разрушаются пластичным образом, в которых прочность древесины выше, чем у крепежа, но не учитывает разрушение из-за хрупкого разрушения древесины.
Прочность заделки определяет силу, приложенную к дереву застежкой. Есть много различных предложенных формул, в основном основанных на экспериментальных тестах. В зависимости от характерной плотности ρ k бруса и диаметра d крепежа, прочность заделки f h , 0, k дюбельного крепежа параллельно к зерну рассчитывается согласно Еврокоду 5 [34] как:
(7.15) fh, 0 = 0,0821−0,01dρ,
, где f h , 0 — прочность заделки параллельно волокну в Н / мм 2 , ρ — плотность древесины в кг / м 3 , а d — диаметр дюбеля в мм.
Jorissen [35], Ehlbeck и Werner [36] или Jumaat [37] предлагают аналогичные формулы с разными факторами, в то время как другие, такие как Sawata и Yasumura [38] и Американская национальная спецификация дизайна [39], предоставляют более простые формулы, связанные только с к плотности древесины. Формулы коррекции предложены в Еврокоде 5 [34] для учета других углов между приложенной нагрузкой и ориентацией волокон древесины.
Для расчета общей несущей способности соединения параметр, называемый эффективным числом n eff , появляется в большинстве проектных кодов, например, в Еврокоде 5 [34]. Этот параметр учитывает групповой эффект застежек стыка. Когда крепежные детали расположены близко друг к другу, нагрузка распределяется неравномерно, и на самом деле некоторые из них становятся более нагруженными.По этой причине количество учитываемых эффективных крепежных элементов меньше фактического. Чем меньше расстояние между застежками, тем выше групповой эффект; следовательно, общая емкость сустава уменьшается.
Как уже было сказано, необходимо избегать хрупкого разрушения древесины, чтобы обеспечить безопасность зданий. Чтобы способствовать пластическому разрушению, Еврокод [34] и другие стандарты проектирования устанавливают минимальные значения расстояния между крепежными деталями и краями. Однако этой процедуры недостаточно, чтобы гарантировать, что вязкое разрушение произойдет раньше, чем хрупкое.Необходимо более глубокое изучение различных режимов хрупкого разрушения, чтобы получить фактическую мощность режима хрупкого разрушения соединения.
2.1.2 Вид хрупкого разрушения
В зависимости от угла между приложенной нагрузкой и ориентацией волокон древесины существует два различных семейства хрупких повреждений: нагрузка параллельна или перпендикулярна волокнам. Для случаев с разными углами приложенная сила должна быть разложена на эти две составляющие.
2.1.2.1 Параллельно волокну
Наиболее важным видом хрупкого разрушения для соединений, нагруженных параллельно волокну, является сдвиг блока, также известный как «разрыв блока» или «сдвиг с пробкой». На рис. 7.14 показан такой тип отказа в экспериментальных испытаниях гвоздевых соединений, проведенных Danielsson et al. [40].
Рисунок 7.14. Блочные испытания на сдвиг, проведенные Danielsson et al. [40].
Для оценки этого режима разрушения периметр области соединения определяет граничную область, образованную тремя различными плоскостями разрушения, как показано на рис.7.15, которые выверены для соответствующих мощностей:
Рисунок 7.15. Эскиз отрыва блока нагруженными плоскостями [31].
- •
Плоскость растяжения головки.
- •
Нижняя плоскость сдвига. Эта плоскость учитывается только в случае соединения гвоздями или шурупами, где крепеж не выступает из древесины.
- •
Две боковые плоскости сдвига.
В зависимости от геометрии соединения, этот вид хрупкого разрушения может привести к разрывам различных конфигураций, как показано на рис.7.16.
Рисунок 7.16. Возможные режимы хрупкого разрушения при отрыве блока [31].
Несколько авторов [41–44] предложили разные методы для прогнозирования емкости трех плоскостей разрушения с учетом различных факторов и режимов измерения площади разрушения, таких как эффективная толщина t eff боковой поверхности. и головные самолеты. В некоторых предложениях поверхность хрупкого разрушения изменяется путем изменения так называемой «эффективной толщины» t eff .Для режима хрупкого разрушения Зарнани и Кенневилль [45] предложили определять эффективную толщину древесины по упругой деформации крепежа, моделируемой как балка на упругопластической основе. В смешанном режиме разрушения древесина выходит из строя после некоторого прогиба гвоздей, но до того, как они достигают полной податливости. В этом режиме разрушения эффективная глубина древесины значительно меньше, чем та, которая связана с режимом хрупкого разрушения, и она определяется основным режимом разрушения крепежной детали.Это подход, применяемый в Еврокоде [34], который не делает различий между различными видами хрупкого разрушения.
В качестве примера Еврокод 5 [34] рассматривает отдельно прочность на растяжение и сдвиг по двум формулам, принимая в качестве максимальной прочности соединения максимальную из них:
(7,16) Fbs, Rk = max1.5Anet, tft, 0, k0.7Anet, vfv, k
, где F bs , RK — емкость стыка, A net , t и A net , v — это чистые площади, подверженные растягивающим и касательным напряжениям, соответственно, f t , 0, k — характерная прочность на растяжение вдоль волокон древесины, а f v , k — это характерная прочность древесины на сдвиг.Оба A net , t и A net , v зависят от геометрии соединения и эффективной толщины t eff крепежного элемента, который в Еврокоде определяется из режима пластической текучести. Недавно Зарнани и Кенневилль разработали альтернативное предложение [45]. Эта процедура получает пропускную способность из модели жесткости для трех плоскостей разрушения, как показано на рис.7.15. Нагрузке на соединение противостоят три рассматриваемых плоскости, и поэтому она распределяется пропорционально их относительной жесткости. K h , K b и K l — жесткость плоскостей головного, нижнего и бокового разрушения соответственно. Несущая способность соединения по дереву P w — это нагрузка, которая приводит к более раннему выходу из строя одной из сопротивляющихся плоскостей.
В проекте будущего нормативного документа Новой Зеландии [46] рассматриваются все эти возможные режимы хрупкого разрушения гвоздевых соединений. Он включает в себя метод жесткости для соединений с небольшими крепежными элементами и более простой метод для стыков с большими крепежными элементами, такими как дюбели.
Помимо сдвига блока, другими возможными видами хрупкого разрушения для направления, параллельного волокнам, являются сдвиг рядов и чистое растяжение, также изображенные на рис. 7.13. Разрушение рядного сдвига аналогично блочному сдвигу, но каждый ряд крепежных элементов ломается отдельно.В результате плоскость натяжения намного ниже, но плоскости бокового сдвига увеличиваются в зависимости от количества рядов. Сетевое натяжение возникает, когда вся секция деревянного элемента ломается в плоскости растягивающей головки. Это связано с прочностью плоскости головы на растяжение.
2.1.2.2 Перпендикулярно волокну
При нагрузке перпендикулярно волокну вид отказа соединения — расщепление. На рис. 7.17 показано разрушение при раскалывании при испытании заклепочного соединения, выполненном Зарнани и Кенневиллем [47].
Рисунок 7.17. Тест на расщепление, проведенный Зарнани и Кенневиллем [47].
Способность древесины противостоять растягивающим напряжениям, перпендикулярным волокнам, действительно мала (как объясняется в разделе 1), и поэтому даже небольшая нагрузка может привести к поломке. Обычно это связано с любой поперечной нагрузкой, перпендикулярной волокну, как показано на рис. 7.18.
Рисунок 7.18. Рисунок сустава, подверженного расщеплению [48].
Было сделано несколько предложений для получения разделительной способности соединения.Среди них можно выделить две основные группы предлагаемых формул:
- •
Геометрические формулы или формулы напряжений. В их основе лежат геометрические параметры соединения и свойства материала. Примерами являются формулы в немецком стандарте [49] и Еврокоде 5 [34].
- •
Формулы, полученные энергетическим методом. Эта группа предложений получить емкость за счет энергетического подхода в рамках линейной механики упругого разрушения.На этой теории основаны модели, предложенные ван дер Путом и Лейтеном [50], Баллерини и Рицци [51], Зарнани и Кенневиллем [47].
Различные подходы к проектированию учитывают разные факторы и требуют различных дополнительных ограничений. В качестве примера в модели Еврокода 5 [34] рассматривается следующая геометрическая формула:
(7,17) V = 14bwhe1 − heh,
, где V — прочность на сдвиг одной из сторон соединения, b — толщина деревянного элемента, w — коэффициент модификации, зависящий от типа крепежа, h — общая высота деревянного элемента, а h e — высота, подверженная растяжению. напряжение и определяется как расстояние между кромкой и последним нагруженным крепежным элементом, как показано на рис.7.18.
Клееный шпон (LVL) как строительный материал
Опубликовано в июле 2016 г. | Id: FAPC-163
От Салим Хизироглу
Клееный брус (LVL) — один из наиболее широко используемых изделий из конструкционной древесины. для применения в строительстве.Это композитный продукт, изготовленный из нескольких тонкие слои шпона, совпадающие по длине с готовым пиломатериалом. Этот информационный бюллетень обобщает основные этапы производства, преимущества и недостатки LVL по сравнению с другими конструкционными изделиями из древесины.
ПроизводствоLVL началось в 1941 году.Он был сконструирован в части самолетов и изготовлен из шпона ели ситкинской толщиной 3,6 мм. В связи с большим спросом на LVL лес USDA Лаборатория продуктов провела значительный объем исследований, связанных с улучшением своего прочностные свойства. Пихта Дугласа — наиболее часто используемое сырье для производства LVL, в дополнение к желтому тополю, южной сосне и другим хвойным породам в США. Сосна лучистая и каучуковое дерево широко используются в Новой Зеландии и Юго-Восточной Азии. страны соответственно.
LVL Производство
Листы шпона толщиной от 2,5 мм до 4,8 мм производятся методом ротационного лущения. техника. Типичная толщина шпона для производства LVL составляет 3,2 мм. Ротационный пилинг бревна производится на токарном станке, который включает геометрию и позиционирование нож как основные параметры изготовления немаловажную роль в качестве шпона.Например, угол наклона выбранного ножа составляет примерно 23 градуса для древесина хвойных пород для эффективного отшелушивания.
Прижимная планка оказывает определенное давление на поверхность шпона, поэтому он будет постоянно отслаиваться от бревна с одинаковой толщиной и без никаких трещин.На рисунке 1 представлена схема типичного производства лущеного шпона методом ротационной лущения. с фиксированным носиком и ножом. Сторона фанеры рядом с острием ножа называется свободной стороной, а другая сторона — плотной стороной. Здесь очень много мелкие трещины на незакрепленной стороне шпона из-за чеков на токарном станке, идущих параллельно зерно.
Рисунок 1. Производство лущеной фанеры.
Болт, который представляет собой короткое бревно, в зависимости от его диаметра, может занять от 5 до 10 секунд. очистить до того, как его сердечник разрядится и зарядное устройство будет готово к следующему циклу. Сплошные ленточные листы шпона обрезаются до определенной ширины и сушатся до заданное содержание влаги с помощью струйных сушилок.Горячий воздух подается на поверхность листы шпона и влага отслаиваются, снижая общую влажность облицовывать фанеру до целевой точки в струйной сушилке. Обычно шпон пихты Дугласа толщиной 3 мм. может потребоваться 10-13 минут, чтобы снизить его влажность до 8-10 процентов. фигура 2 показана типичная струйная трубчатая сушилка.
Рисунок 2. Струйная сушилка для шпона.
В целом производство LVL аналогично производству конструкционной фанеры; Тем не менее Основное различие между двумя продуктами — ориентация волокон каждого шпона. В случае фанеры нечетное количество слоев шпона накладывается друг на друга, поэтому конечный продукт не только будет иметь лучшие механические свойства, но и будет размерно более стабильный.В случае LVL больше виниров монтируется вдоль в продольном направлении, поэтому он будет иметь свойства, аналогичные свойствам массивной древесины, потому что каждая пластина параллельна оси платы, как показано на рисунке 3.
Рисунок 3. Состав LVL.
Дефекты на каждой облицовке устраняются в процессе обрезки. Даже если дефекты остаются на каждом листе шпона, случайное распределение таких дефектов при сборке шпона сделает конечный продукт более однородным и сравнимым по прочностным характеристикам из высококачественного пиломатериала.После нанесения наружного клея, обычно фенолформальдегида. к поверхности каждого листа шпона, они собираются и прижимаются при температурах от 250 до 450 градусов по Фаренгейту.
По сравнению с прессом для фанеры, прессы LVL длиннее. Линия для прессы может быть периодического или непрерывного действия.Пресс периодического действия может иметь одно или несколько отверстий, которые более эффективен для производства LVL меньшей длины. Однако на большинстве заводов используется линия непрерывного прессования. Заготовки производятся шириной до 6 футов с максимальной транспортировкой. длина 80 футов. На рисунках 4 и 5 показана типовая схема производственного процесса LVL.
Рисунок 4. Технологическая схема LVL.
Рисунок 5. Этапы изготовления LVL.
LVL Универсальность
Клееный брус — универсальный продукт на древесной основе.Вместе с фанерой, пиломатериалы или плиты с ориентированной стружкой (OSB), LVL могут использоваться для многих структурных применений. Некоторые из наиболее популярных применений LVL включают двутавровые балки, перемычку, ободья, кузов грузовика настил, дорожный указатель, балка, ферма, специальные приложения, такие как скейтборды, и изготовленные на заказ панели для морского применения.
Преимущества
Основными преимуществами LVL являются его размер, форма, высокие прочностные свойства и бюджетный.Размер LVL не ограничивается размером бревна, в связи с методом изготовления. LVL по своей плотности является одним из самых прочных строительных материалов на основе древесины. Потому что изготавливается однородного качества с минимальным количеством дефектов. или даже распространение дефектов, механические свойства конечного продукта могут быть предсказано. В общем, LVL может производиться в разных формах в зависимости от того, для чего он будет использован.Он также имеет большое преимущество в том, что эффективно использует древесные ресурсы.
Недостатки
Напротив, LVL имеет ряд недостатков по сравнению с древесными композитами. Повышение силы Свойства LVL по уплотнению шпона во время прессования очень ограничены. Хотя его размерная стабильность лучше, чем у цельной древесины, продукт может привести к некоторым дефект, например коробление, если он неправильно хранится на складе.Также LVL требует больших капитальных вложений, чтобы иметь относительно низкую стоимость производства. Следовательно, высокий спрос необходим для рентабельной работы.
Дополнительная информация
Подробную информацию о производстве LVL и его свойствах также можно найти в следующей литературе:
Смульский, С.(Ред.) (1997). Конструкционные изделия из дерева. Фонд исследований PFS: Мэдисон, Висконсин.
Бойер, Дж., Смульски, Р., и Хейгрин, Дж. (2007). Лесные товары и наука о древесине. Издательство Блэквелл: Бостон, Массачусетс.
Болдуин, Р.(1995). Фанера и изделия из шпона, технологии производства. Миллер Фримен: Сан-Франциско, Калифорния.
Американская фанерная ассоциация. Ассоциация инженерной древесины. Получено с www.apa.wood.org
Салим Хизироглу
FAPC Специалист по изделиям из дерева
Была ли эта информация полезной?
ДА НЕТ Свойства масла семян коноплиСуществует более 40 сортов конопли.Коноплю можно выращивать для получения семян, клетчатки или масла. Конопля может использоваться в пищевых продуктах или составах кормов при условии, что продукты одобрены Управлением по контролю за продуктами и лекарствами (FDA) для пищевых продуктов и Ассоциацией американских чиновников по контролю за кормами (AAFCO) для кормовых продуктов. Семена конопли и масло семян конопли можно использовать в пищевых продуктах.
Сельскохозяйственные культурыПищевая промышленностьПищевые продуктыЗерновые и масличные культуры ПОСМОТРЕТЬ ВСЕКлееный брус — Технология производства деревянных панелей
Клееный брус — Технология производства деревянных панелейДепартамент маркетинга лесных товаров
Технология производства деревянных панелей
л В л
Брус клееный
Обзор продукта, производства и рыночной ситуации
Ноябрь 1998 г.
Эрья Неувонен
Минна Салминен
Яни Хейсканен
Миха Хохстрате
Маттиас Вебер
Содержание 1.Определение |
Фиг.1 Oekozentrum NRW, Хамм, Германия
1. Определение
Клееный брус (LVL) представляет собой слоистый композит из древесного шпона и клея. Следовательно, его можно рассматривать как продукт на основе шпона.
2. Введение
LVL — это универсальный продукт, сочетающий в себе лучшие современные технологические процессы и эстетическую красоту натурального дерева. В течение нескольких лет он структурно использовался в Северной Америке и во многих европейских странах.
LVL состоит из параллельных слоев шпона, склеенных и обработанных вместе, чтобы сформировать материал, по толщине похожий на пиломатериал. Отличительная разница между LVL и фанерой заключается в ориентации слоев шпона, как показано на Рисунке 2.
Рис. 2 Ориентация слоев: LVL по сравнению с фанерой
LVL представляет собой новую технологию в использовании древесины, и ее производство постоянно растет, и в разных местах ведется большая работа по развитию как методов производства, так и применения LVL.За последние двадцать лет LVL стал важным новым продуктом, который вызвал значительный интерес в строительной сфере. LVL — это высококачественный конструкционный материал с однородными инженерными характеристиками и гибкостью размеров, что делает его лучше пиломатериалов и клееного бруса, особенно для крупнопролетных конструкций.
Область применения простирается от общественных зданий, больших сборных домов, комплектующих изделий и промышленных складов до деревянных домов по индивидуальному заказу.Новые приложения постоянно разрабатываются в тесном сотрудничестве с заказчиками и профессионалами деревянного строительства. Короче говоря, LVL обеспечивает идеальное решение, когда важны такие характеристики, как долговечность, легкий вес и точность размеров. Эти привлекательные особенности становятся все более популярными как в Европе, так и в Соединенных Штатах. Основными европейскими странами, на которых продается LVL, являются Скандинавские страны, Германия и Франция.
Уникальная сила и универсальностьLVL характерны и для другого близкого родственника, пиломатериалов из параллельных прядей (PSL).PSL — это конструкционный продукт из дерева, который изготавливается из фанеры хвойных пород, которую затем разрезают на длинные и узкие полосы, которые затем склеивают в параллельные пластинки. В этом отчете PSL не описывается.
Инженерные пиломатериалы пользуются все большим спросом на рынке и вытесняют массивные пиломатериалы для строительных конструкций. Растущая популярность этих деревянных изделий растет по многим причинам.
Деревья большого диаметра для пиломатериалов менее доступны на некоторых рынках, что создает прекрасную возможность для LVL.Процесс облицовки и склеивания LVL позволяет изготавливать большие элементы из относительно небольших деревьев, тем самым обеспечивая эффективное использование древесного волокна. Другими словами, LVL позволяет превращать небольшие деревья в доски большого размера. Кроме того, LVL можно производить из сырья, которое ранее нельзя было использовать.
С небольшими модификациями фанерные заводы можно переоборудовать для производства LVL, расширив ассортимент своей продукции и открыв новые рынки.
3.История LVL
LVL впервые был использован для изготовления винтов самолетов и других высокопрочных деталей самолетов во время Второй мировой войны.
До 1970-х годов термин «шпон» был синонимом фанеры. Но все это начало меняться в течение 70-х годов, когда Арт Траутнер и Герольд Томас (в США) использовали параллельные ламинированные слои шпона без поперечной обвязки (перекрестной ламинации) для формирования верхних и нижних фланцев структурных двутавровых балок и балок.Траутнер и Томас официально основали свою компанию, ныне известную как TJ International (США), в начале 1960 года для продажи необычного нового продукта под названием «балочные фермы». В этой открытой ферме в качестве верхних и нижних поясов использовалась древесина, рассчитанная на механическое напряжение. Эти пояса были соединены стальной тесьмой. Этот замечательный новый продукт нес большую нагрузку на фунт собственного веса, чем любой другой конструкционный продукт, доступный на тот момент.
Troutner продолжал совершенствовать продукт Open-Web и изобретать дополнительные продукты на основе пиломатериалов.Вскоре была разработана уникальная балка перекрытия, предназначенная для рынка элитного жилья. Соединительная перемычка из фанеры заменила стальные трубы с открытой перемычкой. Результатом стала структурно эффективная I-образная форма, в которой древесина концентрировалась сверху и снизу, где она больше всего необходима для прочности и поддержки.
Рынок был готов для этого продукта, и продажи выросли. Легкий вес, прочность, однородность и способность преодолевать большие расстояния сделали его идеальным заменителем массивных пиломатериалов.
Однако производство двутавровых балок неизменно высокого качества требовало надежных поставок высокопрочных пиломатериалов с полками, а цельные пиломатериалы такого качества становились все труднее и труднее обеспечивать.
Изобретательный ум форелей перешел на новый уровень творчества. Впоследствии он разработал параллельную ламинированную сборку из шпона пихты Дугласа толщиной 1/10 дюйма (2,54 мм) для создания древесины достаточной прочности и однородных свойств для использования в качестве материала фланца.Затем грубую сборку, называемую заготовкой, разрезали на желаемую ширину.
TJs MICRO-LAM, состоящие из фанерных лент и фланцев из клееного бруса (LVL), затем стали первой коммерчески успешно спроектированной древесиной массового производства, производимой любой компанией в мире.
Спрос, продукция TJs и производственные мощности для этой продукции расширились в течение 70-х годов. Продукция TJ и рынок, который она обслуживала, были хорошо подготовлены, чтобы воспользоваться нехваткой старых лесоматериалов большого диаметра, которые были традиционным источником массивных пиленых ферм, коллекторов, балок и балок.
TJ International в настоящее время является ведущим производителем и продавцом инженерных пиломатериалов в мире.
Рис.3 Двутавровая балка и пиломатериалы
4. Производство
LVLОкоренные еловые бревна длиной 4,9 м замачиваются при температуре +50 ° С водой в течение 24 часов. Бревна подаются на торцовочную пилу и разрезаются на бревна шириной 1,6 м. Блоки ротационно разрезаются на фанеру толщиной 3,2 мм, которые разрезаются на листы, длина которых зависит от требуемой длины LVL-пиломатериала.Отходы сердцевины и округления измельчают и используют для производства бумаги. Шпон сушат в роликовой сушилке непрерывного действия до содержания влаги ниже 5%, что регулируется автоматическим измерителем влажности.
В линии укладки листы сортируются, слишком маленькие и узкие листы удаляются, а слишком влажные листы отделяются для повторной сушки. Классификатор выбирает лучшие листы в качестве облицовки. Сортировка организована таким образом, что определяется вес каждой фанеры, и виниры укладываются в разные стопки, чтобы смешать виниры.Ведущий производитель в США, TJ International, помимо визуальной сортировки классифицирует виниры с помощью передовой ультразвуковой технологии. В зависимости от конечного использования продукта LVL виниры с ультразвуковой градацией специально расположены в материале, чтобы эффективно использовать прочностные характеристики марок шпона. Например, если конечным использованием LVL является доска для строительных лесов, виниры более высокого качества будут размещены на внешних сторонах доски.
Пила для шарфов делает фаски длиной 3 см на обоих концах фанеры.На шарф лицевой фанеры нанесен клей. Подача организована таким образом, чтобы лицевые и стержневые виниры подавались в правильном порядке. Клей представляет собой термореактивную фенольную смолу. Используя специальный тип покрытия для штор, клей наносится на верхнюю сторону каждого листа, за исключением верхней стороны. Листы укладываются в сплошной мат так, чтобы стыки шпона находились на расстоянии более 10 см друг от друга.
При производстве фанеры Kerto-S укладываются в укладку, поэтому направление волокон одинаково для всех фанер.В Kerto-Q и Kerto-T некоторые виниры укладываются так, что их волокна противоположны направлению волокон большинства слоев. Такая конструкция придает ЛВЛ жесткость, не коробится и не скручивается.
Образцы для разных укладок Kerto-Q:
толщина | кв.м. | п | Символ |
27 33 39 45 51 57 63 69 | 9 11 13 15 17 19 21 23 | 2 2 3 3 3 4 5 5 | II-III-II II-IIIII-II II-III-III-II II-IIII-IIII-II II-IIIII-IIIII-II II-III-IIII-III-II II-III-III-III-III-II II-IIII-III-III-IIII-II |
толщина в мм m = общее количествовиниров n = нет. прямоугольных фанер |
По достижении желаемой толщины мат предварительно прижимается для равномерного нанесения клея на нижнюю сторону облицовки. Заготовки шириной 1,6 м и толщиной 27-75 мм разрезаются на желаемую длину (не более 26 м), после чего загружаются в горячий пресс. Горячий пресс двухдневный, температура прессования около +145 ° С. C. Время прессования зависит от толщины заготовки.
LVL-заготовки нарезаются в соответствии с требованиями заказчика.При продольной распиловке заготовки разрезаются либо в продольном направлении на балки (Kerto-S и Kerto-T), либо на доски (Kerto-Q). На фабрике Finnforest есть специальная пила для косой резки, поэтому по желанию заказчика заготовки можно распиливать прямо или наклонно.
5. Структурные свойства LVL
1. Введение
Самая главная причина успеха LVL — это качество самого продукта и его свойства.В процессе производства LVL имеет однородную структуру.
В LVL, как правило, волокна каждого слоя идут в одном (длинном) направлении, в результате чего они становятся прочными, когда край нагружен как балка, или грань, загруженная как доска.
Этот вид ламинирования называется параллельным ламинированием, и он дает материал с большей однородностью и предсказуемостью, чем такой же размерный материал, полученный перекрестным ламинированием.
Перекрестно-ламинированный LVL обеспечивает превосходные усадочные свойства при перпендикулярном продольном направлении плиты и повышенные прочностные характеристики при нагрузке в виде доски.
2. Прочностные характеристики
Одна из основных идей LVL — диспергировать или убрать характеристики, снижающие прочность. LVL — это спроектированный, очень предсказуемый, однородный пиломатериал, потому что естественные дефекты, такие как сучки, наклон волокон и трещины, рассредоточены по всему материалу или были полностью удалены внутри фанеры. В дополнение к этому, листы шпона размещаются в определенной последовательности и в определенном месте внутри продукта, чтобы максимально использовать более прочные сорта шпона.Это можно рассматривать как спроектированную конфигурацию виниров.
Следовательно, прочностные характеристики LVL выше, чем у клееного бруса (клееного бруса) или древесины с градацией напряжений. Среднее значение большинства прочностных свойств выше, а разброс значительно ниже по сравнению с массивной древесиной. LVL — это высококачественный продукт, который является более однородным и демонстрирует улучшенные структурные свойства по сравнению с пиломатериалами.
Продукт | Напряжение изгиба | Модули упругости | Сжатие (перпендикулярно) | Горизонтальные ножницы |
Клееный брус b | 2,800 | 2 000 000 90 500 | 500 | 285 |
Пиломатериалы из параллельных прядей | 2 900 90 500 | 2 000 000 90 500 | 600/400 c | 290/210 c |
Выберите Structural Douglas Fir | 1,800 | 1,800,000 | 625 | 95 |
a Для преобразования английских единиц в международные системы, 1 фунт / кв. Дюйм = 6.89 x 103 Па | ||||
Источник: Progressive Architecture, стр.35 (Р. МакНатт и Р.С. Муди) |
Таблица 1: Сравнение конструктивных характеристик Расчетное значение (фунт / кв. Дюйм) a
Проиллюстрированные расчетные значения явно выгодно отличаются от высококачественных пиломатериалов.Хотя модули упругости (также отвечающие за жесткость) пиломатериалов LVL и PSL на 10 процентов выше, чем у пихты Дугласа, расчетная прочность на изгиб и растяжение более чем на пятьдесят процентов выше.
В целом можно грубо сказать, что прочность LVL в 1,3 раза превышает прочность клееного бруса и в 2 раза превышает прочность пиломатериалов.
Подобно другим продуктам, изготовленным путем склеивания деревянных частей вместе для создания структурных элементов, таких как фанера, клееный брус, пиломатериалы из параллельных прядей (PSL) или OSB / вафельные плиты, LVL предлагает преимущества более высокой надежности и меньшей изменчивости за счет удаления и рассеивания дефектов.
Тем не менее, сильные цифры говорят только половину истории. Согласно отчету Смита Барни :: Менеджмент (TJM Trus Joist MacMillan, США) говорит о том, что если бы кто-то поддержал пол площадью 1000 квадратных футов традиционными перекрытиями 2 «x 10», это потребовало бы сокращения из трех деревьев. Деревянные двутавровые балки (Trus Joist) могут выполнять ту же работу и требуют вырубки только одного дерева. () Это может привести к более эффективному использованию древесного волокна. (Доби, 1993; Из фанеры и изделий из шпона, Ричард Ф.Болдуин, 1995)
Независимо от того, составляет ли коэффициент использования на самом деле 3: 1 или что-то меньшее, последняя информация о конструкции и опыт работы на месте показывают, что инженерная структурная система потребует значительно меньше древесного волокна по сравнению с массивной древесиной.
3. Стабильность размеров
LVL точен по размерам, прямой, он не коробится, но может чашеать, имеет незначительные изменения из-за влажности.
Все остальные листы шпона укладываются плотно вверх или вниз, чтобы конечный продукт не деформировался или не перекрутился.
4. Доступная длина
LVL доступен в любой длине, которая ограничена только размером пресса или ограничениями по транспортировке. Этот факт превосходит пиломатериалы, которые доступны в Финляндии от 1,8 м до 6,6 м. Максимальная длина LVL превосходит только клееный брус или конструкционные пиломатериалы с шиповым соединением.
5. Доступная ширина
Максимальная ширина LVL ограничена до 80 мм в зависимости от производственного процесса.По сравнению с пиломатериалами или клееным клеем LVL предлагается с гораздо меньшей шириной, но из-за его превосходных прочностных свойств в несущих конструкциях допускается меньшее поперечное сечение древесного материала. В дополнение к этому, поперечное сечение LVL может быть оптимизировано за счет увеличения высоты поперечного сечения как основного фактора жесткости и, соответственно, уменьшения ширины как второстепенного фактора жесткости. Следовательно, максимально доступной ширины LVL достаточно для несущих конструкций.
6. Однородность
LVL — однородный продукт.
7. Расщепление, трещины в конечном продукте
Таким образом, виниры LVL сушатся до желаемого содержания влаги, LVL больше не дает усадки после горячего прессования. В результате этого не происходит расколов и трещин, тогда как пиломатериалы и клееный брус по-прежнему подвержены усадке из-за неэффективной сушки.
8.Отходы материала
Потери материала при производстве минимальны для LVL, потому что почти все бревно используется для изготовления шпона, а лишь небольшое количество шпона отбраковывается из-за устранения дефектов.
Напротив, отходы пиломатериалов значительны из-за самого процесса распиловки и дефектов древесины, которые необходимо уменьшить или удалить путем поперечной резки или обрезки кромок.
9. Внешний вид
Естественная эстетическая красота пиломатериалов включает появление сучков, обвалов, карманов из смолы, трещин, наклона волокон и некоторых других менее значительных дефектов. . Некоторые из этих дефектов имеют большое влияние на оптическое качество пиломатериалов и могут значительно снизить стоимость пиломатериалов.
LVL предлагает более однородную поверхность с почти такой же красотой, как у натурального дерева. Видимые на поверхности шарфы могут быть проблемой, которая снижает качество оптического внешнего вида, если используются смолы темного цвета, такие как смолы PF.
10. Качество конечного продукта
LVL предлагает более стабильное качество по сравнению с пиломатериалами.Различия в свойствах менее значительны.
11. Огнестойкость
LVL — это продукт на основе древесины, который реагирует на огонь примерно так же, как массивные пиломатериалы или клееный брус сопоставимого размера.
Клей на основе фенолоформальдегидной смолы, используемый в производстве, является инертным после отверждения. Таким образом, они не влияют на пожарную нагрузку, и на прочность соединения тепло не влияет. При использовании в огнестойких конструкциях полов или кровли LVL по своим характеристикам аналогичен массивным пиломатериалам или клееному брусу.
6. Сферы применения
LVL теперь используется там, где требуются прочность и стабильность размеров.
Являясь однородным и стабильным по размерам строительным материалом, LVL может использоваться как в несущих, так и в ненесущих стенах, в виде досок, балок, коллекторов, в дверных и оконных рамах, направляющих раздвижных дверей, ступенях, а также в крыше. фермы частных домов и инженерных строительных конструкций, таких как плавательные залы, спортивные залы и т. д.
Рис. 4 Внешнее использование плит LVL, Зеефельд, Германия
Рис. 5 Спортивный зал в Оулу, Финляндия
Рис. 6 Конструкция крыши из LVL-балок, Паркштайн, Германия
7. Контроль качества
Производство LVL требует наличия собственной организации по обеспечению качества.Регулярные независимые аудиты качества третьей стороной, проводимые сертификационной организацией, являются обязательной частью программы обеспечения качества производителей.
ПродуктыLVL протестированы и одобрены для использования основными агентствами по кодам и оценке продуктов в США и Канаде. Все произведенные продукты LVL, которые были протестированы и одобрены таким образом, должны иметь печать органа по сертификации, производителя, дату изготовления, уровень LVL и ссылку на любой применимый код или номера одобрения агентства по оценке.
LVL — это запатентованный продукт, технические характеристики которого зависят от материалов, используемых в производстве, а также от процессов сборки и производства продукта. Таким образом, он не соответствует общепринятым стандартам производства. Поэтому проектировщики и установщики должны следовать рекомендациям отдельных производителей по проектированию, использованию и установке.
Канадский центр строительных материалов (CCMC) выпустил оценки продуктов для многих продуктов LVL, продаваемых в Канаде.В Соединенных Штатах большинство производителей получили отчеты об оценке продукции от Совета американских строительных чиновников (CABO).
В настоящее время стандарт для технических условий для оценки изделий из конструкционных композитных пиломатериалов (таких как LVL и PSL) находится в стадии разработки ASTM. В этом стандарте будут изложены процедуры для установления, мониторинга и переоценки структурных возможностей конструкционных композитных пиломатериалов, а также будут детализированы минимальные требования для установления контроля качества, гарантии и аудита.
8.1 Развитие производственных линий LVL по всему миру
Машины для производства LVL теперь доступны от нескольких производителей оборудования и используются все большим числом производителей лесной продукции.
Последняя информация, предоставленная Raute Wood Processing Machinery, Финляндия:
LVL производится в США, Канаде, Финляндии, Японии, Австралии и Новой Зеландии.О растущей популярности LVL свидетельствует и тот факт, что в текущий портфель заказов Raute Wood Processing Machinery входят пять новых производственных линий LVL. Две из них устанавливаются в Индонезии для Surya Dumai Group, а Keytec возводит линию в Японии. Это уже вторая линия LVL, которую японская компания заказала у Raute Wood. На этих линиях сначала будут производиться неструктурные LVL, а в будущем планируется производить структурный продукт.
Finnforest также расширяет свое производство в Финляндии и Evans Products в Б.C., Канада также приобрела линию Raute Wood LVL.
8,2 LVL Производитель в Европе
Подразделение KERTO является важной частью деятельности Finnforest.
KERTO — зарегистрированная торговая марка. На рисунке ниже показан типичный товарный знак KERTO.
KERTO производит и продает Kerto-LVL (клееный брус), разработанный в результате собственных исследований и разработок компании.Завод KERTO находится в Лохья в южной Финляндии.
Kerto-LVL — это исключительно прочная древесная плита, изготовленная путем склеивания лущеной фанеры мягких финских пород древесины.
Finnforest была единственной компанией в Европе, которая производила этот продукт до 1998 года. Годовая производственная мощность завода Kerto-LVL составляет около 60 000 м3. Экспорт составляет почти 90% от общего объема производства. Наиболее важные рынки сбыта — Германия, Франция, Швеция и США.
Производственная линия Kerto сертифицирована по ISO 9001, что означает для клиентов стабильные процессы качества и неизменное качество.
Шведская компания Vänerply, один из крупнейших производителей фанеры в Европе, начала производство LVL в начале 1998 года и собирается стать единственным конкурентом KERTO в Европе.
Рис.7 Завод-изготовитель в Лохья, Финляндия
Эксперты KERTO-LVL из Finnforest и KERTO по всему миру работают в тесном сотрудничестве с конечными пользователями продукции.Высококачественный продукт, ориентированный на клиента, в сочетании с техническими знаниями в области маркетинга — это мощная комбинация, пользующаяся большим уважением среди профессионалов строительной отрасли. KERTO постоянно улучшает качество обслуживания клиентов и выпускает продукцию. Продукция Kerto-LVL подвергается дальнейшей переработке на заводе в соответствии с требованиями заказчика.
8.2.1 Подробнее о Kerto-LVL
Kerto-LVL — это экологически чистый продукт из древесины, изготовленный из финской ели с использованием новейших технологий.Это прочный конструкционный материал, используемый для крепления как балок, так и плит. Благодаря своей однородной и устойчивой к атмосферным воздействиям клеевой структуре Kerto-LVL очень прочный, точный по размеру и прямой. Он не коробится и имеет лишь незначительные изменения из-за влажности. Kerto-LVL сохраняет эти свойства и обладает высокой огнестойкостью.
В качестве несущего материала Kerto подходит для перекрытий перекрытий, перемычек, прогонов, а также для крыш всех форм, таких как балки перекрытий и оконных проемов. Диапазон использования варьируется от промышленных и общественных зданий до промышленных домов, требующих ремонта.Kerto-LVL также используется в других сферах применения: при строительстве мостов и водонапорных башен, передвижных домов, железнодорожных шпал, в шумозащитных ограждениях на автомагистралях, в лестницах и строительных лесах, а также в качестве опор как для несущих, так и ненагруженных. несущие стены.
Многофункциональное использование сырья дает дизайнерам большую свободу в создании разнообразной среды. Естественно.
Рис. 8 Солнечная башня «Гелиотроп», Фрайбург, Германия
8.2.2 Finnforest — Подразделение строительных изделий
Спрос на продукцию Подразделений заметно вырос за год. Заметный рост частного потребительского спроса в Финляндии привел к заметным изменениям, поскольку в этом подразделении внутренний рынок составляет гораздо большую долю от общего объема продаж, чем в других бизнес-подразделениях. Хорошие объемы продаж и цены на окна, двери, ДСП и плиты с меламиновым покрытием.
Большая часть клееного бруса (LVL), производимого бизнес-единицей Kerto, экспортировалась на европейский рынок.Благоприятное экономическое развитие увеличило спрос на продукцию LVL настолько, что стала очевидной потребность в дополнительных производственных мощностях.
Чистый объем продаж подразделения Kerto в 1997 году составил 190,6 млн. Финских марок (178,5 млн. Финских марок), при этом доля экспорта составила 64%. Фокус экспорта сместился из США в Центральную Европу, где рынки хороши для продуктов высокой степени переработки по более высоким ценам. Продажи сдерживались из-за недостаточной мощности бизнес-единицы Kerto, и, поскольку спрос на европейском рынке значительно вырос, было принято важное решение — с далеко идущими результатами — увеличить производственные мощности с нынешних 60 000 кубических метров до 100 000 кубических метров. .
Финансовые показатели предприятия в 1997 году были хорошими.
Чистый объем продаж Подразделения строительной продукции в 1997 году составил 542,7 миллиона финских марок (566,9 финских марок), а на конец 1997 года работало 657 человек.
Рис. 8 Здание бюро, Sortimo
9. Приложение
Данный отчет в основном основан на информации из следующих источников:
- Годовой отчет 1997, Finnforest Oy, Финляндия
- Raute Wood Processing Machinery Ltd, Финляндия
- Kerto, Kertopuu, различная информация о продукте
- Фанера и изделия на ее основе, Ричард Ф.Болдуин, 1995
- раздаточный материал: «Особые виды древесных плит», О. Люкконен
- различных интернет-сайтов
Рис. 10 Каркасная ферма в Эспоо, Финляндия
Клееный брус (LVL) | WoodSolutions
Архитектурные кровельные фермы
Ферма — это конструкция, состоящая из одного или нескольких треугольных элементов. Каждый треугольник состоит из прямых и обычно тонких деревянных элементов, соединенных на концах соединениями.На стыки действуют внешние нагрузки и реакция конструкции на эти нагрузки, в результате чего возникают силы растяжения или сжатия.
Сила фермы заключается в ее триангуляции элементов бандажа, которые работают вместе, обеспечивая преимущество всей конструкции. Что касается ферм, элементы сжатия часто определяют размер элементов, поэтому конструкции, которые имеют короткие элементы сжатия или ограничивают поперечное продольное изгибание, обычно более эффективны, чем фермы с более длинными элементами сжатия.
Внутри здания можно найти две формы ферм. Фермы, покрытые гвоздями, представляют собой скрытые от глаз фермы, в которых в качестве соединителей используются гвоздевые пластины. Архитектурные фермы относятся к тем привлекательно детализированным деревянным фермам, открытым для обозрения. В этом руководстве основное внимание уделяется процессу подачи заявки на последний.
Преимущества деревянных ферм значительны и многочисленны. Деревянные стропильные фермы являются экологически безопасным выбором по сравнению с традиционными скатными крышами, они используют брус меньшего размера, который охватывает большие расстояния, что, в свою очередь, уменьшает общий объем древесины, содержащейся внутри.Архитектурные деревянные фермы легкие, что обеспечивает быстрое и эффективное строительство и установку, что обеспечивает визуальный эффект, которым можно наслаждаться в течение десятилетий.
В этой статье дается всесторонний обзор процессов, связанных с определением, сборкой и установкой архитектурной стропильной фермы.
Обрамление
Легкие деревянные конструкции обычно включают каркасные и скрепленные конструкции, к которым применяется один или несколько типов облицовки.Конфигурации обрамления могут варьироваться от близко расположенных легких бревен, обычно встречающихся в конструкции каркасов с гвоздями, до больших, более широко разнесенных бревен. Здание с деревянным каркасом может быть размещено на бетонной плите или на столбах / столбах или опорах, опирающихся на опоры / пни, опирающиеся на опорные площадки.
Используемая в домах или многоквартирных домах, легкая деревянная конструкция предлагает гибкость широкого диапазона экономичных вариантов дизайна.
Когда древесина поступает из экологически чистых источников, этот метод строительства может быть экологически выгодным, поскольку он сочетает в себе низкую энергию, содержащуюся в древесине, с ее способностью накапливать углерод.
Рамы портала
Каркасы деревянных порталов — одно из самых популярных конструкций для коммерческих и промышленных зданий, функции которых требуют больших пролетов и открытых интерьеров. Как материал, древесина предлагает дизайнерам простоту, скорость и экономию при изготовлении и монтаже.
Деревянные портальные рамы имеют прочную, прочную и превосходную конструкцию. Структурное действие достигается за счет жестких соединений между колонной и стропильной балкой в коленях и между отдельными стропильными элементами на коньке.Эти жесткие соединения обычно выполняются с использованием гвоздей из фанеры и, иногда, со стальными вставками.
От выбора материала до отделки, это руководство по применению дает исчерпывающий обзор процесса использования древесины при спецификации, изготовлении и возведении конструкций портальной рамы.
Клееный брус (lvl) — Kerto® LVL
Невероятно прочная и стабильная по форме деревянная балка
Kerto® LVL от Metsä Wood — это клееный брус, используемый во всех типах строительных проектов, от новостроек до реконструкции и ремонта.Kerto LVL невероятно прочен и стабилен по размерам. Kerto LVL обеспечивает высокую прочность за счет однородной склеенной структуры.
Kerto LVL изготавливается из лущеного шпоном хвойных пород толщиной 3 мм, склеенных между собой в непрерывную слитку. Заготовка разрезается по длине и распиливается на балки, доски или панели LVL в соответствии с требованиями заказчика. Посмотреть видео как производится Kerto LVL.
Продукция Kerto LVL имеет маркировку CE и сертифицирована Eurofins Expert Services Oy.
Пример использования Kerto® LVL (клееный брус)
- Балки
- Балки
- Фермы
- Рамы
- Компоненты элементов крыши, пола и стен
- Компоненты для промышленного применения, например производство дверей и окон
- Компоненты для производства грузовых прицепов
- Бетонная опалубка
- Настил лесов
Дальнейшая обработка
Kerto LVL может подвергаться дальнейшей обработке различными способами в зависимости от конечного использования и конкретных пожеланий заказчика.Услуга дальнейшей обработки является неотъемлемой частью обслуживания клиентов и цепочки поставок.
- Шлифование: оптическое или калибровочное
- Профилирование кромки балки, например, шип и канавка
- Специальная резка: прямые и конические
- Склеивание: повторное склеивание для увеличения толщины
- Обработка с ЧПУ: сверление, шлифование, ослабление краев, надрез
- Наращивание, например, коробчатые плиты
- Защитные покрытия, например, WeatherGuard
Kerto® LVL доступен в следующих вариантах
Смотрите также
приложения для Kerto LVL.
Европейские классы прочности LVL
Продукция Kerto LVL соответствует или превышает требования к классам прочности, установленным европейскими производителями LVL Бюллетень LVL за сентябрь 2019 года согласно следующей таблице
Тип | Плотность 510 кг / м 3 | Плотность 440 кг / м 3 |
Балки, балки, стойки, опалубка | LVL 48 P -> Kerto LVL S-образная балка | LVL 32 P -> |
Вертикальные и горизонтальные панели | LVL 36 C / 32 C -> Kerto LVL Q-панель | LVL 25 C / 22 C -> Kerto LVL L-панель |
Промышленные панели и балки | Kerto LVL Qp-beam и Kate Kerto LVL специальные конструкции |
Ламинированный шпон — Канадский совет по древесине
Ламинированный шпон (LVL)
Впервые использованный во время Второй мировой войны для изготовления воздушных винтов, клееный брус (LVL) был доступен в качестве строительного продукта с середины 1970-х годов.LVL — это наиболее широко используемый конструкционный композитный пиломатериал (SCL), обеспечивающий такие характеристики, как высокая прочность, высокая жесткость и стабильность размеров. Производственный процесс LVL позволяет изготавливать большие элементы из относительно небольших деревьев, обеспечивая эффективное использование лесных ресурсов. LVL обычно изготавливается из таких пород дерева, как пихта Дугласа, лиственница, южная желтая сосна и тополь.
LVL используется, прежде всего, в качестве несущего каркаса для жилищного и коммерческого строительства.Обычные применения LVL в строительстве включают в себя коллекторы и балки, стропила вальмы и ендовы, настил строительных лесов и материал фланцев для сборных деревянных двутавровых балок. LVL также можно использовать в дорожных знаках и в качестве настила кузова грузовика.
LVL изготовлен из высушенного и сортированного деревянного шпона, покрытого водостойким клеем на основе фенолформальдегидной смолы, собранных в упорядоченный узор и сформированных в заготовки путем отверждения в нагретом прессе. Затем заготовка LVL распиливается до желаемых размеров в зависимости от конечного применения.
Волокна каждого слоя шпона идут в одном (длинном) направлении, в результате чего LVL может быть загружен на его короткий край (сильная ось) как балка или на его широкую поверхность (слабая ось) как доска. Этот тип ламинирования называется параллельным ламинированием и позволяет получить материал с большей однородностью и предсказуемостью, чем инженерные изделия из дерева, изготовленные с использованием перекрестного ламинирования, такие как фанера.
LVL представляет собой прочную, предсказуемую и однородную древесину из-за того, что естественные дефекты, такие как сучки, наклон волокон и трещины, рассредоточены по всему материалу или были полностью удалены в процессе производства.
Чаще всего толщина LVL составляет 45 мм (1-3 / 4 дюйма), из которой можно легко построить более широкие балки, скрепив несколько слоев LVL вместе на месте. LVL также может изготавливаться толщиной от 19 мм (3/4 дюйма) до 178 мм (7 дюймов). Обычно используемые глубины балок LVL составляют 241 мм (9-1 / 2 дюйма), 302 мм (11-7 / 8 дюйма), 356 мм (14 дюймов), 406 мм (16 дюймов), 476 мм (18-3 / 4 дюйма). дюйма) и 606 мм (23-7 / 8 дюйма). Другая ширина и глубина также могут быть доступны от конкретных производителей. LVL доступен длиной до 24.4 м (80 футов), в то время как более распространенная длина составляет 14,6 м (48 футов), 17 м (56 футов), 18,3 м (60 футов) и 20,1 м (66 футов). LVL можно легко отрезать на стройплощадке.
Всякая специальная резка, надрез или сверление должна выполняться в соответствии с рекомендациями производителя. LVL — это продукт на основе древесины, огнестойкость которого аналогична массивным пиломатериалам или клееным брускам такого же размера. Каталоги производителя и отчеты об оценке являются основными источниками информации о конструкции, типовых деталях установки и эксплуатационных характеристиках.
LVL в основном используется как конструктивный элемент, чаще всего в скрытых помещениях, где внешний вид не важен. Готовый или архитектурный внешний вид доступен у некоторых производителей, как правило, за дополнительную плату. Однако, когда желательно использовать LVL в приложениях, где важен внешний вид, можно использовать обычные методы отделки древесины для акцентирования текстуры и защиты деревянной поверхности. В готовом виде LVL по широкой поверхности напоминает фанеру или пиломатериалы.
Как и любой другой продукт из дерева, LVL следует защищать от погодных условий во время хранения на рабочем месте и после установки.Упаковка продукта для отправки на стройплощадку важна для обеспечения защиты от влаги. Герметизация торцов и кромок продукта повысит его устойчивость к проникновению влаги.
LVL является патентованным продуктом, поэтому его технические характеристики и размеры уникальны для каждого производителя. Таким образом, LVL не имеет единого стандарта производства и общих проектных значений. Расчетные значения получены на основе результатов испытаний, проанализированных в соответствии с CSA O86 и ASTM D5456, а расчетные значения проверены и утверждены Канадским центром строительных материалов (CCMC).Продукты, соответствующие руководящим принципам CCMC, получают номер оценки и отчет об оценке, который включает указанные сильные стороны конструкции, которые впоследствии указываются в Реестре оценок продуктов CCMC. Название производителя или идентификация продукта и степень напряжений наносятся на материале через различные промежутки времени, но из-за обрезки концов они могут присутствовать не на каждой детали.
Для получения дополнительной информации см. Следующие ресурсы:
APA — Ассоциация инженерной древесины
Канадский центр строительных материалов (CCMC), Институт строительных исследований
CSA O86 Деревянный инженерный дизайн
ASTM D5456 Стандартные технические условия для оценки конструкционных композитных пиломатериалов
Ожидается, что рынок ламинированного пиломатериалавырастет до 4 долларов США.23 миллиарда к 2024 году
НЬЮ-ЙОРК, 21 июня 2019 г. / PRNewswire / — Клееный брус (LVL) изготовлен из шпона, склеенного вместе под действием тепла и давления с использованием полностью атмосферостойкого клея.
Прочтите полный отчет: https://www.reportlinker.com/p04921060/?utm_source=PRN
Это легкий, высокопрочный, долговечный продукт с точностью размеров, однородностью и способностью преодолевать большие расстояния . Он доступен на рынке в двух подтипах — клееная древесина (LSL) и клееная фанера с поперечными лентами.В последнем отчете аналитика под названием «Рынок клееного бруса: глобальные тенденции в отрасли, доля, размер, рост, возможности и прогноз на 2019-2024 годы» говорится, что в 2018 году объем рынка клееного бруса достиг 2,33 млрд долларов США. рост в среднем на 13,7% в течение 2011-2018 гг.
Благодаря своим структурным свойствам клееный брус используется для постоянных строительных конструкций в общественных зданиях, больших сборных домах, компонентах продукции, промышленных складах, деревянных домах по индивидуальному заказу и т. Д.Некоторые из его основных применений включают структурный каркас для жилого и коммерческого строительства, такого как балки, перемычки, прогоны, балки, пояса ферм, бетонная опалубка и доски строительных лесов. Он в основном используется в таких регионах, как Европа и США, как альтернатива конструкционной стали или железобетону. Кроме того, ожидается, что к 2024 году объем рынка достигнет 4,23 миллиарда долларов США.
В зависимости от конечного использования рынок делится на коммерческий и жилой. Жилой сектор является крупнейшим потребителем клееного бруса, на его долю приходится более половины от общего объема мировых долей.В отчете была проведена оценка рынка на основе ключевых регионов и сделан вывод о том, что Северная Америка является крупнейшим рынком клееного бруса. Некоторые из других крупных регионов — это Азиатско-Тихоокеанский регион, Европа, Латинская Америка, Ближний Восток и Африка. В отчете также был проанализирован рынок на основе конкурентной среды и представлены подробные сведения об основных игроках. Некоторые из основных игроков — Clarke Veneers and Plywood, Roseburg, Nelson Pine Industries Limited, Weyerhaeuser и т. Д.
Этот отчет дает глубокое представление о мировом рынке клееного бруса, охватывая все его основные аспекты. Он варьируется от макрообзора рынка до микродеталей производительности отрасли, последних тенденций, ключевых факторов и проблем рынка, SWOT-анализа, анализа пяти сил Портера, анализа цепочки создания стоимости и т. Д. В отчете также представлен всесторонний анализ для создания завод по производству клееного бруса. В исследовании анализируются требования к обработке и производству, стоимость проекта, финансирование проекта, экономика проекта, ожидаемая отдача от инвестиций, размер прибыли и т. Д.Этот отчет необходимо прочитать предпринимателям, инвесторам, исследователям, консультантам, бизнес-стратегам и всем тем, кто имеет какой-либо интерес или планирует каким-либо образом заняться производством клееного бруса.
Ключевые вопросы, на которые даны ответы в этом отчете:
Каковы ключевые факторы успеха и факторы риска в отрасли производства клееного бруса?
Как обстоят дела на рынке клееного бруса и как он будет выглядеть в ближайшие годы?
Какова структура отрасли производства клееного бруса и кто играет ключевую роль?
Какие отдельные операции выполняются на заводе по производству клееного бруса?
Какой общий размер земли требуется для создания завода по производству клееного бруса?
Какие требования к оборудованию необходимы для создания завода по производству клееного бруса?
Каковы требования к сырью для создания завода по производству клееного бруса?
Каковы требования к коммунальным предприятиям при открытии завода по производству клееного бруса?
Каковы требования к персоналу для создания завода по производству клееного бруса?
Каковы затраты на инфраструктуру для создания завода по производству клееного бруса?
Каковы капитальные затраты на создание завода по производству клееного бруса?
Каковы операционные расходы на создание завода по производству клееного бруса?
Каковы будут доходы и расходы завода по производству клееного бруса?
Сколько времени нужно на безубыточность?
Читать отчет полностью: https: // www.reportlinker.com/p04921060/?utm_source=PRN
О Reportlinker
ReportLinker — это отмеченное наградами решение для исследования рынка. Reportlinker находит и систематизирует самые свежие отраслевые данные, чтобы вы могли мгновенно получать все необходимые исследования рынка в одном месте.
__________________________
Связаться с Клэр: [адрес электронной почты защищен]
США: (339) -368-6001
Международный: +1 339-368-6001
ИСТОЧНИК Reportlinker
Ссылки по теме
http: //www.reportlinker.com