Производство фанеры: виды и технология изготовления
Технологический процесс, применяемый на современных фабриках, позволяет создать максимально эффективное производство фанеры высокого качества. В результате получают строительный материал, который используется в изготовлении мебели, разнообразных конструкций и для иных целей.
Сфера применения
Фанера – это строительный материал в форме многослойной плиты, созданный через склеивание слоями лущеного шпона с использованием дополнительных фиксирующих компонентов. Для производства конструкций применяют плиту с разным количеством слоев, склеенных по определенному принципу.
Фанера применяется:
Предел прочности фанеры на изгиб
- Для конструирования больших и маленьких летательных аппаратов.
- Для строительства конструкций разных размеров.
- Во всех направлениях производства мебели.
- В производстве облицовочных материалов.
- В производстве строительных материалов.
- В создании музыкальных инструментов.
- Как основу рекламных щитов.
- Для установки опалубки.
- В производстве тары.
- И в других сферах.
Разновидности фанеры
Сегодня на фабриках производят продукцию, отличающуюся по технологическим и конструктивным признакам в зависимости от сферы применения. Она имеет разную внутреннюю структуру, которая определяет ее эксплуатационные качества.
Виды фанеры:
Характеристика фанеры
- Шлифованная и не шлифованная.
- Профилированная фанера.
- Общего назначения.
- Бакелизированная.
- Ламинированная.
- Армированная.
- Облицовочная.
- Строительная.
- Авиационная.
- Водостойкая.
В зависимости от качества шпона наружного слоя, фанера делиться на 5 сортов: А/АВ, АВ/В, В/ВВ, ВВ/С, С/С.
Стадии производства фанеры
Фабричное производство фанеры разных видов, на некоторых этапах немного отличается, но основной технологический процесс ее изготовления остаётся все тем же.
Существуют следующие этапы производства:
- Подготовка древесины.
- Заготовка шпона.
- Склеивание шпона в листы.
- Нанесение защитного и облицовочного покрытия.
Заготовка древесины для получения фанеры
Для производства фанеры используется шпон из лиственных пород и хвойной древесины. Для наружных слоев предпочитают березу, реже граб, тополь, бук и ольху. Цена березового шпона в закупке материала, является самой дешевой, потому она и обрела такую популярность среди производителей. Граб, тополь, бук и ольху считают дорогостоящими материалами, потому их используют для производства шпона по индивидуальным заказам. С хвойных пород деревьев, часто изготавливают внутренний слой, из-за хорошей прочности и небольшой стоимости этой древесины в закупке.
Привезенный материал в первую очередь проходит калибровку на специальном станке. Снимаются все излишки, сучки и кора в результате достигается ровный круг на срезе в соотношении с центром древесины. Длинные бревна разрезаются на одинаковые чурки и направляются на этап варки.
Древесина должна иметь одинаковую влажность. Это необходимо для сохранения целостности структуры будущей плиты и избегания проблем на этапе производства. Перед лущением, все заготовки на продолжительное время замачивают в теплой воде, тем самым выравнивают их общую влажность.
Размягчённое в воде бревно легче поддается лезвиям станков, это в несколько раз ускоряет процесс нарезания и сохраняет длительное время податливость материала.
В воду могут добавлять вещества, придающие будущим изделиям дополнительные свойства. Как только древесина равномерно пропитываться влагой, ее отправляют на этап изготовления шпона.
Процедура изготовления и отделки шпона
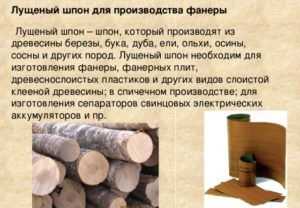
Шпон для производства фанеры
Подготовленные бревна загружают в специальные установки, фиксируя их между тремя валиками и, с помощью лезвий срезают листы или ленту шпона. Валики одновременно фиксируют и вращают бревна с заданной скоростью. Размеры определяют в зависимости от технических характеристик лущильного станка и размеров готовой продукции. Листы складывают в стопки, а ленту сматывают в рулон.
Далее, шпон загружают в форматно-раскроечный станок, с которого выпускают ленту и ножами нарезают ее на листы требуемых размеров. Весь процесс автоматический и настраивается оператором станка.
Сушка проводится в специальных закрытых помещениях, с автоматическим контролем температуры. Горячий воздух стараются распределять неравномерно, чтобы разделить сушку на несколько последовательных этапов. Рулоны или листы в подвешенном состоянии перемещают по многоэтажной роликовой системе. Это позволяет провести процесс сушки максимально эффективно с соблюдением всех временных ограничений. Влажность шпона должна быть – от 4 до 6%.
После сушки, шпон проходит ОТК. Контролеры и рабочие удаляют все дефектные участки, листы сортируют согласно требуемым размерам и влажности. Готовый элемент отправляют в цех производства фанеры.
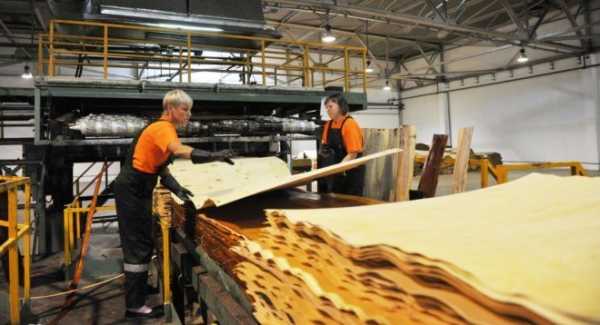
Цех по производству фанеры
Технологический процесс производства
Технологический процесс изготовления фанеры происходит в несколько этапов.
Склеивание
На специально оборудованных столах располагают листы шпона одинакового размера. Их поверхность очищают от древесной пыли и мелкого мусора, чтобы при склеивании не создавалось лишних бугорков. Далее, собирают и группируют по размерам в стопки для будущей склейки каждой плиты.
Вначале изготавливается хвойная фанера, как внутренний слой и будущий каркас. На первый лист наноситься влагостойкий клей, бакелитовая пленка или смола. Сверху его прижимают следующим листом шпона в результате получается своеобразный бутерброд. Процесс могут повторять до получения 3 и более слоев. Вся работа проводиться в хорошо проветриваемых помещениях из-за повышенной токсичности некоторых веществ в составе клея.
Часто, количество слоев увеличивают для повышения прочности. Например, такой способ применяют во время производства строительной фанеры.
Процесс склеивания фанеры
При склеивании волокна древесины каждого нового слоя стараются располагать перпендикулярно предыдущему, что в несколько раз увеличивает прочность будущей конструкции. Если слоев в плите четное количество, это значит, что направление внутренних волокон древесины расположено параллельно друг к другу. Для получения широких полноформатных листов используют способ ребросклеивания по продольным кромкам.
В случае обнаружения поврежденных участков на листах, их вырезают и заменяют специальными заранее подготовленными заплатками. Поврежденный шпон, стараются использовать для создания внутренних слоев фанеры.
Иногда на спиле листа можно увидеть резкие изменения цвета волокон с черными включениями. Это говорит о том, что производитель экономил на закупке качественной древесины, использовал подгнившее второсортное сырье или нарушил технологический процесс изготовления продукции. Такая плита редко когда выдерживает требуемые нагрузки и через непродолжительное время может разрушиться.
Холодное склеивание или термическая обработка под давлением
Первый способ – при холодном склеивании лист фанеры помещают в пресс и оставляют его там при комнатной температуре на 6 часов. После застывания, его отправляют на этап просушки.
Второй способ – готовые тщательно склеенные листы направляют под термопресс, где с давлением и высокой температурой соединения набирают окончательную прочность.

Процесс прессования фанеры
Нанесение покрытия
В отдельном цеху поверхность шлифуют и наносят разнообразные покрытия. Для этого используют всевозможные лаки, краски или готовые наклейки с изображениями.
В зависимости от покрытия фанеру разделяют:
- На облицовочную – состоит из нескольких слоев лущеного шпона. Имеет облицовочное покрытие с одной или с двух сторон.
- Ламинированную фанеру – покрытие чаще всего имитирует древесную структуру.
- Шлифованную и не шлифованную – на поверхности создаётся специфическая текстура.
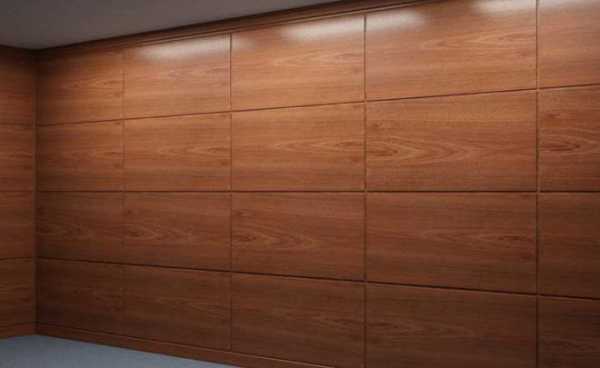
Облицовка фанерой
Особенности производства разных видов фанеры
Бакелизированная фанера – имеет увеличенную прочность структуры. Эффект достигается пропитыванием листов шпона бакелитовой смолой с дальнейшим спрессовыванием, под высоким давлением с температурой 270 °C.
Водостойкая – для производства используется водостойкий фенолоформальдегидный или карбамидоформальдегидный клей.
Профилированная – имеет сложную волнообразную структуру волокон для увеличения продольной прочности.
Армированная – внутри размещают слой, который придает дополнительную прочность будущей плиты, вставка может быть металлопластиковой, стекловолоконной или в форме металлической сетки.
Авиационная фанера – производиться из березового шпона (один из самых легких материалов). Ее могут применять в авиастроении и создании легких конструкций.
Упаковка
Готовая продукция в зависимости от размера и пожеланий заказчика, упаковывается в различные влагозащитные материалы и коробки.
Производство фанеры не требует больших денежных вложений на закупку оборудования и запуск процесса производства. Принцип технологического процесса простой и малозатратный, потому начать свой бизнес по силе каждому предпринимателю.
Видео: Производство фанеры
promzn.ru
Производство фанеры как частный бизнес
Довольно прибыльной отраслью некрупного бизнеса является производство фанеры из шпона. Но чтоб хорошо заработать в этой сфере, нужно правильным образом выбирать стратегию с тактикой для ведения дел. В этом помогут знания тематики и четкий, выверенный бизнес-план. Следует реально оценивать ожидаемые доходы, а также затратную часть и закупку необходимых станков, оптимальные проценты для получения кредитов, если таковые понадобятся.
Производство стройматериалов из древесины во все времена приносит стабильный доход. Сегодня без использования фанерных листов не обходится строительство частных домиков, дач, коттеджей и внутренняя отделка интерьеров, изготовление различной мебели, и поэтому производство фанеры – по-прежнему перспективный бизнес.
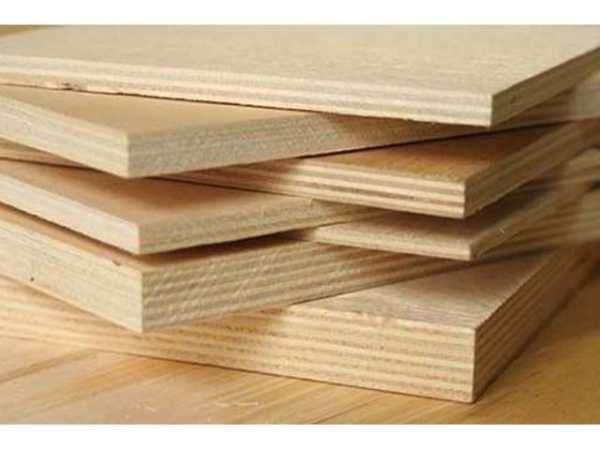
Фанера из шпона
Немного о сортаменте и разновидностях материала
Касаемо обработки, фанерный лист разделяют на:
- нешлифованный (или НШ),
- шлифованный с одной из сторон (или Ш1),
- двухсторонний (Ш2).
А согласно количеству брака поверхности материала, выделяют несколько сортов: начиная с элиты (сорт Е), где отсутствуют видимые дефекты древесины, заканчивая 4-м, который допускает практически любые «недостатки внешности». Сортамент изделия определяется условиями ГОСТа за №3916.1-96 для древесины.
Сортамент фанер
По виду используемого клея определяется марка:
- ФСФ – изготовленная с применением смоляного клея (фенолформальдегид). Она обладает водостойкостью, используется для внутренних работ, и в местах повышенной влажности;
- ФК – используется карбамидный клей. Такая фанера из шпона с низкими показателями водостойкости, быстро набухает, может потерять свою форму;
- ФБ – пропитывается бакелитовым лаком (перед сборкой и склеиванием). Такие листы из древесины используют для работ в неблагоприятных условиях, фанера выдерживает воздействия щелока, микроорганизмов, морской воды.
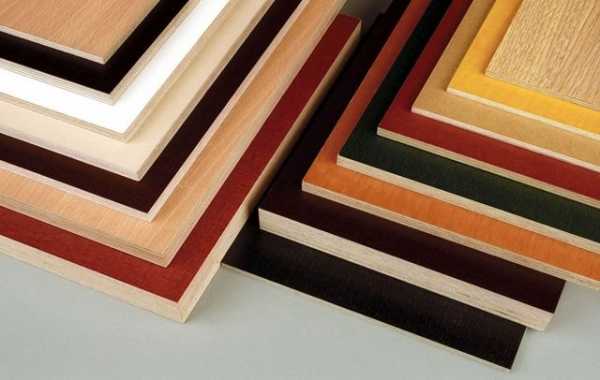
Фанера ламинат
А еще: по своему назначению материал подразделяется на строительный, авиационный, автомобильный, корабельный, тому подобный. Для чистовой отделки в помещениях нынче в фаворе декоративная фанера, сделанная из древесины ценных пород.
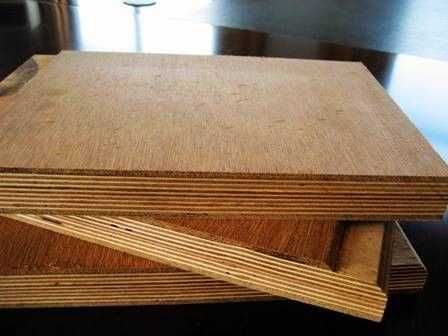
Многослойный и многофункциональный стройматериал
Чтоб заняться производством фанеры конкурентоспособно, вам понадобится высокотехнологичное современное оборудование и подбор квалифицированного персонала.
Техника и перспективы изготовления фанеры
Березовые, хвойные породы – то из чего производится данный материал. Бревна привозят на завод и укрывают от непогоды и солнца — чтоб лучи ультрафиолета не высушили торцы. Возьмем, к примеру, березу — из нее выходит самая прочная фанера.
На производство эта порода дерева привозится в виде сырья: распилованных бревен. Из них формируется подобие вязанки, «перехваченной» массивной цепью из металла.
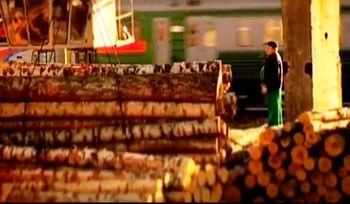
Березовые бревна – сырье для производства фанеры
Эти «вязанки» аккуратным образом перемещаются в бассейн с горячей водой. Тут древесина пропаривается некоторое время.
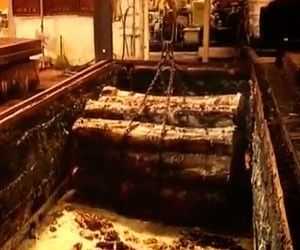
Пропарка сырья
А на поверхность выходит бурая пенка. Это природное вещество — деготь, что выделяется березой.
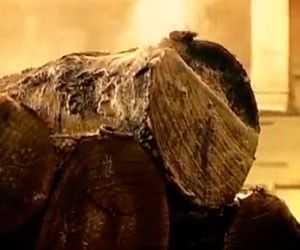
Образование дегтя
А еще через некоторое время потемневшие бревна выгрузят из бассейна и оставят на открытом воздухе, чтоб уравнять внутреннюю температуру — тепло должно дойти до самой сердцевины древесины. Если ее распарить хорошенько, она становится пластичной.
После заготовки отправляются на лущение. Бревна на станке оборачиваются вокруг оси, специальный нож убирает кору, снимая широкую стружку. Движение происходит по так называемой спирали Архимеда.
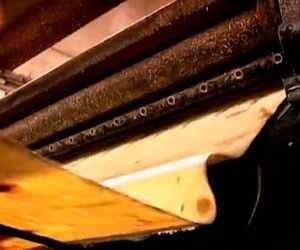
Снятие стружки
Для справки: в третьем столетии до новой эры Архимед изобрел формулу для идеальной спирали — та должна равномерно вертеться вокруг точки, приближаясь с каждым витком к ней на равное расстояние.
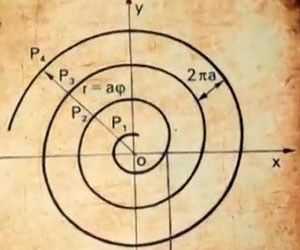
Та самая спираль
Такая спираль позволяет резать с заготовок идеально ровные слои. Эта самая стружка, что снята с бревен, именуется листами шпона.
Длина листов шпона, с одного чурака (так называют бревна-заготовки), порой достигает пятнадцати метров. Лист шпона остается теплым, пропитанным влагой (в течение некоторого времени). Ведь, если бревна предварительно не парить, шпон в процессе лущения станет ломаться, будет рваной. Самый тонкий лист из березы – милиметр в толщину.
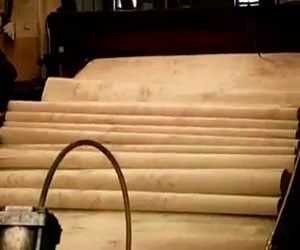
Срезание листа шпона
Кстати, в Штатах, где берез практически нет, фанерный лист режут из хвойных пород. А в Поднебесной – используют тополь.
Стружку затем кроят на специальной гильотине, отправляя в сушилку. Поток горячего воздуха быстро убирает из листов излишнюю влагу, чтоб будущий материал не расслаивался и не шел пузырями.
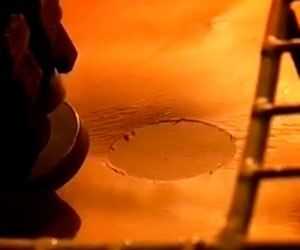
Починочный станок режет дефекты и одновременно ставит заплатки на эти места
Теперь наступает черед сборки. Для листа в один сантиметр толщиной склеивается несколько слоев шпона. Раньше для процедуры использовали казеин — молочный белок. Казеиновый фанерный лист был прочен, однако был не влагостоек и быстро промокал.
Сейчас шпон, в основном, склеивается при помощи смолы формальдегидной — конечный результат получается влагостойким. У фанерного листа нечетное количество слоев (к примеру, пятислойная). Клеем пропитывают только четные листы, что в процессе сборке должны чередоваться с нечетными – сухими. Основное: слои располагаются перпендикулярным образом. Это придает фанере прочность. Так, у первого листа волокна будут располагаться вдоль, а у второго — поперек. Увеличивается, таким образом, противоударная вязкость, то есть способность к поглощению механической энергии.
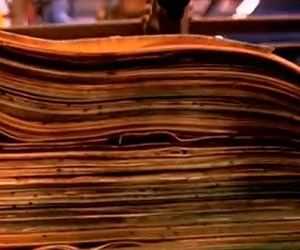
Слои шпона
Пакетированные слои на пару минут отправляются в пресс, сначала холодный. Там сухие, проклеенные «запчасти» схватываются. Это — первый этап, затем следует горячее прессование. Листы будущей фанеры грузятся в подъемником уже в горячий пресс. Под давлением шпон здесь крепко склеивается. Затем в течение суток листы будут остывать, и завершатся процессы полимеризации клеевой основы.
Теперь обрезаются неровные края у шпона, а изделию придается привычный вид.
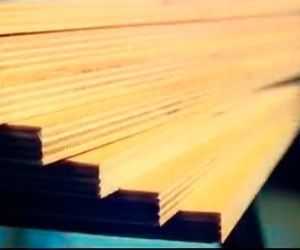
Финальный вариант
Оборудование для бизнеса
Количество и качество станков может варьироваться, зависимо от количества предполагаемого продукта. Но будут необходимыми, по минимуму, следующие станки:
- калибровочный, снимает верхние слои дерева;
- лущильный, снимает основную часть шпона;
- раскроечный, разрезает полотно на необходимого размера листы.
Во сколько может обойтись закупка такого оборудования? К примеру, по оценкам экспертов, сегодня полуавтоматическая линия в цеху может «вылиться в копеечку»: придется выложить от 50 до 65 тыс. долларов. Ну, или прокредитоваться, тогда организация бизнеса на производстве фанерных листов обойдется еще дороже.
Кстати, кроме изготовления обычной, можно производить, к примеру, ламинированную. Изготовление и применение подобного продукта очень востребовано. И заключается в добавочном этапе – покрытии полученного материала пленкой.
Есть ли у вас план?
Приведем наглядный пример. Бизнес-план по открытию цеха производства ФК, нешлифованной фанеры ФК (минимум первоначальных вложений). Для произведения кубометра данного материала требуется примерно 1,5 — 1,8 кубометров бревна березы. Допустим, средняя стоимость его — 2000 р. Допустим, цех обладает мощностью производства 50 кубометров готового листа в месяц. Считаем затраты на цех, они составят:
Таблица калькуляции расходов
Каких результатов ждать?
При загрузке в 50 кубов в месяц, при рыночной цене ФК около 17 тыс. р. За куб, валовый доход будет составлять около 850 тыс. р., при рентабельности около 30%, а чистая среднемесячная прибыль — около 220 тыс. Следовательно, окупаемость денежных вложений в дело – около года.
Но все это при налаженном производстве и рынках сбыта – а везде имеются свои подводные камни.
Подводим итоги
Производство фанерного листа различного сортамента – довольно серьезное и увлекательное дело. Однако, следует помнить, что выстроить с нуля, добиться устойчивой прибыли для крупного производства не каждому будет по силам. Потому и начинать рекомендуют с организации мини цеха, а по времени уже, наработав опыт и навык в технологическом процессе и в управлении персоналом, наладив сбыт продукции, наращивать объем производства фанеры.
Смотрите видео по теме:
viascio.ru
Производство фанеры | Изготовление фанеры
Производство фанеры в настоящее время довольно трудоемкий технологический процесс. История фанеры берет свой отсчет с 15 века до нашей эры. Первые же механические станки для изготовления фанеры были изобретены в 1819 году в Англии, российским подданным, профессором Фишером. С момента создания первого станка технологический процесс производства фанеры существенно усовершенствовался. Но в целом процесс изготовления основан на тех же принципах, что и в первых механических станках.
Изготовление фанеры состоит из нескольких этапов
Выбор древесины
Этот этап характеризуется подбором и подготовкой бревен древесины. Бревна предназначенные для изготовления фанеры называют фанерным кряжом. Доставляют их до места обработки чаще всего железнодорожным транспортом. Для производства могут применяться как лиственные породы древесины – береза, липа, ольха, так и использоваться хвойные породы. Из лиственных пород наиболее часто используется береза. Обусловлено это во многом определенным расположением годовых колец в строении ствола дерева, а также малым количеством сучков. Кроме того, березу отличает средняя плотность порядка 650 кг/м3. Благодаря этим качествам из березового шпона возможно изготовление фанеры различных сортов. К примеру, у других пород древесины, таких как ясень, бук или дуб, при получении шпона часто встречается разрыв волокон и выкрашивание сучков.
Подготовка древесины
Непосредственно перед обработкой древесины необходимо ее подготовить. Процесс подготовки заключается в необходимости придания большей пластичности древесине и увеличения ее влажности. Для этого бревна подвергаются гидротермическому воздействию. Эта процедура подразумевает обработку паром бревен, либо помещением их в воду. В настоящее время в большинстве случаев бревна помещают в специальные бассейны с нагретой водой. Наиболее оптимальная температура воды для березовых бревен составляет порядка 40ºС. Такая температура относится к мягкому режиму. Бывает и жесткий режим. В этом случае температура воды достигает 60-80ºС. Более предпочтителен режим при 40ºС. При этом режиме увеличивается время подготовки древесины, но качество получаемого шпона остается очень высоким. Вымачивают бревна при мягком режиме в летний период до суток, в зимний период до двух суток.
Происходит этот процесс следующим образом. Деревянные бревна помещают в такие бассейны и потом закрывают их крышкой. В зависимости от периода (летний или зимний) выдерживается необходимое время. При этом в бассейн добавляется горячая вода для поддержания нужной температуры. Благодаря данной операции при дальнейшем получении шпона он стремиться вернуться в форму цилиндра. Так как высокая пластичность древесины обеспечивает получения листа шпона с низкими внутренними деформациями.
Предварительная обработка древесины
Предварительная обработка древесины называется окоркой бревен. Из названия понятно, что с бревен удаляют кору. Получившиеся при окорке бревен отходы перемалывают в измельчительных машинах и уже после используют для изготовления ДСП. Камера металлоискателя позволяет определять инородные металлические включения в бревне. Затем оно поступает на распиловочный станок. На этом станке бревна нарезают в чураки. Чурак – кусок бревна длиной от 1,3 до 1,6 метра. При нарезке чураков также удаляют негодные части древесины. Далее такие куски отправляются на участок получения шпона.
Процесс получения шпона
К следующему этапу изготовления фанеры относится процесс получения шпона. Всего насчитывают три основных способа получения шпона. Это лущение чураков на специальном круговом станке, пиление чураков на полосы, а также строгание чураков. Получение шпона процессами пиления и строгания характеризуются низкой экономичностью и малой производительностью, а потому в настоящее время практически не используются.
На лущильных станках чураки режутся в поперечном сечении. Заготовка устанавливается на круговой станок и вращается вокруг своей оси. Путем подведения специального лущильного ножа срезается тонкая часть древесины. Так и нарезается лента шпона. Длина и ширина такой ленты зависят от габаритов чурака и от необходимой толщины самой ленты шпона. Далее такая лента нарезается в стандартные размеры 1,3 или 1,6 м. Листы шпона укладывают стопками и передают на сушку. Некондиционный же шпон поступает на измельчение и дальнейшую переработку.
Наглядное видео по лущению березового шпона
Сушка и ремонт шпона
Сушка шпона осуществляется на специальном конвейере. На нем шпон подвергается обработке теплым воздухом. Затем при помощи специального сканера и влагомера происходит его сортировка. Некондиционные и влажные листы отбраковываются и отправляются на ремонт или досушку.
Починка шпона осуществляется путем вырезания некондиционных фрагментов. Вместо них вставляются куски нового шпона, который подбирается по цвету и фактуре. Толщина нового куска шпона должна полностью соответствовать толщине начального листа. При этом минимально допустимая ширина не должна быть меньше 450 мм. При этом влажность новой части должна быть меньше на 2-4% изначального листа.
Прошедший проверку сканером и влагомером шпон выдерживают на специальном складе хранения в течении суток. Этого времени достаточно, чтобы влажность всех листов стала одинаковой. Ремонтированные листы выдерживают не более 8 часов. Далее шпон передается на участки склейки.
Склейка шпона
Полосы шпона, имеющие различные дефекты отправляются на ребросклейку. Благодаря этой операции получается полотно из склеенных полос шпона. Далее такие полосы стыкуются и склеиваются. Готовая лента полос режется в стандартные размеры.
Стоит отметить, что готовые листы шпона имеют поперечное направление волокон. Однако, необходимая прочность цельных листов фанеры достигается путем попеременного расположения волокон в листах шпона. Достигается это следующим способом. Листы шпона разрезаются пополам, затем в каждом листе формируется специальный выступ и паз для усового соединения.
Видео по нанесению клея на листы шпона
На паз одного из листов наносится специальный клей и отправляется в пресс. В специальном прессе под действием высокой температуры и большом давлении происходит склейка листов шпона. Количество листов шпона в фанерном листе должно быть нечетным. После того, как готовые листы просохнут, их нарезают в нужные размеры.
Дополнительная обработка листов фанеры
В зависимости от марки и степени обработки может производиться дополнительная обработка листов. Часто листы подвергают дополнительной шлифовке. При этом могут быть отшлифованы как обе стороны фанеры, так и только одна.
Также листы для придания более высокой износоустойчивости могут пройти процесс ламинирования. Для этого листы покрывают специальной пленкой. Такая пленка дополнительно защищает фанеру от воздействия влаги. Ламинированная фанера очень часто используется в опалубке, где необходимо многократное использование листов.
Упаковка готовых листов
На этапе упаковки листы укладываются в пачки нужного количества и передаются на отгрузку или склады хранения.
В целом процесс изготовления фанеры можно представить в виде схемы:
Заключение
Изготовление фанеры длительный и трудоемкий процесс. В настоящее время в России качество фанеры регламентируется ГОСТ 3916.1-96. Четкое следование всем технологическим процессам производства фанеры позволяет получать готовый материал высокого качества. Такой материал можно эксплуатировать длительное время.
mosfanera.ru
как делают материал (видео), оборудование для изготовления, производители
Изготовление листовой продукции из древесной основы осуществляется с соблюдением очередности этапов. Производство фанеры по точной и продуманной схеме обеспечивает достижение качественного результата. Характеристики плит зависят не только от условий изготовления, но и от применяемого сырья и способа его компоновки.
Какая бывает фанера?
Классификация по типу обработки:
- ФК. Влагостойкая продукция на карбамидных клеях. Назначение материала – обшивка внутренних конструкций, а также изготовление предметов интерьера и упаковочной тары. Плиты хорошо подходят для укладки на пол под ламинат и паркет в помещениях с высокой проходимостью.
- ФСФ. Фанера с повышенной влагостойкостью. Для производства применяется фенолформальдегидный клей. Материал обладает улучшенными свойствами, позволяющими размещать листы на участках, которые испытывают серьезные нагрузки. Высокие показатели влагостойкости обеспечивают долговечность и возможность использования для кровельных работ.
Визуально фанерные листы разных классов могут быть похожи, но эксплуатационные характеристики у них порой отличаются довольно сильно
- ФБС. Бакелитовая фанера, пропитанная спирторастворимой смолой. Такая продукция выдерживает постоянные колебания температуры и устойчива к воздействию воды. Обработка также повышает сопротивляемость огню, что позволяет использовать изделие в разных условиях.
- ФБА. Изготавливается на основе альбумино-казеинового клея, отличается более высокими показателями экологической безопасности, но не обладает защитой от влаги.
- БВ. Для производства применяется бакелитовая водорастворимая смесь. Является альтернативой ФБС, но не имеет устойчивости к повышенной влажности.
- ФОФ. Улучшенная вариация ФСФ с облицовкой бумагой высокой плотности, пропитанной синтетическими смолами.
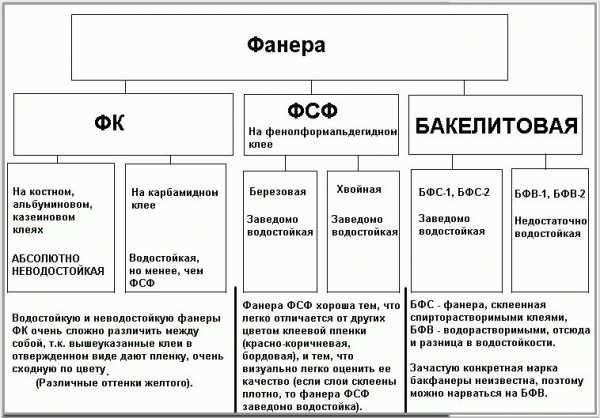
Сорта продукции по качеству используемого для изготовления шпона:
- I – на поверхности встречается минимальное количество дефектов;
- II – допускается небольшое коробление, наличие трещин и вставки из древесины для исправления недостатков;
- III – имеет все описанные дефекты, а также червоточины размером до 6 мм;
- IV – продукция с множеством изъянов, разрешается неровность кромок не более 5 мм.
Следует знать! Допускается комбинирование сырья, тогда фанерные листы имеют дробную маркировку. Например, 2/4 означает, что одна сторона более высокого качества (второго сорта), а обратная включает дефекты.
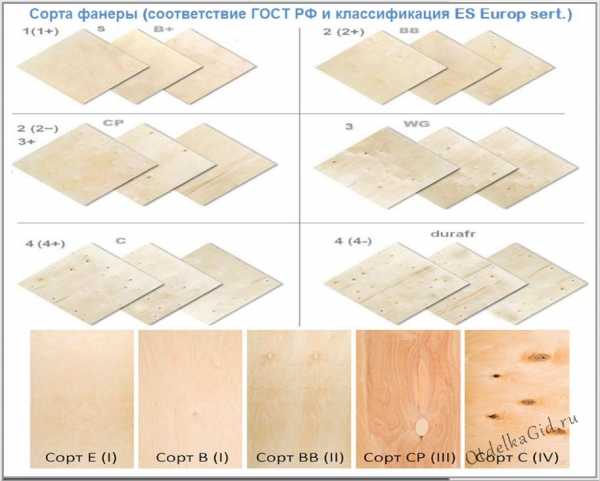
Из какого дерева изготавливают материал?
Производить продукцию можно из древесины хвойных и лиственных пород. Наиболее популярны следующие варианты:
- Береза. Характеризуется твердой структурой, обеспечивает отличное соединение плит между собой, поэтому подходит для получения тонкого и прочного шпона. Готовые изделия можно подвергать любой обработке, в том числе перфорации, без образования серьезных трещин и сколов.
- Ольха. Такой шпон не подвергается усыханию, а постоянное воздействие воды и высоких температур не приводит к появлению деформаций. Используется в качестве дополнения к более дешевому шпону.
- Липа. Обладает близкими с предыдущим вариантом параметрами. Относится к древесине, которая имеет однородную структуру, что обеспечивает образование ровного шпона при лущении.
- Хвойные (сосна, ель, пихта, лиственница и кедр). При обработке этих материалов могут возникать сложности, поскольку часто наблюдается неоднородность структуры годичных колец, особенно у сосны. По прочности такая фанера уступает березовой, но имеет меньший вес, что облегчает самостоятельную транспортировку и укладку. К тому же за счет натуральных смол изделия более устойчивы к появлению плесени и грибка.
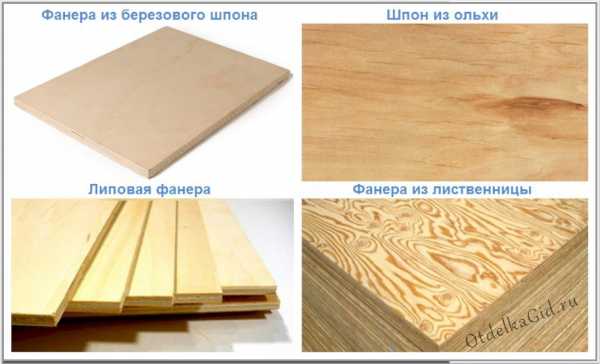
Таким образом, продукцию можно изготовлять из различных сортов, но наибольшую востребованность имеют береза, сосна и ель. Для удешевления материалы могут комбинироваться.
На заметку! Поверхность из лиственных пород имеет более однородную структуру, лицевое покрытие хвойных плит выделяется разводами и многочисленными сучками.
Как делают фанеру
Технология производства включает множество процессов, поэтому в домашних условиях качественного результата добиться не получится. Но своими руками можно осуществить фанерование предметов интерьера или поделок.
Оборудование
Чтобы изготавливать листовые изделия, производство должно иметь соответствующее техническое оснащение с конвейерными линиями. Отбор и обработка шпона проводятся вручную.
Необходимое оборудование:
- Калибровочный и окорочный станок. Используются для очистки бревен. В линию дополнительно включается обрезочное устройство. Технология допускает применение различных модификаций с ваннами для мытья и размягчения.
- Специальная установка для лущения. Наиболее популярны автоматические станки, оснащаемые двойными телескопическими шпинделями, между которыми закрепляется заготовка. Процесс контролируется до получения нужного результата. Настройка оборудования позволяет получать шпон разной толщины.
- Гильотина или специальные ножи. Отвечают за обрезку получаемой ленты до нужной длины. Современные агрегаты выполняют работы самостоятельно, укладывая лущеный материал в стопы.
- Сушилка. Обеспечивает нужный уровень влажности без нарушения структуры. Чаще всего применяется устройство тоннельного типа.
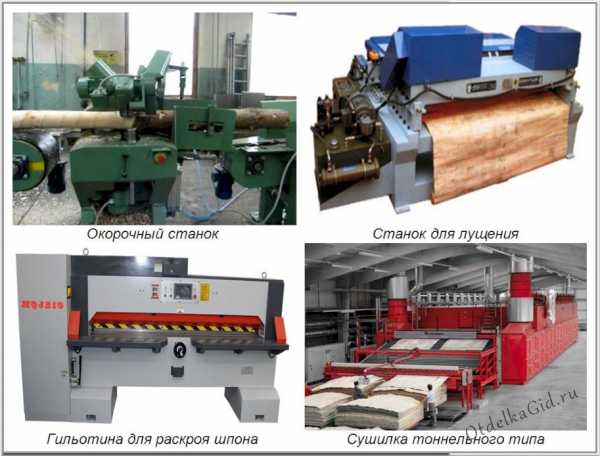
- Комплексная установка для приготовления и нанесения клея. Модификация зависит от вида состава.
- Станки для последовательного склеивания слоев. В технологический участок включено оборудование для первоначального форматирования.
- Холодный и горячий пресс.
- Станки для обработки по длине и ширине.
- Шлифовальные и обрабатывающие устройства. Позволяют получить определенную разновидность плит (например, перфорированные изделия).
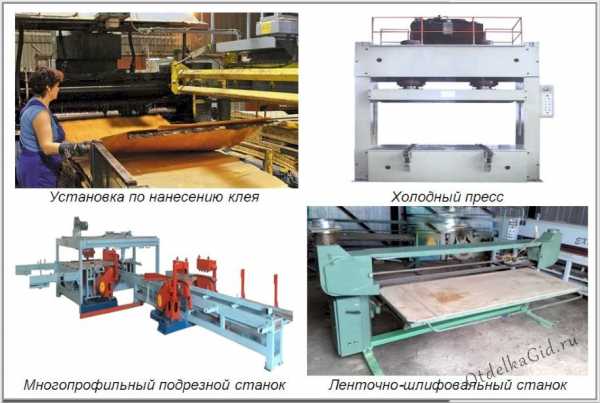
Только качественное и правильно настроенное оборудование обеспечивает производство фанеры, которая будет отвечать всем нормам ГОСТа и потребностям покупателя.
Процесс изготовления
Алгоритм действий:
- Сырье подается на линию калибровки и очистки, где с бревен удаляются сучки и отделяется кора. Материал нарезается на фрагменты нужного размера.
- Получившиеся чурки перемещаются в ванну с горячей водой. В жидкость могут добавляться дополнительные компоненты, отвечающие за сохранение или улучшение определенных свойств. Этот этап необходим, чтобы вся древесина пробрела одинаковую влажность. Также процесс значительно облегчает дальнейшую обработку.
- Бревна помещаются на лущильный станок и фиксируются между двумя валами, которые задают темп вращения. Находящиеся с краю лезвия осуществляют снятие шпона. Можно использовать и другие методы, но лущение является наиболее эффективным.
- Листовой или ленточный шпон помещается на раскроенный станок, где происходит формирование размера. Для этих целей можно применять гильотину или специально настроенные ножи, в зависимости от подачи сырья.
- Наступает этап сушки: передвигаясь по роликовой системе, материал последовательно обрабатывается горячим воздухом. Итогом должна стать продукция с остаточной влажностью 4–6%.
- Шпон подается на проверочный участок, где происходит устранение недостатков и сортировка. Хотя линия производства максимально автоматизирована, часть работы необходимо делать вручную. Сырье распределяется по размеру, осуществляется предварительная очистка и группировка в стопки.
- На материал для сердцевины наносится склеивающая смесь, сверху выполняется облицовка перпендикулярными пластами. Если требуется усилить структуру плиты, то добавляются дополнительные слои.
- Сформированные листы помещаются на участок прессования. В зависимости от используемого клея, применяется холодный или горячий способ. Первый вариант подразумевает сжатие слоев в течение 6 часов при постоянной температуре, второй – применение высокого давления и горячего пресса.
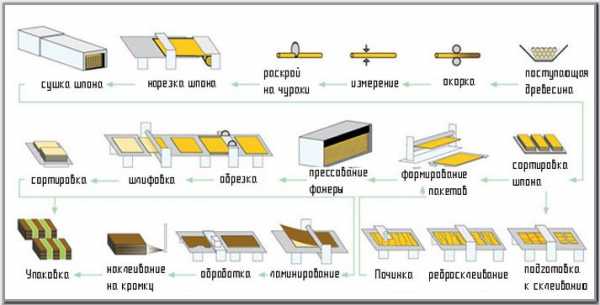
После этого осуществляется конечная обработка, которая позволяет получать материал с необходимой степенью отделки: шлифовка, ламинирование, покрытие различными декоративными составами.
Внимание! От метода прессования и обработки зависит стоимость фанеры.
Обзор производителей
На данный момент популярностью пользуются следующие изготовители:
- Объединенная группа компаний «Свеза». Холдинг включает шесть предприятий, выпускающих качественную продукцию, которая зарекомендовала себя для различных видов работ. Особое внимание заслуживает березовая фанера, отвечающая современным стандартам качества.
- ООО «Сыктывкарский фанерный завод». Основное направление – выпуск большеформатных листов, которые используются для обшивки или изготовления мебели. Также имеется линия производства ламинированной продукции.
- Группа компаний «Юнайтед Панел Груп». Выпускает отличные фанерные материалы 27 форматов с 30 вариантами толщины, специализируется на березовых и ламинированных плитах.
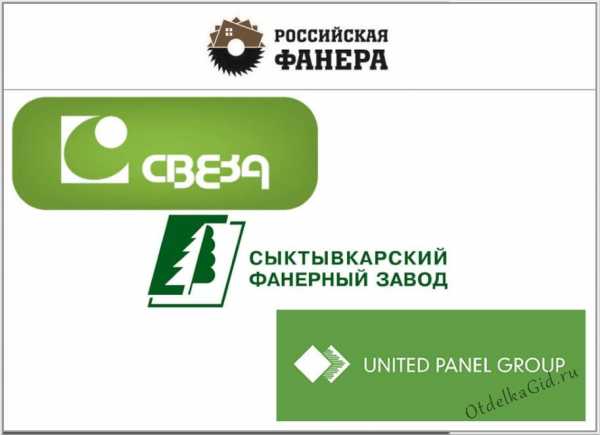
Также часть рынка занимают азиатские производители, качество продукции которых не всегда отвечает заявленным параметрам.
otdelkagid.ru
от «А» до «Я» Лесной комплекс
С развитием монолитного строительства особое значение приобрели опалубочные системы. Делают их из металлического каркаса и ламинированной фанеры, которую благодаря устойчивости к высоким нагрузкам, гладкой поверхности и влагозащищённости можно использовать многократно.
Сегодня мы расскажем о современной технологии производства ламинированной фанеры на примере одного из лидеров в этой отрасли — комбинатов группы «СВЕЗА».
Отбор сырья
Изготовление ламинированной фанеры — сложный многоступенчатый процесс, на каждом этапе которого важна точность соблюдения определённых методик.
Первый этап заключается в тщательном отборе и подготовке сырья. Для производства стандартной для России фанеры (1220х2440 мм) перерабатывают стволы диаметром 20-40 см и длиной 5,2 м (в дальнейшем их можно распилить на чураки по 1,3 или 2,6 м, необходимые для производства продольного и поперечного шпона требуемого формата).
Основным этапом подготовки является проварка сырья. Она осуществляется в специальном бассейне (открытом или закрытом) в течение суток. Летом температура в бассейне держится на уровне 35-40 °С, а зимой — 40-45 °С.
Для повышения качества шпона, из которого впоследствии будет изготовлена фанера, важно, чтобы на этапе проварки соблюдались термический режим и время обработки древесины.
Проваренный фанерный кряж подаётся в отделение по окорке и распиловке.
Окорка осуществляется следующим образом: ножи окорочного станка надрезают кору и снимают её лентами по спирали. В дальнейшем она используется для отопления предприятия и соседних зданий и даже целого посёлка (как на Пермском фанерном комбинате).
Окорённый кряж проходит через металлодетектор, который помогает обнаружить гвозди, остатки проволоки и другие металлические элементы, застрявшие в древесине. В противном случае есть опасность испортить оборудование. На пульт управления станка поступает сигнал, процесс останавливается, и металл удаляется оператором.
После окорки выполняется процесс распиловки. Обработанное сырьё пилится на чураки для производства продольного и поперечного шпона.
Делаем шпон
Следующий этап — лущение шпона на специальных станках, где с подготовленного чурака срезается непрерывная тонкая лента шпона. Чем он тоньше, тем больше слоёв будет в фанере и тем прочнее она будет.
Шпон из российской берёзы — самый тонкий (1,2-1,5 мм) по сравнению с другими породами древесины (например, толщина шпона из тополя 1,6-2,6 мм, а хвойного —
2-4 мм).
На этапе лущения обязательно проводится контроль качества. Для этого каждый день отбирают образцы для проверки толщины и ряда других параметров, а полученные результаты сравнивают с нормативными. С учётом этих данных производится настройка лущильных станков. После лущения лента шпона подаётся на автоматические ножницы, где происходит рубка на форматные листы размером 1,3х2,6 м для производства фанеры формата 1220х2440 мм. Продольный и поперечный шпон (для последующего склеивания в одном листе фанеры) производится на отдельных лущильных линиях.
Затем форматные листы шпона поступаю в сушилку.
«В сушилке листы шпона обдуваются горячим воздухом. За 8-10 минут из древесины уходит до 90% влаги. На выходе листы укладываются на поддон или попадают на транспортёр (в зависимости от конструкции сушилки)», — рассказывает инженер-технолог производства ламинированной фанеры комбината «Фанплит», входящего в состав группы «СВЕЗА» Наталья Андреева.
Сортировка, сортировка, сортировка…
После просушки шпон сортируется по целому ряду параметров, в том числе по наличию выпавших сучков, трещин и т. п. На многих комбинатах на этом этапе используется автоматизированное оборудование: параметры сортов заложены в компьютерную программу, управляющую процессом. Происходит сканирование поверхности и автоматическая оценка, после которой сканер сам управляет раскладкой шпона по стопам. Оператор лишь наблюдает за процессом.
Оценивается влажность листов. Если шпон оказался недосушенным, он откладывается в отдельную стопу и досушивается позже.
Если выявляются дефекты, то листы не утилизируются, а отправляются на починку, которая может осуществляться как на ручных станках, так и на оборудовании с автоматическим управлением. Автоматические станки позволяют повысить качество фанеры, сократив затраты ручного труда в 3 раза. Сейчас существует оборудование для починки шпона любых форматов: как стандартного — 5х5 футов (1525х1525 мм), так и большого — 5х10 футов (1500/1525х3000/3050 мм).
И в заключение этого этапа — снова происходит сортировка шпона.
Комплектование фанеры
Для получения готовой фанеры необходимо склеить несколько листов шпона между собой. Волокна в последовательных слоях располагаются перпендикулярно друг другу, что придаёт прочность готовому продукту и стойкость к деформации в любых направлениях. Эта особенность определяет применимость фанеры в опалубочных системах для монолитного строительства.
При производстве берёзовой фанеры склеивается нечётное количество листов шпона толщиной от 3 до 40 мм. Клей из мела, воды, смолы и древесной или ржаной муки изготавливают здесь же, в специальном смесителе. Важно строгое соблюдение технологии, чтобы не произошло расклеивание. Для этого на современных предприятиях установлено оборудование, которое автоматически контролирует пропорции ингредиентов в соответствии с рецептурой.
Следующий этап — вальцовка. Лист шпона пропускается между двумя валиками, смазанными клеем, после чего его отправляют в наборку.
«В стопе наборного пакета сухой и намазанный клеем шпон чередуются. Их количество зависит от толщины фанеры. В конце процесса комплектования автомат подаёт 2 листа сухого шпона (последний лист предыдущего «сэндвича» и первый следующего), что позволит позже отделить один лист фанеры от другого.
Подготовленная таким образом стопа отправляется на подпрессовку», — комментирует начальник службы качества Пермского фанерного комбината, входящего в состав группы «СВЕЗА» Елена Вершинина.
Холодная подпрессовка пакетов собранного шпона производится непосредственно перед горячим прессованием с целью получения цельных пакетов, удобных для транспортирования и загрузки в горячий пресс. Время холодной подпрессовки составляет 5-10 минут при давлении 1-1,5 МПа.
После этого осуществляется загрузка предварительно склеенных листов в этажерку горячего пресса для окончательного приклеивания при температуре 120-130 ?С и давлении 1,2-1,8 МПа.
После прессования склеенные листы обрезают с четырёх сторон под формат, требуемый заказчиком: к примеру, 1250х2500 мм или 1220х2440 мм с точностью до
3 мм. При производстве ламинированной фанеры станок выполняет предварительную обрезку до размера 1290х2550 мм, чтобы после нанесения плёнки лист можно было ещё раз подровнять, срезав оставшиеся миллиметры.
Далее выполняется шлифование для придания гладкости и выравнивания толщины. Для этого фанера последовательно проходит через шлифовальные ленты с разной зернистостью, после чего её классифицируют по внешнему виду: качество листов оценивает оператор.
Ламинирование
Заключительный этап производства состоит в нанесении с двух сторон плёнки. Затем фанера загружается в многопролётный пресс, в котором одновременно могут находиться 15-18 листов. В процессе прессования плёнка схватывается с поверхностью плиты при температуре 130-136 °С в течение 4,5-10 минут (длительность зависит от плотности плёнки, толщины фанеры и вида покрытия (гладкая или сетчатая).
Благодаря ламинированию фанера приобретает дополнительную защиту от воды, механических повреждений, агрессивных сред. Так, из обычной «белой» фанеры получается фанера с покрытием, или, как её чаще называют, ламинированная. Помимо глянцевой плёнки может наноситься сетчатое покрытие, обладающее антискользящим эффектом. Такая продукция востребована в транспортном машиностроении: она применяется в полах трейлеров и лёгких коммерческих автомобилей. А также в качестве настилов для строительных лесов.
После ламинирования и обрезки фанеру сортируют по внешнему виду и геометрическим параметрам и укладывают в пачки, после чего их подают в покрасочную камеру. Здесь на торцы плиты наносится специальная водоэмульсионная краска на акриловой основе. Такое покрытие защищает фанеру от попадания влаги и разбухания.
Чем лучше прокрашены торцы, тем лучше влагозащитные свойства плиты, а значит, больше циклов заливки бетона фанера сможет выдержать. Особенно это важно для опалубки перекрытий, где фанера подвергается сильным механическим нагрузкам и воздействию агрессивной среды — бетонной смеси.
Если ламинированная фанера хорошо склеена внутри, имеет ровную поверхность, которая покрыта износостойкой плёнкой, и защищённые от влаги торцы, она дольше сохранит свою форму. А это значит, что даже при многократном применении одного и того же листа фанеры (не менее 15-20 циклов) качество монолитных перекрытий будет неизменным.
«Ламинированная фанера особенно востребована в монолитном строительстве. Её популярность объясняется механическими свойствами: только берёзовая фанера, благодаря высокой прочности и упругости, способна выдерживать нагрузки, воздействующие на опалубку в процессе бетонирования», — комментирует Наталья Андреева.
С чего всё начиналось
Первые станки для переработки древесины в шпон, а далее — в фанеру были запатентованы ещё в XVIII веке. Примечательно, что практически все их изобретатели так или иначе связаны с Россией.
Первую модель лущильного станка в конце XVII создал инженер-механик Сэмюэль Бентам, ранее служивший Екатерине II по приглашению князя Потёмкина. По окончании 10-летней службы в России Бентам вернулся в Англию и получил патенты сразу на несколько своих изобретений. Впрочем, изобретённый англичанином станок не был замечен производителями тех времён.
Технология изготовления фанеры практически не изменилась с момента изобретения. Модернизации подверглось управление станками: сейчас оно полностью автоматизировано. Это позволило сократить долю ручного труда и, как следствие, повысить качество конечного продуктаДействительно эффективный прототип всех современных лущильных станков создал шведский инженер-изобретатель Эммануэль Нобель, отец Альфреда Нобеля, основателя Нобелевской премии. Созданная им в конце XVIII века модель ротационного (поворотного) токарного станка позволяла снимать с деревянного чурака шпон определённой и постоянной толщины, благодаря чему фанерный «сэндвич» становился однородным по структуре и толщине.
Эммануэль Нобель жил и работал в России с 1838 по 1859 год, созданные им в этот период изобретения предназначались для военной промышленности и высоко ценились императором Николаем I.
В начале XIX века русский промышленник Дитрих Мартин Лютер, владевший мануфактурой по производству карандашей в эстонском Ревеле (современный Таллинн), изобрёл свой лущильный станок — более крупную версию станка для производства карандашей. В 1819 году он получил патент на своё изобретение.
Первая фанера, производство которой основывалось на станке Дитриха Мартина Лютера, была создана эстонским мебельщиком Александром Лютером, его однофамильцем. В конце XIX века он решил использовать склеенные между собой листы шпона в качестве сидений для венских стульев — мебель получилась лёгкой, прочной и недорогой, благодаря чему на неё возник устойчивый спрос.
Практически одновременно с мебельщиком Лютером фанера была создана русским изобретателем — Огнеславом Степановичем Костовичем, строящем летательные аппараты и остро нуждавшемся в конструкционном материале. В 1881 году он изобрёл арборит — материал, состоящий из склеенных между собой поперёк волокон листов шпона. Лущильный станок и клей для производства фанеры-арборита Костович также изобрёл самостоятельно, причем его фанера обладала высокой устойчивостью к воздействию влаги и была не подвержена гниению.
МНЕНИЕ
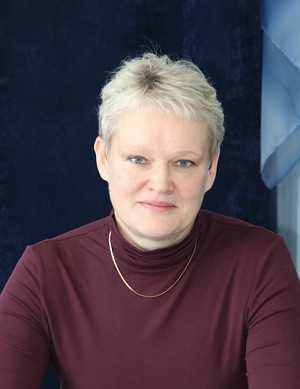
Наталья Андреева, инженер-технолог производства ламинированной фанеры комбината «Фанплит», группа «СВЕЗА»
«Как мы увидели, процесс производства ламинированной фанеры довольно сложен. И качество конечного продукта зависит от чёткого соблюдения технологии на каждом этапе его производства.
Если использовать фанеру ненадлежащего качества, то поверхность стен и перекрытий здания будет неудовлетворительной. Это приведёт к росту трудозатрат на отделочные работы. Поэтому качество фанеры — это не только красота и надёжность зданий, в которых мы живём и работаем, но и экономика рационального строительства».
теги
forestcomplex.ru
Оборудование для производства фанеры: линия и технология изготовления
Производство фанеры является очень сложным, но прибыльным бизнесом. Для открытия предприятия по производству фанеры необходимо, прежде всего, приобрести оборудование, которое используется для этого процесса. Стоит помнить, что качественное оборудование способно значительно упростить процесс производства фанеры.
Оборудование для изготовления фанеры
Для производства фанеры чаще всего используются лущильный, калибровочный и раскроечный станки. С помощью лущильного станка осуществляется получение тонкой поперечной стружки. На этих станках обрабатываются короткие бревна, которые по-другому называются чураки. На суппорте станка устанавливается нож, который при вращении бревна срезает с него слой древесины. Этот слой древесины имеет слой толстой и беспрерывной ленты, которую называют шпоном.
Для улучшения качества шпона и увеличения его прочности во время лущения шпона производится обжим древесины. Для этого используется прижимная линейка.
Калибровочный станок используется для пропуска бревен с сечениями. Благодаря этому станку обеспечивается удаление участков бревен, которые выступают за просветы в нем. Закомелистая часть наиболее толстых бревен обтачивается благодаря наличию калибрующих ножей. Благодаря возможности регулировать положение ножей на роторе можно обрабатывать на этом станке бревна различного сечения. Раскроечные станки предназначаются для раскройки фанеры. Они характеризуются большими габаритами, что позволяет разрезать фанеру на листы разнообразных разрезов.
Для того, чтобы просканировать недостатки отобранного материала используются специальные станки. Ими являются измерители количества влаги, а также конвейеры.
Иногда на производстве фанеры используются линии, благодаря которым осуществляется сортировка шпона.
Технология производства фанеры
Производство фанеры состоит из нескольких этапов. К основным из них относится:
- Подбор материала;
- Снятие коры;
- Снятие слоя шпона на лущильном станке;
- Просушка шпона.
К подбору материала для фанеры необходимо подходить очень тщательно. Зачастую для производства фанеры используют шпон из березы, ольхи, бука, сосны и т.д. Для создания удобств в работе материал проваривается в специальном бассейне. Этот процесс значительно повышает качество сырья.
После этого с древесины снимается кора, а также проверяется материал на наличие металлических элементов. Далее материал поступает на специальное оборудование, которое предназначается для производства фанеры.
На лущильном станке снимаются первый слой шпона, после чего его разделяют на отдельные листы. Качество шпона зависит от вида древесины. При наличии в шпоне большого количества влаги его отправляют на просушку. Далее производится склеивание листов шпона.
Вы можете прямой сейчас узнать какое оборудование для производства сетки рабицы нужно и открыть прибыльный бизнес в этом направлении.
Производство профнастила — замечательный бизнес. Всё об этом Вы можете узнать тут.
Для склеивания шпона используются специальные материалы. Клеящие составы изготавливаются в механизированных смесителях, после чего они подаются желобки нескольких клеевых вальцов. Прокатывается клеящий состав с обеих сторон пиломатериала. Далее промазанные клеем листы шпона склеиваются с помощью пневматических, гидравлических или винтовых прессах.
При склеивании фанеры в комнатной температуре их необходимо продержать в помещении около 6 часов. Наиболее эффективным является прессование фанеры при повышенной температуре. В таких условиях на склеивание шпона уходит всего несколько минут.
В том случае, если производится гнутая фанера, используется специальные инструментальные плиты, которые характеризуются наличием нескольких пресс-форм. Далее фанера поступает на раскроечный станок, где осуществляется ее резка на листы различных размеров. Технология изготовления фанеры напрямую зависит от вида производимого строительного материала.
Линия по производству фанеры
Выпуск фанеры требует наличия специальных линий. Это специализированное оборудование, которое значительно упрощает процесс производства. Работа линии заключается в следующем. Древесина в виде бревна или чурака очищается от разнообразных загрязнений, а также с нее снимается кора. Для этого в течение нескольких часов применяется влаготермическая обработка.
После того, как древесина прошла процесс размягчения, ее закрепляют в специальном станке, который вращается вокруг своей оси. К чураку подводится лущильный нож и с его помощью снимается с него тонкий слой древесины. Благодаря этой процедуре вырабатывается стружка. Эта стружка и становится основой будущей фанеры.
Шпон раскраивается на листы. Эти листы проходят процесс сортировки согласно их качеству. При этом учитывается наличие трещин, сучков и разнообразных незначительных дефектов. Далее листы проходят процесс сушки, после чего их собирают в пакеты. Улаживаются листы в пакеты по принципу перпендикулярности.
Базовый лист фанеры должен быть расположен симметрично. После того, как пакет сформирован, его смазывают специальным клеящим составом. Благодаря клею из отдельных листов шпона образуется единый и цельный лист фанеры. После этого фанера проходит процесс высыхания и охлаждения. На этом процесс производства на линии заканчивается.
Во время производства шлифованной фанеры используются специальные шлифовальные станки, на которых она проходит соответствующую обработку.
В случае изготовления ламинированной фанеры используется специальная пленка, которая наклеивается сверху на фанеру.
Благодаря этой пленке фанера имеет отличные технические характеристики, а также повышенный уровень износоустойчивости. Ламинирование фанеры может быть выполнено как с одной, так и с двух сторон. Водостойкую фанеру во время производства обрабатывают специальными смолами.
Популярные модели оборудования
Лущильный станок СЛ-720
На производствах фанеры используются разнообразные станки. От качества оборудования зависит скорость процесса изготовления фанеры, а также его качество. Именно поэтому к подбору оборудования необходимо подходить очень ответственно. Существует множество фирм, которые занимаются производством оборудования для изготовления фанеры. Наиболее популярными среди станков для производства фанеры считаются:
- Лущильный станок для производства шпона СЛ-720 (1600). С помощью этого станка древесина обрабатывается без дополнительных усилий. Определение оптимального положения оси обеспечивается благодаря наличию специального приспособления. Наличие дебаркера обеспечивает высокое качество начальной обработки чурака. С помощью хорошей фрезы заготовке придается правильная форма. Наличие гибкого гофрированного шланга позволяет беззаботно удалять отходы во время работы.
Хотите открыть свое дело по производству плитки, но не знаете с чего начать? Сперва узнайте, как осуществляется изготовление керамической плитки.
Всё об изготовлении бетона здесь.
Как наладить производство брусчатки? Информация на странице http://buisiness-oborudovanie.com/dlya-dorozhnyx-pokrytij-kamnya/oborudovanie-dlya-proizvodstva-bruschatki/.
- Станок для производства лущенного шпона CЛ-800 (1600) характеризуется наличием специального устройства, с помощью которого устанавливается бревно для его обработки. С помощью этого станка можно обрабатывать заготовки, диаметр которых составляет от 110 до 740 миллиметров. Этот станок способен производить четыре метра шпона в час.
Делительный станок СД-800
Станок делительный для рубки шпона СД-800 (1600). С помощью этого агрегата осуществляется деление ленты шпона на отдельные дощечки или листы необходимой ширины. Задается ширина листа с помощью специального электронного устройства. Использовать этот агрегат необходимо на одной линии со станком по производству шпона. Ширина обрабатываемого шпона может составлять до 1600 миллиметров.
- Калибровочный станок по дереву производится на основе станков эстакадного типа. Наличие высокооборотного привода позволяет управлять скоростью работы станка. Удобства при работе на станке придаются благодаря возможности автоматического управления столом. Благодаря этому агрегату осуществляется калибровка поверхности плиты.
Раскроечный станок по дереву FDB Maschinen FR 6020 предназначается для обработки фанеры. Это изделие характеризуется компактностью, высоким уровнем сборки и наличием специальных устройств, благодаря которым значительно упрощается процесс обработки дерева.
Все станки производятся из материалов высокого качества, что обеспечивает им прочность, надежность и длительный срок эксплуатации. После производства все станки проходят ряд испытаний, что обеспечивает им высокий уровень износоустойчивости, а также значительно упрощает процесс производства фанеры.
Видео про изготовление фанеры
buisiness-oborudovanie.com
Изготовление мебели из фанеры: преимущества материала
Мебель из экологически чистых материалов никогда не утратит своей популярности, однако в поисках новых форм и дизайнерских решений, специалисты по оформлению интерьера все чаще обращаются не к натуральной древесине, а к фанере. Этот материал идеален, так как позволяет изготавливать не только прочную и экологически чистую мебель, но и экспериментировать с формами, линиями изделий – фанера легко поддается резке. При кажущейся простоте внешнего вида этот материал создает особую атмосферу в современных минималистических интерьерах. Изготовление мебели из фанеры – увлекательный процесс, с которым может справиться даже новичок. О свойствах материалах и особенностях работы с ним – сегодняшняя статья.
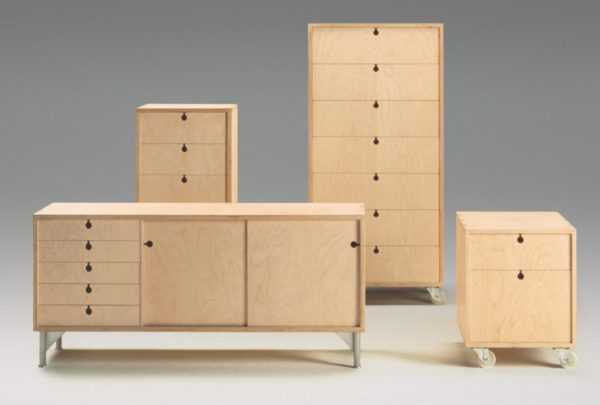
Изготовление мебели из фанеры
Особенности материала
Прежде чем приступать к работе с фанерой, желательно иметь представление об особенностях этого уникального материала – это позволит правильно изготовить мебель, которая прослужит много лет. Преимущество фанеры заключается в простоте работы с ней, она не требует применения дорогостоящих специальных инструментов для обработки.
Из основных особенностей фанеры можно выделить следующее:
- Невысокую стоимость, что позволяет за небольшие деньги самостоятельно изготовить функциональные, практичные и эстетически привлекательные предметы обстановки: детскую мебель, стеллажи и шкафы, тумбы и комоды, мебель для кухни, декоративные ширмы и перегородки.
- Чтобы изготовить уникальную мебель из фанеры не обязательно иметь особые навыки.
- Фанера – идеальный материал для изготовления детской мебели, так как она экологически чиста и безопасна.
- Фанера может быть декорирована различными способами, что существенно расширяет модельный ряд изделий.
Природный рисунок на поверхности фанерной мебели
- Эксплуатационные характеристики материала говорят о его стойкости к механическим воздействиям и влаге, высокой прочности и долговечности.
- При обработке современными средствами фанера становится более устойчивой к возгоранию.
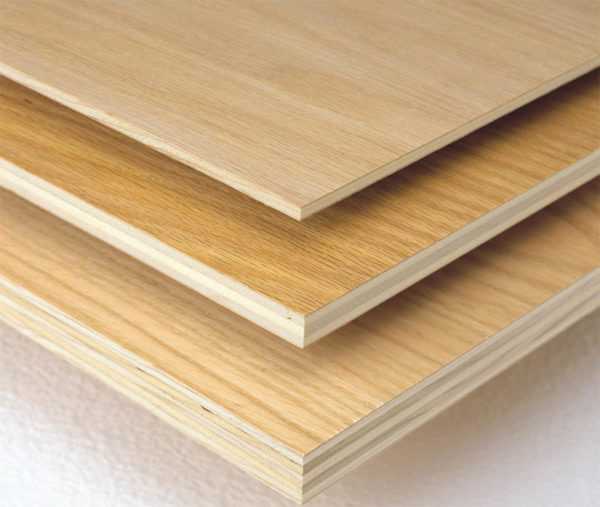
Фанера имеет разную толщину, что позволяет выбирать необходимый материал в зависимости от назначения детали
На что обратить внимание при выборе фанеры
Для изготовления фанеры применяется шпон из древесины хвойных пород или березы. Для хвойной фанеры характерен более привлекательный внешний вид и прочность. Листы шпона склеиваются между собой при высокой температуре и давлении, образуя монолитную плиту заданной толщины. При этом каждый слой укладывается перпендикулярно предыдущему – это делает фанеру устойчивой перед деформациями.
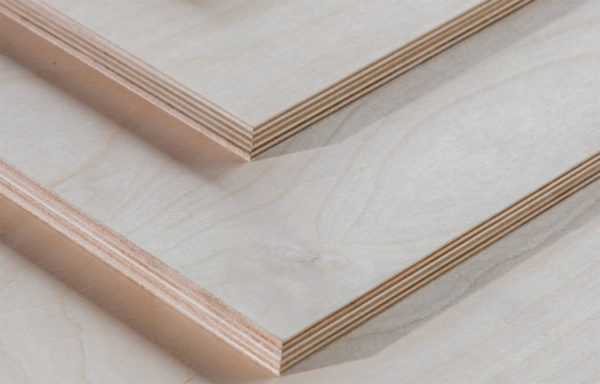
Березовая фанера
Фанера бывает шлифованной и нешлифованной, а также, в зависимости от эксплуатационных свойств, делится на несколько категорий.
Таблица 1. Категории фанеры
Внешний вид материала и маркировка | Описание |
---|---|
![]() ФОФ | Лицевой слой этой влагостойкой ламинированной фанеры имеет специальное покрытие в виде пленки ПВХ, которое обеспечивает дополнительную защиту от влаги. |
ФСФ | Для склеивания листов применяется формальдегидные смолы, поэтому этот материал не желателен для изготовления мебели, не смотря на то, что фанера этой марки отличается высокой влаго- и износостойкостью. |
![]() ФК | Эта разновидность материала обладает широким спектром применения. ФК-фанера – прочная, влагостойкая и экологически безопасная, поэтому широко применяется для оформления интерьеров и изготовления мебели. |
ФБС | При изготовлении бакелитовой фанеры применяется одноименный лаковый состав, которым пропитывают каждый лист шпона, а затем при помощи него же склеивают все слои плиты. Материал характеризуется уникальными эксплуатационными качествами: прочностью, долговечностью, стойкостью к деформациям, агрессивным веществам. Фанера этого типа экологически безопасна, поэтому может применяться для изготовления детской мебели. |
ФБА | Для склеивания шпона при производстве этого типа фанеры применяется натуральный альбуминоказеиновый клей, благодаря чему материал получается экологически чистым и безопасным. Однако влагостойкость фанеры марки ФБА невысокая. |
Обратите внимание! Наиболее безопасной является фанера, изготовленная в соответствии с сертификатом безопасности Е1 и Е0.
Толщина листов фанеры варьируется от 1,6 до 76 мм, чаще применяются листы с толщиной от 6,4 до 19 мм.
Цены на листовую фанеру
Фанера листовая
Способы обработки фанеры
Независимо от навыка работы с древесиной и материалов из нее, необходимо заранее изучить способы реза фанеры, так как изготовление мебели из нее предусматривает нарезку деталей в соответствии с чертежом. Нюанс заключается в том, что лист фанеры необходимо разрезать без разрыва. Использовать для этого можно разные инструменты, но чаще всего детали из фанеры вырезают при помощи электролобзика, являющегося наиболее дешевыми доступным устройством. Качественный результат во многом зависит от правильно подобранной пилки.
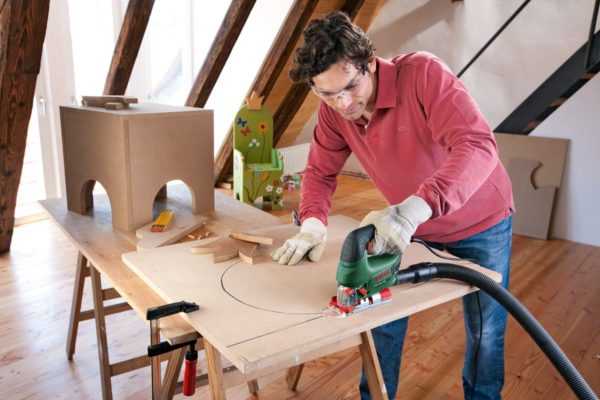
Для уменьшения образования древесной пыли при раскройке материала, лобзик подключают к пылесосу
Чтобы не получить скола в месте реза можно поступить двумя способами: предварительно надрезать линию канцелярским ножом или по обеим сторонам разметки наклеить скотч и выполнить рез лобзиком.
Метод реза через скотч и результат
Если оборудование оснащено маятниковым ходом, то его необходимо отключить.
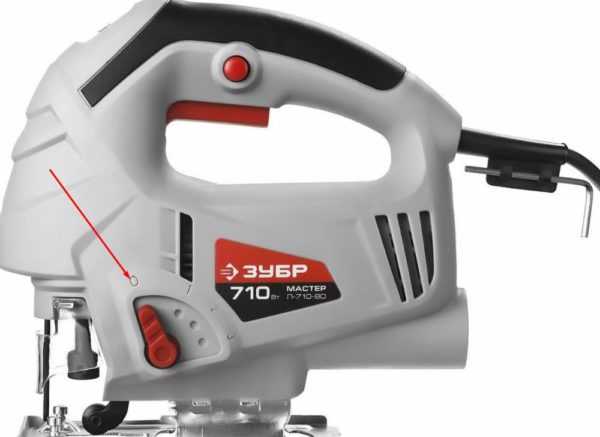
Регулятор маятникового хода устанавливают на значение «0»
Цены на популярные модели электролобзиков
Электролобзик
Результаты реза с включенным и выключенным маятниковым ходом
Некоторые электролобзики оснащены противоскольным вкладышем. Чтобы его установить, лобзик отключают от сети!
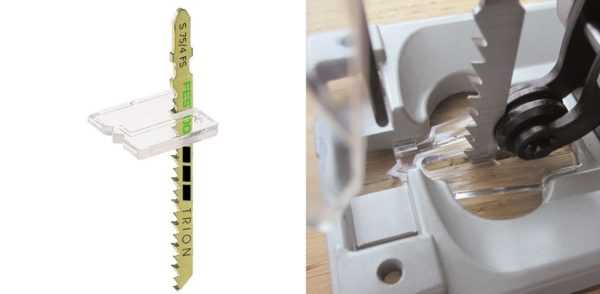
Принцип действия противоскольного вкладыша для электролобзика
Конструкция этой насадки такова, что пилка электролобзика движется внутри ограничивающей прорези.
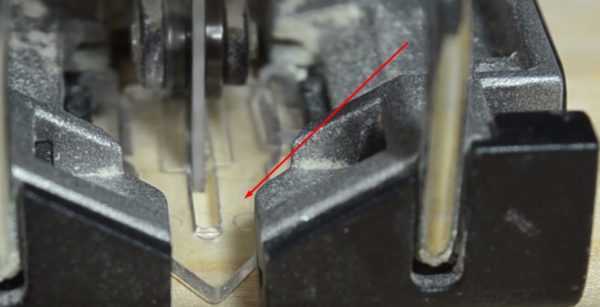
Движение пилки при использовании ограничителя
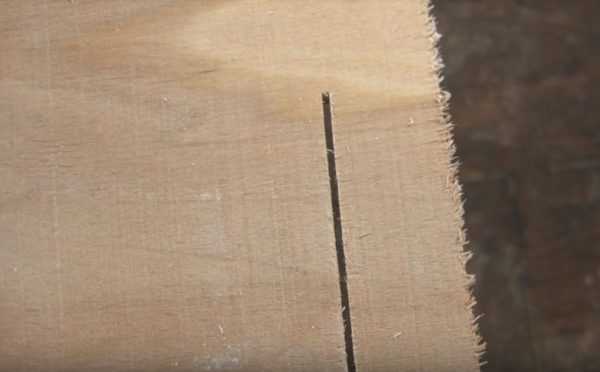
Результат реза фанеры лобзиком с противоскольным вкладышем
Таблица 2. Причины, по которым не получается изготовить прямолинейный рез
Изображение | Описание |
---|---|
![]() Причина 1 | Подошва лобзика не выставлена перпендикулярно. |
![]() Причина 2 | Материал имеет большую толщину, а лобзик – недостаточную мощность для реза. |
![]() Причина 3 | Изначально кривое расположение пилки в недорогом лобзике. |
![]() Причина 4 | Чрезмерное давление на лобзик в процессе реза. |
![]() Причина 5 | Затупившаяся пилка. |
Подготовка к изготовлению фанерной мебели
Приступать к изготовлению мебели из фанеры можно после того, как приобретены все необходимые инструменты и материалы. В процессе работы потребуется следующее:
- Фанерные листы. Толщина используемых фанерных листов зависит от предстоящей нагрузки на деталь и ее назначения. Для изготовления прочного каркаса и полок применяют материал толщиной 18 мм. Для фасада хватит толщины не более 12 мм. Дверки навесных шкафов, которые фиксируются при помощи ребер жесткости, могут быть изготовлены из фанеры толщиной 6 мм.
- Крепеж. Для обеспечения надежного и эффективного крепления отдельных деталей конструкции между собой применяется специальный крепеж – видимый и скрытый. Для крепления отдельных деталей используют шурупы. С помощью клея или силиконового герметика можно дополнительно зафиксировать отдельные элементы конструкции.
- Важным элементом мебели является фурнитура, которая применяется для обеспечения функциональности конструкции и формирует ее декоративный облик. Сюда относятся: ручки, навесы, доводчики, колесики, ограничители.
- Материал для декоративной отделки: лак, морилка, пленка, шпаклевка.
- Из инструментов потребуется: электролобзик, измерительные инструменты (рулетка, угольник), струбцина и поперечный зажим, наждачная бумага, шуруповерт.
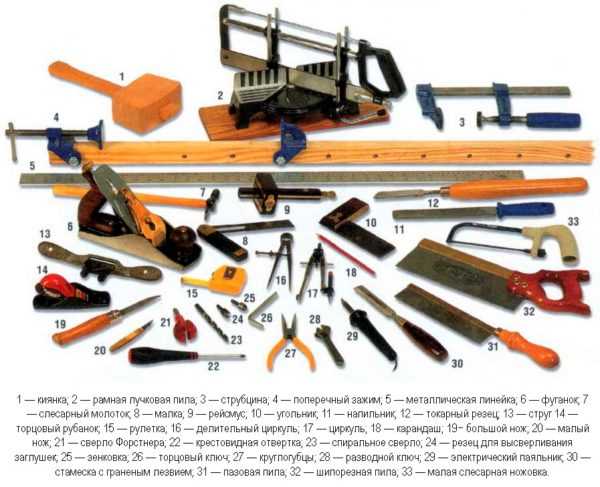
Инструменты
Пошаговая инструкция изготовления простых предметов обстановки из фанеры
Начинать изготовление фанерной мебели рекомендуется с наиболее простых конструкций, постепенно приобретая и совершенствуя навык работы с этим материалом.
Кресло-качалка
Самостоятельное изготовление кресла-качалки станет отличным вариантом испробовать свои силы в столярном деле. И не стоит бояться того, что мебель будет иметь некоторые изъяны – недостатки можно скрыть при помощи окрашивания или декоративного текстиля.
Таблица 3. Изготовление кресла-качалки
Иллюстрация | Описание |
---|---|
Фанера | Для изготовления такого кресла потребуются фанерные листы толщиной 15, 10 и 4 мм. |
Этап 2: изготовление эскиза. | Сначала необходимо изготовить лекала для раскройки деталей. Чертеж выкройки выполняют на плотной бумаге или картоне в масштабе 1:1. |
![]() Этап 3: раскрой деталей | Лекала вырезают и с их помощью переносят контуры детали на фанерные листы, стараясь уместить их как можно экономичнее. |
![]() Этап 4: подготовка к сборке | Детали вырезают при помощи электролобзика. Сразу в необходимых местах изготавливают отверстия для крепежа. Перед тем как приступать к сборке изделия, все детали необходимо тщательно отшлифовать. Сразу же потребуется загрунтовать и покрасить детали. |
![]() Этап 5: изготовление сидения и спинки | Для изготовления спинки и сидения используют фанерные планки, которые при помощи клея фиксируют на тонких листах фанеры толщиной 4 мм. |
![]() Этап 6: сборка каркаса | Сначала собирают каркас изделия. |
![]() Этап 7: сборка сидения и спинки | После этого фиксируют спинку и сидения. Места крепления маскируют планками. |
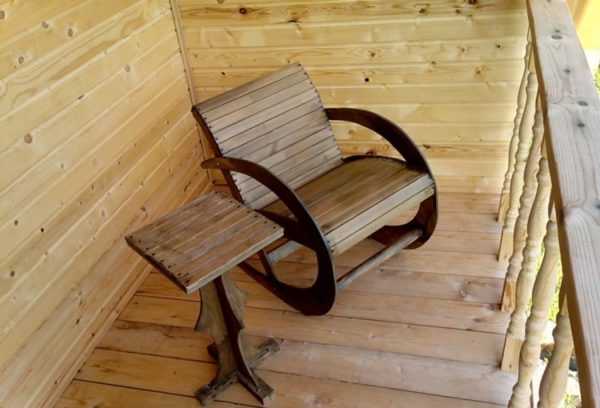
Готовое кресло-качалка
Табурет из фанеры
Табурет – это простой в исполнении и универсальный в применении предмет обстановки. Чтобы изготовить его из фанеры потребуется следующее.
Таблица 4. Изготовление табурета
Иллюстрация | Описание |
---|---|
![]() Шаг 1: разметка | На фанере толщиной 20 мм, шириной 200 мм и длиной 430 мм размечают ножку табурета. Форму ножек рекомендуется продумать заранее, выполнив эскизный чертеж. Деталь вырезают при помощи электролобзика. Ее используют в качестве шаблона для изготовления еще трех таких же деталей. |
![]() Шаг 2: раскрой | Деталь вырезают при помощи электролобзика. Ее используют в качестве шаблона для изготовления еще трех таких же деталей. |
![]() Шаг 3: шлифовка | Вырезанные детали шлифуют. |
![]() Шаг 4: изготовление сидения | Сиденье имеет размеры 320 х 320 мм. Вырезав квадрат, при помощи лобзика углы делают скругленными. |
![]() Шаг 5: шлифовка сидения | Сиденье шлифуют сверху и с торцов. |
![]() Шаг 6: фрезерование сидения | Все детали обрабатывают полукруглой фрезой, которую можно заменить наждачкой. |
![]() Шаг 7: фрезерование ножек | Фрезой также обрабатывают ножки будущего табурета. |
![]() Шаг 8: подготовка к сборке | Изготавливают отверстия под саморезы. |
![]() Шаг 9: подготовка отверстий под саморезы | Затем, при помощи сверла большего диаметра отверстия зенкуют, чтобы шляпки крепежа были утоплены при вкручивании. |
![]() Шаг 10: сборка изделия | Приступают к сборке изделия. Чтобы исключить расслоение фанеры детали засверливают сверлом № 3 и закручивают саморезы. |
![]() Шаг 11: фиксация ножек | Крепление ножек крест-накрест получается очень прочным за счет того, что каждая ножка будет держаться на 4 саморезах. |
![]() Шаг 12: нанесение разметки | Ножки устанавливают на крышку и наносят разметку так, чтобы по центру каждой ножки располагалось отверстие под саморез. |
![]() Шаг 13: подготовка отверстий | В крышке высверливают отверстия согласно разметке. Отверстия зенкуют. |
![]() Шаг 14: сборка изделия | Изделие собирают при помощи саморезов. |
![]() Шаг 15: окончательная обработка | После того как изделие собрано, отверстия шпаклюют и покрывают лаком. |
Цены на популярные модели шуруповертов
Шуруповерты
Прикроватная тумба
Несложной в изготовлении считается прикроватная тумба. Сделать ее самостоятельно можно следующим образом.
Таблица 5. Изготовление прикроватной тумбы
Иллюстрация | Описание |
---|---|
![]() Шаг 1 | Раскрой материала осуществляется согласно чертежу и выбранным размерам деталей. Чтобы при раскрое фанера не трескалась под нее можно подложить пару листов пенополистирола. |
![]() Шаг 2 | Для окантовки деталей используют планки, вырезанные из 4-х миллиметровой фанеры. Фрезой убирают выступающие излишки. |
![]() Шаг 3 | Затем кромки шлифуют. |
![]() Шаг 4 | Для сборки тумбочки применяются березовые мебельные шканты 8 х 40. Под них высверливают отверстия. |
![]() Шаг 5 | В отверстия забивают шканты. |
![]() Шаг 6 | Собирают каркас тумбы, вставляя шканты в отверстия, предварительно смазывая их клеем. |
![]() Шаг 7 | При сборке ящиков используется шиповое соединение. |
![]() Шаг 8 | Для этого заготовку размечают под шиповое соединение. |
![]() Шаг 9 | Отверстия согласно разметке надрезают при помощи лобзика. |
![]() Шаг 10 | А затем выдалбливают при помощи стамески. Во избежание образования сколов с внутренней стороны слегка надбивают, а с лицевой полностью отбивают паз. |
![]() Шаг 11 | В месте крепления дна из шестимиллиметровой фанеры деталь фрезеруют. |
![]() Шаг 12 | При сборке ящика пазы смазывают клеем. |
![]() Шаг 13 | Фасад крепят на саморезы. |
![]() Шаг 14 | Внутри тумбы и на боковинах ящика закрепляют направляющие. |
Таблица 6. Изготовление основания тумбы
Иллюстрация | Описание |
---|---|
![]() Шаг 1 | Для изготовления основания используют 4 детали со скошенными под 45 градусов краями. |
![]() Шаг 2 | Детали рамки фиксируются на шканты и склеиваются. |
![]() Шаг 3 | Торец детали и вставленный в заранее подготовленное отверстие шкант, смазывают клеем. |
![]() Шаг 4 | Конструкцию стягивают и оставляют сохнуть. |
![]() Шаг 5 | К основанию приклеивают и фиксируют ножки. |
![]() Шаг 6 | На торцы основания приклеивают кромки. |
![]() Шаг 7 | Фрезером выравнивают кромку. |
![]() Шаг 8 | По периметру основания снимают фаску. |
![]() Шаг 9 | Основание шлифуют. |
Цены на популярные модели эксцентриковых шлифмашин
Эксцентриковая шлифмашина
Таблица 7. Сборка изделия и его окрашивание
Иллюстрация | Описание |
---|---|
![]() Шаг 1 | Ящики покрывают бесцветным паркетным лаком. |
![]() Шаг 2 | Каркас собирают на шканты и клей ПВА. |
![]() Шаг 3 | Выполняют окрашивание за два раза – первый слой наносят кистью, второй – распылителем. |
![]() Шаг 4 | На завершающем этапе изделие покрывают маслом с твердым воском. |
Видео — Прикроватная тумба из фанеры своими руками
Способы декорирования фанерной поверхности
После того, как изделие собрано можно, приступать к его декорированию. В некоторых случаях достаточно покрыть фанеру защитным матовым прозрачным лаком – это позволит сохранить ее оттенок и рисунок. В иных случаях используют методы отделки поверхности, которые меняют изначальный оттенок изделия – обработка маслом, окрашивание.
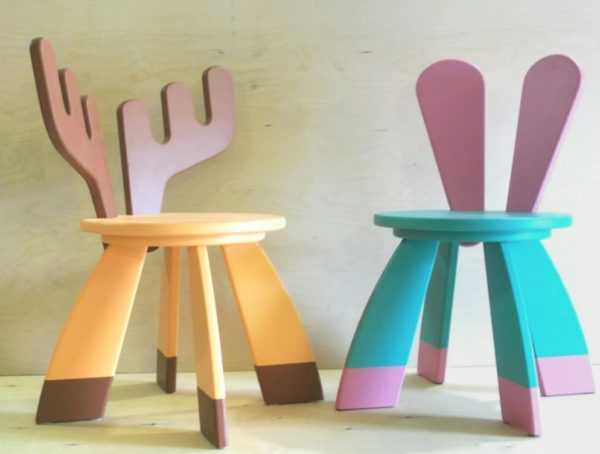
Оригинальную форму детской мебели подчеркнуть яркие цвета
Яркие, сочные оттенки при окрашивании применяются в случае, когда форма и цвет изделия доминируют.
Скворечник из фанеры – это отличная возможность одновременно позаботиться о пернатых и попрактиковаться в столярном деле. Собственноручно созданный домик для птиц сможет украсить балкон многоэтажного дома или садовый участок. Рабочий процесс несложный, нужно лишь следовать правилам и рекомендациям. О них и расскажем в специальной статье.
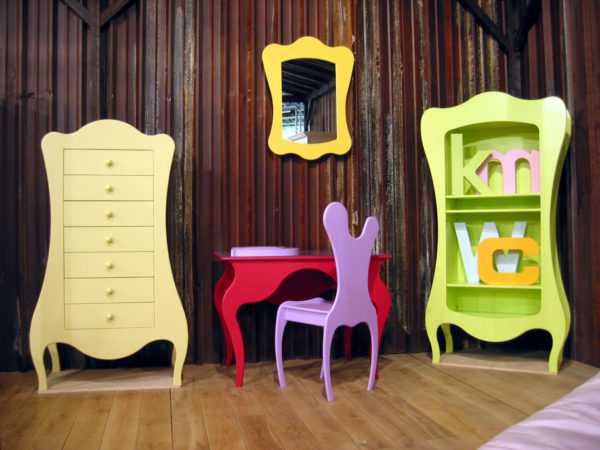
Набор детской мебели из фанеры
Один из оригинальных способов декорирования мебели из фанеры – техника «декупаж». Актуален такой способ декорирования для мебели в стиле винтаж, Прованс, шебби-шик. С помощью такой технологии можно разнообразить внешний облик мебели с простой формой.
Стоит заметить, что техника «декупаж» проста в исполнении и не требует особых навыков: основание грунтуют, сверху приклеивают рисунок и покрывают лаком.
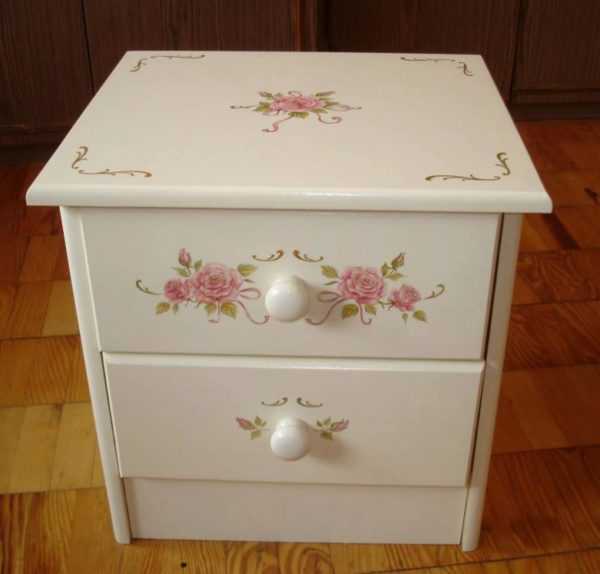
Декор, выполненный в технике «декупаж»
Таблица 8. Декорирование фанерной столешницы
Иллюстрация | Описание |
---|---|
![]() Шаг 1 | Поверхность столешницы шлифуют при помощи наждачной бумаги. |
![]() Шаг 2 | Выполняют грунтовку при помощи акриловой бело краски. Наносить грунт необходимо кистью в два слоя. |
![]() Шаг 3 | Когда грунт просохнет, его верхний слой выравнивают при помощи шлифовки. |
![]() Шаг 4 | Подготовленная поверхность покрывается краской, выбранного оттенка. |
![]() Шаг 5 | По периметру столешницы наклеивают малярную ленту, которая обозначит бордюры. |
![]() Шаг 6 | Бордюры окрашивают в необходимый цвет и после высыхания краски, ленту аккуратно удаляют. |
![]() Шаг 7 | Столешницу обтягивают кружевной тканью, которую фиксируют на прищепки. |
![]() Шаг 8 | Столешницу окрашивают контрастной краской из баллончика сквозь кружево, которое оставляют на поверхности столешницы до полного высыхания краски. |
![]() Шаг 9 | После удаления кружева, столешницу покрывают прозрачным лаком в несколько слоев. |
Видео — Покрытие маслом березовой фанеры
mebel-expert.info