12 методов изготовления изделий из пластика и примеры их использования [Часть 1]
Производство пластмасс необходимо для большинства отраслей промышленности. От полистироловой упаковки для пищевых продуктов до промышленных компонентов, изготовленных из полиэфирэфиркетона инженерного класса, производство пластмасс вносит огромный вклад в жизнь, какой мы ее знаем. Без возможности изготовления пластмассовых изделий нам пришлось бы разрабатывать принципиально новые системы производства.
Однако производство пластмасс включает в себя множество различных методов. Литье под давлением, экструзия пластика и 3D-печать FDM — все это методы изготовления пластмасс, и кроме них существует множество других. Эти различные методы изготовления подходят для разных пластиковых деталей, и выбор между ними не всегда прост. Бюджет, дизайн детали и материал — вот лишь некоторые из факторов, которые влияют на выбор метода изготовления пластмасс.
В этой первой части данной статьи мы рассмотрим 6 различных методов изготовления пластмасс, раскроем их основные процессы и то, почему они эффективны.
1. Литье под давлением
Литье под давлением является наиболее распространенным процессом изготовления пластмасс. Данный метода подходит для обработки термопластичных и термореактивных полимеров.
Этот метод быстрого изготовления пластмасс заключается в нагревании пластиковых гранул до расплавления, затем расплавленный пластик заливается в металлическую форму с помощью возвратно-поступательного шнека. Расплавленный материал остывает, затвердевает и принимает форму полости формы. Затем твердая деталь извлекается из формы.
Литье под давлением подходит для огромного разнообразия материалов и деталей. Детали должны иметь тонкие и ровные стенки, но в остальном могут иметь различные формы и размеры.
Примеры литья под давлением: одноразовые подносы для еды, приборные панели автомобилей, детали LEGO.
2. Выдувное формование
Выдувное формование — это процесс литья пластмасс, который используется реже, чем литье под давлением. Он имеет три разновидности: экструзионно-выдувное формование, выдувное формование под давлением и выдувное формование с растяжением.
Этот процесс изготовления пластмасс работает с использованием пресс-формы и расплавленной термопластичной трубки, называемой заготовкой (вместо полностью расплавленных гранул). Сжатый воздух поступает в заготовку, заставляя пластик расширяться и соприкасаться с внутренними стенками формы, в конечном итоге принимая вид полости формы.
Выдувное формование подходит для полых пластиковых деталей, таких как пластиковые бутылки для воды, с наиболее распространенным материалом HDPE.
Примеры выдувных деталей: бутылки, бочки, топливные баки.
3. Ротационное формование (центробежное формование )
Ротационное формование — это еще один процесс литья пластмасс, в котором для формирования пластмассовых деталей используются высокие температуры и низкое давление. Он осуществляется путем вращения формы для перемещения пластикового материала внутри нее.
В процессе ротационного формования порошкообразный пластик помещается в форму, которая нагревается и вращается вокруг двух (или более) осей. Благодаря этому вращению расплавленный пластик покрывает всю внутреннюю поверхность формы и принимает форму полости.
Преимущества ротационного формования включают более простую оснастку, постоянную толщину стенок и прочные внешние углы. Однако процесс может быть медленным, поскольку перед извлечением детали вся форма должна остыть.
Примеры ротационного формования: контейнеры, емкости для хранения, игрушки.
4. Вакуумное литье
Вакуумное литье — это процесс изготовления пластмассы, обычно применяемый для изготовления небольших партий разноцветных прототипов. Для изготовления уретановых пластиковых деталей используются силиконовые формы.
Во время этого процесса оператор заливает уретановую смолу в силиконовую форму; затем с помощью вакуума удаляются воздушные карманы и пузырьки, в результате чего получается исключительно гладкая готовая деталь. Затем уретановые детали полимеризуются в печи.
Вакуумное литье — популярный процесс изготовления пластика для частично прозрачных деталей, таких как опытный экземпляр.
Примеры деталей: корпуса и крышки для электроники, различные прототипы и опытные образцы.
5. Обработка пластмасс
Обработка пластмасс — это очень популярный процесс изготовления изделий из пластика. Он включает в себя фрезерование с ЧПУ, токарную обработку с ЧПУ и другие смежные процессы.
Хотя разные станки работают по-разному, обработка пластмасс обычно подразумевает вырезание участков из пластмассовой заготовки с помощью ручных или управляемых компьютером режущих инструментов.
Обработка пластика также полезна для совмещения деталей, изготовленными с использованием других методов, таких как экструзия.
Примеры обработанных деталей: различные промышленные детали, оснастка и приспособления, автомобильное освещение.
6. Моделирование методом послойного наплавления
Моделирование методом послойного наплавления (FDM) — это наиболее распространенный процесс 3D-печати для изготовления изделий из пластика. Он работает с обычными термопластами, такими как ABS и PLA, а также с такими современными материалами, как PEEK.
FDM работает путем нагрева экструдированной термопластичной нити, а затем выкладывания ее в точные формы из движущегося сопла (прикрепленного к печатающей головке) в соответствии с компьютерными инструкциями. 2D-фрагменты детали печатаются слой за слоем, пока не будет создан полный 3D-объект.
В небольших количествах FDM является очень быстрым и экономически эффективным и может производить широкий спектр форм, включая формы со сложной внутренней геометрией. Однако он не дает особо прочных деталей.
Примеры деталей FDM: различные прототипы, запасные части, композитные промышленные детали.
Технологический процесс изготовления пластиковых изделий – Технология изготовления и производства пластмассовых изделий
В промышленности, как правило, используются следующие технологические методы формообразования изделий из пластмасс: экструзия, прессование, литье под давлением, спекание, механическая обработка, сварка.
При переработке в изделия термопласты подвергают воздействию теплоты, механического давления, кислорода воздуха и света. Чем выше температура, тем материал пластичнее и тем легче проходит процесс переработки. Однако под влиянием высоких температур и названных выше факторов в пластмассах происходят разрыв химических связей, окисление, образование новых нежелательных структур, перемещение отдельных участков макромолекул и их самих относительно друг друга, ориентация макромолекул в различных направлениях.
Основной задачей при переработке пластмасс является замедление отрицательных процессов и создание необходимой структуры материала. Самыми простыми приемами для достижения этой цели являются регулирование температуры, давления, скорости нагрева и охлаждения материала. Кроме того, используют стабилизаторы, увеличивающие стойкость материала против старения, пластификаторы, понижающие вязкость материала и повышающие гибкость молекулярных цепей, а также различные наполнители, которые вводят в материал при переработке.
Особенность переработки реактопластов в изделия состоит в сочетании формования с отверждением, т. е. с химическими реакциями образования сшитой структуры макромолекул. Неполное отверждение ухудшает свойства материала. Достижение необходимой полноты отверждения (даже в присутствии катализаторов и при повышенных температурах) требует значительного времени, что увеличивает трудоемкость изготовления детали. Окончательно отверждение материала может происходить вне формующей оснастки, так как изделие приобретает устойчивую форму до завершения этого процесса.
При переработке композиционных материалов большое значение имеет адгезия (сцепление) связующего вещества с наполнителем. Величина адгезии может быть повышена путем очистки поверхности наполнителя и сообщения ей химической активности. При плохой адгезии связующего вещества с наполнителем в материале появляются микропоры, которые значительно снижают его прочность. При переработке термопластов происходит ориентация их макромолекул, причем прочность материала в направлении ориентации возрастает, а в поперечном направлении — уменьшается. При получении пленок и тонкостенных изделий это явление играет положительную роль, а в остальных случаях — отрицательную (вызывает структурную неоднородность и служит причиной возникновения остаточных напряжений). Различия по сечению изделия в скоростях охлаждения, степени кристаллизации, полноте релаксационных процессов (для термопластов) и степени отверждения (для реактопластов) приводят также к структурной неоднородности и появлению дополнительных остаточных напряжений в изделиях. Для снижения остаточных напряжений применяют термическую обработку изделий, формирование структуры при переработке и другие технологические приемы.
Технологический процесс изготовления пластмассовых изделий
Таблетирование. При переработке пластических масс компрессионным прессованием большое значение приобретают точная дозировка пресс-материала, загружаемого в пресс-форму, уменьшение потерь на грат, удобство загрузки пресс-формы и т.д. С этой точки зрения большие преимущества дает таблетирование материала, заключающееся в его механическом спрессовывании в твердые таблетки самой разнообразной формы.
Таблетирование порошкообразных материалов дает следующие преимущества:
- Сокращается объем необходимого материала, соответственно и размеры загрузочных камер пресс-форм;
- Исключается процесс взвешивания материала перед загрузкой в пресс-форму, т.к. таблетки обладают определенным весом;
- Ускоряется загрузка пресс-формы;
- Благодаря уменьшению включения воздуха ускоряется отверждение изделий и сокращается цикл прессования;
- Улучшаются условия предварительного подогрева, так как прогрев таблеток осуществляется при более высокой температуре;
Обычно таблетки имеют форму цилиндров различной высоты, но в отдельных случаях им можно придавать форму, близкую к форме готового изделия.
Не все материалы в одинаковой степени поддаются таблетированию. Лучшие результаты получаются при таблетировании гранулированного пресс-материала, имеющего одинаковую величину зерен, обеспечивающую требуемые объем и вес с минимальным включением воздуха.
Таблетки из порошкообразного материала имеют меньшую плотность.
Таблетирование может быть холодным ( необогреваемых пресс-формах) и горячим ( способствует уменьшению содержания летучих в материале таблетки, повышению ее прочности и удельного веса).
Предварительный подогрев. Предварительный подогрев является одним из важнейших этапов общего процесса прессования пластических масс. Различают два вида подогрева: низкий и глубокий. Низкий подогрев применяется для всех видов порошкообразного и гранулированного пресс-материала. Низкий подогрев применяется для всех видов порошкообразного и гранулированного пресс-материала. Глубокому подогреву подвергаются таблетированные пресс-материалы.
Предварительный глубокий подогрев дает возможность равномерно прогреть таблетки по всей их толщине до температуры, равной температуре прессования. Вследствие этого таблетки, загружаемые в формующую полость компрессионной пресс-формы или тигель литьевой формы, при приложении давления пуансона сразу же раздавливается. Материал, таблетки, переходя в пластифицированное состояние, растекается по формующей полости и быстро отверждается.
Применением предварительного подогрева достигается:
- Сокращение времени выдержки изделия в пресс-форме на 50-60 %;
- Снижение удельных давлений прессования на 20-60 %;
- Повышение текучести материала на 25-60 %;
- Уменьшение износа пресс-формы.
Прессование и литье пластмасс. Технологический процесс прессования и литья пластмасс формируется из таких стадий: подготовка материала к прессованию, подготовка пресс-формы, собственно прессование и отделочные операции.
Подготовка материала включает в себя отвешивание или отмеривание дозы материала, необходимой для прессования, изготовление таблеток и предварительный подогрев. При изготовлении изделий на литьевых машинах дозирование материала, поступающего в цилиндр машины, производиться автоматически непосредственно перед инжекцией.
В подготовку пресс-формы входят: очистка пресс-формы, установка арматуры (при ее наличии) в формующую полость и загрузка пресс-материалом.
Процесс компрессионного прессования заключается в непосредственном формовании изделия, в период которого могут быть сделаны подпрессовки, в раскрывании пресс-формы и удалении из нее отпрессованных изделий. При литьевом прессовании подпрессовки не производятся.
Нарушение режима прессования ведет к браку изделий даже при вполне исправной пресс-форме и доброкачественном материале.
Узнать цену на литье изделий из пластмасс вы можете сбросив заказ на электронную почту или позвонив по телефонам м/т 067-64-63-882, 095-408-41-39, т/ф 0462-65-15-44. Не стоит обременять себя мыслями о доставке готовых изделий, мы сделаем это, причем в любой город Украины (Львов, Черновцы, Запорожье и пр.).
www.ooo-stk.org
Технологические процессы производства полимерных материалов и пластмасс
Полимерами называются продукты химического соединения одинаковых молекул в виде многократно повторяющихся звеньев. Молекулы полимеров состоят из десятков и сотен тысяч атомов. К полимерам относятся: целлюлоза, каучуки, пластмассы, химические волокна, лаки, клеи, пленки, различные смолы и др.
По своему происхождению полимерные материалы делятся на природные и синтетические. К природным относятся: крахмал, канифоли, белки, натуральный каучук и др. Основную массу полимерных материалов, применяемых в современной промышленности, составляют синтетические полимеры. Они получаются с помощью реакций полимеризации (без образования побочных продуктов), например получение полиэтилена, и поликонденсации (с образованием побочных продуктов), например получение фенолформальдегидных смол.
Получение полимеров по реакции полимеризации осуществляется следующим образом. В реакцию полимеризации вступают органические вещества, содержащие в молекуле двойные связи. Под воздействием света, тепла, давления или в присутствии катализаторов молекулы веществ за счет раскрытия двойных связей соединяются друг с другом, образуя полимер.
При получении полимеров по реакции поликонденсации в реакцию вступают два мономерных продукта с образованием полимера и побочного продукта.
Среди полимерных материалов особое место принадлежит пластмассам. Это материал, в состав которого в качестве основного компонента входят высокомолекулярные синтетические смолы. Их получают путем химического синтеза простейших веществ, извлекаемых из столь доступного сырья, как уголь, известь, воздух, нефть.
Главное преимущество использования пластмасс по сравнению с другими материалами – это простота переработки их в изделии. Присущие им пластические свойства позволяют с помощью пресс-автоматов, автоматов для литья и др. изготавливать в час сотни деталей сложных конфигураций. При этом расход материалов минимальный (практически нет отходов), уменьшается количество станков и обслуживающего персонала, сокращается расход электроэнергии. Ввиду этого требуется значительно меньше капиталовложений в организацию производства изделий из пластмасс.
Методы переработки пластмасс и изготовления пластмассовых изделий зависят от отношения пластмасс к температуре. Выделяют термопластичные и термореактивные пластмассы.
К термореактивным относятся пластмассы, которые при нагревании до определенной температуры размягчаются, а затем переходят необратимо в неплавкое и нерастворимое состояние. Термореактивные пластмассы после отвердевания не могут быть переработаны повторно и поэтому называются необратимыми. Примером термореактивных пластмасс могут служить фенопласты. Изделия из термореактивной пластмассы получают методом прессования в пресс-формах. Последние имеют внутреннюю полость, соответствующую форме и размерам будущего изделия, и обычно состоят из двух разъемных частей – матрицы и пуансона. Матрица укрепляется на нижней плите пресса, пуансон – на подвижном ползуне пресса. Отмеренное количество пресс-порошка, нагретого до 90 – 120 °С, подается в матрицу, имеющую температуру, необходимую для прессования. Под воздействием тепла от нагретой матрицы полимер размягчается и приобретает необходимую пластичность. Под действием пуансона размягченный материал заполняет полость пресс-формы. При этом в термореактивной смоле проходят сложные химические превращения, приводящие к образованию неплавкого материала. Затвердевание изделия происходит в форме, находящейся под давлением. После определенной выдержки изделие извлекается из пресс-формы. Температура, давление и время прессования определяются свойствами прессуемых материалов. Кроме того, для переработки термореактивных пластмасс применяют и метод выдавливания, или экструзию. Этим методом получают изделия плоской (листы, пленки) или цилиндрической (стержни, трубы) формы.
Для получения изделий из термопластичной пластмассы применяют следующие способы: литье под давлением, экструзию (выдавливание) и формование из листа. Их применение обусловлено термопластичностью материала.
Наиболее применимый способ переработки термопластичных пластмасс – литье под давлением. Выполняется на специальных литьевых машинах. Порошкообразный или гранулированный полимер подается в обогреваемый цилиндр литьевой машины, где и расплавляется. При охлаждении термопластичный полимер застывает и приобретает вид детали.
Также при переработке пластмасс в изделия применяют формовку, штамповку, механическую обработку резанием, выдувание пустотелых изделий. Все способы характеризуются коротким технологическим циклом, небольшими затратами труда и легкостью автоматизации.
Синтетические волокна получают из синтетических высокомолекулярных смол. Большую группу составляют полиамидные волокна – капрон, нейлон. Они характеризуются высокой прочностью, эластичностью, стойкостью к действию щелочи, электроизоляционной стойкостью. К группе полиэфирных волокон относится лавсан. Он используется для производства тканей, трикотажных изделий, электроизоляционных материалов. Отличается высокой механической прочностью.
Технологический процесс получения химических волокон включает следующие стадии:
1) приготовление прядильной массы;
2) формование волокна;
Отделка.
Каучук – характерный представитель высокомолекулярных (полимерных) соединений. Он является основной составной частью резины, бывает растительного происхождения (натуральный) и синтетический. Наиболее широкое применение в промышленности получил синтетический каучук. Его химический состав и строение, а также физические свойства могут быть весьма разнообразны и сильно отличаться от свойств натурального каучука, в чем и заключается преимущество синтетических каучуков.
Основным сырьем для производства синтетических каучуков являются попутные газы нефтепереработки, этиловый спирт и ацетилен. Основные методы получения – полимеризация и поликонденсация. При переработке каучуки превращают в резину. Она характеризуется высокой эластичностью, сопротивлением к истиранию, изгибам, обладает газо- и водонепроницаемостью, высокими электроизоляционными свойствами, стойкостью к агрессивным средам.
Резину получают добавлением к каучуку ряда компонентов (ингредиентов). Затем эту смесь подвергают вулканизации. Вулканизация заключается в образовании мостиков между линейными молекулами каучука и получении трехмерной пространственной молекулярной структуры. Такая структура приводит к повышению термической стойкости и прочности материала, к уменьшению его растворимости и увеличению химической стойкости. Наиболее распространенным вулканизатором является сера, она же определяет и твердость резины. Также вводятся различные наполнители как для улучшения свойств (сажа, цинковые белила, каолин, противостарители), так и для удешевления (мел, тальк).
Резиновые изделия изготавливают: методом шприцевания, штамповкой, литьем под давлением, окунанием моделей в латекс и др. Разделяют резиновые изделия по назначению и условиям эксплуатации.
В химической промышленности наибольшие расходы приходятся на сырье и составляют в среднем 60 – 70 % себестоимости, а на топливо и энергию – около 10 %. Амортизационные отчисления составляют 3 – 4 %, заработная плата основных производственных рабочих колеблется от 3 до 20 % себестоимости продукции и зависит от типа производства.
megaobuchalka.ru
Классификация пластмасс
В зависимости от состава:
- Листовые термопластмассы – винипласт, органическое стекло. Они состоят из смолы, стабилизатора и пластификатора небольшого объема.
- Слоистые пластики – гетинакс, стеклотекстолит, текстолит – пластмасса, в состав которой входят наполнители бумаги или ткани.
- Волокниты – стекловолокна, асбестовые волокна, хлопчатобумажные волокна. Наполнители в этой пластмассе волокнистые.
- Литьевые массы – пластики из смолы, являющейся единственным компонентом в массе.
- Пресс-порошки – пластмасса с порошкообразными наполнителями.
По области применения:
- Теплоизоляционные – применяются в строительстве (пенопласт, поропласт и другие. Это газонаполненная пластмасса).
- Химически стойкие – применяются в промышленности (полиэтилен, винипласт, полипропилен, фторопласт).
- Конструкционные (стеклотекстолит, текстолит и другие).
- Пресс-порошки – пластмасса общего назначения.
В зависимости от связующего материала:
- Эпоксипласты (для связки используются эпоксидные смолы).
- Фенопласты (связующее вещество – фенолформальдегдные смолы).
- Аминопласты (меламинофармальдегидные и мочевиноформальдегидные смолы используются как связующее вещество).
По тому, как связующее вещество реагирует на повышение температуры, пластмассы бывают:
- термореактивными – при нагреве становятся мягкими и плавятся, но после проведения некой химической реакциипластмасса твердеет и становится нерастворимой и неплавкой. Ее нельзя будет использовать повторно, переплавка бесполезна. Такая пластмасса годна как наполнитель при создании пресс-порошков;
- термопластичными – такие пластмассы легко плавятся при нагревании и твердеют при охлаждении. Этот материал можно переплавить и изготовить из него новое изделие, однако его качество будет несколько ниже.
Процесс производства изделий из пластмассы и его особенности
Главная Статьи Особенности процесса производства изделий из плас class=»aligncenter» width=»600″ height=»450″[/img] Изделия из пластмассы пользуются широкой популярностью в быту, сельском хозяйстве, а также в большинстве отраслей промышленности. Для их производства применяется литье под давлением, а сырьем служат полипропилен, полистирол, полиэтилен (низкого и высокого давления) и др. Как правило эти материалы имеют вид гранул, которые в процессе производства превращаются в требуемые пластмассовые изделия.
Если изготавливаются предметы, использование которых не требует особой чистоты, либо которые будут служить дополнительными частями различных устройств, то для них как правило применяется вторичное сырье. В изготовлении изделий для пищевой промышленности используют пищевой полистирол, либо полиэтилен с высокими показателями чистоты.
Заводы по производству пластмассовых изделий оснащены специализированным оборудованием. Процесс литья происходит посредством термопласт автоматов, где расплавленная пластмасса перетекает в форму под давлением. Далее она остывает и затвердевает. Продолжительность этих процессов определяется технологическими особенностями. Следующий этап – это обработка (покраска, ультразвуковая сварка и т.д.)
Виды пресс-форм
Изготовление пластмассовых изделий происходит в пресс-формах, которые представляют собой две стальные плиты с пустотами внутри, соответствующими необходимой форме детали. Они также содержат литниковый канал, по которому осуществляется заполнение горячим сырьем. Сами плиты соединяются и фиксируются с помощью зажимов термопласт автомата. После остывания получается изделие в готовом виде.
Возможно два варианта размещения пресс-форм в термопласт автомате:
- Горизонтальное;
- Вертикальное.
Последний вариант используется в процессе изготовления изделий с закладными деталями.
Наиболее простой и распространенный тип пресс-формы – двухплитная конструкция.
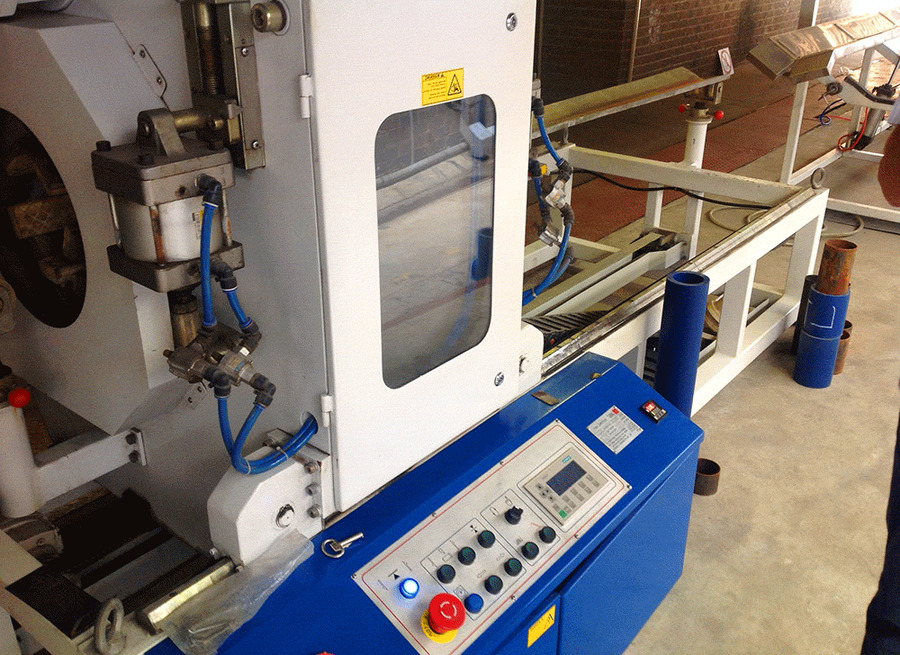
Процесс разработки и изготовления пресс-формы достаточно трудоемкий и длительный. От точности соблюдения всех параметров и чистоты обработки будет зависеть качество изделий, изготавливаемых впоследствии. Изготовление пресс-форм происходит с использованием обрабатывающих центров или станков ЧПУ, которые точно и быстро выполняют сверлильные и фрезерные операции.
Большинство предприятий, занимающихся производством пресс-форм, имеют в распоряжении целый ряд станков подобного типа. Практически все операции на них осуществляются без участия человека. В обязанности оператора входит контроль наличия заготовок и соблюдения технологического процесса в целом. На таких предприятиях часто практикуется изготовление пресс-форм под заказ.
www.vladneoplast.ru
Экструзия
Экструзионное формование применяют для изготовления из термопластов прутков, труб, шлангов, плит, пленок, фасонных профилей (поручней, плинтусов и т. д.). Процесс осуществляется на шнековых прессах непрерывного действия (экструдерах). Литьевая масса подается через загрузочный бункер в обогреваемый цилиндр шнека, подхватывается витками шнека (в свою очередь подогреваемого) и перемещается вдоль цилиндра, подвергаясь перемешиванию и уплотнению. Уплотнение массы достигается уменьшением шага или высоты витков шнека. На выходном конце цилиндра устанавливают фильеру с отверстием, соответствующим форме поперечного сечения изделия. Отформованное изделие, выходящее непрерывным жгутом из фильеры, охлаждается. После затвердевания его режут на куски необходимой длины.
В последнее время для подогрева литьевой массы используют тепло, возникающее в результате трения массы о стенки цилиндра и витки шнека («адиабатическое экструдирование»). При этом методе упрощается конструкция пресса и повышается экономичность процесса.
Метод экструзии широко применяют для нанесения изолирующих оболочек на проводники, кабели и т. д. Проводники, подлежащие покрытию, подаются из бунта через центральное отверстие в шнеке и в фильере обволакиваются литьевой массой.
Для изготовления пленок на выходном конце пресса устанавливают угловую головку. Заготовка выходит из фильеры в виде тонкостенной трубы, поворачивается под углом 90°, раздувается сжатым воздухом до получения стенок необходимой толщины и поступает в клиновидный зазор между двумя бесконечными лентами, где сплющивается. Образующаяся двойная лента подается вытяжными валками на разрезание.
Из труб, получаемых экструзией, изготовляют (методом раздува в формах) пустотелые изделия (флаконы, бутылки, фляги и пр.). Днище изделий заваривают.
Литье пластиковых изделий – особенности технологии
Сегодня в мире более двух третей штучных и серийных изделий изготавливают из различных пластмасс. Вес деталей может быть от десятых долей грамма до нескольких тонн. Ассортимент еще более обширный – от элементов, используемых в микропроцессорной технике, до монолитных конструкций и частей сооружений.
Литье пластиков под давлением является наиболее распространенной и самой эффективной технологией, которая широко применяется в наше время.
Описание технологии и суть литья под давлением
Литье пластиковых изделий под давлением – технология, позволяющая добиться высокой точности получаемых элементов вне зависимости от сложности конфигурации и других конструктивных параметров.
Технологический процесс представляет собой отдельный вид переработки исходного сырья, которое расплавляется до необходимой консистенции и впрыскивается под определенным давлением в специальную пресс-форму, где затем происходит охлаждение состава.
Как происходит сам процесс? Если применить условную схему этапов технологии, то они выглядят примерно так:
- подготовительная стадия. На этом этапе разрабатывается рецептура будущего состава, рассчитываются пропорции материалов, которые будут составлять исходное сырье. В зависимости от свойств, которыми должно будет обладать конечное вещество, состав и массовые доли компонентов будут различаться. На этой стадии происходит добавление красителей, сушка и смешивание всех ингредиентов будущего сырья;
- наладка оборудования.
Специальные автоматы для литья пластика настраиваются операторами, в них вводятся программы литья и происходит закрепление пресс-форм;
- этап загрузки. В это время происходит загрузка в бункеры заранее подготовленного сырья в необходимом объеме для осуществления литья;
- процесс отливки. Прежде, чем сырье сможет поступать в пресс-форму по специальным каналам (литниках), его необходимо нагреть до необходимой температуры. После этого, методом прямого впрыска под давлением масса попадает в форму и быстро ее заполняет;
- завершающий этап. После заполнения формы, пластик начинает остывать. Сначала температура массы снижается в области стенок, а затем и по всему объему. Происходит кристаллизация. Затем готовое изделие извлекается из автомата и проходит дальнейшую механическую обработку, где освобождается от остаточных элементов литья.
Приведенные стадии далеко не полностью описывают подробности, а лишь дают поверхностное представление о том, что такое литье пластиков.
Разновидности литья
На сегодняшний день существует несколько основных методов, в основе которых лежит технология литья под давлением. Каждый из способов отличается конструктивными особенностями оборудования, масштабами и некоторыми технологическими нюансами.
Наиболее распространенными методами с использованием давления являются:
- инжекционный способ. Суть процесса заключается в подаче определенной массы вещества под давлением в 100-200 МПа в специальную форму. Сам процесс занимает считанные секунды. Неоспоримым преимуществом такого способа является возможность получения готовых изделий различной конфигурации с любой толщиной стенок. Метод считается наиболее массовой для мелкосерийного литья и крупных промышленных объемов;
- интрузионный способ. Основное отличие от предыдущего варианта – более низкое давление вещества. Разогретая масса поступает на специальный червячный механизм, при помощи которого попадает в форму. Сам червяк останавливается при полном заполнении необходимого объема, а затем время от времени добавляет массу, компенсируя естественную усадку пластика.
Такой способ применяется для отливки изделий с толстыми стенками, благодаря постепенному заполнению формы. Конфигурация итоговых деталей или узлов должна быть максимально простой;
- инжекционно-газовый способ. Довольно новый метод, который еще полностью не изучен. Суть процесса состоит в том, что, как и при стандартом инжектировании под давлением, расплав попадает в форму. Только в данном случае она заполняется на 75-80%. Затем через специальные сопла внутрь попадает смесь газов (углекислый газ и азот). Подача может совершаться один раз или несколько, в зависимости от конкретного процесса и сложности получаемой детали. Благодаря воздействию смеси газов, разогретая пластическая масса более тщательно заполняет все конструктивные углубления в пресс-форме. После этого, газ удаляется через специальные каналы, а на место образовавшихся пустот впрыскивается дополнительная доза вещества. Преимуществами этого метода является снижение брака и существенных дефектов почти на 30%. Из недостатков стоит отметить очень сложное и дорогостоящее оборудование, точные расчеты всех процессов и тщательный контроль над всей процедурой;
- комбинированный способ.
Его еще называют методом многокомпонентного литья. Несмотря на сложность и дороговизну, это единственный метод, при помощи которого можно получить детали с разделением по цветовой гамме или конструкции, изготовленные из различных полимеров – сердцевина детали будет из одного материала, а оболочка (периферийная часть) из другого.
Существуют и другие способы отливки пластиков при помощи давления, которые считают гибридными вариантами, полученные благодаря совмещению основных технологий.
Сегодня процессы литья могут быть полностью автоматизированы, но нередко встречаются линии с дополнительным использованием ручного труда – добавление в бункеры сырья, контроль над технологическим процессом отливки, извлечение готовых деталей из форм и их последующая обработка. Как правило, все крупные компании, выпускающие несколько однотипных деталей большими тиражами, имеют полностью автоматизированные линии производства с минимальным вмешательством человека.
Что использовалось до пластика?
Было и есть много других предметов, которые можно использовать вместо пластика. До изобретения пластика люди использовали дерево, металл, стекло, керамику и кожу. Также использовалась смола с деревьев. Резина также обычно использовалась вместо пластмассы.
Заключение
Хотя мы признаем, что изобретение пластика произвело революцию во многих отраслях промышленности, оно также поразило нашу планету. Существует много альтернатив пластику, которые можно использовать в нашей повседневной жизни.
Чтобы распространить важность переработки и избавления наших полигонов и океанов от пластика, Пластиковые коллекторы сделать все возможное, чтобы повысить важность утилизации, а также компенсировать их усилия. Это растущий коллектив энергичных и трудолюбивых людей по всему миру. Plastic Collectors стремится создать мир, свободный от пластика, мотивируя людей перерабатывать пластик и выплачивать им вознаграждение. Нажмите знать, как вы можете присоединиться к делу.
Эти 4 технологии произведут революцию в производстве пластмасс в США
Отрасль производства пластмасс находится на пороге радикальных преобразований, поскольку несколько ключевых технологий обещают революционизировать то, как и где производятся и используются пластмассы.
Планируется, что эти достижения будут стимулировать рост индустрии пластмасс в течение следующих нескольких лет.
Нанотехнологии
Нанотехнологии — горячая тема в области технологий, производства и медицины. Используя обычные смолы, технология основана на производстве чрезвычайно тонких нитей материала толщиной от одного до 100 нанометров.
Сто нанометров — это толщина обычного листа бумаги.
Нанотехнология уже используется для усиления существующих пластиков, но пока не как самостоятельный материал.
Будущие области применения включают микроскопические медицинские имплантаты и мониторы, устойчивые к царапинам краски, электропроводящие нанотрубки, микросхемы памяти сверхвысокой емкости и «умные» строительные материалы.
Аддитивное производство
Широко известное как 3D-печать, аддитивное производство стало широко распространенным методом быстрого прототипирования.
Работая с цифровым файлом, 3D-принтер может создать физическую модель за время от нескольких часов до нескольких минут.
По сравнению со строительными формами, закупка которых требует больших затрат и которые трудно модифицировать, внесение изменений в цифровой файл занимает очень мало времени.
Это позволяет компаниям дорабатывать конструкцию, прежде чем переходить к инструментам, необходимым для чего-то вроде литья под давлением.
Сквозное отслеживание
Технология блокчейн идеально подходит для обеспечения качества сырья и готовой продукции на протяжении всего жизненного цикла продукта.
Он может точно сказать покупателю, из какой партии химикатов были изготовлены гранулы, отслеживать и составлять отчеты о процессе производства деталей и даже предоставлять данные в режиме реального времени, такие как время, стоимость, отходы и соответствие стандартам.
Биополимеры
В ответ на растущую озабоченность по поводу загрязнения окружающей среды и экологической устойчивости индустрия пластмасс начала уделять особое внимание органическим полимерам, также известным как биополимеры.
Обычный пластик изготавливается из синтетических соединений, что делает его очень прочным и легким, но за счет того, что он не поддается биологическому разложению.
Органические полимеры не имеют такой проблемы и легко разлагаются на органические соединения, которые могут повторно поглощаться окружающей средой, что делает их, по сути, возобновляемыми пластиками.
Health of the Industry
Эти достижения, наряду с прочными и универсальными свойствами пластика, способствовали огромным продажам. По данным, собранным MNI, компилятором и издателем промышленных данных, лежащих в основе IndustryNet, средний объем продаж в индустрии пластмасс превышает 757 миллиардов долларов.
И 2% компаний-производителей пластмасс сообщают о росте продаж по сравнению с 1% компаний-производителей в целом. Занятость также выросла по сравнению с прошлым годом на 2,5%.
Рост также был благоприятен для других отраслей обрабатывающей промышленности. Сталь, например, широко используется в процессе производства пластмасс.
Из-за этой взаимосвязи пластмассы оказывают заметное влияние на здоровье сталелитейной промышленности. Поскольку спрос на пластмассы, по прогнозам, не замедлится, сталь также сможет извлечь выгоду в течение следующих нескольких лет.
Географическое распределение
Географическое распределение производителей пластмасс относительно равномерное. Большинство, 37%, проживает на Среднем Западе, на Юге 28%, а затем почти поровну между Западом и Северо-Востоком, чуть более 17% каждый.
Информация взята с сайта IndustryNet.com. Вы можете прочитать статью полностью, нажав здесь.
Инновации в производстве пластмасс: двуокись углерода играет мускулами
Паоло Кирхпфенинг, глобальная коммерциализация Linde Technologies, Plastics, и Андреас Праллер, глобальный эксперт по технологиям, Plastics, Linde, обсуждают технологические и экологические инновации, возникающие в индустрии пластмасс.
Глобальное воздействие COVID-19 было беспрецедентным, поскольку отрасли во всем мире столкнулись с многочисленными проблемами. Блокировки для сдерживания передачи вируса, неопределенность на рынке, снижение инвестиционных и операционных ограничений привели к отсрочке проектов по всему миру и неизбежным последствиям для мировой экономики.
Expand
Linde
Инновации в производстве пластмасс: углекислый газ играет мускулами
Поскольку многие виды производственной деятельности во всем мире замедляются или даже останавливаются, спрос на пластмассовые изделия значительно пострадал: мировой рынок продемонстрировал спад на 1,2% в 2020 году[1], а Европа пережила падение на 5,1% до 55 миллионов человек. тонн[2]. В частности, существенно снизился спрос на пластмассы в автомобильной, строительной и строительной отраслях. В автомобильном секторе, который является одним из крупнейших покупателей пластика после упаковочной и строительной промышленности, его потребление упало на 18% (или на 9%).00000 тонн)[3] в Европе.
Возможность Несмотря на недавние проблемы, в индустрии пластмасс наблюдается восстановление, при этом годовой темп роста (CAGR) прогнозируется на уровне 3,4% в период с 2021 по 2028 год[4]. Ожидается, что возрождение потребления пластика в наиболее пострадавших отраслях — строительстве и автомобилестроении — поддержит этот рост. Стремление к снижению веса для повышения эффективности использования топлива и сокращения выбросов углерода приведет к использованию пластмасс в качестве заменителей металлов при производстве автомобильных компонентов.
Ожидается, что нормативные положения, касающиеся истощения природных ресурсов, возможности вторичной переработки традиционных материалов, таких как металл и дерево, и законодательство по повышению энергоэффективности, также будут стимулировать рост спроса на пластик в строительной отрасли для широкого спектра применений, таких как изоляция, трубы, кабели, полы, окна и резервуары для хранения. Пластмассы имеют на 85 % меньшую гравитацию по сравнению с металлами, а при использовании в автомобильной и строительной отраслях они обеспечивают снижение веса примерно на 80 % и снижение затрат на отдельные компоненты на 30–50 %.
Короче говоря, никогда не было более важного времени для оптимизации производительности, снижения энергопотребления и сокращения затрат.
Только от 80% до 90% рабочего времени машины для литья под давлением фактически приходится на продуктивную работу. Ценное производственное время теряется из-за запланированных простоев и технических сбоев, а также из-за процесса наладки. Хотя техническое обслуживание оборудования и замена пресс-формы могут помочь сократить время простоя, наибольшую выгоду можно получить за счет оптимизации времени цикла.
Время цикла играет важную роль в процессе литья под давлением, включая качество производимых деталей, но особенно его влияние на финансовый результат компании. Исключение секунд из времени цикла может привести к увеличению количества деталей, производимых за то же или меньшее время.
Передовые технологии для повышения производительности Промышленные газы играют незаменимую роль на ряде технологических этапов производства пластмасс, два из которых используются в качестве вспенивающих агентов для литья под давлением пены (FIM) и в качестве среды под давлением для литья под давлением газа (ГИМ).
До сих пор производители, которые полагались на процессы впрыскивания пены, должны были выбирать между физическими и химическими методами пенообразования. В химических процессах пенообразователь смешивается с пластиковым гранулятом. Простой в обращении, этот процесс может быть установлен на стандартных машинах для литья под давлением. Однако, в отличие от физических процессов вспенивания, химические методы обеспечивают только низкое давление вспенивания, что делает их непригодными для пластмасс с тонкими стенками. Химические пенообразователи также являются дорогостоящими, и образуются нежелательные побочные продукты, оставляющие остатки на форме. В методах физического вспенивания вспенивающий агент обычно вводят непосредственно в расплавленный полимер. Это требует дополнительных доработок термопластавтомата и специального шнека для обеспечения однородного смешения с расплавом полимера. Также требуется блок дозирования газа высокого давления для контролируемого впрыска газа. Это увеличивает затраты на установку и ограничивает гибкость.
Компания Linde объединилась с Kunststoff-Institut Lüdenscheid (KIMW) и ProTec Polymer Processing GmbH для разработки нового процесса, объединяющего лучшее из обоих миров. Технология литья пены под давлением PLASTINUM® сочетает в себе преимущества простого химического вспенивания с повышением эффективности физического вспенивания. Эта технология позволяет производить вспенивание на стандартных машинах для литья под давлением. Пластиковый гранулят пропитывают вспенивающим агентом диоксидом углерода (СО 2 ) под давлением перед подачей в машину для литья под давлением, при этом газ диффундирует в гранулят. СО 2 растворяется в расплаве при пластификации и образует микроячеистые пузырьки газа при сбросе давления при вдувании расплава в полость. Таким образом, можно добиться значительной экономии материалов и веса.
Кроме того, этот процесс повышает качество продукции за счет обеспечения высокой стабильности размеров и функциональности деталей, изготовленных методом литья под давлением из вспененного материала. PLASTINUM® Perfoamer от системного партнера ProTec Polymer Processing GmbH является центральным элементом технологии. Его можно легко перемещать с одной машины для литья под давлением на другую или даже обслуживать несколько машин одновременно, что делает производственный процесс более гибким.
Когда речь идет о методах производства с использованием технологии впрыска газа, традиционно она основывалась на газе азота под высоким давлением (N 2 ) для формирования полости или канала в формованной пластиковой детали. Тем не менее, Linde снова использует свойства CO 2 в своем ассортименте PLASTINUM® GIM C. Заменив газообразный N₂ жидким CO₂, процесс соответствует производительности теплоотвода и времени цикла литья под давлением воды, но не оставляет влаги на продуктах или форме, что исключает стадию сушки, связанную с циклом впрыска жидкости. Кроме того, СО 2 имеет более высокую плотность и удельную теплоемкость, чем азот, и обеспечивает значительное охлаждение при расширении, что означает сокращение времени цикла на целых 50%.
В технологиях PLASTINUM FIM и GIM компания Linde использует уникальные характеристики CO₂. CO 9 часто подвергается тщательному анализу, когда его улавливают как побочный продукт другого химического процесса, такого как синтез аммиака или производство оксида этилена, и используют в качестве естественной альтернативы более вредным газам.0101 2 может сыграть свою роль в эффективности использования ресурсов. Стремясь смягчить последствия изменения климата, Linde стремится свести к минимуму свой углеродный след за счет повторного использования CO₂ вместо создания новых потоков этого газа, и около 80% его запасов улавливается в результате других химических процессов.
Углекислый газ в действии: At Wirth Werkzeugbau GmbH Wirth Werkzeugbau GmbH является лидером в разработке и производстве крупных пластиковых инструментов и форм весом до 40 тонн. Компания имеет собственный технический центр, где разрабатывает и тестирует собственную технологию производства. В течение последнего десятилетия основное внимание уделялось разработке решений для физического вспенивания, которое сегодня составляет более 50% инструментов, производимых в Wirth.
До сих пор процесс на основе N 2 зарекомендовал себя, но оказался дорогим и менее экономичным для небольших и средних машин для литья под давлением. Управляющий директор Вернер Вирт задался целью найти мощную альтернативу, которая могла бы быть «более рентабельной, менее сложной и, прежде всего, более гибкой, потому что мы хотели предложить нашим клиентам перспективное решение для каждой машины на горизонте». «.
Вирт и его команда нашли то, что искали, в CO 9 компании Linde.0101 2 на основе технологии PLASTINUM® FIM. Теперь, когда несколько клиентов проводят испытания в Техническом центре Wirth компании, они могут предложить литьевым машинам проверенное и простое в реализации решение, которое не требует модификации существующих производственных линий — и при значительно меньших инвестиционных затратах.
С годовым доходом более 22 миллионов евро всего за 20 лет венгерская компания AQ Anton быстро превратилась в успешную компанию, специализирующуюся на инструментах, механообработке и производстве пластмасс. Являясь пионером в применении передовых технологий, таких как многокомпонентное литье под давлением, горячее тиснение, тампонная печать, ультразвуковая сварка и кондиционирование, GIM естественным образом вписался в широкий технологический портфель компании.
Компания Bosch, ключевой клиент, связалась с AQ Anton по поводу новой линии GIM для производства ручек для цепных пил своего мирового бренда, что побудило фирму расширить установленную базу из 21 машины GIM. Изучив все варианты литья под давлением в поисках решения, позволяющего повысить свою конкурентоспособность за счет сокращения продолжительности цикла, компания AQ Anton обратилась к своему надежному поставщику газа, компании Linde.
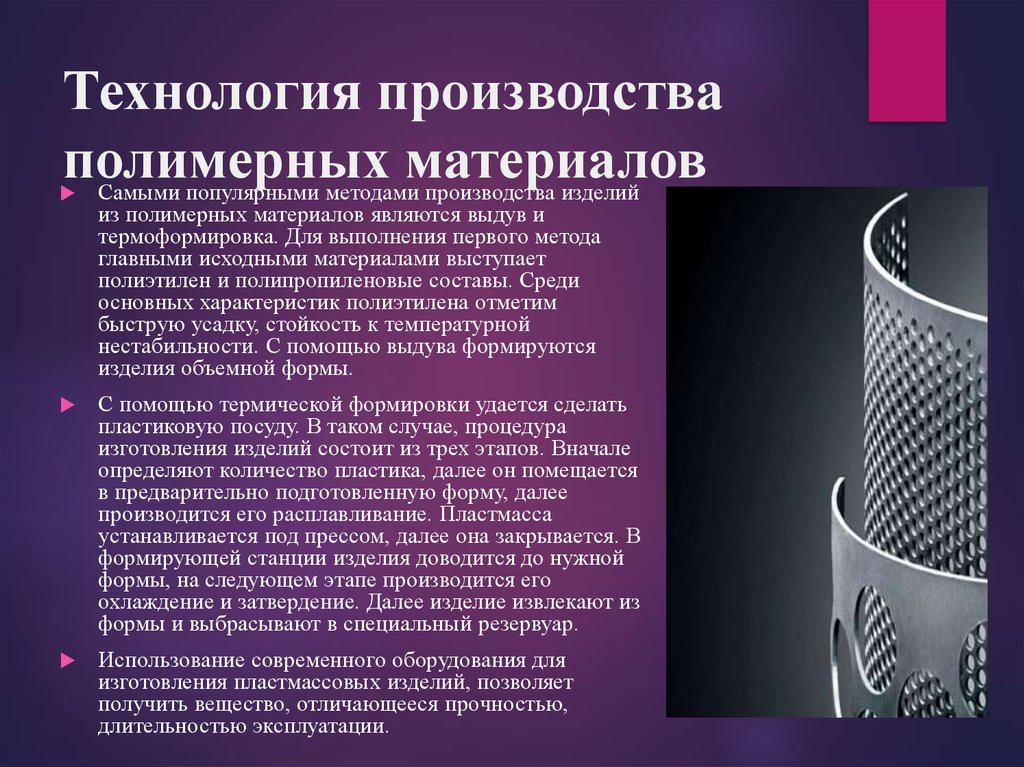
Тесты, проведенные AQ Anton для сравнения N 2 с CO 2 , продемонстрировали преимущества нового подхода, и впоследствии компания развернула PLASTINUM® GIM на основе CO 2 компании Linde на поддоне коллекторного цилиндра (MCP) для надежное газоснабжение. «Мы постоянно изучаем новые возможности для бизнеса, основанные на технологиях, и PLASTINUM® GIM от Linde с CO 2 быстро стал идеально подходящим для нашей культуры инноваций, что дало нам ценное конкурентное преимущество в этой области», — говорит Кристина Балог, менеджер по материалам в AQ Anton.
Будучи единственной компанией, предлагающей эту технологию, широкая клиентская база Linde указывает на то, что первые пользователи технологии GIM с кодом CO 2 уже получают значительные преимущества в стабильности процесса и качестве деталей.
1 июль 2021 г.; Объем рынка пластмасс, доля и анализ воздействия COVID ; Fortune Business Insights
2 10 июня 2021 г.