Наш собственный опыт переработки шин

Иногда полезно знать чужие ошибки , что бы не совершать свои или хотя бы минимизировать их. И глупо думать, что проблемы бывают у кого угодно, а у меня все будет хорошо. Это как знание истории, которое помогает избежать собственных проблем.
Собственный опыт производственной деятельности ( идея переработки покрышек в г. Находка и ее реализация) . Статья №1 Начнем с предистории. Намеренно не будем называть имена и названия компаний , так как это не профессионально. Наша компания существует с 2004-2005 года , а это на 2017 год 12 лет на рынке утилизации резины и продажи оборудования, много это или мало? Мы не были абсолютными пионерами в России, кто открыл шиноперерабатывающий цех механического дробления в крошку. До нас так же было две или три компании, которые делали резиновую плитку, было с десяток предприятий по всему СНГ, которые делали бесшевные покрытия по франшизе. Было несколько старых предприятий, работающих еще на советском оборудовании с довольно высокой производительностью. Так же были на тот момент ввезено несколько китацский простеньких линий, которые толком не работали и простаивали в качестве металлалома, так как в те времена еще не было опыта как победить высокое содержание текстиля в отечественных шинах, каких было большинство. Так же , были попытки у некторых торгующих организаций продавать Б,У европейское и пр-ва США дробильное оборудование . В те времена , больше всего было в регионах пиролизных линий, созданных для переработки шин термическим методом. Только в Приморском Крае на 2005 год их было поставлено 4 штуки в разные года и ни одно производство не работало тогда, а сейчас уже переплавлено . Свою первую линию мы начали искать еще в конце 2003 года в России, затем в Китае. В поднебесной , были неплохие предложения по цене простеньких линий с вальцами. Однако, мы такие линии видели стоящими и не работающими у нас в стране и к тому моменту выяснили что проблемма в высоком содержании текстиля Российских шин. Это было общее знание без подробностей и без полного понимания в чем именно причина . В КНР нам демонстрировали работу таких линий и при демонстрациях все казалось лаконично и легко, но мы уже знали что заграничные шины отличаются от наших тем, что в них только металл и резина. Очень хотелось купить себе такую линию, даже с имеющейся негативной информацией, ведь у нас была команда хороших технических специалистов с Находкинского судоремонтного завода, которые имели опыт и золотые руки. При всем желании, наши учредители приняли иное решение: купить в несколько раз более дорогое и по тем меркам «красивое» оборудование на юге китая . Его мы нашли, посетив международную выставку в Гуанчжоу 2004 году. В нагрузку скаем, что до этого мы посещали и другие выставки и видели предложение на другие линии, которые выдаваи как оборудование, способное работать с тканекордными колесами. Видели внешне привлекательные универсальные комплексы для дробления покрышек от фирм, специализирующихся на оборудовании по переработке пластика. Так же посещали производства по сборке отдельных измельчающих станков разного назначения, в т.ч и резины. В общем, купили наиболее понравившуюся в Гуанчжоу красивую, выглядящую наиболее технологично, производительность заявленная 5000 тонн шин в год. И решение по большей степени принимали учредители далеко не с техническим складом ума и уж тем более ни дня не работавшие даже на подобном оборудовании. Подкупило лиц, принимающих решение несколько факторов : А) Автоматизация процесса работы . Ручной и автоматический режим. Автоматика европейских производителей. Линия с большим количеством электроприводов, которыми в ручном режиме управлять затруднительно и более затратно по энергопотреблению. Электродвигателя запускаются не сразу, а каждый в свою очередь для оптимизации процесса, что бы , например не «завалило» сырьем одну из «узких» стадий, а более производительные измельчители не работали в холостом режиме зря тратя электроэнергию. В общем, для нас автоматизация оборудования тогда была одним из плюсов. Хотя без нее легко могут обойтись не сложные линии , но тем не менее очень эффективные. Автоматика необходима только для линий с множеством стадий дробления, сепарации, классификации и транспортировки материала. Необходимо смотреть на комплектацию линии. Б) Ножевые дробилки и шредеры линии были точной копией европейских, когда то ранее подсмотренных китайскими товарищами на одной из Европейских выставок. Мысли были такие: в Европпе плохие вещи не делают , а это оборудование точная копия. В) На заводе-изготовителе, нам сказали, что эти линии разрабатывались для рынка Индии, где много сельскохозяйственных тракторных шин с тканевым кордом. Действительно, линии были оснащены воздушными сепараторами текстиля. Таких две линии было продано до нас в 2 крупных города Индии. Комплектация даже будущему техническому директору пр-ва казалась продуманной и рабочей. Г) Производитель китайского оборудования по переработке покрышек был крупной компаний, внушал абсолютное доверие. Огромные новые сборочные цеха, современные залы для конференций и призентаций и т.д Это выглядело очень убедительно. Профессионализм инженеров не вызывал сомнений. Те, кто был в такой ситуации, возможно более других поймут. Д) В линии был предусмотрен мощная шредерная дробилка для дробления цельных шин до 1200 мм на чипсы. Автомобильную обувь необходимо было только положить на транспортер подачи, а на выходе линии необходим был рабочий который бы только принимал зашитые шинной гранулой мешки. Те кто видел работу шредера, когда в него попадает старая покрышка, знает какое это завораживающее зрелище, когда ее зажевывают валы и какой при этом стоит хруст. На тот момент мы знали случаи травмоопасность дисковых ножниц, которые участвуют в производстве чипс и шредер как альтернатива нам подходил больше. В этом мы тогда не ошиблись. Е) Так же , получаемая крошка была как и линия красивая. На тот момент мы не знали свойст рубленой гранулы . Не хватало опыта, что бы сравнить ее с раваной крошкой. Так как мы почему то считали чистоту от примесей главным фактором качества. Тут нам просто повезло с одной стороны, однако это было и недостатком, так как ножи грануляторов при работе со сталью тупились быстро и были дорогим расходником. Но об этом чуть позже остановимся подробнее. Накопив достаточно опыта, мы позже решили эту проблемму. Ж) В линии была предусмотренна очистка воздуха , выходящего из пневматических трасс и порционников, а так же воздушных сепараторов. Для нас собрали такую шиноперарабатывающую линию в оговоренные контактом сроки. Технический директор с опытом производственной деятельности 25 лет приехал на предварительную приемку в Гуанчжоу, смотрел работу с пристрастием. Все хорошо в различных режимах. Где то даже нашли с десяток не больших тракторных покрышек с нейоновым кордом и запустили в дробление. Подписан акт предварительной примеки, остаток стоимости переведен на счет производители и линия идет в 4 сорокафутовый контейнерах в прт Восточный (г. Находка) Линию привезли на территорию, выгрузили в заранее подготовленный бокс 15/45 метров с высотой потолка 5 метров. Был получен первый опыт разгрузки тяжелого оборудования и его расстановки. Затем, прилетели 2 китайских специалиста по шеф монтажу , с нашей стороны был нанят на работу технический переводчик и рабочие, которые должны ыли участвовать в монтаже и затем стать штатными сотрудниками цеха. В дальнейшем, мы сформировали три смены в сутки. Так же на время проведения монтажа был нанят опытный электрик, а технический директор и ген. директор на постоянную работу. С момента принятия решения о закупке оборудования, после того как определились с местом расположения цеха по переработке покрышек начали самостоятельно свозить утиль сырье. Я лично участвовал в разработке логистической схемы доставки на завод автомобильной обуви, а так же компактное размещение ее в кузове пятитоннгого старенького японского грузовика с ручкой манипулятором. Участвовал в строительстве цеха и монтаже оборудования. Затем , занимался сбытом резиновой крошки. Но не будем забегать в перед. За пол года до того, как мы привезли линию переработки покрышек в гранулу мы начали собирать утиль сырье, так как были опасения что наш не большой город и прилегающие территории не смогут загрузить мощную линию работой. Это в дальнейшм оказалось правдой. Сложно , не имея практического опыта расчитать оъемы собираемой резины на покрываемой территории. Запустили линию и тут же первые остановки из за забитых порционников, подающий смесь крошки 2-4 мм с примесями распушенного текстиля. Оказалось что у нас в Крае очень много покрышек отечественного производства диагональной конструкции корда , а так же смешанного типа. ¾ входного сырья были с текстилем. Такого никто не ожидал. Мы полагали, что если в линии есть работающие сепараторы, они будут справляться. Предварительно никто не резал покрышки основных типов и не смотрел на их состав в разрезе. Перед приходом оборудования мы разрезали две покрышки и видели порезанные шины на чипсы , но никто не занимался точным подсчетом текстильного волокана, который будет в виде ваты на выходе. Производительность линии на местном сырье оказалась более чем в 2 раза ниже чем на приемке в КНР. А ведь все экономические расчеты: рентабельность, окупаемость , себестоимость и тп строились на расчетной производительности. В дальнейшем, после того как ножи первого гранулятора подтупились об проволоку производительность стала еще ниже. Автоматизированный комплекс оказался не способным к данности по сырью. В дальнейшем, мы поняли что по всей России и СНГ похожая ситуация. Далее началось время траты денег , времени и нервов на то, что бы «довести линию до ума» . На это в общей сложности мы потратили первые 2 года и в последующем не отрываясь от работы делали полезные доработки и опыты. Через два года работы, мы согласились представлять интересы завода изготовителя на территории России и поставлять такое уже модернизированное с улучшениями оборудование. Мы сами делаи шеф монтаж и наладку проводили обучение персонала. В 2006 году поставили первое оборудование по выпуску резиновых плиточных покрытий, затем освоили «бесшевку» и напыление и так же возили такое оборудование в РФ. Имея опыт, производственные мощности и кадры, мы сперва для себя стали проектировать и собирать дополнительные станки, а затем обкатав их на собственном производстве предлагать их покупателям из других регионов. Все это время мы ездили по России и КНР , посещая тематические выставки и предприятия по утилизации резинового вторсырья. К настоящему времени накоплен огромный БЕСЦЕННЫЙ опыт собственных производств, зарубежных компаний и опыт наших друзей из различных уголков СНГ. Мы помогли многим не наступить на те же грабли что и мы в начале пути, однако часть начинающих переработчиков не прислушиваясь к советам до сих пор совершает ошибки и хорошо если финансовая прочность позволяет это проглатывать и идти дальше. Очень много аналитической информации по рециклингу резины в отечественных условия мы выкладываем на наших сайтах. Однако не все утруждают себя чтением. Многие люди разучились или обленились думать и читать статьи без картинок или текст в котором более 2-3 коротких предложений . Есть те кто читают наши статьи и даже дают положительные оценки, но информацию не усваивают или принимают выборочно, только то что соответствует собственным шаблонам. Часто, что бы голова заработала правильно необходимо совершить ошибки, которых можно избежать и сэкономить много времени и денег, начав зарабатывать быстро, не набивая болючих шишек. К сожалению многие становятся как завороженные, видя «красивую» технологичную 3 D модель линии и красивое описание с новомодными иностранными терминами, доверяют хорошо оформленным сайтам и рекламным роликам. Делая это точкой опоры в принятии решений , предприятие неизбежно проваливается в проблемы, а учредители разочаровываются начатому делу. Не все что красиво завернуто , соответствует внешней подачи- об этом знают многие, где то уже слышали, однако клюют на красивую обертку- золотинку. То оборудование что лучше и громче всего рекламируют, в продвижение чего вкладывают большие деньги , неизбежно стоит дороже прочих вариантов , но очень редко когда по качеству на самом деле лучше. В современном мире люди покупают не товар, а его подачу- хорошо запакованную обертку. Есть примеры, когда одно и то же оборудование, но упакованное в разные ТМ продают несколько поставщиков. Каждый называет себя изготовителем и украшает свой товар мнимыми преимуществами, завышая характеристики. По сути один и то же «металл» стоит по разному, в зависимости от затрат на его повреждение. Если у конкурентов линия имеет индекс 400, делается индекс 450 или 500, мол у нас лучше , новее и более производительней… Даже цвет покраски влияет на выбор, признает это лицо принимающее решение или нет… Данная статься показывает только часть ошибок, совершенных нами. Печально когда на те же грабли наступают и другие , идущие похожим путем. В этом мы убеждаемся почти каждый день. В своих статьях мы не призываем покупать именно наше оборудование и не выдаем себя как единственную организацию, которая знает как и что делать. Однако, мы готовы поделиться своим опытом с клиентами. Читайте наши статьи на этом и других наших сайтах.
Самохин И.Ю
tehno25.tiu.ru
Переработка шин превращается из угрозы экологии в высокодоходный бизнес
Экологическая проблема в России набирает обороты. Эксперты обращают внимание, что власти часто не видят решения проблемы: ну закрывают одну свалку, а мусор куда везти? Отфутболивают на другой полигон.
Необходимы комплексные подходы на уровне региональных властей, серьезные инвестиции в ЖКХ, строительство современных заводов и комплексов, оборудование. Муниципалитеты самостоятельно справиться с этим не в состоянии, но на государственном уровне — вполне. Тем более что тема хранения и переработки отходов имеет решение.
БОЛЕЕ МИЛЛИОНА ТОНН ПОКРЫШЕК В ГОД
…Город Обнинск Калужской области. Физико-энергетический институт имени А. И. Лейпунского широко известен ядерными реакторами для АЭС, космических спутников и подводных лодок (подробнее см. «Из досье «КП»). В последнее время обнинские ядерщики, которые входят в структуру «Росатома», активно развивают технологии по переработке отходов.
— У нас очень активный коллектив: 2,5 тысячи человек, из которых 240 кандидатов и 50 докторов наук. Да, какое-то количество инженеров и технологов в 1990-е ушли в бизнес, но научный костяк остался. Мне известно только два случая выезда за границу наших сотрудников. Но они вернулись и теперь замечательно у нас работают. Оказалось, что у нас трудиться интереснее и комфортнее. Тем более что институт у нас многопрофильный: если одна «лапка» — направление — увязнет, то другая ее вытащит, — не скрывает удовольствия генеральный директор ГНЦ РФ — ФЭИ доктор наук Андрей Говердовский.
Возьмем обычные автомобильные шины. На первый взгляд кажется: какие от них могут быть проблемы? Но отслужившая свой век резина — это бытовые отходы наивысшего класса опасности. На свалке колеса будут разлагаться больше 100 лет. Надумаете сжечь? В окружающую среду попадут сера, бензопирен, фуран, диоксины и ряд других канцерогенных соединений, которые создают угрозу и для окружающей среды, и для здоровья человека. Причем от загрязнения воздуха не спасает даже сжигание резины на специальных заводах — уж очень сложно уловить выделяемые вещества.
Добавим, что за год в России приходит в негодность более миллиона тонн покрышек. И масштаб бедствия становится очевидным.
Обнинские атомщики создали технологию, которая позволяет утилизировать резину без каких бы то ни было побочных влияний на окружающую среду. Более того, она экономически выгодна!
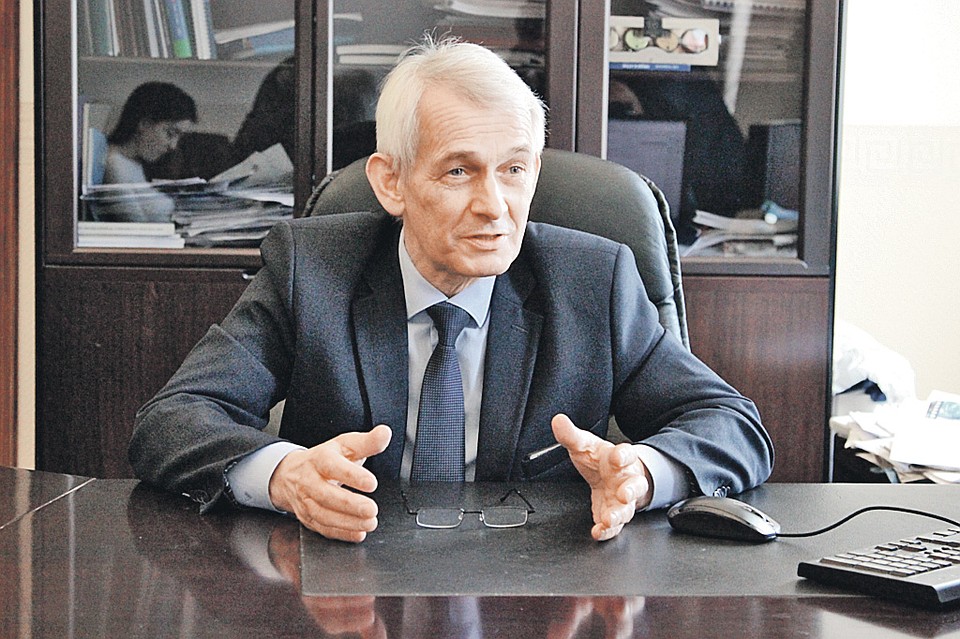
Андрей Говердовский считает, что в России научным работникам трудиться интереснее и комфортнее. Фото: Александр ЗЮЗЯЕВ
ГОРЮЧЕЕ ИЛИ ПРИРОДНЫЙ РАСТВОРИТЕЛЬ?
— Загружаем покрышки в емкость и заливаем жидким свинцом, — как можно проще старается объяснить технологию утилизации резины ведущий научный сотрудник ФЭИ им. А. И. Лейпунского Владимир Ульянов. — Жидкий металл — отличный теплоноситель, поэтому весь процесс переработки одной партии покрышек у нас занимает не более одного часа.
Технология пиролиза востребована во многих странах. В специальных герметичных емкостях при ограниченном доступе кислорода резина нагревается до 450 — 650 градусов, но не горит. Вредные соединения разлагаются, не загрязняя атмосферу. Ущерба экологии нет. Но если на Западе процесс утилизации покрышек занимает от 8 до 12 часов и отнимает массу энергии, то российским ученым удалось его существенно упростить, заменив газ на жидкий металл.
Опытная установка по переработке резины в своей простоте напоминает автомат Калашникова: два мощных герметичных бака, которые легко перевезти в кузове грузовика. Технология позволяет переработать до 1000 кг использованных покрышек в сутки. Одна установка может окупиться за год.
В процессе переработки ученые получили четыре основных продукта. Первый — металлокорд, который сдаем в металлолом. Второй — пиролизный газ, аналог природного газа. Его можно использовать для обогрева самой установки, в которой утилизируются шины. Третий продукт — технический углерод, сырье для производства черного пигмента красок. И наконец, четвертый, наиболее ценный — пиролизная жидкость, близкая по своему составу к синтетической тяжелой нефти или мазуту.
Но мазут мазуту рознь. Пиролиз в жидком металле преподнес российским ученым неожиданный подарок: ценное вещество — лимонен. Это отличный органический растворитель, который обычно производят из лимонов. Вещество безопасно для здоровья человека, поэтому широко применяется при производстве моющих веществ. А больше всего высокочистый лимонен востребован в парфюмерии. При переработке 1000 кг покрышек можно получить до 60 — 90 кг лимонена.
— Стоимость получаемого лимонена выше, чем стоимость покрышки, именно поэтому установки по утилизации резины окупаются чрезвычайно быстро, — сообщил Андрей Говердовский. — Сегодня в процессе обсуждения несколько десятков заявок от частного бизнеса на предоставление технологии переработки, два договора подписаны.
Полученную технологию пиролиза можно использовать и при утилизации других продуктов. От тины, которая образуется в очистных сооружениях, до отходов, появляющихся при производстве бумаги.
ДОВЕРЯЮТ «РОСАТОМУ»
Непростая ситуация с накоплением и переработкой твердых коммунальных отходов в России усугубляется сложностью работы с особо опасными веществами. Речь идет о ртути, отходах предприятий химической отрасли, нефтешламах, электролитах аккумулятора — десятки наименований отходов, которые могут нанести непоправимый вред окружающей среде. Эта сфера регулируется специальными нормативно-правовыми актами, а отходы необходимо перерабатывать на специализированных предприятиях. Поэтому Минприроды России выступило с инициативой о создании единой государственной системы, центральное место в которой должен занять федеральный оператор по обращению с отходами высших классов опасности.
С учетом успешного опыта выполнения государственной политики в области обращения с радиоактивными отходами, а также наличия современных технологий комплексного обращения с особо опасными отходами при развитой управленческой и производственной инфраструктуре Минприроды предложило закрепить полномочия по организации обращения с отходами I и II классов опасности за госкорпорацией «Росатом».
ИЗ ДОСЬЕ «КП»
Физико-энергетический институт имени А. И. Лейпунского Госкорпорации «Росатом» — один из ведущих российских научно-исследовательских центров в области ядерной энергетики.
С 1946 года институтом (в то время он назывался Лаборатория «В») разработано свыше 120 различных проектов, в том числе реакторы на тепловых и быстрых нейтронах для атомных электростанций, реакторы для подводных лодок (особая гордость — энергоустановка для лодки-истребителя «проекта 705», занесенной в Книгу рекордов Гиннесса за скоростные и маневренные качества, позволяющие уклоняться от торпед) и космического назначения (энергоустановки типа «Бук» и «Топаз» использовались в советских спутниках).
В последнее время сотрудники Физико-энергетического института имени А. И. Лейпунского активно развивают научно-исследовательские разработки в области экологии, материаловедения, энергетики, нефтегазовой промышленности, наноматериалов, медицины и других направлений. Например, налажен выпуск микроисточников с радиоактивным йодом-125 для брахитерапии рака. Ученые института совместно с медиками разработали препарат на основе иттрия-90 для лечения рака печени и сейчас проводят его доклинические испытания. Следующий этап — препарат на основе радия-223, который уже называют убийцей метастазов.
www.kp.ru
Не кошмар, а продукт. Как переработать тонны использованных шин и заработать деньги
Оставляя отжившее свое покрышки на шиномонтаже или складах спецорганизаций (предположим, что все действительно сдают их правильно, а не выносят на мусорку или куда-нибудь подальше в лес), мы и понятия не имеем, что будет с ними дальше. Оно и неудивительно: для автомобилиста судьба шины важна ровно до того момента, пока та без «булок» и не лысая. Что потом, нас, откровенно говоря, не очень-то заботит — ну кто ломает голову над перспективами мусора? Наверное, поедет же на свалку. Но благо в наше время можно переработать если не все, то очень многое. И покрышки не исключение. Им также можно подарить вторую жизнь (и речь сейчас совсем не про клумбы и лебедей возле подъездов). Смотрим, как тонны изношенных шин перерабатывают в Латвии.Завод Eco Baltia vide в Тукумсе (город на 17 тыс. жителей расположен в 70 километрах от Риги) существует всего несколько месяцев. Это структурное подразделение местного гиганта сбора, сортировки и переработки отходов, умеющего создавать деньги прямо из мусора. Для Латвии (как и для нас) переработка шин — это не такая уж и исхоженная тропа: тех, кто занимается этим профессионально, можно пересчитать по пальцам одной руки.
На территории нового мини-завода (к тому же мобильного: производство всегда может сняться с места и переехать на новую площадку, если это необходимо) уже лежит огромная куча шин, гора высотой в несколько метров — это улов за прошлую неделю, когда на площадке разгрузились шесть больших авто. Теперь весь этот резиновый ужас предстоит переработать и (в идеале) продать. Пока предприятие молодое, работа идет на имя и узнаваемость.
— То, что вы видите, действительно выглядит как какой-то кошмар. Но, к счастью, все шины можно переработать, и тогда мы уже получим продукт, имеющий свою цену, — рассказывает руководитель проекта Андрис Жимелис. — Гранулы (итоговый продукт) можно использовать по-разному, например в дорожном строительстве.
К слову, в Финляндии такая добавка к дорожному полотну успешно применяется повсеместно, даже на законодательном уровне закреплено, какой процент гранул должен быть использован. В Латвии тоже хотят внедрить такой подход, но пока все стопорится.Также из гранул получаются отличные безопасные покрытия для детских площадок (резиновая плитка). Ну и еще один вариант — из переработанных шин мы делаем «чипсы», которые на заводах выступают в качестве резинового топлива.
На Eco Baltia vide принимают практически все виды покрышек (пока вход закрыт только для шин погрузчиков). Бо́льшую часть сырья поставляют компании, у которых много транспорта. От «отработки» они избавляются относительно бесплатно: с учетом специфики работы предприятия изначально делают особые отчисления в пользу государства. Так что отдельно Eco Baltia vide платить уже не нужно. Если же такой платеж предусмотрен не был, то расчеты надо будет вести непосредственно с заводом.
Что касается рядовых латышей, то лысую резину они могут сдать либо бесплатно в специальных пунктах приема, либо ближе к дому, но уже за деньги — примерно €8 за четыре колеса.
Что же происходит с шинами на заводе? Сперва их сортируют: большие, маленькие, грязные — все распределяются по разным кучам. С шинами от грузовиков приходится повозиться: прежде чем отправить их на переработку, надо извлечь корд. Для этого есть специальная машина, которая оснащена «крюком-выдирателем».
Впрочем, и эти «внутренности» пойдут в дело: металл будет продан, причем за неплохие деньги.
Далее шины разрезают на несколько частей. Эта процедура повторяется раз за разом. Когда «лаптей» не останется, «стружку» передадут на дорогущий французский станок, который начнет разрывать резину на мелкие гранулы. Никакой тепловой или химической обработки не требуется.
В результате получатся гранулы различных размеров — для каждого вида будущей продукции нужны свои исходники.
— Мы делаем полуфабрикат, с которым производителям будет удобно работать. Сами запустить производство той же безопасной плитки не стремимся: зачем, если уже есть компании, которые крепко стоят на ногах и знают свое дело? Сейчас мы рассылаем «пробники» продукции по различным организациям. По большому счету, нам все равно, куда продавать, одной только Латвией себя не ограничиваем. Если наши пластиковые гранулы пользуются популярностью в Азии, то почему бы и резиновые не продавать по всему миру? — объясняет Андрис.
При переработке одной шины потери на металл и текстиль составляют всего 5%. Так что затея, считай, беспроигрышная. Если переводить шины в готовый продукт, то курс получается 4 к 1: из четырех покрышек от легкового автомобиля можно «наварить» один квадратный метр резинового покрытия для детской площадки.
Пока завод работает вполсилы — всего одна смена с четырьмя людьми на линии. Заработок сотрудников не раскрывают, но мы-то с вами знаем, что минимальная зарплата в Латвии — €430, а средняя — €1036 до уплаты налогов. Планы у Eco Baltia vide большие: работа в три смены (строительство ангара, который будет погашать шум, сделает это возможным) и семь тысяч тонн перерабатываемых шин в год. Это если дело пойдет. Ну а чего ему не пойти?
Благодарим за помощь в организации поездки дилера Jaguar Land Rover в Беларуси «Атлант-М Британия», а также партнеров проекта — «Технобанк» и Латвийское внешнеэкономическое представительство в Республике Беларусь.
Новые шины для новой зимы:
Библиотека Onliner: лучшие материалы и циклы статей
Auto.Onliner теперь в Telegram! Присоединяйтесь!
Быстрая связь с редакцией: читайте паблик-чат Onliner и пишите нам в Viber!
Перепечатка текста и фотографий Onliner без разрешения редакции запрещена. [email protected]
auto.onliner.by