Особенности технологии производства LVL — компания All-Fanera
LVL (Laminated Veneer Lumber) – один из наиболее перспективных строительных и отделочных материалов, сфера применения которого постоянно расширяется, соответственно растут и объёмы его производства. Технология производства LVL сходна с технологией производства фанеры. Для производства используют лущёный шпон хвойных и лиственных пород древесины толщиной 2.5-3.2 мм. Прессование осуществляется в прессах непрерывного действия, поэтому длина плиты может быть до 18 м. Ширина заготовок – от 80 до 1800 мм, а толщина — от 21 до 75мм. Этот материал применяется для несущих конструкций жилых, общественных и промышленных зданий, изготовления многоразовой опалубки, столярно — строительных изделий (окон, дверей, лестниц) и отделки интерьеров.
Исследования Американской Ассоциации деревообработчиков показывают, что для укладки 100 м2 пола с использованием обыкновенных балок из пиломатериалов необходимо срубить три дерева.
Технология получения LVL во многом схожа с технологией производства фанеры, но есть в ней и свои особенности. Начальная стадия производства – гидротермическая обработка фанкряжа в бассейнах с горячей (до + 500С) водой не имеет отличий, но операция лущения уже проходит несколько иначе.
Лущение, сушка и сортировка
Брёвна разделываются на чураки длинно до 2000 мм, которые подаются к лущильному станку. Современные лущильные станки оснащены лазерным центровочным устройством, которое позволяет снизить отходы лущения на 20-25%. Несколько лет назад были созданы бесцентровые лущильные станки. Их появление сопровождалось очень громкими заявлениями о перевороте в технологии производства лущёного шпона, но спустя некоторое время оказалось, что с точки зрения экономичности они не дают того результата, которого от них ожидали. Главное отличие от лущения фанерного шпона – толщина шпона для LVL, который составляет 3.
Далее полоса шпона режется на листы определённо длины. Шпон, полученный из заболони, имеет большую влажность, чем полученный из ядра. В соответствии с этим листы сортируются и укладываются на различные уровни конвейера проходной сушильной камеры. Обычно конвейер имеет 5-6 уровней. На выходе камеры – охлаждающая секция, оборудованная приборами для контроля влажности, прочностных характеристик и внешнего вида листов шпона. Листы, имеющие влажность выше допустимой, возвращают на повторную сушку. Для внешних слоёв плит конструкционного назначения отбираются листы шпона с наиболее высокими прочностными характеристиками. Для сортировки по этомк признаку используют ультразвуковые сканеры.
Формирование пакета
Особенность формирования пакета шпона для плит LVL состоит в том, что обычно все слои в нём продольные. Линии, формирующие эти пакеты, имеют различную конструкцию, но общим является то, отсортированные листы шпона определённой длины (цельные и прошедшие починку и ребросклеивание) сращиваются в «бесконечную» ленту. Перед началом сращивания листы шпона, как правило, снова проверяют на наличие дефектов и уровень влажности. Листы соединяются между собой чаще всего либо на ус, либо просто внахлест или встык. При соединении на ус заусовочная машина на переднее и задней (по ходу конвейера) кромке листа делает наклонный срез шириной 30 мм. После нанесения клея последующий лист накладывается на предыдущий с нахлёстом на ширину этого среза. Клей наносится в основном методом налива или распыления. Как только сформируется лента определённой длины, она укладывается на конвейер перед прессом, а следующая за ней кладётся на неё со смещением, так, чтобы её край отступал от предыдущей на определённое расстояние, и так до тех пор, пока не наберётся необходимое число слоёв. На задний край этого пакета, имеющий ступенчатую форму, последовательно накладываются листы следующего пакета.
Прессование
В производстве LVL применяются однопролётные и многопролётные прессы. Однопролётные прессы называют ещё прессами непрерывного действия. В этом случае заготовка непрерывно подаётся в пресс, а раскраивается готовая плита. Для многопролётных прессов заготовка кроится по размерам пресса перед прессованием. Обычно перед основным прессованием заготовка предварительно подпрессовывается.
Основные прессы часто используют микроволновые генераторы для быстрого и равномерного по всей толщине предварительного прогрева заготовки. Эти генераторы формируют вертикально стоячую волну, которая даёт наибольший эффект прогрева в средних слоях заготовки. Окончательный прогрев осуществляется нагретыми стальными листами пресса. Температура на входе в пресс составляет +1900С и постепенно снижается до +1500С на выходе.
Наибольшее значение давления – примерно 15 атм. Затем оно постепенно снижается до нуля на выходе из пресса.
По сравнению с другими композитными материалами на основе древесины скорость подачи в пресс непрерывного действия относительно низкая. Она составляет от 4.4 м/мин для 11 слоёв шпона до 1.5 м/мин для 25 слоёв.
Вот некоторые данные о времени прессования (непрерывный пресс фирмы Diffenbacher, общая длина 46 м).
Для 11 слоёв (33мм) – 16.6 секунд на 1 мм толщины плиты, т.е. время прессования составляет 9.1мин, суточный выход (22.8 часа) – 273 м3; годовой выход (350 дней) – 95671м3.
Для 25 слоёв (75 мм) – 24.9 секунд на 1мм толщины плиты, т.е. время прессования 31.1 мин; ежедневный выход -182 м3; годовой выход – 63720 м3.
Для 25 слоёв с применением микроволновой системы предварительного прогрева производительность пресса существенно увеличивается: ежедневны выход 258 м3 при времени прессования 21.
Заключительные операции
После прессования плиты проверяются на наличие непроклеенных участков. Затем обрезаются в боковые кромки. Обычно в отходы уходит до 50 мм с каждого края. Избежать этих потерь невозможно из-за волнистости шпона. Далее плиты корятся на детали необходимых размеров. Так же, как и фанера, LVL может быть отшлифован с обеих сторон. На предприятиях часто ставится оборудование для производства готовых строительных конструкций, стандартных или по чертежам заказчиков. Это могут быть коробчатые или ферменные конструкции, а также двутавровые балки и перекрытия различных форм. Заключительные операции — это пропитка готовых деталей различными защитными составами и покраска.
В последнее время производство LVL, активно развивается в Новой Зеландии, где сырьевой базой для них служат искусственно созданные плантации сосны Монтерей*, известно также под названием «сосна радиата» (radiate pine).
В России в 2003 г. запущен первый завод по производству плит LVL (г. Нягань, Ханты-Мансийский автономный округ). Сырьё здесь конечно не то, что в Новой Зеландии. Но благодаря возможности обработки тонкомерной низкокачественной древесины, сырьевые ресурсы предприятия можно считать неограниченными.
Сергей Афанасьев
Источник информации: журнал «Дерево.RU» № 4 июль-август 2003г.
*Общепринятое ботаническое название этой сосны – сосна замечательная (RADIATA PINE). Другие названия: insignis (ЮАР), Monterey pine (США)
Естественный ареал этой породы ограничен узко полоской побережья южной части Калифорнии (США), но её широко разводили в культурах в ЮАР и во многих других районах южного полушария. В лесах естественного распространения сосна замечательная обычно имеет высоту 15-18 м. В южном полушарии она растёт быстрее и к 25-30 годам достигает высоты 21-25 м, обычно при диаметре 0.
Технология изготовления фанеры. Самые актуальные статьи.
Сегодня фанеру производят из таких пород деревьев, как береза, лиственница, сосна, ель и ряд некоторых других. Если брать показатели прочности, структурную целостность, наибольшим спросом пользуется как раз береза. Из нее получается идеально гладкий шпон, имеющий различную толщину. По своим показателям среди лиственников также можно отметить липу и ольху, из которых также получается отличная фанера, цена которой немного дороже. У них отлично лущится древесина, материал обладает превосходной эластичностью и плотной равномерной структурой. Как противоположный пример, можно назвать такие породы, как бук, дуб и ясень, обладающие неравномерными по толщине годовыми слоями.
Кроме того, для производства фанеры активно используется ряд хвойников, таких как сосна и лиственница. Хотя здесь можно отметить и существенный минус этих деревьев – наличие большого количества смол, что затрудняет отбор подходящего сырья. И все же, поскольку наша тайга преимущественно состоит из хвойных деревьев, не использовать этот ресурс будет крайне нерационально. По факту хвойная влагостойкая фанера также пользуется устойчивым спросом.
Технология производства фанеры делится на несколько последовательно реализуемых этапов:
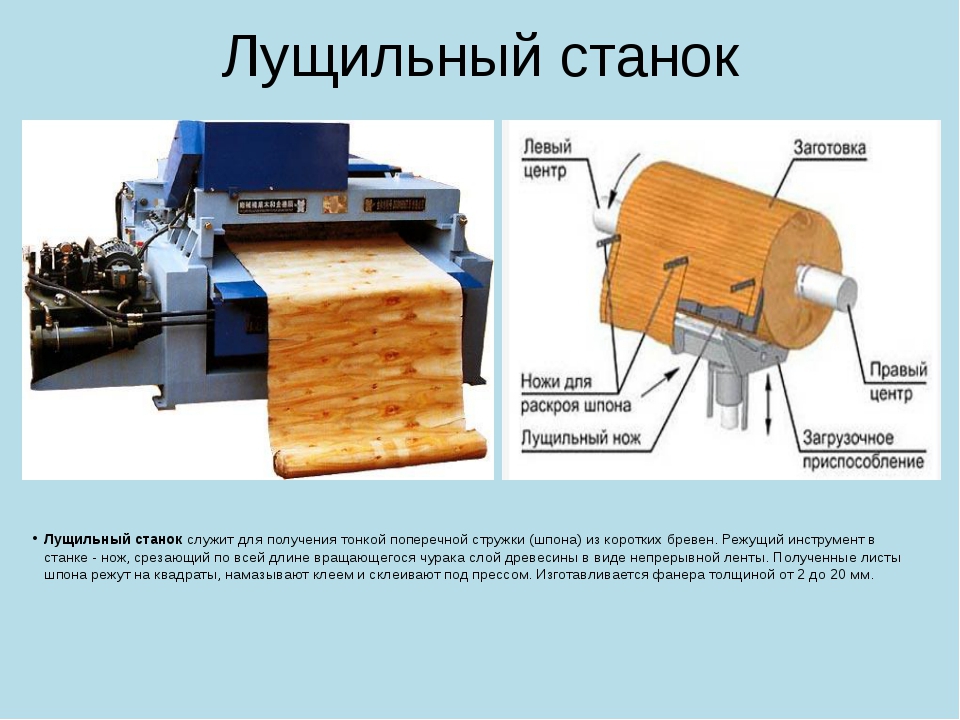
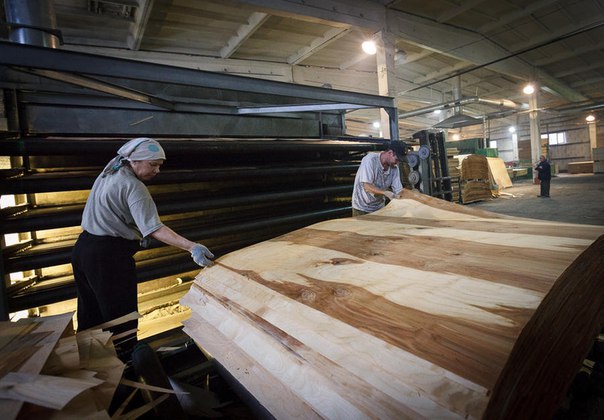
Если сравнивать фанеру с другим распространенными материалами – ДСП и МДФ, нужно отметить, что фанера имеет лучшие характеристики по таким параметрам, как прочность, экологичность и теплопроводность, небольшая себестоимость. Именно поэтому фанера является ведущим материалом, применяемым в строительной отрасли.
Как производят ламинированную фанеру
В связи с развитием монолитного строительства особое значение для качества возводимых конструкций приобретают опалубочные системы. В состав опалубки входят металлический каркас и ламинированная фанера. Качественная ламинированная фанера имеет гладкую, ровную поверхность и хорошо прокрашенные, защищенные от влаги торцы. Именно эти свойства позволяют использовать ее многократно.
Производство ламинированной фанеры – сложный многоступенчатый процесс, на каждом этапе которого важна точность соблюдения производственных методик. Рассмотрим процесс производства ламинированной фанеры на примере комбинатов группы «СВЕЗА», мирового лидера в производстве берёзовой фанеры.
Первые станки для переработки древесины в шпон, а далее – в фанеру, были запатентованы ещё в XVIII веке. Примечательно, что практически все их изобретатели так или иначе связаны с Россией. С момента изобретения сама технология переработки практически не изменилась. Модернизации подверглось управление станками, сейчас оно полностью автоматизировано
Начало: подготовка сырья
Процесс производства ламинированной берёзовой фанеры требует тщательного отбора и подготовки сырья. В первую очередь подбираются стволы нужного размера. Для производства стандартной для России фанеры (1220х2440 мм) перерабатываются стволы диаметром 20-40 см и длиной 5,2 м (в дальнейшем такие стволы можно распилить на чураки по 1,3 или 2,6 м, необходимые для производства продольного и поперечного шпона требуемого формата).
Основным этапом подготовки является проварка сырья. Она осуществляется в специальном бассейне (открытом или закрытом) в течение 24 часов. Летом температура в бассейне держится на уровне 35-40оС, а зимой – 40-45оС. Для повышения качества шпона, из которого впоследствии будет изготовлена фанера, важно, чтобы на этапе проварки соблюдались термический режим и время обработки древесины.
Проваренный фанерный кряж подаётся в отделение по окорке и распиловке.
Окорка осуществляется следующим образом: специальные ножи окорочного станка надрезают кору и снимают её лентами по спирали. Снятая кора используется как для отопления самого комбината, так и соседних зданий или даже целого посёлка. Так происходит, например, на Пермском фанерном комбинате (группа «СВЕЗА»). Котельная предприятия обслуживает и комбинат, и посёлок Уральский, в котором расположено предприятие.
Окорённый кряж (практически без коры) проходит через металлодетектор. Он помогает обнаружить металлические включения в древесине: гвозди, остатки проволоки и т.п., которые могут испортить оборудование. При обнаружении металла на пульт управления станка поступает сигнал, процесс останавливается, и металл удаляется оператором.
После окорки выполняется распиловка. Обработанное сырьё пилится на чураки для производства продольного и поперечного шпона.
Производство и обработка шпона
Следующий этап – лущение шпона на специальных станках, где с подготовленного чурака срезается непрерывная тонкая лента шпона. Чем тоньше шпон, тем больше слоёв будет в фанере определённой толщины. Чем больше слоёв, тем прочнее фанера. Шпон из российской берёзы – самый тонкий (1,2-1,5 мм) по сравнению с другими породами древесины (например, толщина шпона из тополя 1,6-2,6 мм, а хвойного шпона – 2-4 мм).
На этапе лущения осуществляется контроль качества шпона: ежедневно отбираются образцы для проверки толщины и ещё ряда параметров, а полученные результаты сравниваются с нормативными. С учётом этих данных производится настройка лущильных станков.
После лущения лента шпона подаётся на автоматические ножницы, где происходит рубка на форматные листы шпона размером 1,3х2,6 м для производства фанеры формата 1220х2440 мм. Продольный и поперечный шпон (для последующего склеивания в одном листе фанеры) производится на отдельных лущильных линиях.
Разрезанный на форматные листы шпон поступает в сушилку.
«Находясь в сушилке, листы шпона обдуваются горячим воздухом. За 8-10 минут из древесины уходит до 90% влаги. На выходе из сушилки листы шпона укладываются на поддон или попадают на транспортёр (в зависимости от конструкции сушилки)», – комментирует Наталья Андреева, инженер-технолог производства ламинированной фанеры комбината «Фанплит», входящего в состав группы «СВЕЗА».
После просушки шпон сортируется по целому ряду параметров, в том числе на наличие выпавших сучков, трещин и т.п. На многих комбинатах на этом этапе используется автоматизированн На этом же этапе оценивается влажность листов. Если шпон оказался недосушенным, он откладывается в отдельную стопу и досушивается позже.
Если на этапе сортировки выявляются дефекты, то листы не утилизируются, а отправляются на починку. Починка шпона может осуществляться как на ручных станках, так и на оборудовании с автоматическим управлением. Автоматические станки позволяют повысить качество фанеры, сократив затраты ручного труда в 3 раза. Сейчас существует оборудование для починки шпона любых форматов: как стандартного – 5х5 футов (1525х1525 мм), так и большого – 5х10 футов (1500/1525х3000/
Комплектование фанеры
Для получения готовой фанеры необходимо склеить несколько листов шпона между собой. Волокна в последовательных слоях шпона располагаются перпендикулярно друг другу, что придаёт прочность готовому продукту. Полученные листы оказываются стойкими к деформации в любых направлениях. Эта особенность определяет применимость фанеры в опалубочных системах для монолитного строительства.
При производстве берёзовой фанеры склеивается нечётное количество листов шпона в фанеру толщиной от 3 до 40 мм. Между собой листы склеиваются при помощи клея, который изготавливают здесь же, в специальном смесителе. Он состоит из мела, воды, смолы, а также древесной или ржаной муки. Важно строгое соблюдение технологии производства клея, чтобы не произошло расклеивание слоёв фанеры. На современных предприятиях установлено оборудование, которое автоматически контролирует пропорции ингредиентов в соответствии с рецептурой.
На следующем этапе, вальцовке, лист шпона пропускается между двумя валиками, смазанными клеем. Клей равномерно распределяется по обеим поверхностям листа, после чего эти листы отправляются в наборку.
«В стопе наборного пакета сухой шпон чередуется со шпоном, намазанным клеем. Количество чередующихся листов зависит от толщины фанеры. В конце процесса комплектования одного листа фанеры автомат подаёт 2 листа сухого шпона (последний лист предыдущего «сэндвича» и первый следующего), что позволит позже отделить один лист фанеры от другого. Подготовленная таким образом стопа отправляется на подпрессовку», – комментирует Елена Вершинина, начальник службы качества Пермского фанерного комбината, входящего в состав группы «СВЕЗА».
Холодная подпрессовка пакетов собранного шпона производится непосредственно перед горячим прессованием с целью получения цельных пакетов, удобных для транспортировани
После этого осуществляется загрузка предварительно склеенных листов в этажерку горячего пресса для окончательного приклеивания при температуре 120-130оС и давлении 1,2-1,8 МПа.
После прессования склеенные листы обрезаются с четырёх сторон под формат, требуемый заказчиком: к примеру, 1250х2500 мм или 1220х2440 мм с точностью до 3 мм. При производстве ламинированной фанеры станок выполняет предварительную обрезку до размера 1290х2550 мм, чтобы после нанесения плёнки лист можно было ещё раз подровнять, срезав оставшиеся миллиметры.
Далее выполняется шлифование на станке для придания фанере гладкой поверхности и выравнивания её по толщине. Фанера последовательно проходит через шлифовальные ленты с разной зернистостью. После этого фанеру снова классифицируют по внешнему виду: качество листов оценивает оператор.
Завершение: ламинирование поверхности
На заключительном этапе на лист фанеры с двух сторон наносится плёнка. Затем фанера загружается в многопролётный пресс, в котором одновременно могут находиться 15-18 листов продукции. Прессование, в процессе которого пленка схватывается с поверхностью плиты, осуществляется в течение 4,5-10 минут при температуре 130-136оС. Время прессования зависит от плотности плёнки, толщины фанеры и вида покрытия (гладкая или сетчатая). За счёт пленки фанера приобретает дополнительную защиту от воды, механических повреждений, агрессивных сред. Так, из обычной «белой» фанеры получается фанера с покрытием, или ламинированная.
Помимо глянцевой плёнки, на ламинированную фанеру может наноситься сетчатое покрытие, обладающее антискользящим эффектом. Такая фанера востребована в транспортном машиностроении: она применяется в полах трейлеров и лёгких коммерческих автомобилей. А также в качестве настилов в строительных лесах на стройплощадках.
Далее ламинированная фанера попадает на линию обрезки, где обрезается по формату.
После этого готовую продукцию сортируют по внешнему виду и геометрическим параметрам и укладывают в пачки. По завершении сортировки пачки фанеры подаются в покрасочную камеру. Здесь на торцы плиты наносится специальная водоэмульсионная краска на акриловой основе. Такое покрытие защищает фанеру от попадания влаги и разбухания.
Чем лучше прокрашены торцы, тем лучше влагозащитные свойства плиты, а значит, больше циклов заливки бетона фанера сможет выдержать. Особенно это важно для опалубки перекрытий, где фанера подвергается сильным механическим нагрузкам и воздействию агрессивной среды – бетонной смеси.
Если ламинированная фанера хорошо склеена внутри, имеет ровную поверхность, которая покрыта износостойкой плёнкой, и защищённые от влаги торцы, она будет дольше сохранять свою форму. А это значит, что даже при многократном применении одного и того же листа фанеры (не менее 15-20 циклов) качество монолитных перекрытий будет неизменным.
«Ламинированная фанера особенно востребована в монолитном строительстве. Её популярность объясняется механическими свойствами: только берёзовая фанера, благодаря высокой прочности и упругости, способна выдерживать нагрузки, воздействующие на опалубку в процессе бетонирования», – комментирует Наталья Андреева (группа «СВЕЗА»).
Как мы увидели, процесс производства ламинированной фанеры довольно сложен. И качество конечного продукта зависит от чёткого соблюдения технологии на каждом этапе его производства.
Если использовать фанеру ненадлежащего качества, то поверхность стен и перекрытий здания будет неудовлетворител
При подготовке статьи использованы материалы пресс-службы «СВЕЗА»
Историческая справка
Первую модель лущильного станка в конце XVII создал инженер-механик Сэмюэль Бентам, ранее служивший Екатерине II по приглашению князя Потёмкина. По окончании 10-летней службы в России Бентам вернулся в Англию и получил патенты сразу на несколько своих изобретений. Впрочем, изобретённый англичанином станок не был замечен производителями тех времён.Действительно эффективный прототип всех современных лущильных станков создал шведский инженер-изобрета В начале XIX века русский промышленник Дитрих Мартин Лютер, владевший мануфактурой по производству карандашей в эстонском Ревеле (современный Таллинн), изобрёл свой лущильный станок — более крупную версию станка для производства карандашей. Он получил патент на своё изобретение в 1819 году. Первая фанера, производство которой основывалось на станке Дитриха Мартина Лютера, была создана эстонским мебельщиком Александром Лютером, его однофамильцем. В конце XIX века он решил использовать склеенные между собой листы шпона в качестве сидений для венских стульев — мебель получилась лёгкой, прочной и недорогой, благодаря чему на неё возник устойчивый спрос. Практически одновременно с мебельщиком Лютером фанера была создана русским изобретателем — Огнеславом Степановичем Костовичем, занимавшимся созданием летательных аппаратов и остро нуждавшимся в конструкционном материале для их постройки. В 1881 году он изобрёл арборит — материал, состоящий из склеенных между собой поперёк волокон листов шпона.
Лущильный станок и клей для производства фанеры-арборита Костович также изобрёл самостоятельно, причем его фанера обладала высокой устойчивостью к воздействию влаги и была не подвержена гниению.
RAUTE: smart-технологии для производства шпона и фанеры
Комплексные технологические smart-решения компании Raute повышают эффективность деревообрабатывающего производства на каждом из этапов, от биржи сырья до готовой фанеры. Название финской компании Raute образовано из двух финских слов: первые три буквы rau – от слова rauta, что значит «железо», последние две буквы te – от слова teollisuus, «промышленность».
Начав свою работу более ста лет назад, в 1908 году, с производства оборудования из стали и небольших судов, Raute зарекомендовала себя как один из ведущих международных экспертов и новаторов в технологиях деревообрабатывающего производства, в частности, в производстве фанеры и бруса на основе клееного шпона.
Международный эксперт в области деревообработки
Растущая популярность различных изделий, изготовленных из возобновляемых материалов – одна из главных тенденций последнего десятилетия. Наиболее яркое воплощение этот тренд получил в строительстве – на подъеме каркасное деревянное домостроение и использование натуральных материалов в отделке, – что, в свою очередь, напрямую отражается на росте деревообрабатывающей промышленности.
Непосредственный вклад в этот рост вносит финская компания Raute, занимающая первое место в мире в области полного оснащения фанерных комбинатов и комбинатов по производству ЛВЛ (бруса на основе клееного шпона). Доля компании в производстве фанеры 15–20%. Позиции в сегменте производства ЛВЛ также сильны: примерно половина бруса на основе клееного шпона, производимого по всему миру, выпускается на оборудовании Raute.
В сфере оснащения деревообрабатывающих производств Raute работает по принципу «под ключ»: пакет предложений включает как поставку оборудования для налаживания производственного процесса заказчика, так и полный комплекс услуг по обслуживанию оборудования – от ремонта и поставки запасных частей до регулярного технического обслуживания и модернизации. Кроме этого, компания активно развивает цифровые услуги: сбор данных в режиме реального времени, контроль оборудования в удаленном режиме, обучение сотрудников по сети, круглосуточную линию технической поддержки.
Производственные центры Raute расположены Финляндии, городах Настола и Каяани, а также в Канаде, вблизи Ванкувера, и в одном из крупнейших городов Китая, Шанхае. Сеть продаж компании охватывает все страны мира, постоянно расширяются зоны обслуживания и поставки запасных частей.
В основе эффективности – smart-технологии
Клиенты Raute – компании-производители шпона, фанеры и ЛВЛ со всего мира. В России крупнейшим потребителем продукции финского производителя является фанерная промышленность: наиболее востребованы линии по лущению и сушке шпона, прессы. На счету Raute несколько интересных проектов с российскими деревообрабатывающими компаниями. В их числе строительство «Вятского фанерного комбината» (Кировская область) по выпуску березовой фанеры; проектная мощность производства – 93 тыс. м3 березовой фанеры в год. Высокопроизводительной техникой марки Raute (линии раскроя, лущения, сушки и сортировки, линии шпонопочинки, ребросклейки и сращивания, линии клеенанесения,прессования и линии ламинирования, линии обрезки и шлифования) были оборудованы два? предприятия группы «СВЕЗА», одного из мировых лидеров в производстве березовой фанеры, – «СВЕЗА Мантурово» (Костромская область) и «СВЕЗА Новатор» (Вологодская область). И не только эти два завода холдинга Свеза, а так же Свеза Усть-Ижора, Свеза Кострома, Свеза Уральский, Свеза Верхняя Синячиха.
Клиенты выбирают Raute не только за более чем столетнюю экспертизу и опыт в производстве деревообрабатывающего оборудования, но и за активное внедрение в производственный процесс современных высокотехнологичных решений. Один из примеров – технология Smart Mill (Умная «мельница» Умный комбинат), разработанная корпорацией Raute. В основе концепции Smart Mill – комплексные технологические решения, позволяющие при помощи умных анализаторов и цифровой информационной системы улучшить работу оборудования на каждом из этапов, от биржи сырья до готовой фанеры и клееного бруса. Совершенствование технологического процесса повышает общую эффективность производства, снижая материальные потери и увеличивая прибыль. К примеру, коэффициент использования сырья возрастает до 15% по сравнению с традиционными технологиями изготовления шпона.
Умное производство фанеры на основе технологий G5
Разработкой линейки smart-технологий под общим названием G5 занималось структурное подразделение корпорации Raute – Mecano. Передовое программное обеспечение и устройства управления технологическим процессом измеряют, анализируют и калибруют шпон, за считанные секунды принимая решения по его обработке. К примеру, если по расчетам сканера дальнейшие действия по обработке материала не оправданы, шпон извлекается из технологического процесса еще на этапе лущения и далее перерабатывается в топливо или древесную массу. «Умные» устройства также берут на себя решения о починке, ребросклейке или ремонте сращиванию шпона.
Установка сканеров в начале производственной линии, позволяет не прогонять низкосортный шпон через все этапы, как это бывает на большинстве фанерных комбинатов, и тем самым оптимизировать работу. За счет увеличения пропускной способности линий сушки, починки, сращивания и ребросклейки, на которые подается только деловой шпон, достигается существенная экономия сырья, а также других ресурсов (электричества, времени, площадей для хранения). Выстраивание технологического процесса с помощью smart-технологий позволяет оптимизировать работу всего производства и, как следствие, сэкономить значительные средства.
Помимо оптимизации технологического процесса в целом, каждый из блоков G5 повышает коэффициент выхода продукции и ее эксплуатационную готовность в рамках каждой отдельной линии. Результат достигается благодаря совокупности факторов: модернизированной системе машинного зрения-определения дефектов шпона, высокой точности определения влажности шпона, удобному пользовательскому интерфейсу, улучшенному процессу загрузки рецептуры и т. д. Система G5 может быть установлена как на новых линиях и станках, так и в рамках модернизации систем машинного зрения и определения влажности шпона. Возможен как постепенный, от линии к линии, так и единовременный переход на технологию на всем производстве.
Влагостойкая фанера: технология изготовления
Технология изготовления
В общем случае, имеем следующую последовательность:
- Заготавливается древесина (березовые, сосновые и другие виды кряжей).
- Выполняется термообработка с последующим лущением на шпон заготовленной древесины.
- Нанесение клеевых компонентов на специальных станках. При этом верхние шары шпона промазываются с одной стороны.
- Выдержка в пресс-формах высокого давления до высыхания клея.
- Обрезание готовых фанерных листов до технических размеров изготавливаемой фанеры.
В некоторых случаях возможно внесение дополнительных пропитывающих веществ.
С целью увеличения влагостойкости фанерных листов, во время их производства шпон пропитывают дополнительными веществами, как бакелитовый лак или спирторастворимые смолы. Главным фактором наличия влагостойкости является использование синтетических формальдегидов. Они позволяют получить в одночасье крепкий и устойчивый к воздействию влажной среды материал.
Виды влагостойкой фанеры
По своей сути абсолютно все сорта фанеры относятся к влагостойким сортам (кроме изготовленных с применением некоторых клеев естественного происхождения, например, казеинового). Ведь в любом случае при производстве фанерных плит добавляют разнообразные клеи и смолы, что правда различной степени стойкости к растворяемости в воде. По составу соединительных веществ, различают следующие влагоустойчивые материалы:
- Карбамидно-формальдегидная (ФК). Способна выдерживать до 80% влагонасыщенности воздуха, поэтому применима при внутренней отделке помещений и в мебельном производстве.
- Феноло-формальдегидная (ФСФ). Химически активные вещества имеют высокую водоотталкивающую способность. Благодаря этому применяется в наружных отделках. Ее часто применяют как многоразовую опалубку при заливке бетонных растворов, как материал уличной мебели, ограждений и т.
д.
- Ламинированная ФСФ — наличие ламината усиливает влагостойкие свойства материала до максимума.
- Бакелизированная или бакелитовая фанерная плита. Благодаря спирторастворимым смолам, обладает наибольшей стойкостью к воздействию влагой, поэтому может применяться для подводных сооружений.
Бакелизированная фанера
Как повысить влагостойкость в домашних условиях
Не каждый раз есть возможность приобрести более дорогую фанеру высокой влагостойкости. Поэтому процедуру улучшения данного показателя выполняют самостоятельно. И здесь предпочитают 3 основных способа:
- Применение лакокрасочных материалов. Для повышения срока эксплуатации вашей фанеры и повышения ее влагостойкости помогает покрытие лакокрасочным материалом. Процесс предполагает:
- Шлифование поверхности фанерного листа до гладкого состояния;
- Грунтование после обработки от пыли;
- Сушку при нормальных условиях;
- Покраску, максимальный эффект которой достигается при работе распылителем.
Внешнее покрытие лаком укрепит эффект.
- Применение олифы. Процесс разделяют на такие этапы:
- Использование водяной бани для нагрева до 50-60°С олифы.
- Нанесение жидкости на лист фанеры, расположенный горизонтально.
- Просушка листа, например, строительным феном либо утюгом.
- Покрытие вторым слоем олифы с повтором процесса.
- Выполняется до потери фанерой возможности впитывать материал.
Технология фанеры — сырье и материалы
Лекция №4. Технология фанеры
План лекции:
— сырье и материалы в производстве фанеры
— подготовка сырья к лущению, — получение, сушка шпона,
— подготовка шпона к склеиванию;
— обработка готовой фанеры.
4.1 Сырье и материалы в производстве фанеры
Сырье на предприятия производящие фанеру поступает в
виде кряжей, реже в виде чураков. Чураки получают из фанерных кряжей их
разделкой по длине. Длина чурака должна быть равна формату необрезной фанеры с
учетом припусков на усушку и механическую обработку. В цеха по производству
фанеры сырье может поступать в виде лущеного шпона. Лущеный шпон – это
тонкий лист древесины заданной толщины, полученный при лущении фанерного
чурака. В производстве фанеры используют клеи на основе
карбамидоформальдегидных и фенолоформальдегидных смол, реже казеиновые клеи.
4.2 Технология фанеры
Технологические процессы производства фанеры на различных предприятиях могут отличаться набором технологических операций, применяемыми режимами обработки и оборудованием. Однако, технологии во много похожи и могут быть условно разделены на следующие этапы:
— первичная обработка и подготовка сырья к лущению;
— лущение и подготовка шпона к склеиванию;
— нанесение клея, сборка пакета, горячее прессование фанеры;
— обработка готовой фанеры, сортировка, маркировка, упаковка.
Принципиальная схема технологического процесса
производства фанеры приведена на рисунке 4. 1.
4.2.1 Первична обработка и подготовка сырья к лущению
— Разделка кряжей на чураки (раскряжевка)
Данная операция является важнейшей на участке подготовки сырья к лущению, поскольку определяет эффективность использования древесины. Разделывать кряжи на чураки можно до окорки и гидротермической обработки (ГТО) (1 метод), после ГТО в окоренном виде (2 метод). Второй метод позволяет более точно определить качество кряжей.
Существует два способа разделки: по наибольшей массе и наибольшему качественному выходу. При реализации первого способа получают чураки наибольшего объема не зависимо от их качества, с наименьшей потерей древесины при вырезке дефектов.
Промышленное производство фанеры основано на опыте и ноу-хау нескольких поколений.
Бизнес-модель фанерной промышленности все больше ориентируется на ноу-хау, управление производственными технологиями и обслуживание клиентов. Фанера производится из северных мягких пород древесины и березы, которые подходят для изготовления фанеры, требующей долговечности.
Мировые тенденции благоприятствуют использованию фанеры
По словам Мики Силланпяя, исполнительного вице-президента UPM Plywood, основными тенденциями мирового развития являются увеличение использования фанеры в нескольких отраслях. «Урбанизация увеличивает количество новых зданий с фанерой, но этот материал также имеет много потенциальных применений при ремонте и расширении. В то же время рост электронной коммерции привел к увеличению грузоперевозок, где фанера является основным материалом для полов при строительстве транспортного оборудования ».
По словам Силланпяя, легкий вес фанеры является важным активом в транспортной отрасли.«Экологические ценности постоянно увеличивают спрос на возобновляемые и более легкие материалы», — говорит Силланпяя.
Строительство резервуаров для жидкого азота (СПГ) было стабильным бизнесом в течение трех десятилетий.Успех UPM в отрасли основан, в частности, на изоляционных свойствах березовой фанеры в экстремально холодных условиях. Во время транспортировки температура газа составляет минус 163 градуса, а березовая фанера хорошо сохраняет свою прочность, несмотря на экстремальные минусовые температуры.
«Танкеры СПГ большие, а это значит, что в их конструкции используются большие объемы фанеры. На одну цистерну требуется от одной до трех тысяч кубометров фанеры в зависимости от технологии утепления.Транспортировка СПГ находится на подъеме, что отражается в строительстве подходящих транспортных судов », — заключает Силланпяя.
Помимо строительной индустрии и строительства транспортного оборудования и резервуаров для СПГ, фанера производится для мебельной промышленности, а также для внутренней отделки и производства паркета. «Обычно эти конечные пользователи потребляют высококачественную фанеру в более высоких ценовых диапазонах, и мы инвестировали в развитие производства и сеть обслуживания конечных потребителей, чтобы обслуживать этих клиентов.”
Новые инвестиции для увеличения производства фанеры
Строительство в Европе растет после длительного спада, и рост значительно увеличил спрос на фанеру. Строительство — это крупнейший сектор конечного использования фанеры. По словам Силланпяя, фанерный бизнес позиционирует себя как производитель материалов в строительной отрасли и не заинтересован в том, чтобы заходить слишком далеко в сферу конечного использования своих клиентов. «Когда мы работаем через дистрибьюторские сети, мы можем продавать продукцию любому оптовику, которого пожелаем. Что касается количества использованной и потребляемой фанеры, для нас не имеет большого значения, будет ли метод строительства бетонным или деревянным. В бетонных конструкциях, в том числе, используется фанера в литейных формах ».
Большая часть фанеры, используемой в строительстве, — это фанера хвойных пород. Березовая фанера, будучи более прочной и ценной, используется в промышленной переработке. На один кубометр фанеры нужно два кубометра древесины хвойных пород, а на то же количество березовой фанеры — три кубометра березовой древесины.«Доступность березы будет серьезной проблемой в будущем, поскольку Финляндия и Россия — единственные регионы, где дерево растет в изобилии, требуемом для промышленного использования».
«Расширение завода в Чудово в России — важный шаг в реализации нашей будущей стратегии, которая включает обеспечение поставок сырья. Наша цель — еще больше укрепить наши позиции в наиболее важных сферах применения фанеры. Добавленные мощности по производству березовой фанеры являются конкурентоспособными, что улучшает нашу способность удовлетворять растущий спрос на ключевых рынках », — напоминает нам Силланпяя.
Силланпяя, наличие сырья будет увеличиваться как побочный эффект инвестиций в новый целлюлозный завод. «По мере роста спроса на всю древесину доступность видов древесины, необходимых для деревообрабатывающей промышленности, должна улучшиться вслед за увеличением производства целлюлозы. А поскольку мы покупаем самую дорогую часть бревна, это тоже хорошая новость для лесовладельцев ».
По словам Силланпяя, Финляндия имеет хорошую репутацию в деревообрабатывающей промышленности как поставщик и экспортер.«Мы используем сертифицированную древесину в своей обработке, и у нас нет этических проблем в нашем производстве».
В последние годы UPM инвестировала в увеличение производства в Финляндии и Эстонии, а также в настоящее время расширяет фанерный завод в Чудово, Россия. Общая стоимость инвестиций составляет 50 миллионов евро. Инвестиции увеличат производственную мощность завода на 45 000 кубических метров, увеличивая годовой объем до 155 000 кубических метров, и расширит ассортимент продукции завода. На территории завода также строится новая электростанция, работающая на биомассе.
UPM Plywood — ведущий производитель фанеры в Европе, поставляющий фанеру и шпон, в частности, для нужд строительной и транспортной отраслей. Компания также производит древесный материал UPM Grada, пригодный для компрессионного формования. Компания работает в десяти разных странах, имеет в общей сложности девять заводов и около 2500 сотрудников. Оборот в прошлом году составил 484 миллиона евро.
Эта статья является частью серии статей, написанных Маркку Лаукканеном и Микко Вильякайненом.В этой серии представлены различные передовые практики и тенденции финской деревообрабатывающей промышленности. Цель состоит в том, чтобы распространить информацию о передовых методах и решениях в финской деревообрабатывающей промышленности для повышения ее конкурентоспособности и более широкого распространения финского опыта. Статьи будут опубликованы на финском и английском языках. Они будут бесплатно доступны для использования в качестве исходного материала и для публикации в том виде, в котором они есть. Статьи будут распространяться в виде информационных бюллетеней Puuinfo, а также будут публиковаться на сайте puuinfo.fi и woodproducts.fi. Эта серия статей финансируется Операционной программой деревянного строительства Министерства окружающей среды.
Все о фанере — обновленное руководство по дизайну и типам фанеры
Если вы планируете реконструировать свой дом или заказать мебель, то есть некоторые термины, с которыми вам следует ознакомиться. Лучше познакомиться и с некоторыми техническими терминами, чтобы плотник вас не обманул.
Вы наверняка видели дерево в различных формах в столярной мастерской или в собственном доме, когда вы ремонтировали свой дом.
Древесина, которая выглядела так, как будто некоторые слои были соединены вместе и использовалась для изготовления мебели, особенно гардероба и кухонных шкафов , называется фанерой. Это ваш лучший помощник при изготовлении мебели для интерьера.
Что такое слой?
Давайте выясним, из чего делается слой. Фанера или фанера — это термин, используемый для продукта, который изготавливается путем склеивания тонких деревянных листов. Тонкие листы дерева склеиваются для получения фанеры одинаковой толщины.
Источник
Проще говоря, тонкие слои древесины определенного размера связываются вместе, чтобы получить лист древесины хорошей толщины.Каждый слой называется шпоном.
Шпон обычно изготавливается из различных пород дерева, таких как тик, ель, береза и т. Д. Обычно шпон получают из древесины хорошего качества.
Обычно выбирается нечетное количество виниров, например 3, 5, 7 и т. Д. . Такие слои уравновешивают лист и исключают коробление. Фанера широко используется в деревообрабатывающей промышленности.
Сегодня большая часть предметов домашнего декора и домашней мебели изготавливается из фанеры.Преимущество слоев в том, что они дешевы, могут быть переработаны и гибкие. Таким образом, их можно использовать для изготовления многих продуктов. Кроме того, поскольку слои могут быть изготовлены на месте, их легко достать.
Плотники и дизайнеры интерьеров предпочитают фанеру простой древесине, потому что, в отличие от простой древесины, фанера долговечна и не сжимается, не трескается, не деформируется и не скручивается. Конечно, это тоже длится долго.
Процесс изготовления слоя:
Если вы думали, что сделать слой проще и что для его склейки нужно всего лишь несколько слоев дерева и качественный клей, то вы в чем-то правы, но во многом ошибались.Хотя процесс изготовления слоя кажется проще, это не так просто. Для изготовления прочного слоя требуется как минимум 14-15 этапов процесса.
Переход от неровной твердой древесины к гладкому, ровному и прочному куску фанеры — долгий. Процесс действительно интересный.
Источник
Вот шаги, которые превратят обычную древесину в красивый слой:
Блокировка отделения:
Бревна снимаются и разрезаются на требуемый размер. Этот процесс известен как блокировка отделения.
Приготовление:
Этот процесс назван так потому, что ксилография подвергается воздействию заданной температуры около 60-80 градусов.
Для завершения процесса приготовления может потребоваться около 12 часов. Это делается для удаления крахмала, а также для уничтожения микроскопических организмов, присутствующих в древесине.
Потому что, если организмы не погибнут, они могут атаковать образовавшийся слой и таким образом повредить его.
Пилинг:
Это именно то, что следует из названия.Бревно после приготовления очищается от кожуры до необходимой толщины. Это делается с помощью машины для очистки от кожуры.
Намотка:
Теперь древесину можно назвать шпоном. Впоследствии его наматывают.
Источник
Вырезка:
Шпон обрезан по требуемым размерам.
Сушка:
Теперь шпон просушен при определенной температуре. Цель этого шага — удалить всю влагу, а также уничтожить оставшиеся микроорганизмы.Этот шаг очень важен, потому что любой шпон, содержащий влагу, не подходит для изготовления слоя.
Смола:
Этот этап также можно назвать процессом склеивания. Это также важная и самая важная часть производственного процесса, потому что правильное склеивание — это секрет прочного слоя. Большинство компаний предпочитают производить смолу собственными силами, чтобы гарантировать максимальное качество.
Шпон склеен и доведен до совершенства, чтобы обеспечить прочность и стабильность размеров.
Тестирование:
Только что изготовленная фанера проходит лабораторные испытания на предмет дефектов.
Прессование:
Обычно существует два метода прессования: один — метод предварительного прессования, второй — горячее прессование. Процесс предварительного прессования помогает расширить и стабилизировать каждый слой, чтобы гарантировать, что продукт не деформируется. Процесс горячего прессования должен гарантировать, что слой имеет однородную плотность на всех уровнях и точках.
После выполнения обоих этих действий слою дают остыть в течение 24 часов.
Раскрой и обрезка:
Очень важно, чтобы слой имел точность размеров. Именно поэтому этот процесс выполняется очень осторожно.
Шлифовка:
Этот шаг обеспечивает ровную поверхность слоя
Также читайте: О слоях и производстве ДСП
Инспекция и отправка:
Последний шаг — проверка качества фанеры, после чего слои отправляются в различные места в соответствии с полученными заказами.В Индии доступны различные типы фанеры В Индии доступно множество типов фанеры в зависимости от толщины, вида древесины, из которой сделан слой, а также качества.
То, как будет использоваться слой, также является одним из факторов классификации слоя. В Индии доступны следующие типы фанеры:
Внутренний и наружный слой :
В интерьере и экстерьере используются разные виды слоев. Обычно для наружных работ используют водостойкий или водостойкий слой.Под термином «интерьер» это означает, что такой слой используется для изготовления мебели, дверей и т. Д.
Такой тип фанеры известен как коммерческая фанера MR, где MR является аббревиатурой от словосочетания «Влагостойкость». Внешняя фанера называется фанерой BWP или BWR. BWP означает «Устойчивость к кипящей воде», тогда как BWR означает «Устойчивость к кипящей воде».
Источник
Коммерческая фанера: В Индии термин коммерческая фанера обозначается как слой «MR».Этот слой является внутренним слоем и используется для изготовления внутренней мебели. Когда говорят, что влагостойкий, это не значит, что он водостойкий.
Как вы знаете, существует огромная разница между водой и влагой. Водонепроницаемые слои — это слои BWR, устойчивые к кипящей воде. Таким образом, коммерческий слой может выдерживать определенную влажность, но он не является водонепроницаемым.
Номера спецификаций индийских стандартов для различных видов фанеры
IS: 303 — фанера MR, фанера BWR, Flexi Ply
IS: 710 — Морская фанера
IS: 10701 — Конструкционная фанера
IS: 5509-1980 — Огнестойкая фанера
IS: 4990 — Фанера опалубочная
Калиброванный слой:
Этот слой используется для максимальной точности.Внутренний слой иногда имеет толщину всего 0,005 дюйма, поэтому вы можете себе представить, насколько совершенен этот слой.
Калиброванный слой в основном используется для такой мебели, где необходимо поддерживать однородность по толщине.
Морской слой:
Этот термин используется для обозначения наружной фанеры и пользуется большим спросом в судостроении. Морская ткань также используется для изготовления лодок и предпочтительна в промышленности из-за ее водостойкости.
Морской слой, хотя и не очень часто используется в интерьере, некоторые все же используют его для изготовления кухонной мебели, поскольку такие типы мебели часто подвергаются воздействию воды.
Классификация на основе используемого сырья (древесины) Фанера из твердой древесины — это термин, используемый для слоев тикового дерева или натурального дерева. Это одна из самых качественных фанер.
Источник
Слой мягкой древесины
Это термин, используемый для дерева, сделанного из мягких деревьев, таких как сосна, ель, ель или кедр.Слои, изготовленные из древесины манго, также относятся к хвойным.
Метрические размеры фанеры хвойных пород:
Слой мягкой древесины имеет метрические размеры 1,2 м x 2,4 м или 4 фута x 8 футов.
Прочие термины, связанные с фанерой Гибкая фанера , как следует из этого термина, представляет собой гибкие слои, которые можно гнуть или катать. Такие слои крайне востребованы при изготовлении дизайнерской мебели. Огнестойкий слой используется в торговых центрах, театрах, кухнях ресторанов для предотвращения возгорания.
Поскольку древесина чрезвычайно горючая, огнестойкие слои могут предотвратить возгорание слоев или распространение огня. Толщина слоев указывает на их использование. В Индии доступны слои различной толщины от 3 мм до 25 мм.
Толщина индийской фанеры доступна от 3 до 9 мм, 12 мм, 15 мм, 16 мм, 19 мм, 22 мм и 25 мм. Фанера толщиной 3, 4 и 6 мм. Обычно используется для изготовления мебели и предметов интерьера.
Толщина от 12 мм до 19 мм -> Такие слои обычно водонепроницаемы и изготавливаются из твердой древесины. Следовательно, такие слои обычно используются в кухонной мебели, особенно для изготовления модульных кухонь и другой мебели.
Его высокое качество также делает его пригодным для изготовления потолков, ванных комнат, дверей и окон. Большинство таких слоев также оказывают сопротивление термитам, вечным врагам древесины.
В наши дни почти нет простой кухни. Большинство домовладельцев предпочитают модульную кухню, так как она проста в использовании, элегантно выглядит и придает кухне красивый вид.В Индии для изготовления модульной кухни предпочтительнее использовать плиточный материал.
Почему для Modular используется слой толщиной 16 мм?
Слой толщиной 16 мм является предпочтительной для этой толщины, что гарантирует прочную модульную кухню, а также служит долгое время благодаря своей прочности.
Фанера толщиной 25 мм -> Такая фанера также известна как фанера для опалубки. Этот тип слоя является лучшим из всех слоев и используется при опалубке во время строительства, а также для других строительных целей.
Декорирование фанеры Фанеру обычно декорируют ламинатом, красками и затем полируют. Сунмика — это наиболее распространенный ламинат, используемый для декорирования слоев. Он также популярен, потому что доступен в разных цветах, фактурах и даже узорах.
По сравнению с ламинатом, краски дешевле и надолго защищают дерево. Хотя полировка обычно выполняется на твердой древесине, слои также полируются, чтобы она выглядела ровно и хорошо. Ply лучше всего подходит для гардеробы. По мере того как дизайн интерьера совершенствуется с развитием технологий, в гардеробах также произошли некоторые большие инновации.
Разве вы не хотите, чтобы гардероб был уникальным и отличался от гардероба вашего соседа? Лучший способ убедиться в этом — сделать гардеробы из фанеры.
Гибкость и прочность Ply делают его наиболее подходящим материалом для изготовления шкафов. Конечно, их также можно украсить по вашему выбору, придав им красивый вид снаружи.
Посмотрите это видео, чтобы узнать материалы:
youtube.com/embed/hkLb7EYHRFg?start=3″ frameborder=»0″ allowfullscreen=»allowfullscreen»/>
Преимущества слоя
- Удобно использовать: Ply легко использовать.Слой легко прибить гвоздями или винтами, и, в отличие от дерева, эти процессы не повреждают слой. Доступны самые разные размеры. Слои доступны в различных размерах и имеют подходящую длину и ширину, поэтому их удобно использовать для изготовления любой мебели.
- Обеспечивает хорошую прочность: Слои намного прочнее любых других пород дерева. Они также прочные.
- Высокоэкономичный: При изготовлении слоя древесины тратится немного.Из тонких листов разного качества тоже можно сделать слой превосходного качества.
- Не сильно повреждает: Слои сделаны таким образом, что они не деформируются и не сжимаются, поэтому подходят для использования в течение длительного времени.
- Гибкость и разумность: Ply гибкий и поэтому пользуется большим спросом для создания креативных дизайнов в дизайне интерьеров и других декоративных материалов. Он также прост в использовании, и поэтому дизайнеры интерьера предпочитают фанеру любому другому материалу для изготовления высококлассных кухонь и других внутренних работ.
Кроме того, слои более прочные и долговечные, что делает его очень популярным среди плотников и в промышленности.
Теперь, когда вы знаете тонкости этого слоя, лежащего в вашем доме, вы сможете получить лучшую мебель со слоем и сделать внутренние работы для вашего дома.
После того, как ваш дом будет закончен, скажите мягкое «спасибо» слою, который делает ваш дом таким красивым.
Следите за нами и ставьте лайки:
Фанера
Наша компания предлагает березовую фанеру различных пород и сортов. Вся поставляемая нами фанера производится на современном европейском оборудовании и имеет международные сертификаты (CARB, FSC и др.), Подтверждающие отличное качество и безопасность нашей продукции.
Предлагаем к поставке следующие виды фанеры.
ФАНЕРА БЕРЕЗОВАЯ, INT
Описание
Березовая фанера — многослойный строительный материал, изготавливаемый путем приклеивания березового шпона. Количество слоев обычно неравномерное. Слои шпона расположены относительно друг друга с направлением пересечения зерен для увеличения прочности фанеры.
Приложение
Мебельная промышленность активно использует фанеру INT для производства оптовой и штучной упаковки. Этот строительный материал также можно использовать для композитной теплоизоляции. Фанера высокого качества известна своей прочностью, стабильностью формы и твердостью поверхности. Этот вид древесины популярен благодаря своей простоте использования. Диапазон толщины заготовок довольно широк и может составлять от 4 до 40 мм.
Формат | 1525 * 1525 |
Толщина (мм) | 3, 4, 6, 8, 9, 10, 12, 15, 18, 20, 21, 22, 24 |
Марка | B / BB, BB, BB / CP, BB / C, CP, CP / C, C |
Качество поверхности | шлифованный, нешлифованный, шлифованный с одной стороны |
Класс эмиссии формальдегида | E1 |
Водонепроницаемость | стандарт |
ФАНЕРА БЕРЕЗОВАЯ, EXT
Описание
Это многослойный строительный материал, изготовленный методом склеивания березового шпона.Количество слоев шпона всегда неравномерное. Слои шпона расположены по отношению друг к другу с направлением пересечения волокон для повышения долговечности фанеры.
Приложение
Отличительной особенностью данного продукта является использование клея на основе фенолформальдегидных смол. Это делает изделия особо прочными, с низким коэффициентом насыщения. Эту фанеру можно использовать во внешней среде. Его физико-механические свойства не оставляют сомнений в качестве и долговечности этого продукта.
EXT может использоваться для следующих целей:
- Наружные и внутренние строительные работы и внутренняя отделка;
- Мебельное производство;
- В качестве строительного материала;
- Автомобильная промышленность;
- Производство вагонов;
- Упаковка;
- Изготовление полов (паркет, ламинат, паркетная доска, линолеум).
Формат | 2440 * 1220, 1250 * 2500, 2500 * 1250, 1220 * 2440 |
Толщина (мм) | 4, 6.5, 9, 10, 12, 15, 18, 21, 24 |
Марка | B / BB, BB, BB / CP, BB / C, CP, CP / C, C |
Качество поверхности | шлифованный, односторонний шлифованный, нешлифованный |
Класс эмиссии формальдегида | E1 |
Водонепроницаемость | продвинутый |
ФАНЕРА БЕРЕЗОВАЯ ПЛЕНКОВАЯ, ВНЕШНЯЯ, ГОСТ 53920-2010
Описание
Ламинированная фанера — лучшая водостойкая древесина. Доказал свою высокую плотность и долговечность. На наших производственных линиях ламинированная фанера изготавливается из березового шпона. От стандартной фанеры она отличается тем, что имеет поверхностный слой из плотной бумаги, обработанной фенолформальдегидными смолами или полимерной пленкой. Поверхность материала может быть глазурованной (маркировка F), рифленой (маркировка W) или иметь тиснение.
Приложение
Этот вид фанеры обычно используется в монолитном строительстве, производстве мебели, POS и складском оборудовании, в транспортной автомобильной промышленности и в различной внутренней отделке.
Формат | 2440 * 1220, 1220 * 2440, 2500 * 1250, 1250 * 2500 |
Толщина (мм) | 4, 6, 8, 9, 10, 12, 15, 18, 20, 21, 22, 24 |
Марка | 1/1, 1/2, 1/3 |
Пленка | Темно-коричневый, плотность 120 г / м2, Ж / Ж, В / Ш |
Класс эмиссии формальдегида | E1 |
Водонепроницаемость | продвинутый |
ФАНЕРА СПЕЦИАЛЬНАЯ
Наша компания ориентирована как на конечного потребителя, так и на поставку сырья производственным предприятиям. У нас есть широкий спектр оборудования для производства готовой продукции и полуфабрикатов для дальнейшей продажи.
Предлагаем:
- Фанера, ламинированная разными видами пленок;
- Заготовки машинной резки в соответствии с вашим техническим заданием;
- Фанера нестандартных размеров фанера 2500 * 4500, фанера с однонаправленным слоем шпона;
- Фанерные заготовки — аналоги латофлекса и многих других изделий.
Перед заказом фанеры рекомендуем сначала связаться с нами: возможно, мы сможем предложить Вам готовую продукцию.
Если вы заинтересованы в этом типе продукции, не стесняйтесь обращаться к нам.
Фанера | WoodSolutions
Облицовка, внешняя
Ни один другой облицовочный материал не может предложить свободу дизайна, простоту в обращении, ассортимент и естественную красоту древесины. Деревянная облицовка позволяет создать здание, подходящее практически для любой среды, вкуса и стиля.
Деревянная облицовка имеет встроенную гибкость, которая обеспечивает естественные преимущества на участках, подверженных сильным ветрам, экстремальным климатическим условиям, высокореактивным грунтам, просадкам или подземным толчкам.В отличие от кирпичной кладки и других жестких материалов, естественная упругость и высокое соотношение прочности и веса древесины позволяют ей выдерживать гораздо большие нагрузки и движения.
Современная отделка придает деревянной облицовке долговечный и привлекательный вид и может использоваться для изменения цвета и стиля здания, что делает ее универсальным материалом, который будет соответствовать меняющимся вкусам и моде.
Двери
Вне зависимости от того, изготовлен ли он из массивной или конструкционной древесины, существует множество стильных и практичных вариантов, которые не снижают прочности и структурных характеристик. Характерная деревянная дверь также может создать визуальный эффект, добавляя ценности любому коммерческому или домашнему зданию.
Древесина является привлекательным выбором для дизайна и строительства дверей, предлагая прочность, гибкость и универсальность, с которыми трудно сопоставить другие материалы.
Деревянные двери, защищенные от влаги, прослужат долго в любом здании. При регулярном техническом обслуживании тщательно спроектированные и обработанные деревянные двери могут работать в самых тяжелых внешних условиях и, при необходимости, могут быть легко и эффективно отремонтированы или обновлены.
Это руководство по применению описывает общие элементы, используемые при выборе и отделке деревянных внутренних и внешних дверей.
Полы
Будь то конструкционные или готовые полы, древесина обеспечивает долговечность, универсальность и адаптируемость. Теплота, прочность и естественная красота деревянных полов пользуются неизменной популярностью в самых разных интерьерах.
Деревянные полы — это вневременной продукт, предлагающий тепло и естественную красоту, в значительной степени не имеющий аналогов в других вариантах напольных покрытий. В этой статье представлен обзор укладки деревянных полов на несущие балки и балки, деревянных полов и бетонных плит. Деревянные полы обычно поставляются в виде изделий из цельной древесины или клееной древесины, изготовленных из слоев клееной древесины. Он стыкуется с шипом и пазом, а после установки шлифуется и шлифуется.Существует множество видов напольных покрытий, из которых можно выбрать напольное покрытие, и правильный вид для конкретного применения будет зависеть от множества факторов. В этом разделе представлена информация, касающаяся выбора видов, экологической оценки, окончательного выбора и рекомендуемых процедур обслуживания.
Обрамление
Легкие деревянные конструкции обычно включают каркасные и скрепленные конструкции, к которым применяется один или несколько типов облицовки. Конфигурации обрамления могут варьироваться от близко расположенных легких бревен, обычно встречающихся в конструкции каркасов с гвоздями, до больших, более широко разнесенных бревен. Здание с деревянным каркасом может быть размещено на бетонной плите или на столбах / столбах или опорах, опирающихся на опоры / пни, опирающиеся на опорные площадки.
Легкая деревянная конструкция, используемая в домах или многоквартирных домах, предлагает гибкость широкого диапазона экономичных вариантов дизайна.
Когда древесина поступает из экологически безопасных источников, этот метод строительства может быть экологически выгодным, поскольку он сочетает в себе низкую энергию, содержащуюся в древесине, с ее способностью накапливать углерод.
Столярные изделия
Столярные изделия из дерева придают классический, уникальный и стильный вид любому дизайну интерьера или экстерьера. Продукция производится для различных внутренних применений, включая дверные и оконные рамы, краснодеревщики, плинтусы, молдинги и наличники. При взгляде на улицу, столярные изделия варьируются от декоративных карнизов и столбов до привлекательных перил.
Многие породы древесины подходят для изготовления столярных изделий, поэтому следует тщательно выбирать древесину, идеально подходящую для конкретного изделия и его предполагаемой отделки.Редкие и экзотические породы, такие как тик и палисандр, могут создавать изделия выдающейся красоты, но стоимость материалов и их доступность также являются важными факторами.
Коммерчески доступные породы, такие как тасманский дуб, австралийский кипарис, пятнистая камедь и т.п., часто являются более практичным выбором, с дополнительным преимуществом, заключающимся в том, что их можно легко сочетать с другими деревянными изделиями в здании, такими как пол.
Массивная древесина для столярных изделий обычно поставляется как «чистая отделка», но доступны варианты «степени окраски», которые обычно состоят из композитного материала, такого как МДФ или клееный брус.
Большое количество специализированных поставщиков и производителей предлагают потребителю широкий выбор профилей для всех наиболее распространенных и популярных столярных изделий. Выбор во многих случаях ограничен только воображением.
Мебель для мебели часто ассоциируется со столярными изделиями и чаще всего включает шкафы, скамейки и другую аналогичную «встроенную» мебель. Как и столярные изделия, столярные изделия обычно обозначаются как лакокрасочные, так и прозрачные, и, естественно, для древесины с прозрачной отделкой внешний вид и отделка поверхности имеют решающее значение для достижения успешного применения.
Обшивка, Интерьер
Внутренняя обшивка, также известная как внешний вид и облицовка, — это не просто практическое средство для покрытия одной или нескольких стен и потолков в здании, ее включение в дизайн интерьера комнаты может создать эффектный и стильный вид. Внутренняя обшивка может быть либо массивной натуральной деревянной обшивкой, либо листами из конструкционной древесины, которые обеспечивают прочную и износостойкую поверхность для участков, подверженных сильным ударам. Поскольку они обычно служат для создания внешнего вида, к ним обычно не предъявляются требования к конструкции. В этом руководстве описывается разнообразие доступных панелей и описывается простой процесс их установки.
Рамы порталов
Каркасы деревянных порталов — одно из самых популярных конструкций для коммерческих и промышленных зданий, функции которых требуют больших пролетов и открытых интерьеров.Как материал, древесина предлагает дизайнерам простоту, скорость и экономию при изготовлении и монтаже.
Рамы деревянных порталов имеют прочную, прочную и превосходную конструкцию. Структурное действие достигается за счет жестких соединений между колонной и стропильной балкой в коленях и между отдельными стропильными элементами на коньке. Эти жесткие соединения обычно выполняются с использованием гвоздей из фанеры и, иногда, со стальными вставками.
От выбора материала до отделки, это руководство по применению дает исчерпывающий обзор процесса использования древесины в спецификации, изготовлении и возведении конструкций портальной рамы.
Рельсы и балюстрады, интерьер
Универсальность, красота и прочность древесины делают ее идеальным материалом для изготовления внутренних перил и балюстрад. Обработанная древесина хвойных пород и прочная древесина твердых пород являются наиболее популярными вариантами древесины, и их можно обрабатывать для создания ряда уникальных стилей и дизайнов, отвечающих различным вкусам и декорам.
При использовании внутри балюстрады и поручни обычно покрываются прозрачным лаком, чтобы продемонстрировать естественную красоту древесины. При надлежащем уходе и внимании они прослужат всю жизнь.Здесь вы найдете общую информацию о размерах элементов, соединениях и подходящих материалах, а также важные моменты, касающиеся спецификации и конструкции внутренних перил и балюстрад.
Стенки сдвига
Каркасные деревянные здания, состоящие из столбов и балок или стоек и балок, выдерживают боковые нагрузки (ветер, землетрясение или удар) за счет использования жестких рам (порталов), скрепленных каркасов (фермы и поперечные связи) или конструктивных элементов обшивки (диафрагмы).
Мембраны — это эффективное конструктивное решение для противодействия боковым силам. Листовые материалы, которые обычно используются в качестве футеровки или облицовки, обычно можно легко и экономично модернизировать, чтобы выдерживать сдвиговые нагрузки. В этом случае каркас выполняет двойную функцию, выдерживая как горизонтальные, так и вертикальные нагрузки.
В тех случаях, когда диафрагмы представляют собой конструктивную обшивку, могут быть включены дополнительные конструктивные решения, позволяющие противостоять нагрузкам, нормальным к стенам, полу и крышам, с использованием композитной напряженной оболочки, возникающей между обшивкой и деревянным каркасом.
К преимуществам деревянных стен и диафрагм относятся:
- свобода архитектурного дизайна (изгибы, консоли, прозрачные пролеты)
- легкая конструкция
- высокая устойчивость к ударным нагрузкам
- упругость (без хрупких трещин)
- быстрое обычное строительство
В этом разделе вы найдете информацию о конструкции и деталях конструкции деревянных диафрагм (как горизонтальных, так и вертикальных), используемых в жилых, малоэтажных коммерческих и промышленных зданиях.
Конструкция каркаса для статических нагрузок или постоянных и постоянных нагрузок, действующих перпендикулярно каркасу, описана в AS 1720.1 Деревянная конструкция s и AS 1684 Жилое деревянное каркасное строительство . Чтобы добиться эффективного действия диафрагмы, обычно требуются некоторые настройки, в частности детали соединения.
Информация о материалах и системах диафрагмы включена, однако большая часть представленных здесь деталей конструкции и конструкции относится к конструкционным фанерным диафрагмам, для которых доступна задокументированная информация о конструкции.
Внешняя лестница
Все внешние лестницы служат функциональному назначению, но выбор дерева в рамках применения превратит функциональный элемент здания в эстетически приятный элемент. И хотя строительство лестницы требует больших усилий, затраченное время окупится: хорошо построенная деревянная лестница обычно прослужит десятилетия.
Наружные лестницы обычно строятся из обработанной мягкой древесины и прочных твердых пород дерева и обычно покрываются краской.Описанная здесь процедура строительства применима к большинству лестниц обычного или современного типа.
Когда дело доходит до лестниц, существует множество вариантов применения в зависимости от требований к конструкции здания. В этом руководстве обсуждаются наиболее часто задаваемые типы лестниц.
Лестница внутренняя
Внутренние работы по лестнице считаются специализированной областью столярных и столярных работ, поскольку их строительство требует высокого уровня мастерства, детализации и точности.Многие внутренние лестницы построены из качественной столярной древесины, вырезанной и обработанной специально для лестниц. Внутренние лестницы значительно различаются по дизайну: от простых прямых пролетов, обычно используемых в домашних условиях, до более сложных лестниц, специально построенных в качестве отличительных черт в общественных и коммерческих зданиях.
Описанная здесь процедура строительства применима к большинству лестниц обычного или современного типа.
экологичных отпечатков на дереве En
Пожалуйста, замените этот текст своей Политикой конфиденциальности.Пожалуйста, добавьте ниже любые дополнительные файлы cookie, которые использует ваш веб-сайт (например, Google Analytics)
Эта политика конфиденциальности определяет, как Plywood Print использует и защищает любую информацию.
которые вы предоставляете Plywood Print при использовании этого веб-сайта.
Plywood Print стремится обеспечить защиту вашей конфиденциальности.
Если мы попросим вас предоставить определенную информацию, с помощью которой вас можно будет идентифицировать при использовании этого веб-сайта,
тогда вы можете быть уверены, что он будет использоваться только в соответствии с этим заявлением о конфиденциальности.Компания Plywood Print может время от времени изменять эту политику, обновляя эту страницу. Вам следует время от времени проверять эту страницу, чтобы убедиться, что вас устраивают любые изменения.
Что собираем
Мы можем собирать следующую информацию:
- название Контактная информация
- , включая адрес электронной почты
- демографическая информация, такая как почтовый индекс, предпочтения и интересы
- другая информация, относящаяся к опросам клиентов и / или предложениям
Полный список файлов cookie, которые мы собираем, можно найти в разделе Список собираемых файлов cookie.
Что мы делаем с собираемой информацией
Нам нужна эта информация, чтобы понять ваши потребности и предоставить вам лучший сервис, и, в частности, по следующим причинам:
- Внутренний учет.
- Мы можем использовать эту информацию для улучшения наших продуктов и услуг.
- Мы можем периодически отправлять рекламные электронные письма о новых продуктах, специальных предложениях или другой информации, которую мы
Думаю, вам будет интересно воспользоваться предоставленным вами адресом электронной почты.
- Время от времени мы также можем использовать вашу информацию, чтобы связываться с вами в целях исследования рынка. Мы можем связаться с вами по электронной почте, телефону, факсу или почте. Мы можем использовать эту информацию для настройки веб-сайта. в соответствии с вашими интересами.
Безопасность
Мы стремимся обеспечить безопасность вашей информации. Чтобы предотвратить несанкционированный доступ или раскрытие, мы внедрили подходящие физические, электронные и управленческие процедуры для защиты и защиты информацию, которую мы собираем в Интернете.
Как мы используем файлы cookie
Cookie — это небольшой файл, который запрашивает разрешение на размещение на жестком диске вашего компьютера.
Как только вы соглашаетесь, файл добавляется, и cookie помогает анализировать веб-трафик или сообщает вам, когда вы посещаете
конкретный сайт. Файлы cookie позволяют веб-приложениям реагировать на вас как на человека. Веб-приложение
может адаптировать свою деятельность к вашим потребностям, симпатиям и антипатиям, собирая и запоминая информацию о
ваши предпочтения.
Мы используем файлы cookie журнала трафика, чтобы определить, какие страницы используются.Это помогает нам анализировать данные о посещаемости веб-страниц. и улучшить наш веб-сайт, чтобы адаптировать его к потребностям клиентов. Мы используем эту информацию только для статистических в целях анализа, а затем данные удаляются из системы.
В целом, файлы cookie помогают нам предоставлять вам лучший веб-сайт, позволяя нам отслеживать, какие страницы вы считаете полезными.
а у вас нет. Файл cookie никоим образом не дает нам доступа к вашему компьютеру или какой-либо информации о вас,
кроме данных, которыми вы хотите поделиться с нами.Вы можете принять или отклонить куки.
Большинство веб-браузеров автоматически принимают файлы cookie, но обычно вы можете изменить настройки своего браузера. отказаться от файлов cookie, если хотите. Это может помешать вам в полной мере использовать возможности веб-сайта.
Ссылки на другие сайты
Наш веб-сайт может содержать ссылки на другие интересные веб-сайты. Однако, как только вы воспользуетесь этими ссылками чтобы покинуть наш сайт, вы должны принять во внимание, что мы не контролируем этот другой сайт.Поэтому мы не можем нести ответственность за защиту и конфиденциальность любой информации, которую вы предоставляете во время посещение таких сайтов и таких сайтов не регулируется данным заявлением о конфиденциальности. Вам следует проявлять осторожность и ознакомиться с заявлением о конфиденциальности, применимым к рассматриваемому веб-сайту.
Управление вашей личной информацией
Вы можете ограничить сбор или использование вашей личной информации следующими способами:
- всякий раз, когда вас просят заполнить форму на веб-сайте, найдите поле, которое вы можете щелкнуть, чтобы указать что вы не хотите, чтобы информация использовалась кем-либо в целях прямого маркетинга
- если вы ранее дали нам согласие на использование вашей личной информации в целях прямого маркетинга,
вы можете изменить свое мнение в любое время, написав нам или отправив нам электронное письмо по адресу
info @ plywoodprint.
com
Мы не будем продавать, распространять или передавать вашу личную информацию третьим лицам без вашего разрешения. или требуются по закону. Мы можем использовать вашу личную информацию для отправки вам рекламной информации. о третьих лицах, которые, по нашему мнению, могут вас заинтересовать, если вы сообщите нам, что хотите, чтобы это произошло.
Вы можете запросить подробности личной информации, которую мы храним о вас, в соответствии с Законом о защите данных 1998 года. Будет выплачена небольшая плата.Если вы хотите получить копию имеющейся у вас информации, напишите по адресу .
Если вы считаете, что любая информация о вас, которую мы храним, неверна или неполна, пожалуйста, напишите нам или напишите нам как можно скорее по указанному выше адресу. Мы незамедлительно исправим любую информацию, которая окажется неверной.
Список файлов cookie, которые мы собираем
В таблице ниже перечислены файлы cookie, которые мы собираем, и какую информацию они хранят.
Имя COOKIE | COOKIE Описание |
---|---|
КОРЗИНА | Связь с вашей корзиной покупок. |
CATEGORY_INFO | Сохраняет информацию о категории на странице, что позволяет быстрее отображать страницы. |
СРАВНИТЬ | Элементы, которые у вас есть в списке сравнения продуктов. |
ВАЛЮТА | Ваша предпочтительная валюта |
ЗАКАЗЧИК | Зашифрованная версия вашего идентификатора покупателя в магазине. |
CUSTOMER_AUTH | Индикатор, если вы в данный момент авторизованы в магазине. |
CUSTOMER_INFO | Зашифрованная версия группы клиентов, к которой вы принадлежите. |
CUSTOMER_SEGMENT_IDS | Хранит идентификатор сегмента клиента |
EXTERNAL_NO_CACHE | Флаг, указывающий, отключено ли кеширование.![]() |
ПЕРЕДНИЙ | Ваш ID сеанса на сервере. |
ГОСТЕВОЙ ВИД | Позволяет гостям редактировать свои заказы. |
ПОСЛЕДНЯЯ КАТЕГОРИЯ | Последняя посещенная вами категория. |
ПОСЛЕДНИЙ ПРОДУКТ | Последний просмотренный вами продукт. |
НОВОЕ СООБЩЕНИЕ | Указывает, было ли получено новое сообщение. |
NO_CACHE | Указывает, разрешено ли использование кеша. |
ТОРГОВАЯ КОРЗИНА | Ссылка на информацию о вашей корзине и истории просмотров, если вы просили сайт. |
ОПРОС | ID всех опросов, в которых вы недавно голосовали. |
ОПРОС | Информация о том, по каким опросам вы проголосовали.![]() |