Пресс-формы для ТЭП подошв, Пресс-формы для железо, Xieli Пресс-формы для спортивной обуви
Пресс-формы для ТЭП подошв
Пресс-формы для ТЭП подошв могут быть использованы для производства подошв из пенного и непенного материала. В частности они используются для изготовления любых видов спортивной обуви. В качестве сырья для обуви используется пенный термопластик.
Материал | Железо |
Код ГС | 8480719090 |
Модель | Одноместная |
Оборудование | Пресс-формы для ТЭП подошв прекрасно подойдут для инжекционных литьевых машин, приобретенных на Тайване, в Италии, на материковом Китае и т.д. |
Размер (длинаxширинаxвысота) | (200-400)x(150-240)x(80-220)мм |
Вес | 50-1800кг |
Упаковка | картонная коробка или трехслойная картонная коробка |
Обработка | На станке ЧПУ |
Производственная среда | 100℃-275℃ |
Доставка | картонная коробка или трехслойная картонная коробка |
Срок службы | Более 5 лет |
Особенности
Пресс-формы данной серии отличаются превосходной герметизацией, экономичностью и возможностью осуществляя инжекционного литья на большой скорости. Высокое качество пресс-форм обеспечивает получение обуви без как-либо дефектов.
Преимущества
1. В нашей компании есть 45 станков ЧПУ и 4 офиса для осуществления компьютерного дизайна. Также наша компания обладает 3D-сканером из Германии, машинами для производства цветных трехмерных пресс-форм из США. Наша компания также может осуществлять 3-4-5-х осевое программирование и 3-4-5-х осевое программирование.
2. В нашей компании есть большие демонстрационные залы для образцов – пресс-форм для ТЭП подошв. Образцы взяты нами у клиентов со всего мира, включая материковый Китай. Постоянное изменение моделей позволяет клиентам изготавливать конкурентоспособную продукцию.
4. В нашей компании работают 700 сотрудников. Двухсменный режим работы позволяет выполнять заказы клиентов в полном объеме. Во время работы сотрудникам предоставляется возможность прослушивания ритмичной музыки. Это обеспечивает взаимное понимание и оптимизм среди сотрудников.
Компания XIELI – это профессиональный производитель и поставщик пресс-форм для ТЭП подошв в Китае. Наша компания рада предложить Вам широкий ассортимент продукции, включая: пресс-формы для резиновых подошв, пресс-формы для прозрачной обуви, инжекционные пресс-формы для обуви из ЭВА, пресс-формы для воздухопроницаемой обуви из ПВХ и т.д.
Информация, связанная с данным продуктом
Пресс-формы для ТЭП подошв
shoe-mould.ru
Пресс форма для производства подошв из резины
- Пресс форма для одноцветной резиновой подошвыДанная пресс форма используется для производства одноцветной подошвы и всякого рода резиновых аксессуаров к подошвам. Пресс форма для производства одноцветных подошв для кроссовок и ботинок является наиболее часто используемой пресс формой из-за низкой стоимости и износостойкости резины. Будучи сделанной из …
- Пресс форма для двухцветной подошвыПресс форма для производства двухцветной резиновой подошвы используется для производства подошв и аксессуаров к ним. Оно является частью оборудования для производства обуви. Подошва, сделанная с помощью данного оборудования, характеризуется износостойкостью, долговечностью и низкой стоимостью. …
Вступление
Данная пресс форма используется для производства резиновых подошв и аксессуаров к ним. Ооборудование для производства подошв из резины используется совместно с оборудованием для производства обуви. На выбор клиентов мы предлагаем пресс форму для одно- и двухветных изделий из резины. Благодаря тому, что оборудование сделано из алюминия и железа, оно не изменяет своих форм, т.е. не деформируется даже при 400 ℃ . Во время процесса производства, расплавленная резина подается в пресс формы, где и получает желаемую форму. Резиновые подошвы, которые сделаны с помощью данных пресс форм обладают износостойкостью и выгодны в использовании.
1. Сначала разрабатывается технологическая схема процесса. Потом происходит реализация дизайна с помощью CAD, NC. На третьем этапе происходит разработка пресс формы и ее усовершенствование до получения нужных параметров.
2. После перечисленных выше процессов следует процесс формировки пресс форм вместе с декоративными узорами подошв. Испытания пресс форм для производства резиновых подошв на оборудовании для производства подошв. И лишь после этого, пресс формы, которые успешно прошли все испытания, попадают в продажу.
Особенности
Они состоят из верхней, средней и нижней пресс формы… В процессе производства подошвы, расплавленная резина подается в закрытую пресс форму, где она приобретает необходимую форму. Верхняя часть пресс формы отвечает за формовку внутренних поверхностей изделия, а нижняя – за наружные детали, тогда как средняя заготовка отвечает за пропорциональность наружных и внутренних размеров.
Преимущества
1. Материалом для производства пресс форм для резиновых подошв является алюминиевый сплав от известного производителя алюминия в провинции Гуандонг. Подошвы для обуви характеризуются высоким качеством за счет того, что наши пресс формы сделаны с алюминиевого сплава высокого качества.
2. Чтобы следовать последним технологиям и моде, в нашей компании имеется профессиональный исследовательно-проектировочный отдел. Обладая более 10 годами опыта изготовления пресс форм для производства подошв, мы успешно продаем данное оборудование как в Китае так и за границу. К тому же, наша продукция высоко оценена клиентами.
3. Качество и функциональность пресс форм для производства резиновой обуви проверяется более 4 раз, что делает наши пресс формы надежными при производстве обуви.
4. У нас есть сервис-центры по всему миру. Гарантийное обслуживание включает в себя техобслуживание, ремонт и технологическое консультирование.
На что надо обратить внимание при покупке
(1) Определитесь с применением пресс форм для производства резиновой обуви. Резина является износостойким материалом, именно поэтому, с помощью данного оборудования можно получить высококачественные подошвы для сапог и первоклассные кроссовки.
(2) Срок службы пресс формы ( >5 лет)
(3) Правильно выберите размеры пресс формы
Техобслуживание и ремонт
1. Очищайте оставшиеся частицы материала с помощью медных веничков и специальных щеток (не разрешается использовать твердые материалы, например металлические прутки и провода) по окончанию производства подошвы. Потом необходимо осушить пресс форму с помощью воздуходувки. Ржавую поверхность необходимо зачистить и покрыть слоем защищающего от ржи масла. И напоследок, необходимо поместить пресс форму в сухое, не пыльное, без прямого попадания солнечных лучей прохладное помещение.
Аутентификация
Пресс формы для производства резиновых подошв прошли сертификацию ISO
Оплата и доставка
Деревянные пресс формы поставляются в течении 20 дней с момента заказа. Груз покрывается картоном либо трехслойной деревянной упаковкой.
Компания Jili специализируется на производстве оборудования для изготовления обуви, вспомогательного оборудования и пресс форм для обуви. Пройдя многочисленные проверки качества, наша продукция характеризуется высоким качеством. Например, пресс форма для производства резиновой обуви стойка к деформациям даже при температуре 400 ℃.
jicmachine.ru
Подошва для обуви, из чего производится, характеристики сырья
Обувь является неотъемлемой частью гардероба, влияющей на внешний вид людей и комфортность их пребывания в разной обстановке. Во многом удобство, долговечность, практичность этого элемента гардероба определяет подошва для обуви — именно эта часть изделий подвергается самым сильным механическим воздействиям, она контактирует с водой, солью, химическими реагентами, присутствующими на земле. Именно поэтому для ее изготовления используются наиболее прочные, надежные, устойчивые к влиянию окружающей среды материалы.
Базовые требования
В производстве используется как проверенное прошлым, так современное сырье, изготавливаемое по новым технологиям. Каждое из них имеет свои особенности, определяемые составом ингредиентов, назначением готовых изделий.
Материал подошвы обуви должен соответствовать следующим требованиям:
- Прочность. Должен выдерживать сильное вертикальное давление и постоянные удары, неизбежные в процессе ходьбы.
- Износостойкость. Трение является одним из факторов, приводящих к преждевременному разрушению подметки.
- Гибкость, упругость. Это свойство обеспечивает удобство передвижения, возвращая верх обуви в исходное состояние.
- Мягкость. Качественные подошвы для обуви обеспечивают комфортное состояние ступни, смягчая удары от неровностей грунта или резких движений.
- Теплопроводность. Данное качество важно для зимней обуви, в которой необходима изоляция ноги от холода.
При приобретении ботинок, туфель, кроссовок следует интересоваться, из чего изготовлено основание товара. Это позволит сделать правильный выбор, обеспечивающий комфорт передвижения в любых погодных условиях.
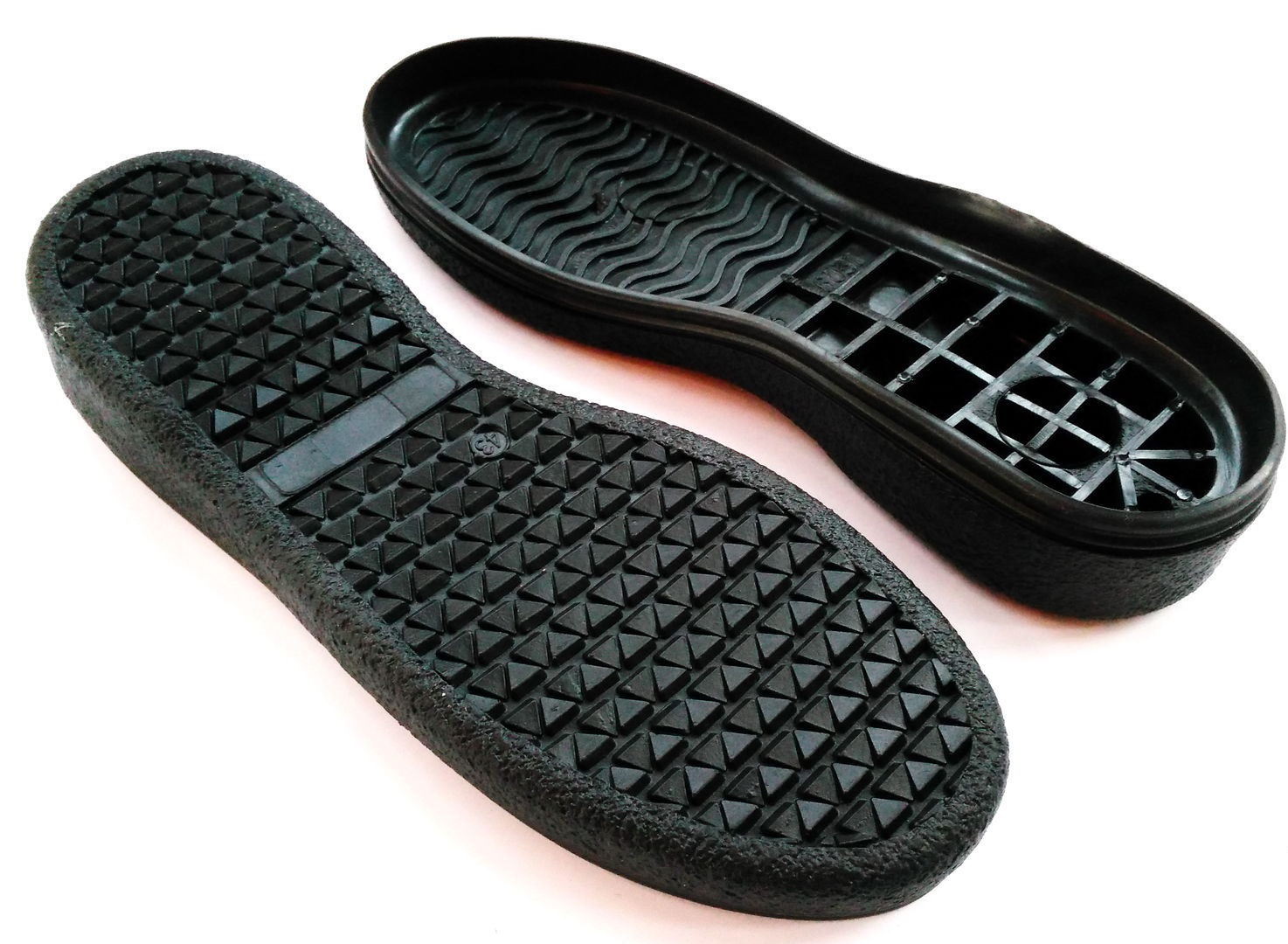
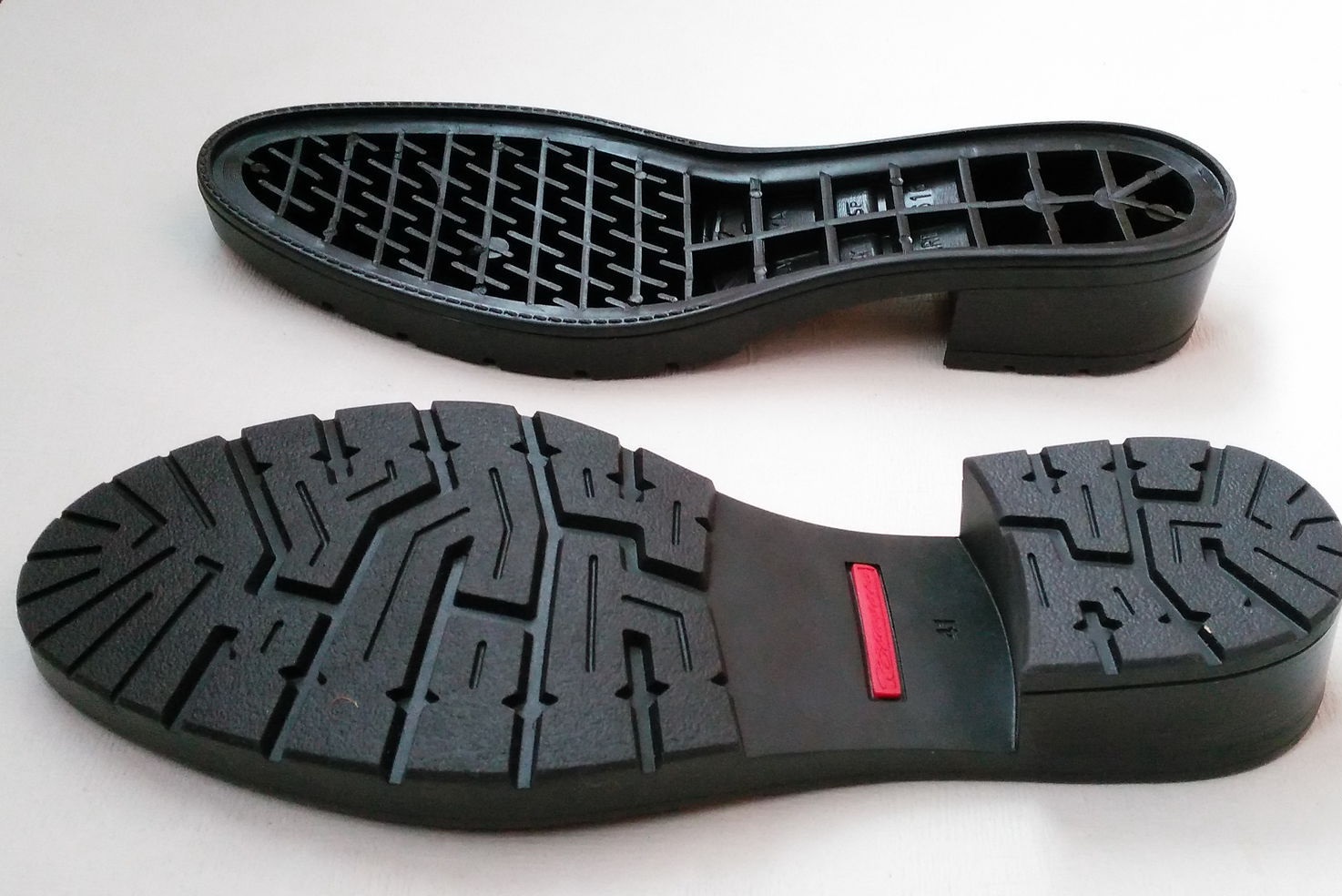
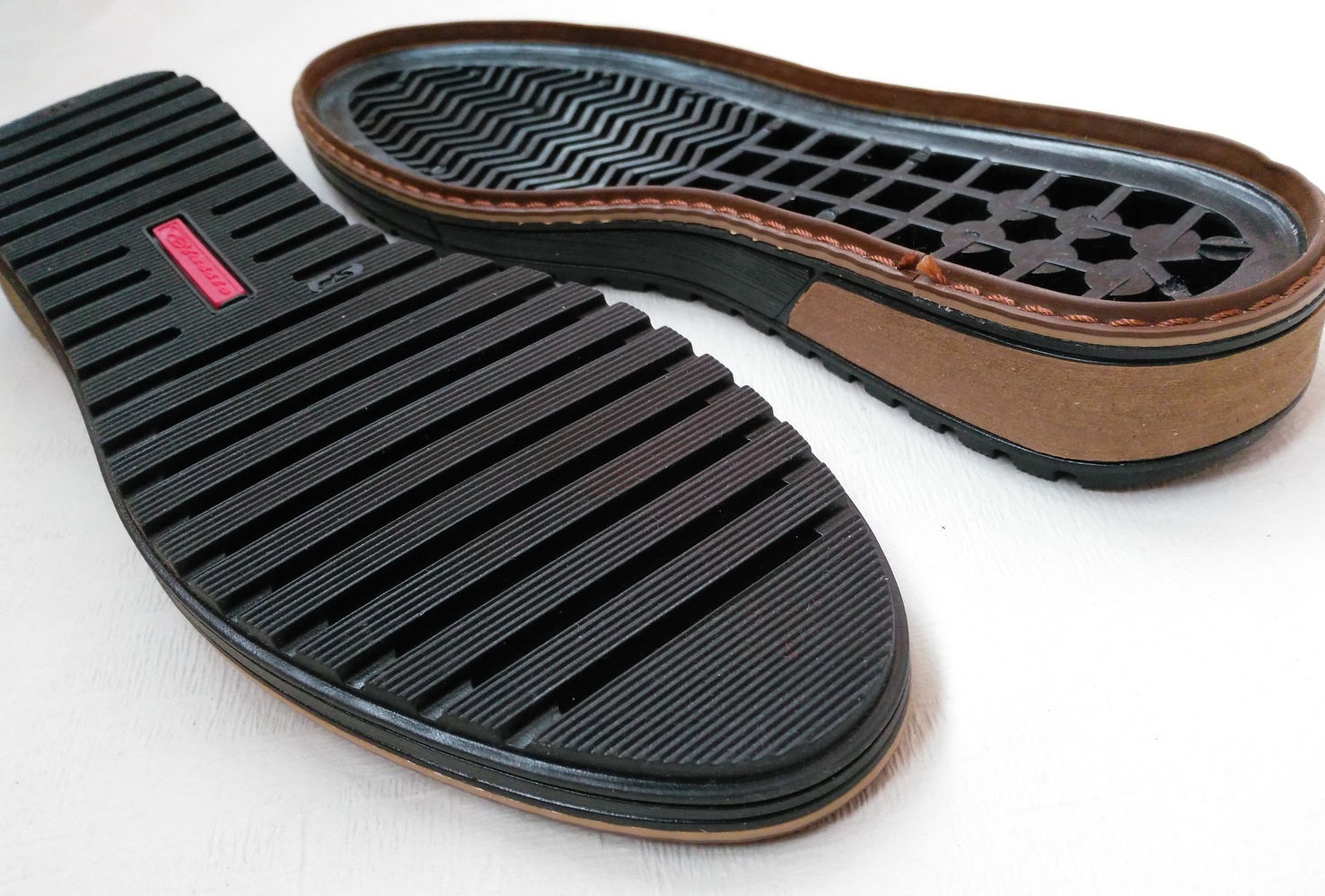
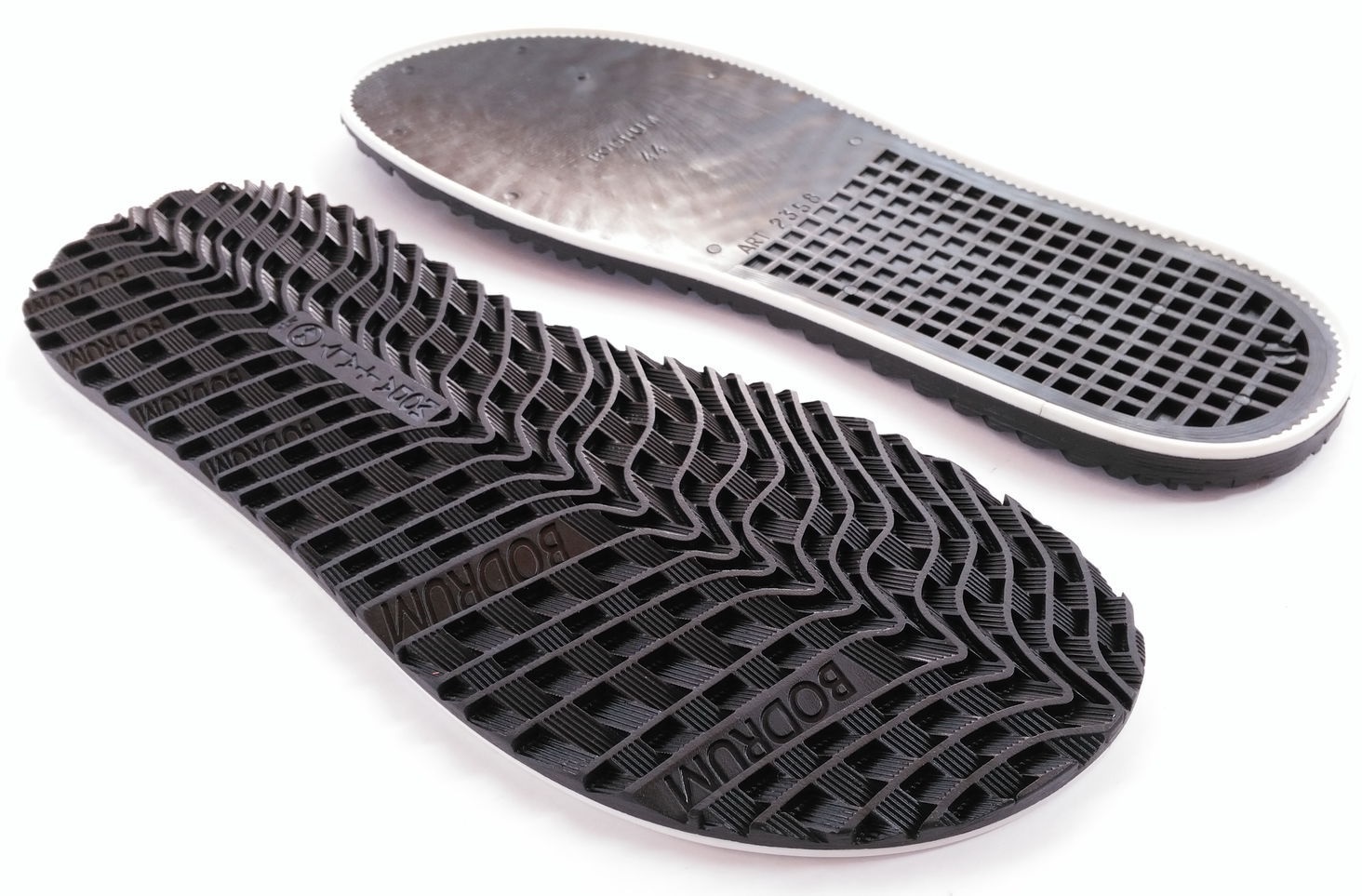
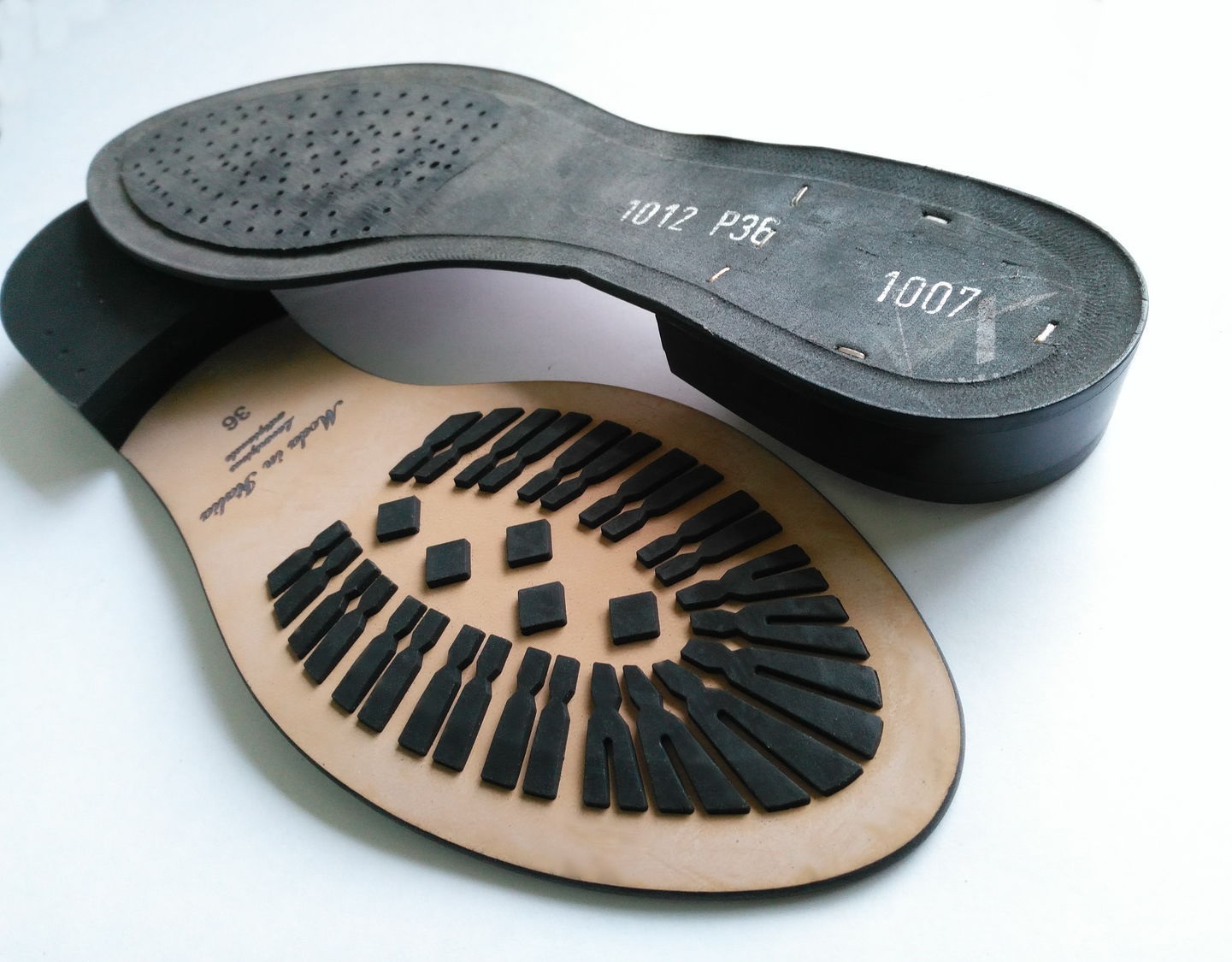
Материалы изготовления с учетом моделей
В процессе разработки, производства применяется такой материал подошвы обуви, который максимально соответствует ее назначению, дизайну.
Современная промышленность использует следующие виды сырья:
- Полиуретан. Представляет собой вспененную массу черного цвета. Отличается низкой теплопроводностью, мягкостью, небольшим весом. Недостаток заключается в плохой прочности, быстром истирании.
- Термопластичный полиуретан. Материал получают путем формовочного литья под давлением. Такие обувные подошвы обладают плотностью, износостойкостью, презентабельным внешним видом. Минус — низкие теплоизоляционные качества.
- Комбинированный полиуретан. Подметки состоят из двух слоев, благодаря чему достигается плотность, устойчивость к истиранию, защита от холода. Недостаток в том, что оба слоя могут расклеиться.
- Термоэластопласт. Материал пористый, легкий, эффективно защищает ноги от холода. Несмотря на небольшую плотность, подошвы из ТЭП хорошо выдерживают трение, имеют долгий срок службы. Минус в том, что невозможно придать основе четкие ровные очертания.
- Поливинилхлорид. Материал плотный, тяжелый. Может быть окрашен в любой цвет в процессе производства. Отличается надежностью, добротностью. Недостаток — большой удельный вес.
- Этиленвинилацетат. Представляет собой вулканизированную пену, обладает отличной гибкостью, мягкостью, упругостью. Минусы — неустойчивость к низким температурам, постепенное уменьшение объема под давлением.
- Синтетический каучук. Материал отвечает всем требованиям, которые предъявляются к качественной обуви. Недостаток в дороговизне сырья и высокой стоимости изготовления.
- Тунит (кожволон). Является композитом из резины, натуральной кожи. За счет этого осуществляется вентиляция основания. Минусов у искусственной кожи много — она тяжелая, твердая, быстро стирается.
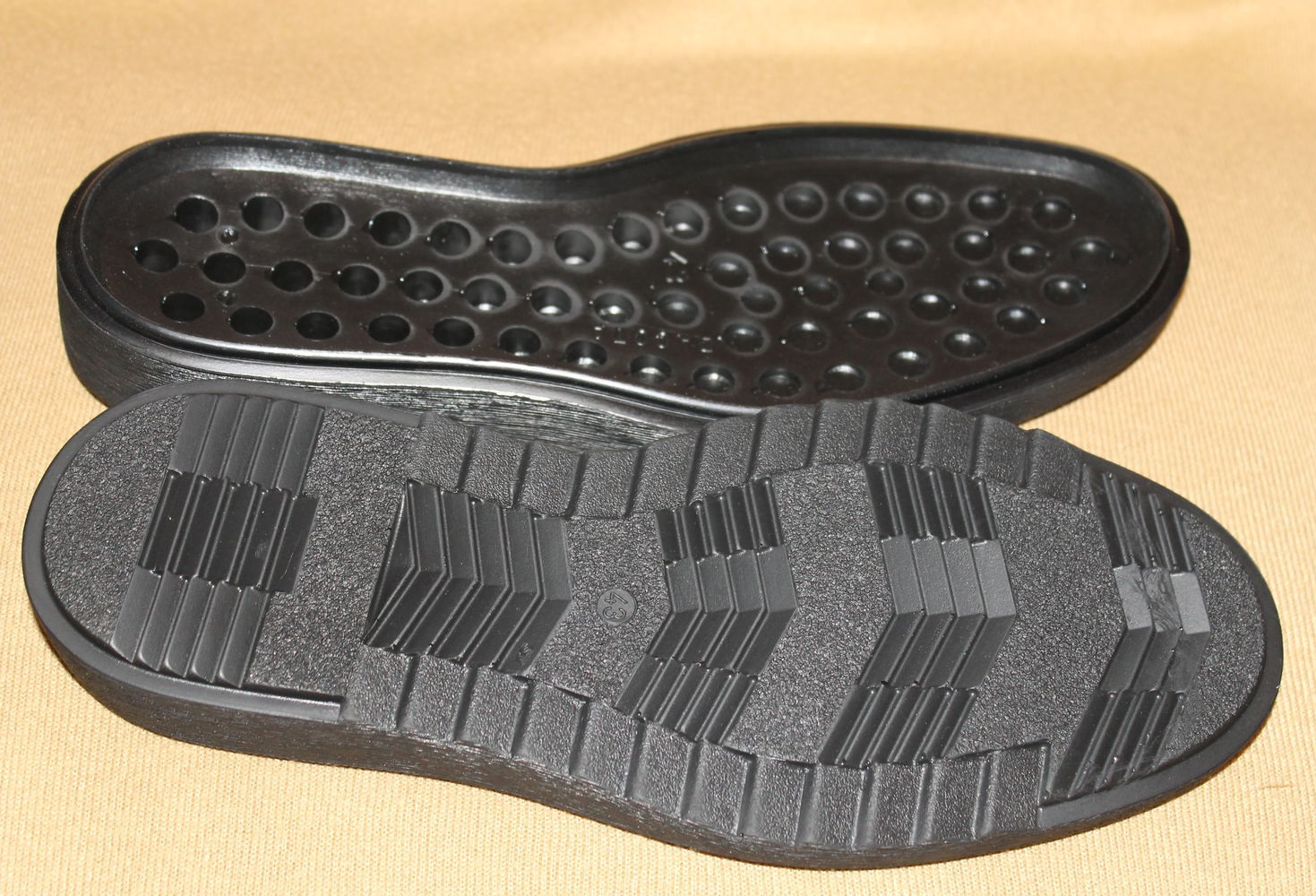
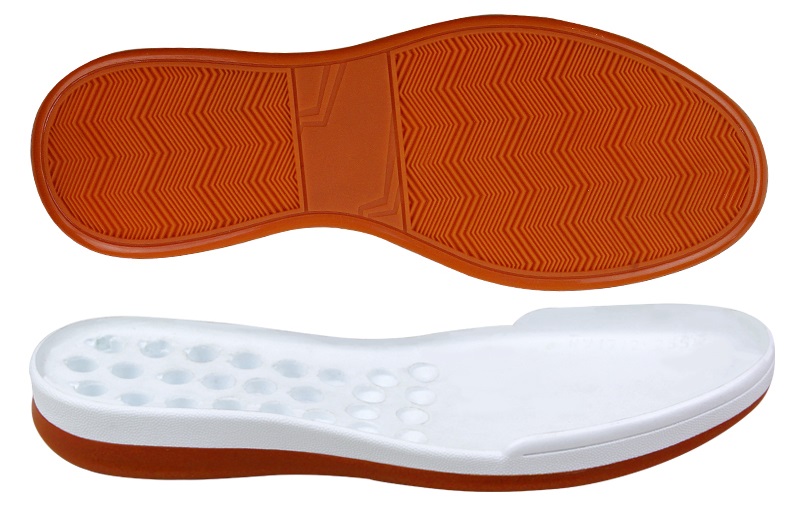
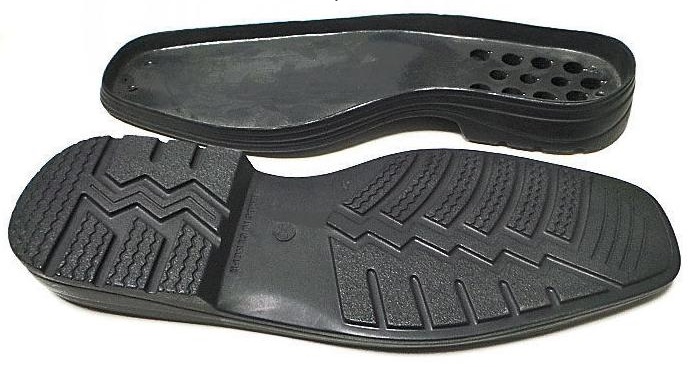
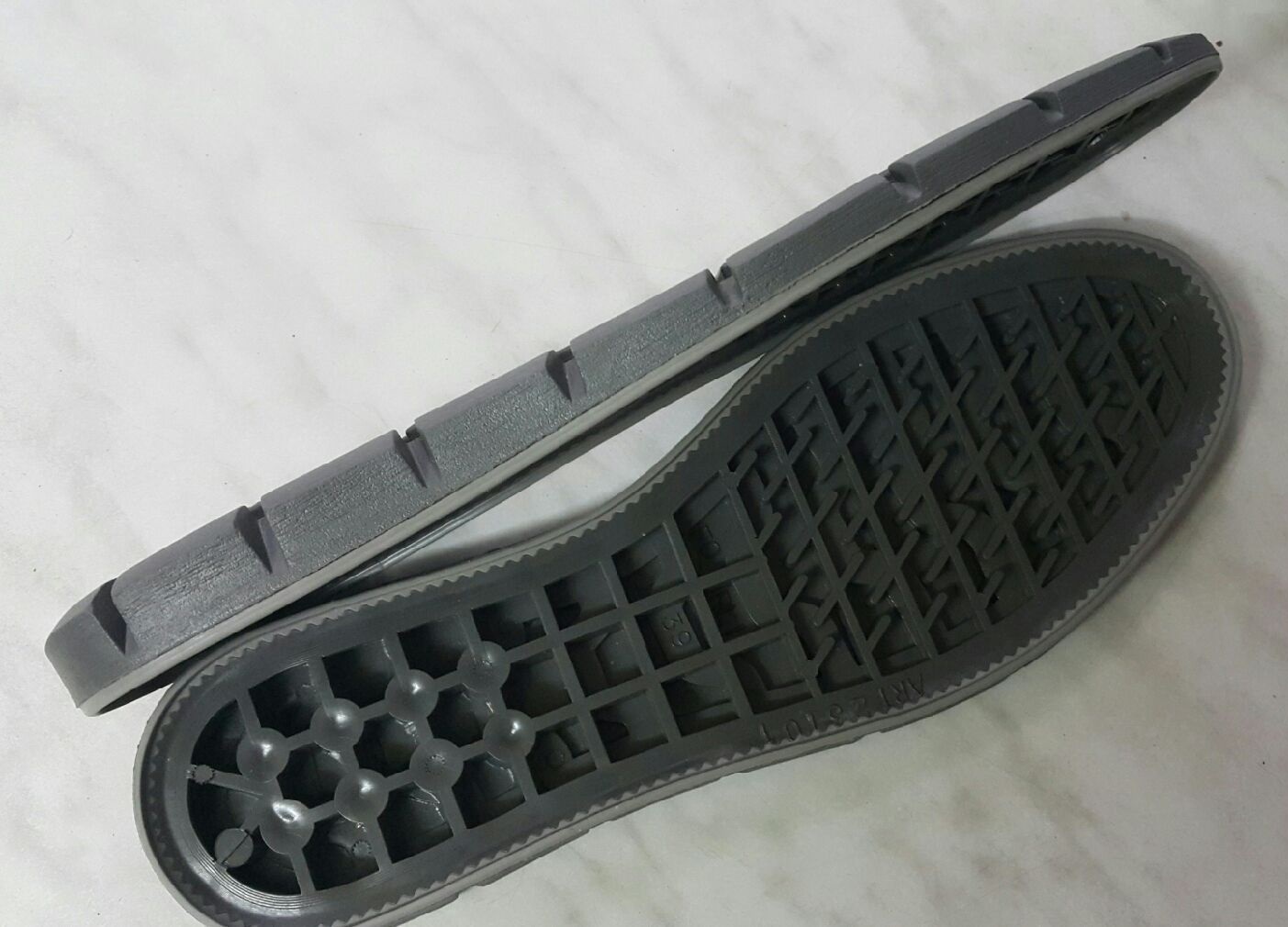
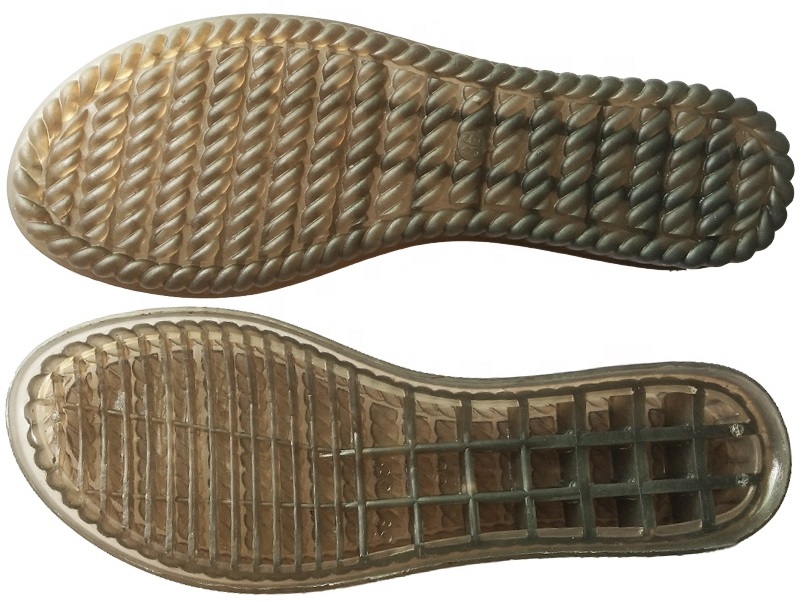
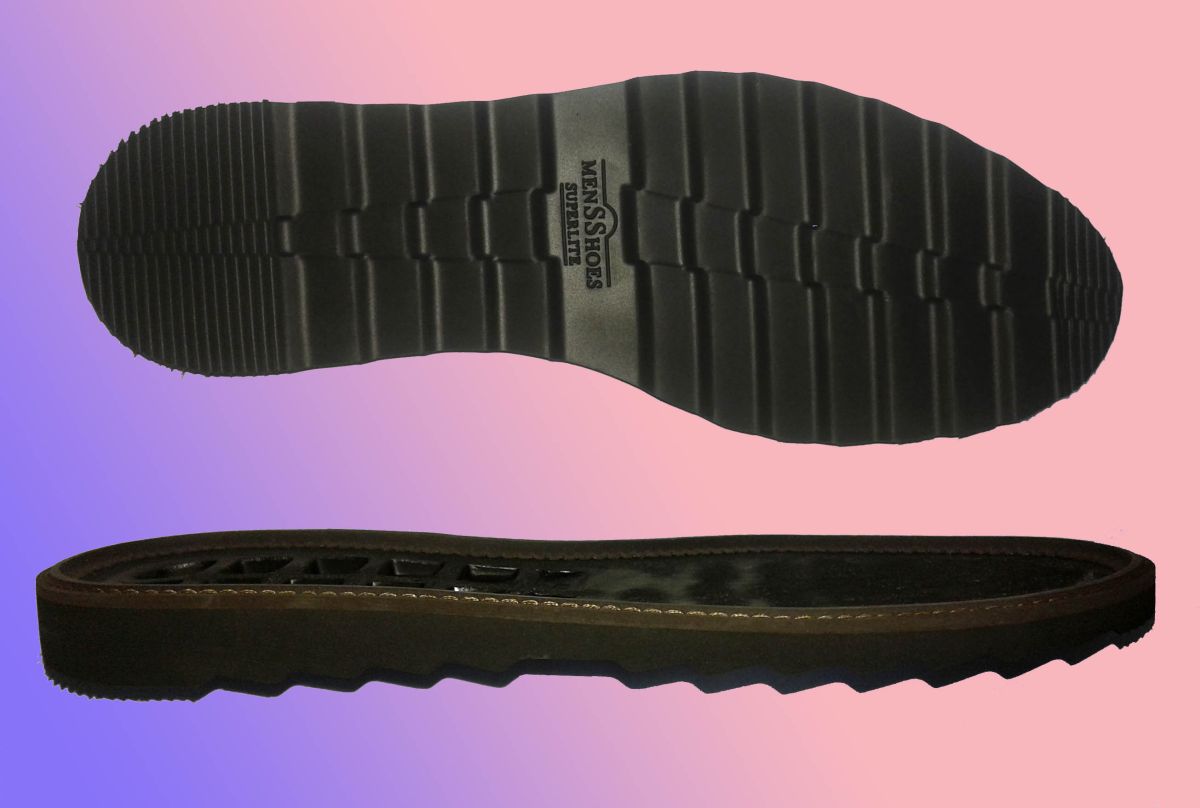
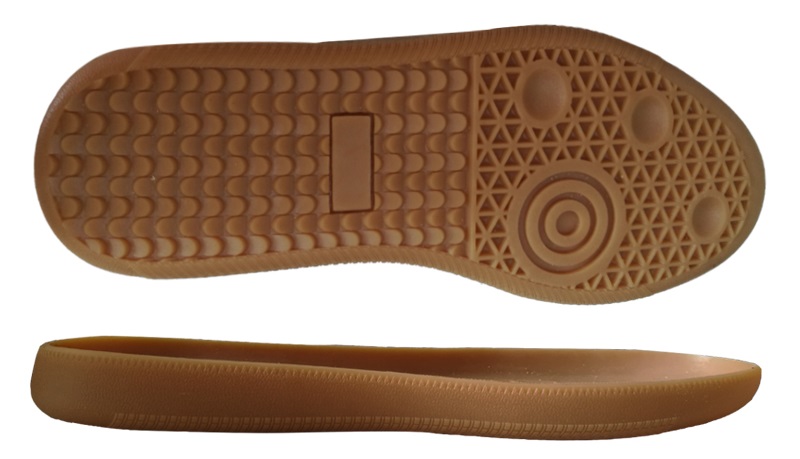
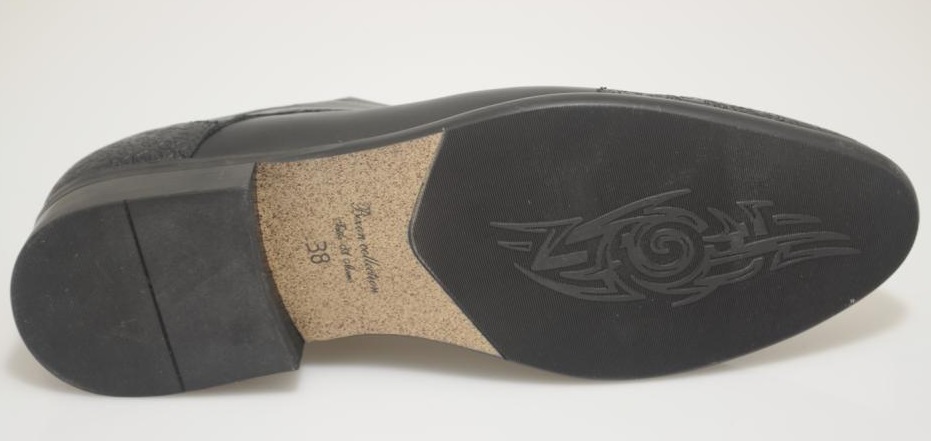
Модельная обувь
Изделия модельного ряда отличаются четкостью линий, изящностью, привлекательностью. Износостойкость здесь стоит не на первом месте. Такую обувь не носят в грязь, снег, дождь. Для изготовления модельной женской обуви лучше подходит кожа или термополиуретан. Материалы прочные, им легко придать заданную форму.
В производстве презентабельных мужских ботинок, подошва которых должна выглядеть аккуратно и изящно, используется синтетический каучук или тунит. Материал обладает прочностью, точностью граней, подметка изготавливается так, как задумал модельер.
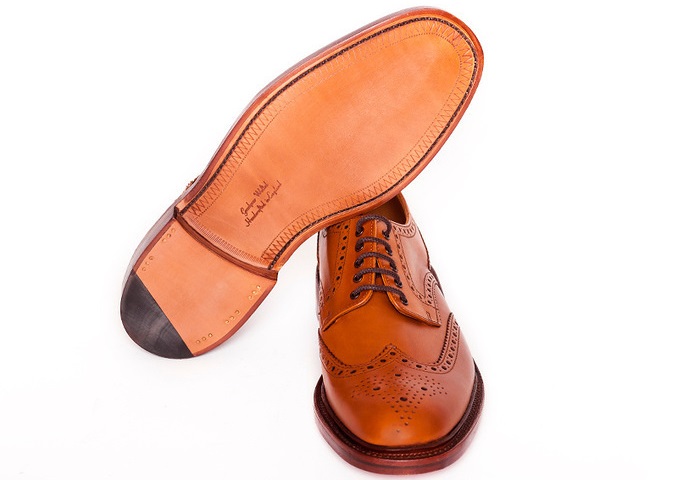
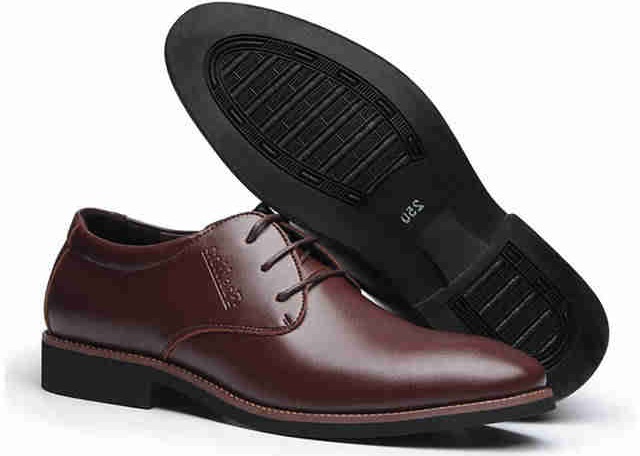
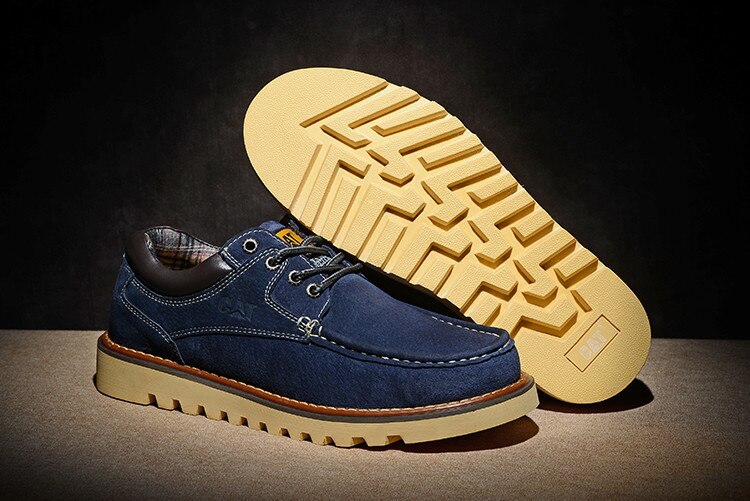
Спортивные и треккинговые модели
Для занятий физкультурой и спортом нужна удобная, легкая, эластичная обувь. При этом она должна обладать хорошими вентиляционными качествами. Все это есть у этиленвинилацетата и синтетического каучука. Материалы упругие, имеющие низкий удельный вес, прочность. Их используют для изготовления подошв кроссовок, кед, военной обуви.
При больших спортивных нагрузках обувь нужно менять каждые 2–3 года. Для ценителей комфорта эти затраты не покажутся обременительными.
Изделия для трекинга отличаются прочностью, надежностью и увеличенной толщиной, так как должны защитить стопу от высоких нагрузок и обеспечить безопасность в походах, на склонах. Треккинговые подошвы состоят из жесткой подметки (ТПУ со стеклянной крошкой), виброгасящего слоя (ПУ) и торсионного элемента (сталь, пластик).
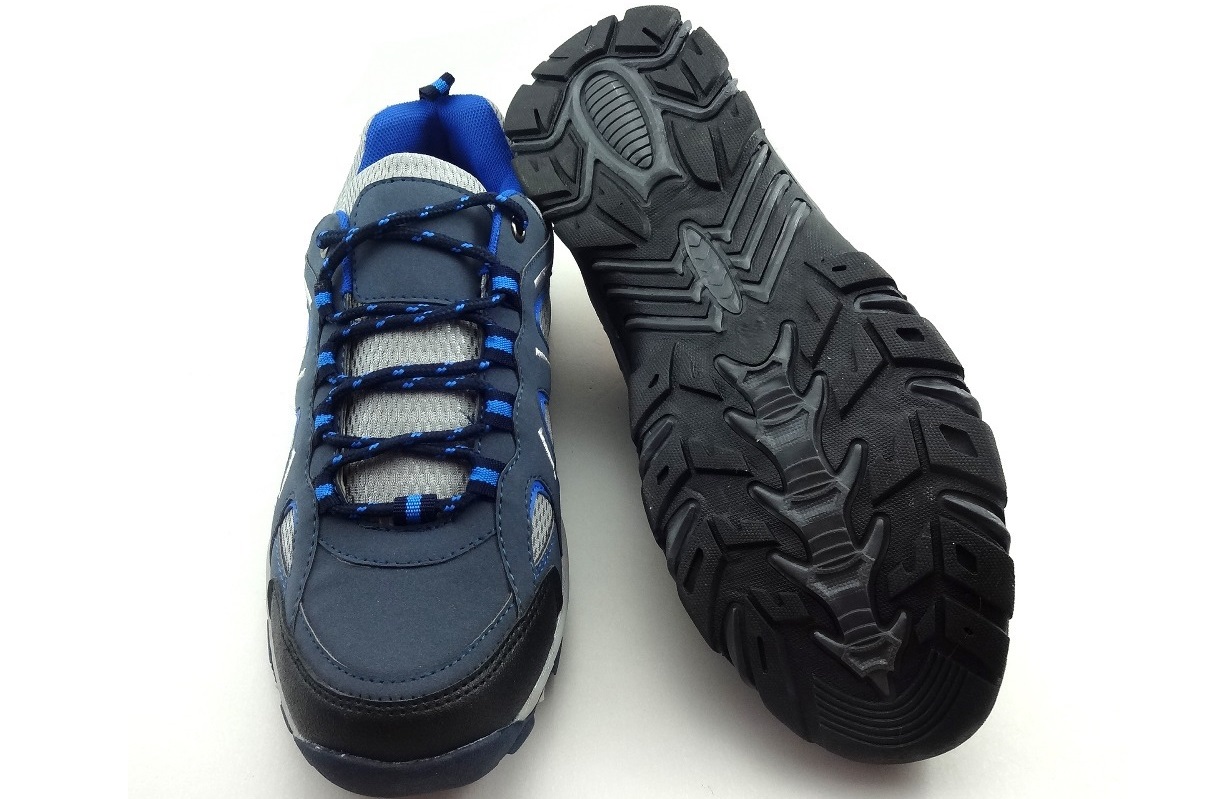
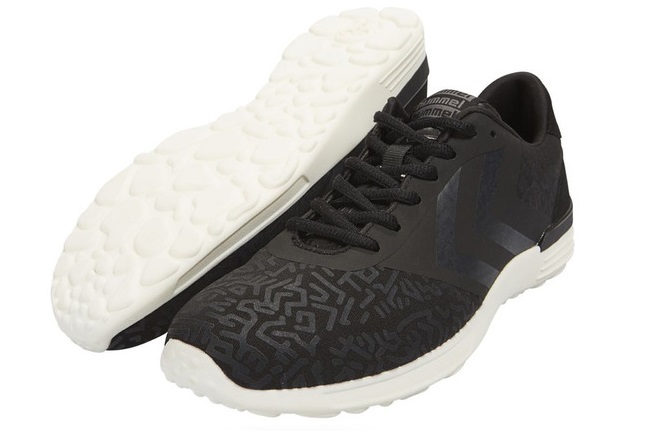
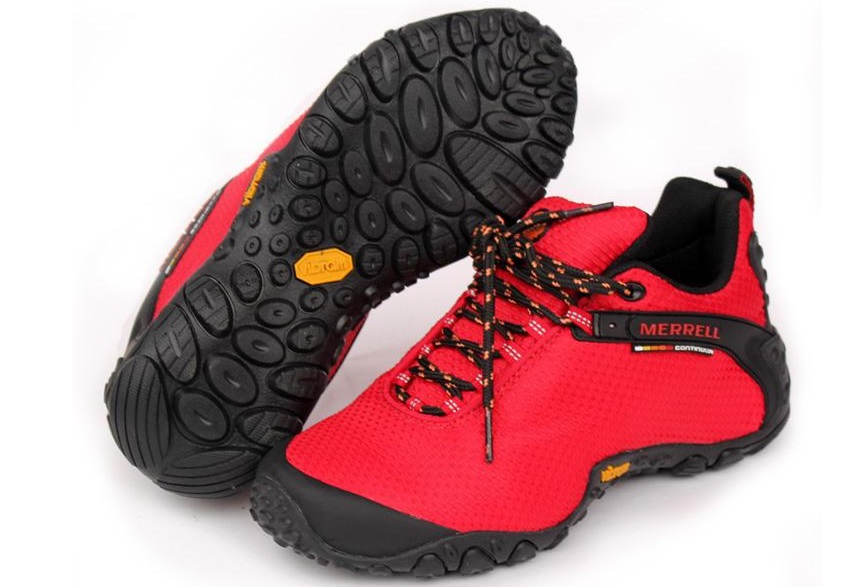
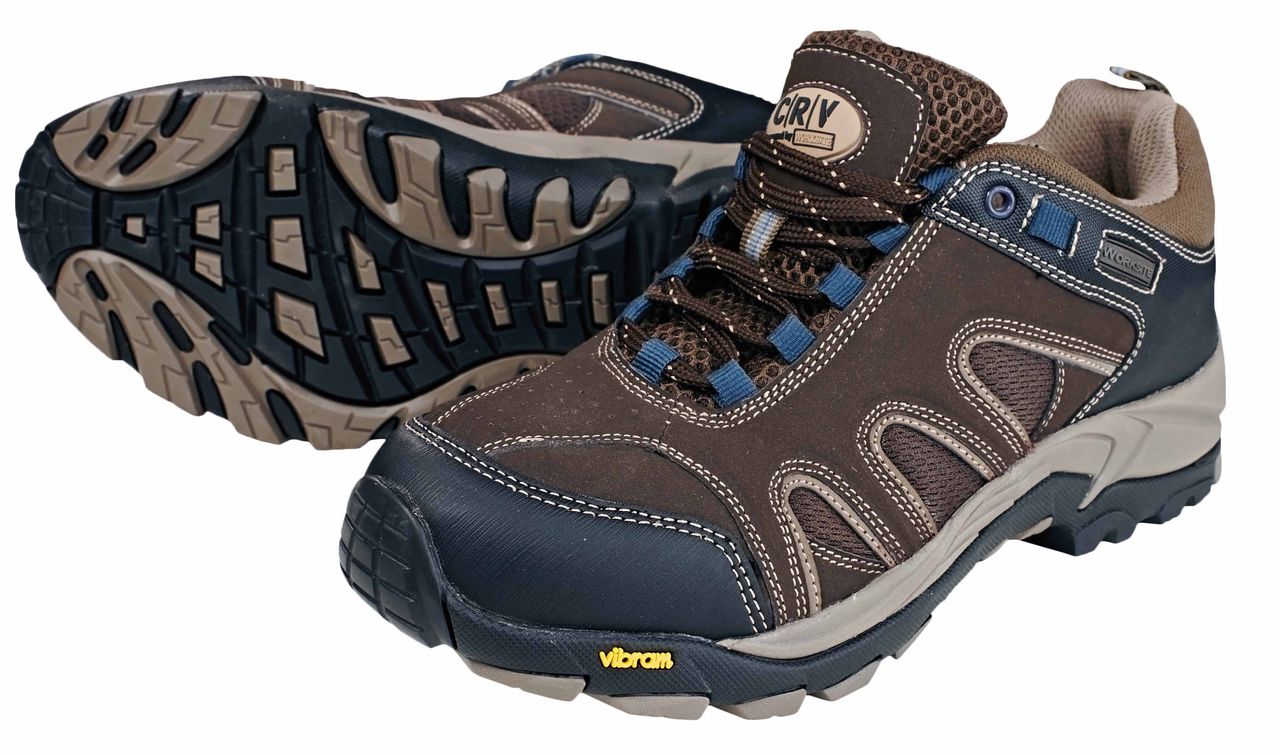
Сапоги
Как женские, так и мужские сапоги используются в межсезонье, зимой. Подошва подбирается под условия эксплуатации. Основание должно быть толстым, водонепроницаемым, устойчивым к низким температурам.
Для изготовления используется комбинация из мягкой микропоры сверху и жесткой снизу. Такое сочетание позволяет достичь хорошей износостойкости и теплоизоляции одновременно. Хорошо зарекомендовали себя термоэластопласт, ТПУ, синтетический каучук, поливинилхлорид. Материалы обладают всеми необходимыми для комфортного ношения обуви характеристиками.
Следует избегать обуви, подошва которой изготовлена из полиуретана. При низких температурах полимер становится твердым, теряет гибкость, трескается, рассыпается. При этом речи о каких-либо изоляционных качествах идти не может.
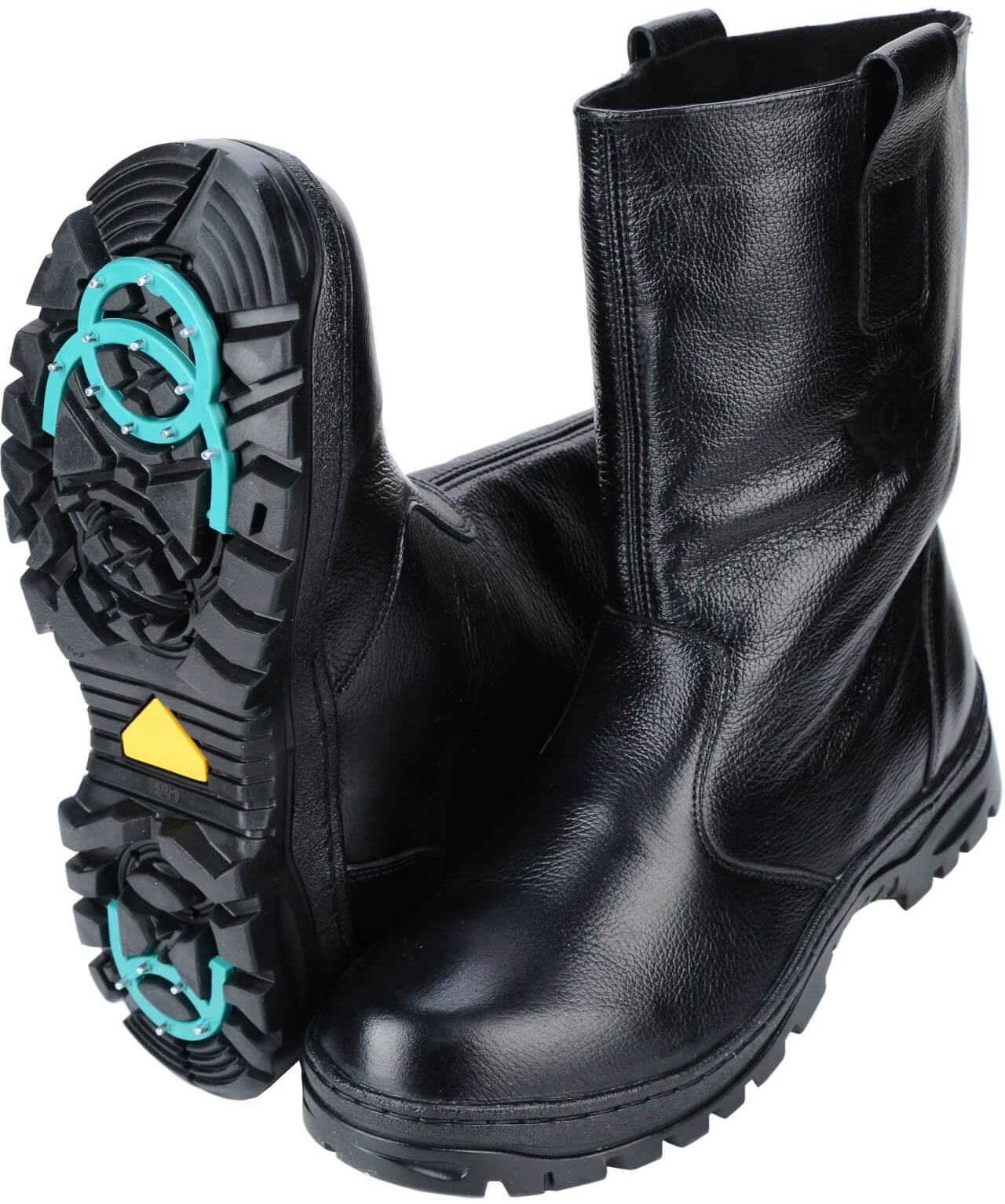
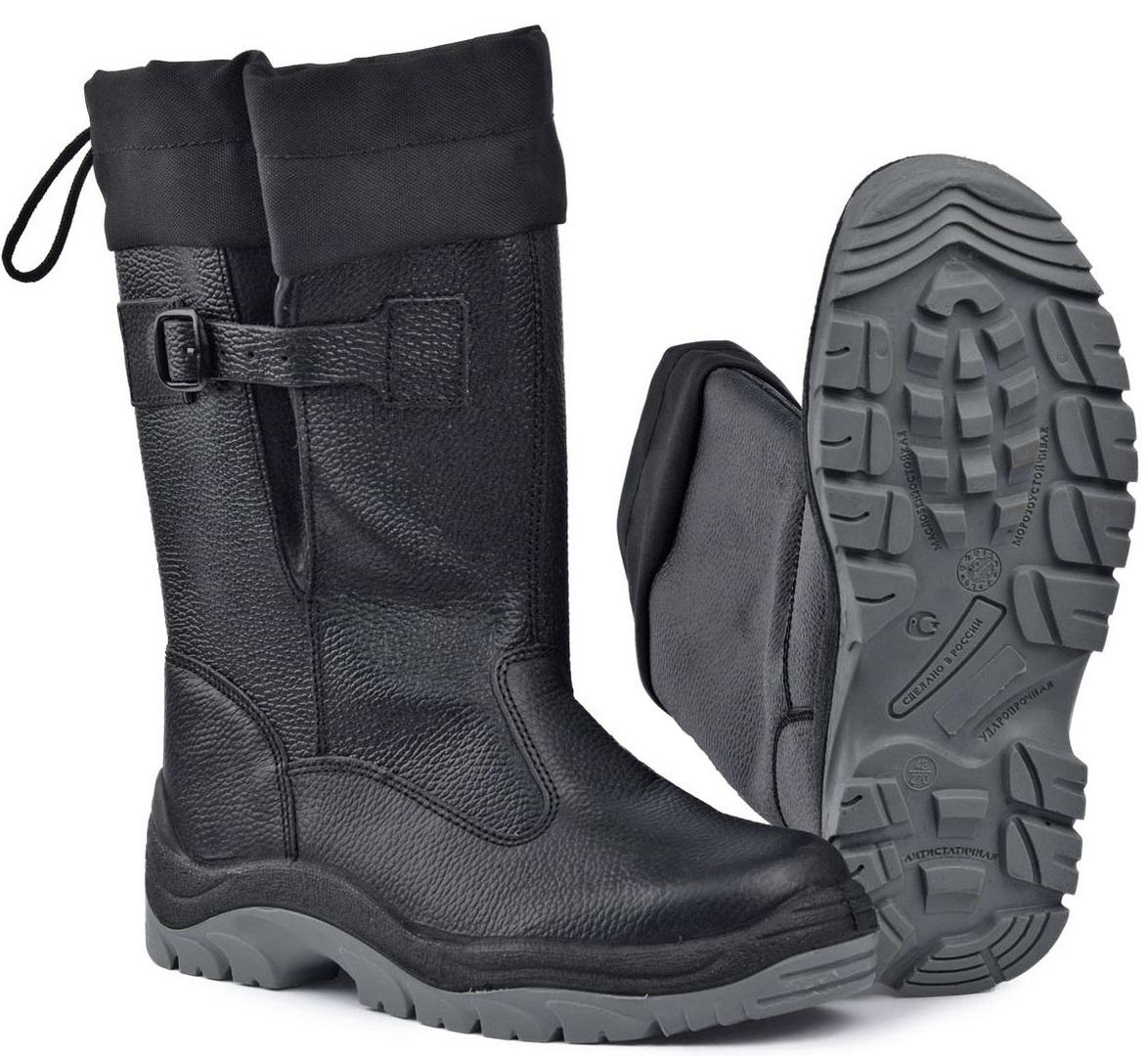
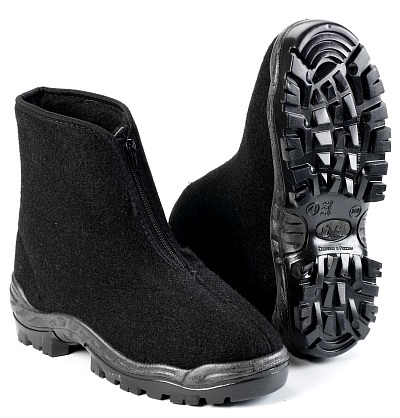
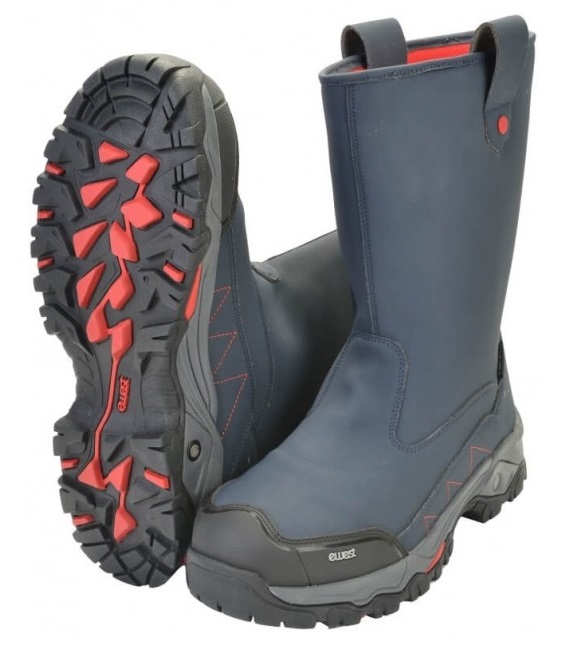
Ботинки
В зависимости от модели ботинок, для них применяется подошва из искусственной кожи, термопластичного полиуретана или поливинилхлорида.
Для летних моделей применяется устойчивый к истиранию материал – это тунит, искусственный каучук. Сырье не изнашивается от хождения по асфальту и бетону, хорошо смотрится благодаря аккуратности граней.
Хорошее сырье для изготовления подошвы обуви — термоэластопласт, комбинированный полиуретан. Эти материалы надежно защитят ноги от холода и сырости.
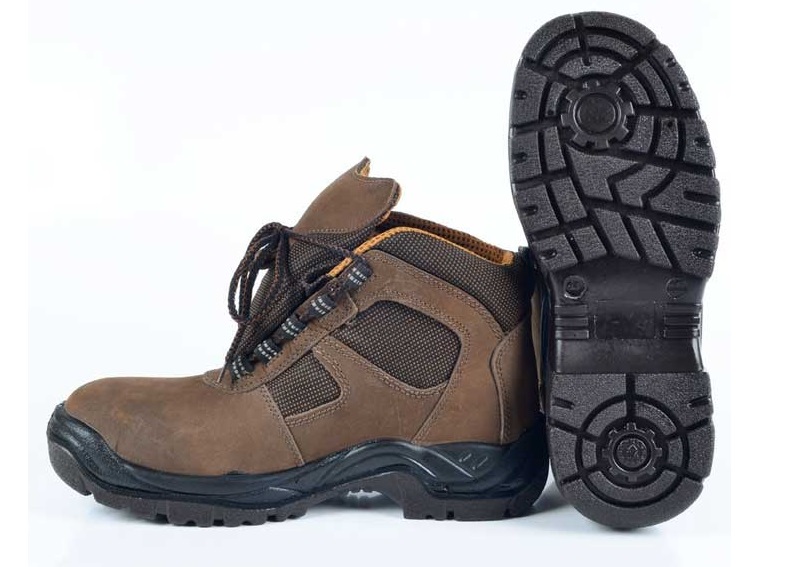
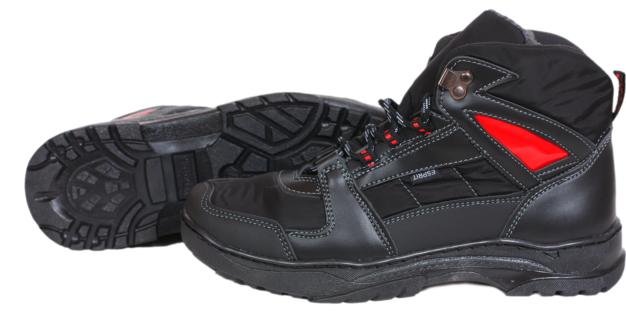
Летние босоножки и сандалии
К летним босоножкам, сандалиям предъявляется требование устойчивости к высоким температурам. При их воздействии многие виды материалов меняют свои качества, становятся мягкими, теряют прочность. Если при изготовлении обуви использовался клей, то он может потечь, что приводит к отслоению пластов и разрушению изделий.
Следует выбирать летнюю обувь, для изготовления подошвы которой используется этиленвинилацетат, поливинилхлорид, искусственная кожа. Эти вещества без проблем переносят жару, трение, механическое воздействие. Кроме этого, ношение такой обуви не сопровождается негативными ощущениями. Материал легкий, прочный, приятный на ощупь.
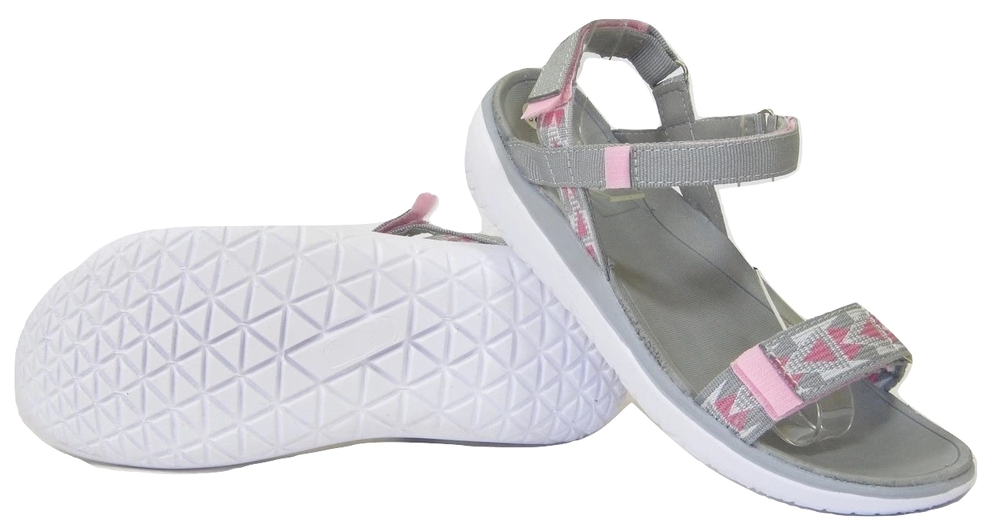
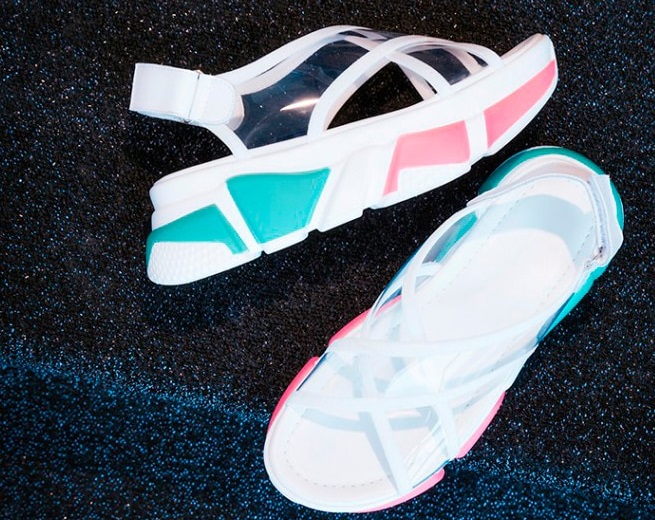
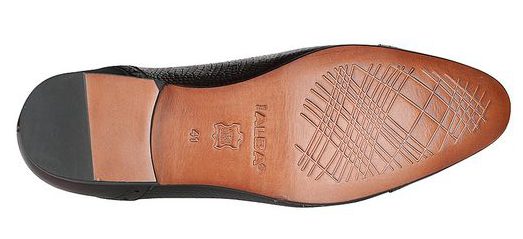
Повседневные модели
К повседневным моделям не предъявляются повышенные требования в отношении элегантности, изящности, презентабельности. На первом плане находится удобство, практичность, долговечность. При этом изделия должны выглядеть достаточно прилично, чтобы в них была возможность ходить на работу и посещать другие общественные места.
Выбирать рабочую обувь лучше с подошвами, сделанными из термопластичной резины, термоэластопласта, поливинилхлорида. Эти материалы устойчивы ко всем видам воздействия окружающей среды.
Следует избегать выбора изделий с основанием из искусственной кожи, этиленвинилацетата. Данные вещества не выдерживают длительной нагрузки, быстро истираются и теряют свою исходную форму.
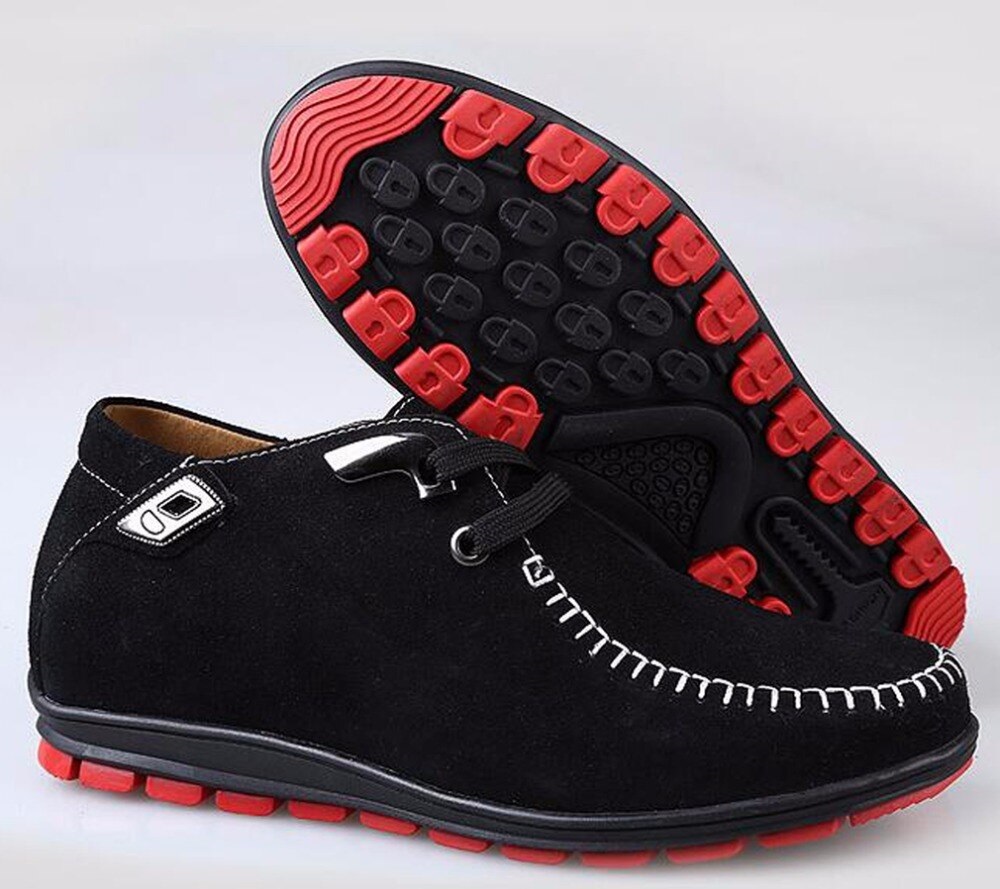
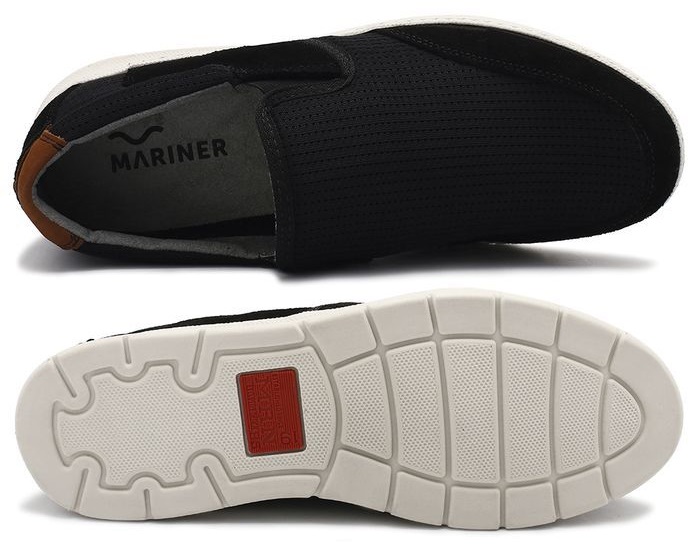
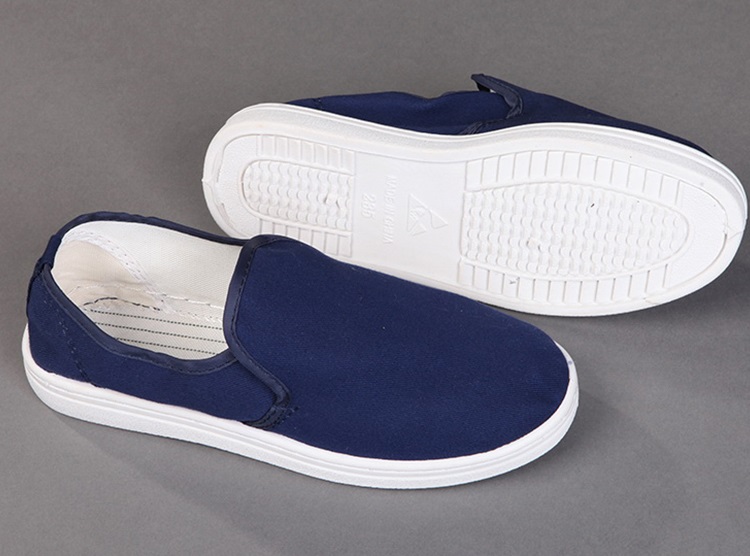
Способ крепления подошвы
Современная промышленность использует несколько способов крепления верха обуви с подошвой. Выбор основывается на назначении изделия, типе модели и стиле обуви.
Соединение деталей осуществляется такими методами:
- Прошивной. Применяется при изготовлении повседневной и модельной обуви. Представляет собой соединение верха и основания с помощью прочной синтетической нити. Такой вариант считается презентабельным и достаточно прочным. На начальном сроке ношения так оно и есть. Но со временем происходит постепенное истирание прошивочного материала, прочность ухудшается. Другой минус технологии – пропускание воды через отверстия. Сегодня производители отказываются от данного способа крепления.
- Литьевой. Создает полностью герметичное соединение между верхом и подметкой. Кожаная или синтетическая верхняя часть опускается в форму подошвы, в которую заливается расплавленный материал. После остывания подошва становится единым целым с заготовкой. Плюс такого метода в его прочности и надежности. Недостаток заключается в том, что основание имеет слабую адгезию с качественной кожей, обладающей низкой пористостью.
- Клеевой. Наиболее распространенный способ по причине дешевизны, простоты, надежности. Готовые изделия отличаются прочностью, износостойкостью, герметичностью. Минус заключается в сложности подбора клея для подошвы, так как для разных моделей используются составы, устойчивые к различной температуре.
Качество крепления основания и верха зависит не только от применяемого метода, но и от соблюдения технологии производства.
Выбор в зависимости от сезона
От правильности выбора материала, из которого изготовлено основание обуви, зависит удобство ее ношения, самочувствие и даже состояние здоровья человека. Необходимо учитывать все параметры материалов, чтобы обезопасить себя от неприятностей и тем более болезней в области ступней. Для каждого сезона установлены свои критерии условий эксплуатации подошвы.
Лето
Данное время года характеризуется как сильной жарой в солнечные дни, так влажностью во время осадков. Необходимо быть готовыми к любым капризам погоды. Для теплого времени лучше выбрать обувь с основанием из термополиуретана и поливинилхлорида. Материалы сохраняют свои характеристики даже при экстремально высокой температуре.
Летом следует воздерживаться от изделий с подметками из термоэластопласта, который просто плавится при нагревании.
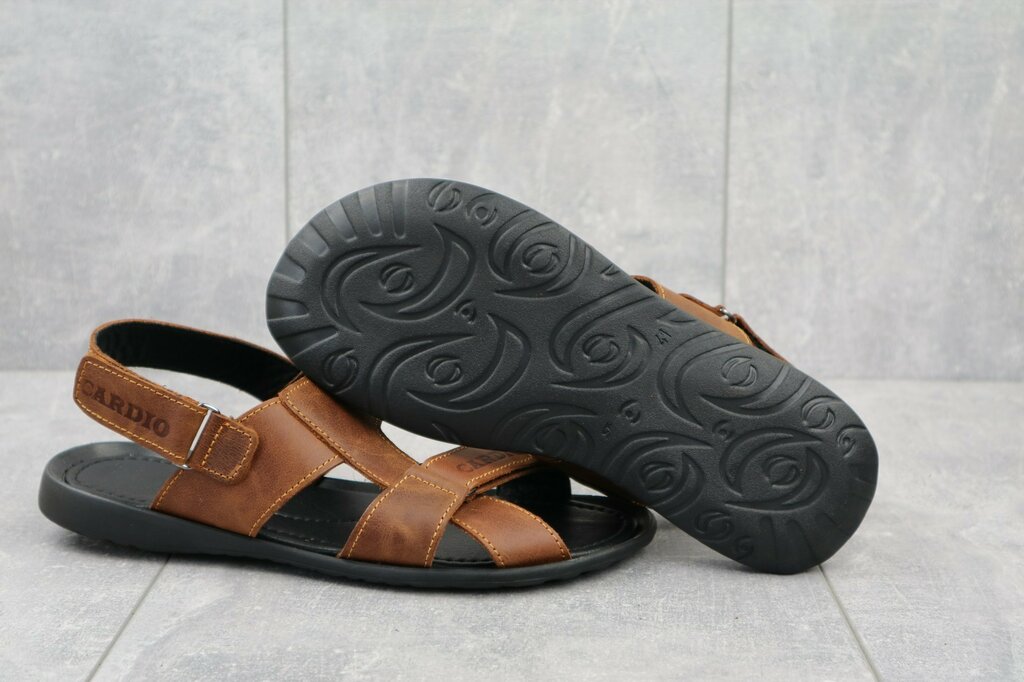
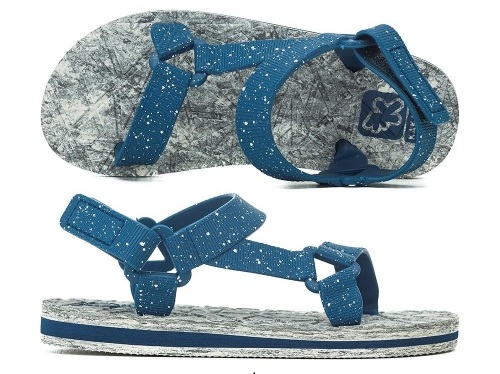
Весна-осень
Межсезонье, несмотря на непредсказуемость погоды, характеризуется наиболее оптимальными условиями для всех типов подошв. Температура держится в пределах, при которых сохраняются рабочие параметры всех материалов. Что касается водонепроницаемости, то ею обладают все представленные на рынке варианты подошвы. Для защиты от холода толщина подметки делается от 1 см и больше. При этом на нее наносится протекторный рисунок, обеспечивающий вытеснение воды и хорошее сцепление со скользким грунтом.
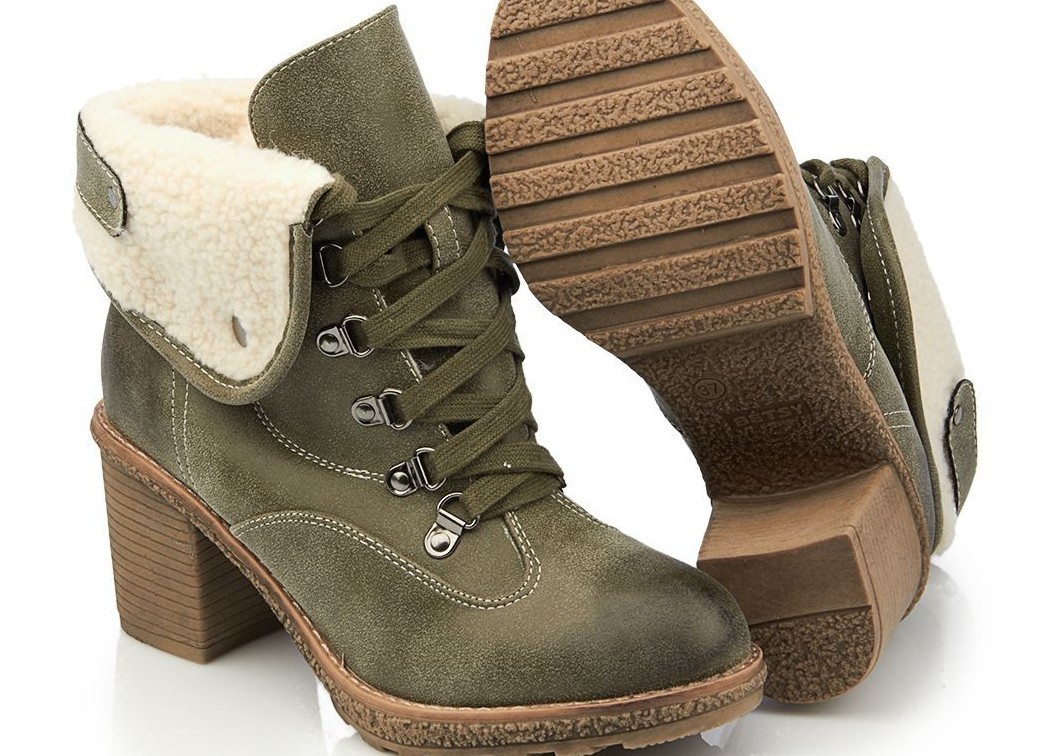
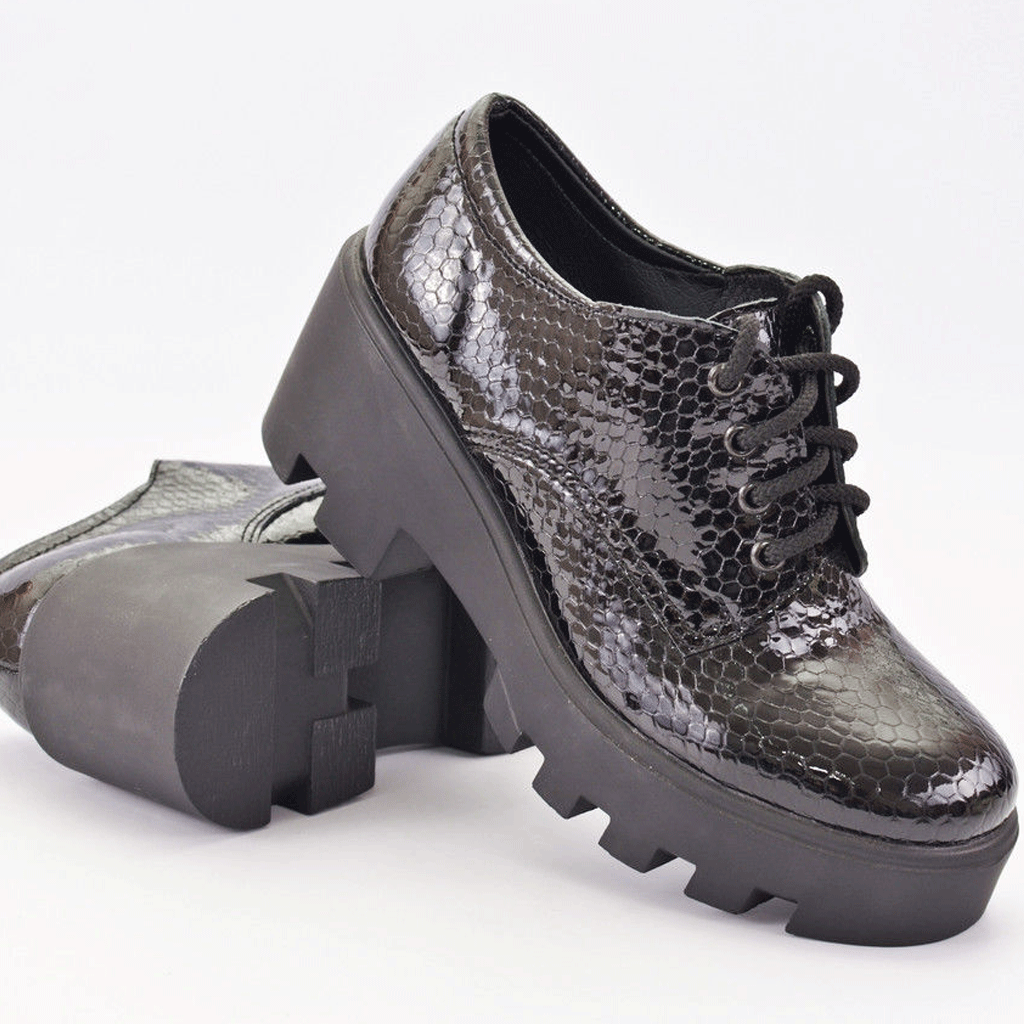
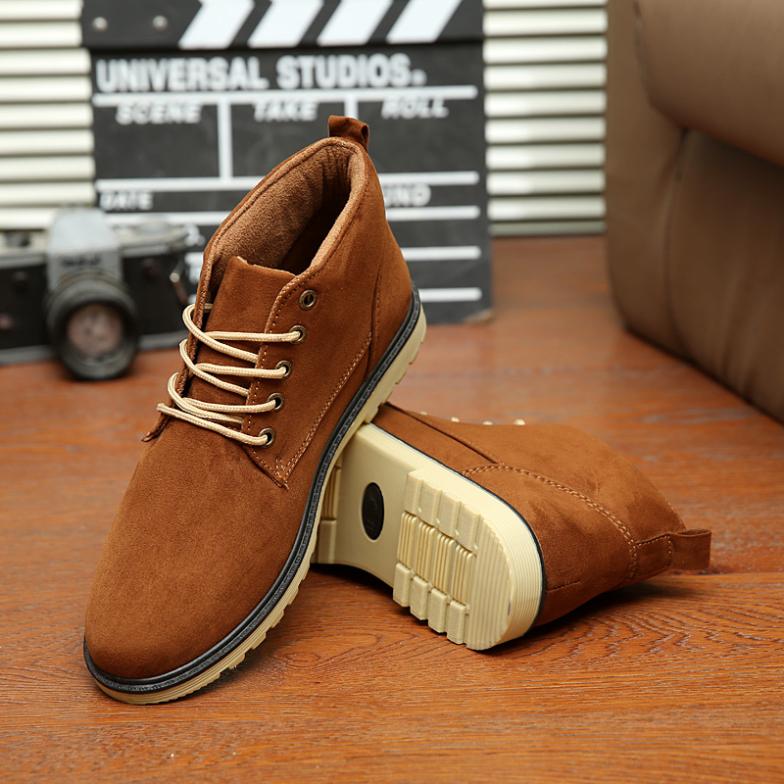
Зима
К подметкам зимней обуви предъявляются повышенные требования. Они не должны скользить, одновременно обеспечивая хорошую теплоизоляцию. Большое значение имеет высота протектора подошвы, обеспечивающей надежное сцепление со снегом. Такими качествами обладает термополиуретан и комбинированный полиуретан. Оба материала сохраняют гибкость, эластичность при любом морозе и отличный контакт с самой скользкой поверхностью.
Не следует выбирать изделия из ПВХ, натуральной, искусственной кожи. Эти материалы сильно скользят. Ходить в такой обуви зимой не только неудобно, но и опасно.
При изготовлении зимней обуви особое внимание уделяется толщине и рисунку на подошве. Для достижения хорошей теплоизоляции качественные модели оснащаются подошвой высотой от 2 см. Протектор на подошве делается глубоким, с ломаными линиями. Это предотвращает фронтальное и боковое скольжение на снегу.
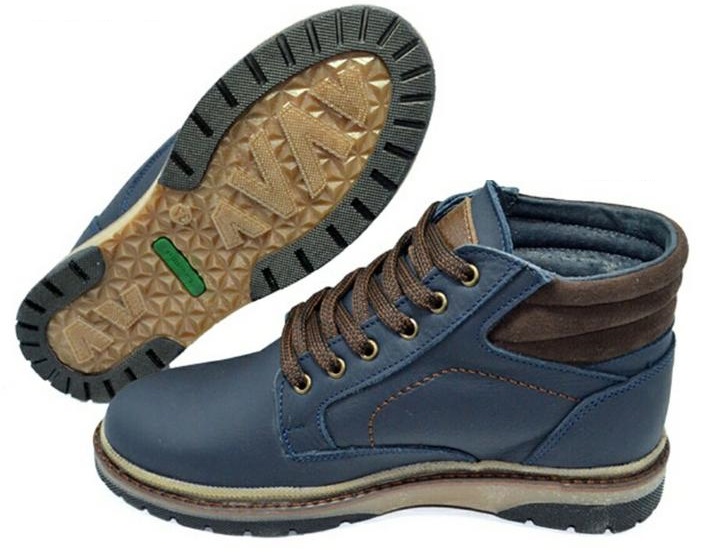
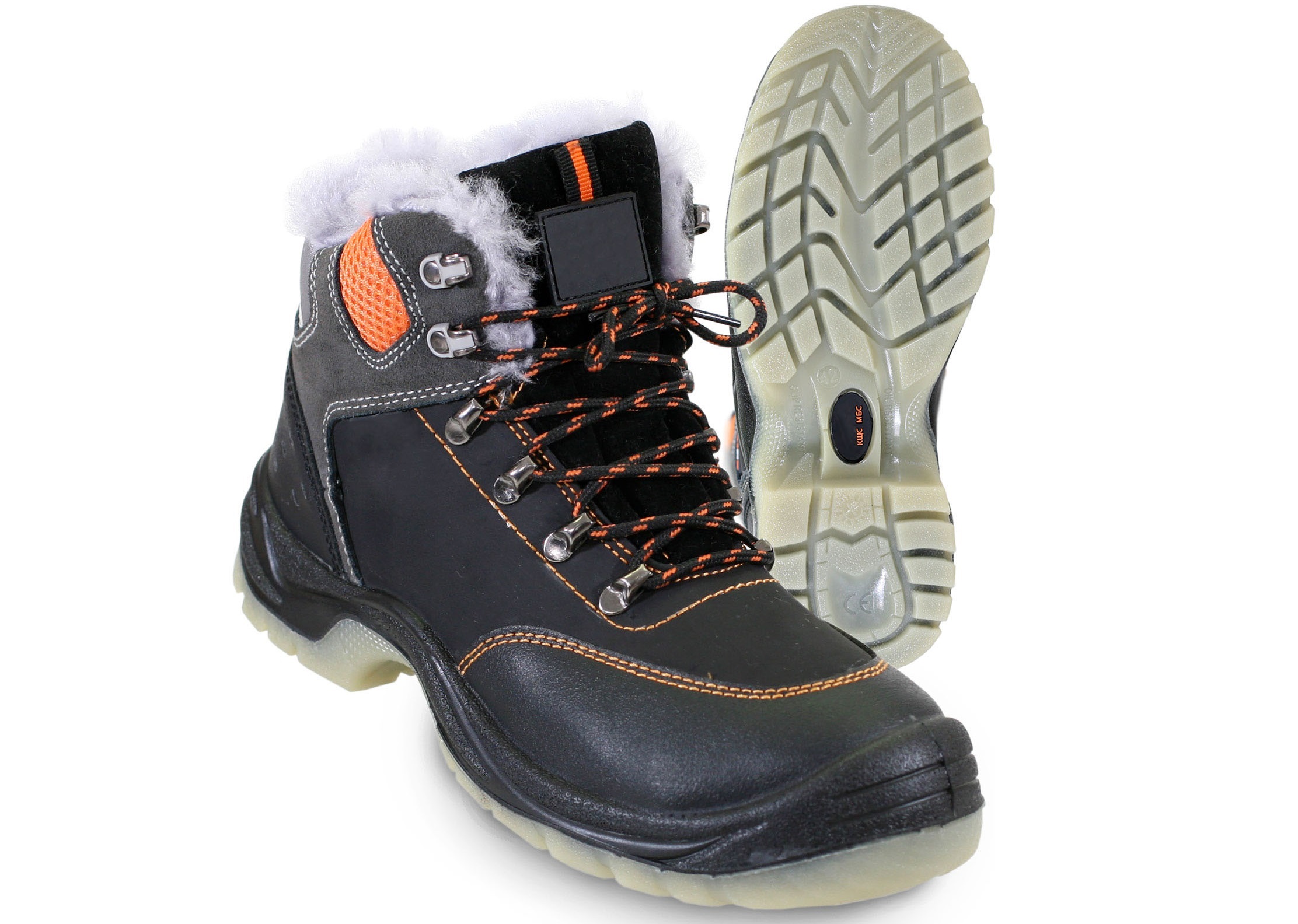
Видео
obuv.expert
Как это делается. Репортаж с производства специальной обуви
Обувь специального назначения — неотъемлемая часть средств индивидуальной защиты, без упоминания которой наш цикл статей о спецодежде не был бы полным. Само производство обуви связано с рядом технических нюансов, напрямую влияющих на ее качество. Поэтому мы решили посвятить этому направлению отдельную статью — репортаж с производственной линии СООО «Стецкевич-спецодежда», раскрывающий все секреты создания современной обуви с нуля.
Спецобувь предназначается для работников, которым требуется дополнительная защита ног от производственных рисков и неблагоприятных факторов окружающей среды. Диапазон характеристик такой обуви очень широк и напрямую зависит от области ее применения. Спецобувь может обладать устойчивостью к кислотам и щелочам, масло- и бензостойкостью, влагонепроницаемостью. Отдельные модели способны выдерживать сверхвысокие и сверхнизкие температуры (например, ботинки пожарного используются при температурах от –60 до +300 градусов). Нередко обувь специального назначения оснащается усиленным подноском (из металла или поликарбоната), фиксатором пятки или антипрокольной стелькой — все для защиты стопы от повреждений. Выпускают ботинки и с улучшенной фиксацией голеностопа, что снижает вероятность вывихов. Словом, специальная обувь может быть как комфортной ежедневной «одеждой» для ног, так и настоящей броней, значительно повышающей безопасность труда. Причем одно другого не исключает. Но из каких материалов ее делают?
Материал верха обуви — преимущественно, натуральная кожа. Ее качество и уровень обработки влияют на комфортность носки и защитные свойства изделия. Однако не менее важный показатель качества обуви — материал, из которого изготовлена подошва. Наиболее распространены подошвы из ПУ (полиуретана), комбинированные из ПУ и ТПУ (термополиуретана), нитрила. Эти материалы обладают высокой износостойкостью и гибкостью, устойчивостью к маслам, нефтепродуктам, щелочам. Термополиуретан практически по всем характеристикам превосходит полиуретан. Но и вес его выше, поэтому большая часть производимой в РБ и РФ обуви содержит комбинированную подошву ПУ/ТПУ. Такая подошва обладает и большей гибкостью по сравнению с ТПУ-монолитной. Последний, относительно новый для нашего рынка материал — нитрил. Подошва из него характеризуется еще более высокой износо-, термо- и химической стойкостью, для большинства видов работ этот материал наиболее оптимален.
Второй важный показатель качества — способ крепления подошвы к верху обуви. Наиболее распространенными являются: литьевой, метод прессовой вулканизации и клеепрошивной. Литьевой способ — наиболее современный. Он исключает вероятность возникновения зазора между верхом обуви и подошвой, попадание влаги внутрь, что иногда случается с обувью, скрепленной другими способами. Литье подошв применяется сегодня на производствах большинства экономически развитых стран мира.
Рассмотрим процесс изготовления обуви специального назначения подробнее. На производство поступает сырье — в большинстве своем это натуральные материалы. Из них кроят детали различными способами: либо рубят прессом со специальными режущими формами (резаками), либо нарезают на автораскройном комплексе.
Автоматический раскройный комплекс «Atom» предназначен для раскроя деталей верха и низа будущей обуви. Натуральные материалы кроятся на нем в один слой, искусственные — в несколько, в зависимости от их толщины. Голенище, ремень, подносок, задник, стелька, вкладная стелька — комплекс позволяет кроить любые обувные детали.
На начальном этапе модельер создает карты раскроя на компьютере. Затем карта проецируется откалиброванными проекторами прямо на материал, где автоматически раскладывает проекции деталей таким образом, чтобы они занимали максимальную площадь материала, и отходов было как можно меньше. Проекторы еще и помогают оператору визуально контролировать весь процесс. Если он увидит, что можно добавить в раскладку еще несколько мелких деталей — он это сделает «вручную», при помощи компьютерной мыши.
Затем раскроенные детали поступают на швейное производство, где сшиваются в единое целое — верх обуви. На пошивочном участке происходит затяжка обуви на колодку, крепится стелька, вставляется подносок и задник (их наличие зависит от модели). И уже затянутые заготовки пакуются в коробки, отправляются на участок для прилива подошвы.
Для наглядности рассмотрим процесс литья на примере комбинировонной подошвы из полиуретана и термополиуретана. Поступившие со швейной ленты заготовки обуви одевают на алюминиевую колодку в форме стопы (ее габариты соотносятся с распространенными размерами обуви). Колодка вставляется в свое посадочное место на автоматической линии Desma. Сама линия представляет собой «карусель» из 18 посадочных позиций, что позволяет одновременно изготавливать 9 пар обуви. Каждое посадочное место оснащено поворотным механизмом, позволяющим менять положение заготовки (верхнее/нижнее) на определенной стадии работы. На первой стадии колодки с надетыми на них заготовками устанавливаются в положение «сверху».
«Карусель» прокручивается и приносит закрепленную заготовку к роботу — координатно программируемой «руке». Робот производит «взъерошивание»: абразивным кругом подпиливает верхнюю часть кожи по контуру прилегания будущей подошвы. Это делается для того, чтобы сцепление бортика подошвы с кожей было наилучшим.
После обработки роботом «карусель» снова приходит в движение и заготовка перемещается к оператору, где он переворачивает ее сверху вниз. Заготовку помещают в пресс-форму, где происходит впрыск полиуретана.
Вкладыши поступают на производство в готовом виде, их отливает отдельная организация. Но оборудование Desma позволяет производить обувь и с цельной ПУ-подошвой. В таком случае полиуретан заполняет весь объем пресс-формы, низ которой выполнен в форме протектора.
Далее заготовку прокручивают к месту впрыска полиуретана. Впрыск в пресс-форму производится через узкое отверстие, чтобы избежать миграции материала. Пресс-форма четко задает размеры между заготовкой (верхом обуви) и нижней частью, поэтому весь объем заполняется полностью и равномерно.
Полиуретан в пресс-форме должен провести определенное время (время выдержки) при заданной температуре. Это нужно для того, чтобы заготовка хорошо «схватилась» с полиуретаном после его впрыска.
После выдержки заготовка с подошвой проходит по кругу до следующего оператора, который снимает ее и кладет в специальную холодильную установку, где подошва за считанные секунды остывает до комнатной температуры, а полиуретан окончательно принимает заданную структурную прочность.
По завершении литья на подошве остаются «бортики» (облой), могут встречаться и наплывы ПУ. Все это убирается вручную с каждой единицы обуви на машине для обрезки облоя. После чего обувь поступает на участок отделки.
На отделке изделию придают окончательный лоск: убирают все мелкие дефекты и окрашивают специальным составом — аппретурой. В ее состав входят пропитки, которые проникают глубоко внутрь кожи, закрепляют ее водоотталкивающие свойства и придают обуви «товарный» вид. После завершения этой операции внутрь вкладывают стельку и передают изделие на контроль качества.
Контролер сверяет каждый экземпляр с эталонным образцом, находящимся у него перед глазами. Поступившие к нему изделия должны строго соответствовать ГОСТу, в котором прописаны правила приемки и допуски по всем основным параметрам. В случае возникновений каких-либо подозрений (например — на неправильный размер обуви) производится обмер измерительными инструментами. Прошедшая контроль обувь поступает на шнуровку и пакуется в коробки, отправляясь на склад готовой продукции, откуда отгружается клиентам.
В соседнем цеху функционирует вторая линия Desma. Она предназначена для литья нитрила — более современного, но и более дорогостоящего материала для подошвы. Линия включает 12 посадочных позиций и позволяет лить подошвы для 6 пар обуви одновременно.
Сырьем для литья служит резиновая лента, поступающая от стороннего производителя. Лента заправляется внутрь шнека, где разогревается до температуры 170–175 градусов, при которой происходит вулканизация резины. Размягченная резина впрыскивается в пресс-форму тем же методом, что и на линии ПУ-литья.
После чего заготовка выдерживается заданное время, извлекается из пресс-формы и остывает естественным способом. Далее все происходит по вышеописанному техпроцессу: обрезка облоя, отделка, контроль и упаковка.
Результатом всех вышеперечисленных операций становится широкий ассортимент обуви, способный удовлетворить потребности любого производства, строительной компании или отдельно взятого человека. На этом мы прощаемся с производством обуви, но не прощаемся с нашими читателями — впереди вас ждет подробный репортаж о крупнейшем производстве спецодежды в Республике Беларусь. Следите за обновлениями на сайте!
stroyka.by
Пресс-формы для подошв из ЭВА пены, Пресс-формы для алюминий, Xieli Инжекционные пресс-формы для подошв
Пресс-формы для подошв из ЭВА пены
Пресс-формы для подошв спортивной обуви из ЭВА пены изготавливаются в соответствии с проверенными технологиями. Благодаря высокому качеству продукции и низким ценам, наша продукция закупается многими известными китайскими компаниями по производству спортивной обуви, включая Dearway, Peak, ABC Kids, Jordan, Hongxing Erke Group, Qingmei etc.
Особенности
1. Двухразовое вспенивание
2. Точность размеров
3. Превосходная обработка, конкурентоспособная цена
4. Обработка на станке ЧПУ
5. Сертификация ISO
Параметры пресс-формы
Материал: алюминий
Код ГС: 8480719090
Модель: пресс-форма для одной пары/двух пар/трех пар/четырех пар обуви
Пресс-формы для подошв из ЭВА пены подойдут для инжекционных машин для производства пресс-форм, изготовленных в Италии, на Тайване, в материковом Китае и т.д.
Размер: длина(200-450)*ширина(200-350)*высота(60-120)mm
Вес: 10-50кг
Упаковка: картонная коробка или трехслойная картонная коробка
Обработка: на станке ЧПУ
Производственная среда: 175℃-210℃
Обувная колодка: для каждого размера обуви предоставляются четыре бесплатных колодки
Доставка: 25 дней (после изготовления деревянной пресс-формы)
Срок службы: Более 5 лет
Для того, чтобы клиенты могли получше ознакомиться с продукцией в нашей компании есть два больших демонстрационных зала для образцов. Все данные образцы собраны нами у клиентов со всего мира, включая материковый Китай. В настоящее время мы прикладываем все усилия для модификации наших пресс-форм, чтобы наши клиенты могли создавать обувь новых моделей и фасонов.
Наша компания обладает десятилетним опытом в данной индустрии, что позволяет нам предлагать клиентам высококачественную продукцию по конкурентоспособным ценам. Компания Quanzhou Xieli Mould Company Ltd., которая является профессиональным производителем пресс-форм для обуви, была основана в 2002 году в г. Цзиньцзян, Китай.
Наша компания для производства пресс-форм для обуви использует только высококачественный алюминий. Для изготовления пресс-форм мы используем различные технологии, включая 4х осевое проектирование. Это обеспечивает защиту продукции от коррозии и её долговечность. Более того, наша компания обладает различным производственным и тестирующим оборудованием, системой планирования ресурсов предприятия (ERP), системой научного управления и строго соблюдает требования стандарта ISO9001:2000. Все это позволяет нам производить пресс-формы высокого качества, соответствующие требованиями международных стандартов.
В нашей компании работают 700 сотрудников, которые могут обеспечить своевременное изготовление и доставку продукции. Более того, у нас есть профессиональная команда, занимающаяся предоставлением послепродажных услуг.
shoe-mould.ru
Гвоздевой метод крепления Самый старый способ, в настоящее время постепенно уходит в прошлое – это «каменный век» в способе изготовления обуви. При этом методе крепления готовая формованная резиновая подошва присоединяется к жесткой основной стельке верха при помощи металлических (стальных или латунных) обувных гвоздей. Основные недостатки: достаточно трудоемкое изготовление и медленный производственный процесс. Готовая обувь получается весьма тяжелой по весу, имеет неэстетичный, «неуклюжий» и несовременный внешний вид. Производство такой обуви малорентабельно, цена на эту обувь достаточно низка (обувь не имеет никаких конкурентных преимуществ, выглядит грубо), а трудозатраты высоки. В настоящее время на многих обувных предприятиях России обувь гвоздевого метода крепления полностью снята с производства. |
Клеепрошивной метод крепления Основан на применении клея и ниточных соединений. В производстве специальной обуви наиболее распространен бортопрошивной метод крепления. Готовая формованная подошва из резины имеет бортик по периметру. Заготовка обуви сначала приклеивается к подошве, а затем прошивается нитками по бортику подошвы. Минусы бортопрошивного метода крепления – невозможность установки защитного подноска и отсутствие герметичности соединения верха и подошвы (влага может проникать внутрь обуви через отверстия пришивания подошвы). Другая разновидность – это ранто-прошивной метод. Подошва состоит из нескольких проклеенных слоев и дополнительно прострачивается нитками по верху, вдоль ранта. Этот вид крепления очень дорог в производстве, но является одним из самых прочных методов крепления. Данный вид крепления используется производителями крайне редко из-за дороговизны производства. |
Литьевой метод крепления Самый распространенный на сегодняшний день метод крепления в производстве специальной обуви. Этим методом изготавливается однослойная ПУ подошва, двухслойные подошвы ПУ/ПУ, ПУ/ТПУ, ПУ/Нитрил. Жидкие компоненты полиуретана впрыскиваются в пресс- форму и подошва формируется непосредственно на заготовке обуви. Обувь, изготовленная этим способом, имеет ряд преимуществ. — чрезвычайно легкий вес обуви — высокая гибкость готовой обуви и подошвы — высокотехнологичное изготовление — прочность крепления подошвы и заготовки — возможность создания моделей самого современного и эстетичного вида. Таким способом можно изготовить как спортивного вида кроссовки, так и модельного типа ботинки. Модельный ряд самый широкий: от легких туфель, до утепленных сапог — на обувь, изготовленную этим методом, возможно установить металлический ударопрочный подносок, антипрокольную стельку, любые защитные элементы и детали. — возможность придать подошве любую форму и высоту. Литьевая обувь занимает лидирующую позицию в ассортименте и структуре продаж большинства российских и зарубежных производителей специальной обуви. |
Метод горячей вулканизации Используется для изготовления обуви на нитрильной резиновой подошве. Сырая резина для подошвы подается в пресс- форму, подошва формируется непосредственно на заготовке (аналогично литьевому методу). Технологически этот метод немного отличается от производства подошвы из полиуретана, т.к. резину сначала нагревают до определенной температуры, и процесс вулканизации и формирования подошвы происходит при более высоких температурах, а также для лучшей адгезии верха и подошвы дополнительно применяется специальный клей (при изготовлении полиуретановой подошвы клей не используется). |
moderam.ru
Особенности проектирования подошв из полимерных мате- риалов и пресс-форм для их изготовления Текст научной статьи по специальности «Технологии материалов»
Л. Л. Никитина, Л. Ю. Махоткина, Л. Г. Хисамиева
ОСОБЕННОСТИ ПРОЕКТИРОВАНИЯ ПОДОШВ ИЗ ПОЛИМЕРНЫХ МАТЕРИАЛОВ И ПРЕСС-ФОРМ ДЛЯ ИХ ИЗГОТОВЛЕНИЯ
Ключевые слова: формованная подошва, полимерные материалы, пресс-форма,
полимерные материалы.
Современные материалы для обуви — это полимерные материалы. Наиболее широко полимерные материалы используются для деталей низа обуви. Рассматриваются полимерные материалы, применяемые для формованных подошв, приводятся показатели их свойств и особенности проектирования подошв и пресс-форм для их изготовления.
Keywords: the molded sole, polymeric materials, mold, polymeric materials.
Contemporary materials for the foot-wear — these are polymeric materials.
Most widely polymeric materials are used for the components of the bottom of footwear. Are examined the polymeric materials, used for the molded soles, they are brought the indices of their properties and special feature of the design of soles and molds for their production.
Использование формованных подошв при изготовлении обуви клеевого метода крепления значительно уменьшает трудоемкость и увеличивает производительность за счет исключения ряда технологических операций по получению деталей, их предварительной и окончательной обработке, улучшает потребительские свойства: повышается сопротивление истиранию подошвы, увеличивается срок службы обуви, водопроницаемость приближается к нулю и т.п. Особенности проектирования формованных подошв и пресс-форм для их изготовления определяются рядом факторов, наиболее важными из которых являются физико-механические свойства материалов и технология изготовления подошв.
Для изготовления формованных подошв используют, в основном, резины, полиуретаны (ПУ), поливинилхлориды (ПВХ), термоэластопласты (ТЭП), также этиленвинилаце-тат (ЭВА). Наиболее распространенным методом изготовления подошв из названных полимерных материалов является литье под давлением, также для изготовления полиуретановых подошв используется метод жидкого формования, для резиновых — метод горячей вулканизации.
Обувная резина — большая группа искусственных материалов, используемых, в основном, для изготовления низа обуви; очень прочный и эластичный материал, но имеющий меньшую эластичность, чем каучук. Обувная резина представляет собой сложное соединение полимерной основы (каучука, в основном, синтетического: бутодиенстирольного СКС-10, СКС-30, СКС-50, СКС-85, бутадиенового СКБ, дивинилового СКД и изопреново-го СКИ-3) и различных добавок. В процессе вулканизации происходит изменение свойств резиновой смеси вследствие взаимодействия каучука с серой и образования пространственной (трехмерной) структуры. [1, 2, 3]
Поливинилхлорид получают полимеризацией хлористого винила при температурах от 20 до 100оС с пероксидными инициаторами. В полимер вводят пластификаторы (эфиры
фталевой, себациновой и адипиновой кислот) для улучшения эластопластических свойств, стабилизаторы (бариевые, кадмиевые и другие соли жирных кислот) — для повышения стойкости к внешним воздействиям, преобразователи, красители и другие ингредиенты, меняя свойства полимера. Подошвы из ПВХ вырабатывают методом литья под давлением. По структуре материала они могут быть монолитными и пористо-монолитными (микропористыми) [1, 2].
Особое место среди подошвенных материалов занимают термоэластопласты (ТЭП), которые сочетают в себе эластические свойства каучуков и пластические свойства термопластов и находят широкое применение в обувной промышленности. Такое сочетание свойств определяется структурой полимеров. ТЭП представляют собой блок-сополимеры структуры А — Б — А или А — Б — С — Б — А, где А — термопластичный блок, Б — эластичный блок, С — агент полимеризации. В начале 60-х годах прошлого столетия началось производство ТЭП на основе этилена и винилацетата. В качестве блока А используют полистирол, полипропилен, полиметилметакрилат, поливинилхлорид и др., в качестве блока Б -полиизопрен, полибутадиен, полиизобутилен и др. От термопластов ТЭП отличаются низкими остаточными удлинениями, высоким сопротивлением истиранию и коэффициентом трения. Наиболее широко применяют трехблочные дивинилстирольные термоэластопласты ДСТ-30, ДСТ-50 и ДСТ-75. их используют для производства пористых формованных подошв. Также используются изопренстирольные ИСТ-20, ИСТ-30, дивинилметилсти-рольные ДМСТ-30. Оптимальными свойствами обладают трехблочные полимеры с содержанием стирола 20 — 30 %. Для улучшения технологичности (перерабатываемости), снижения стоимости и улучшения некоторых свойств в ТЭП вводят мягчители, наполнители, порообразователи, стабилизаторы, красители и т.п. [1, 2, 3].
Этиленвинилацетат (ЭВА) в обувном производстве начал применяться в конце 70-х годов прошлого столетия. ЭВА — сополимер этилена и винилацетата характеризуется невысокими показателями физико-механических свойств, однако отличается легкостью и низкой ценой. В 90-е годы появился поперечно-сшитый пенно ЭВА. Структурирование (процесс поперечной сшивки) позволил улучшить эксплуатационные характеристики ЭВА и перерабатывать его методом формования. Подошвы из ЭВА используют для домашней, пляжной, спортивной обуви.
Полиуретаны — это звенья макромолекул полиуретановых смол, связанные между собой уретановой группой. На основе полиуретанов производятся износостойкие подошвы и набойки, синтетические кожи для верха и подкладки обуви, клеев и покрытий, стойких в различных условиях эксплуатации. Основными исходными продуктами для получения полиуретана служат поли- и диизоцианаты и высокомолекулярные вещества с гидроксильными и эфирными группами. При изготовлении формованных полиуретановых подошв используют гидроксилсодержащие компоненты или жидкие каучуки. В качестве гидроксилсодержащего компонента наиболее часто применяют простые и сложные полиэфиры. Из простых полиэфиров наиболее часто применяют полиэтиленгликоль, полиоксипропи-ленгликоль и полифурит, представляющие собой жидкости с молекулярной массой 400 -1500, из сложных полиэфиров — полиэтиленгликольадипинат, поликапролактон, полиэти-ленбутиленгликольадипинат и др. — воскообразные и кристаллические вещества с молекулярной массой до 3000. При получении ПУ гидроксилсодержащие компоненты реагируют с изоцианатами. В смесь также вводят поверхностно-активные вещества и прорегуляторы. Композиции на основе сложных полиэфиров перерабатывают при температуре 40 — 60оС, из простых полиэфиров — при температуре 20 — 22оС. Композиции на основе сложных полиэфиров обеспечивают высокую прочность и сопротивление истиранию. В основном их
применяют для литья низа на верх затянутой обуви. Композиции на основе простых полиэфиров обеспечивают высокую гидролитическую устойчивость при меньшей прочности и сопротивлению истиранию и используются для литья подошв.
Подошвы из ПУ вырабатывают двумя методами: жидкого формования и литья под давлением. Наиболее часто используют метод жидкого формования. Подошвы, полученные этим методом, имеют микроячеистую структуру, что обеспечивает легкость, хорошие теплозащитные свойства и экономию материалов. Метод жидкого формования условно считают разновидностью метода литья под давлением. С литьем под давлением термопластичных полимеров жидкое формование объединяет лишь наличие операций заполнения пресс-формы и получения в ней изделия. При жидком формовании ингредиенты композиции на литьевом агрегате поступают по шлангам из реакторов в виде двух потоков (А и Б) в смесительную камеру, в которой соединяются в один поток, а затем впрыскиваются в пресс-форму, где происходят синтез, вспенивание и отверждение полимерной композиции, формование и фиксация форм низа обуви. Ингредиенты композиции могут соединяться в поток тремя методами: одно- двухстадийным (преполимерным), псевдопреполимерным. При производстве полиуретановых подошв жидким формованием предпочтителен псевдо-преполимерный метод, при котором смешивают потоки разной вязкости и массы, отсутствует саморазогрев смеси, преполимер получают готовым с химических заводов [1, 2, 3, 4].
Способность жидкой полиуретановой композиции равномерно распределяться по площади при незначительных силах деформации позволяет применять их для изготовления пресс-форм и затворных устройств пресс-форм несложных конструкций. При этом не только удешевляются пресс-формы из эпоксидных или других смол, из полиуретана, силикона, но и резко сокращаются сроки их изготовления, достигается высокая мобильность смены моделей низа и всей конструкции изделия, что важно в условиях быстрой сменяемости ассортимента. Например, для заполнения подошвенной пресс-формы объемом 400см3 требуется: 480г ПВХ-пластиката, 450г непористой резиновой смеси, 400г транспарентной резиновой смеси, 210г микроячеистой композиции из уретановых эластомеров для повседневной обуви, 180г микроячеистой смеси уретановых эластомеров для модельной обуви. Расход электроэнергии при разогреве пресс-форм при жидком формовании низа обуви из уретановых эластомеров значительно ниже, чем при горячей вулканизации и даже при литьевых методах с применением ПВХ или ТЭП, где пресс-формы охлаждаются, а разогреваются шнек и другие элементы агрегатов. При изготовлении подошв из уретано-вых эластомеров температура пресс-форм 45 — 55оС, при вулканизации резинового низа -170 — 190оС, при литье температура разогрева композиции ПВХ-пластиката 180 — 190оС. Снижение температуры пресс-форм также способствует улучшению условий труда.
Помимо свойств материалов, оказывающих существенное влияние на формирование потребительских свойств, при построении подошвы предусматриваются полости для облегчения конструкции и повышения гибкости. В подошвах из резины, ПВХ и ТЭП полости проектируются в виде решетки, стенки которой имеют уклон к основанию 3 — 5о. В полиуретановых подошвах выполнение решетки с остроугольными переходами недопустимо, поскольку они являются местами концентраций напряжений, вызывающих излом подошвы. Из этих соображений на ходовой поверхности не делаются поперечные желобки, недопустима грубая нарезка (имитация швов) и т. п. для облегчения таких подошв выполняются цилиндрические или конические отверстия, максимальная глубина которых составляет 2/3 толщины подошвы. Диаметр отверстий 8 — 15 мм. При моделировании геометрии ходовой стороны подошвы сложной формы необходимо учитывать особенности технологии ее изготовления, в том числе возможности фрезерного станка с ЧПУ, на кото-
ром будет обрабатываться оснастка для литья. При проектировании пресс-форм большое значение имеют технологические параметры переработки полимерных материалов, в частности, усадка — это свойство пластических масс уменьшаться в размере при охлаждении после извлечения из пресс-форм. Уменьшение неодинаково по длине и ширине подошвы. На практике необходимо уточнять значение величины усадки в разных поперечных сечениях.
Литература
1. Иванова, В.Я. Материаловедение изделий из кожи / В.Я. Иванова. — М.: Альфа-М: ИНФРА-М, 2008. — 208 с.
2. Зурабян, К.М. Справочник по материалам, применяемым в производстве обуви и кожгалантереи / К.М. Зурабян. — М.: 8Ьое-1еоп8, 2003. — 209 с.
3. Фомченкова Л.Н. Современные полимерные материалы для низа обуви / Л.Н. Фомченкова // Кожевенно-обувная промышленность. — 2009. — №4. — С. 25 — 30.
4. Пермяшкина, О.И. Совершенствование устройств формирования потока вспененного полимера на выходе из экструдера / О.И. Пермяшкина, В.А.Куничан, М.В. Обрезкова // Вестник Казан. технол. ун-та. — 2009. — №4. — С.159 — 165.
© Л. Л. Никитина — канд. пед. наук, доц. каф. конструирования одежды и обуви КГТУ; Л. Ю. Махоткина — д-р тех. наук, проф., зав. каф. конструирования одежды и обуви КГТУ; Л. Г. Хисамиева — канд. пед. наук, доц. каф. моды и технологии,: [email protected].
cyberleninka.ru